Thread milling is a highly effective and precise method used in machining to create threads in a workpiece. This technique involves using a tool that has limited contact with the workpiece, making it efficient and versatile.
For industry professionals, mechanical engineers, and buyers, understanding thread milling is crucial for making informed decisions in the manufacturing process.
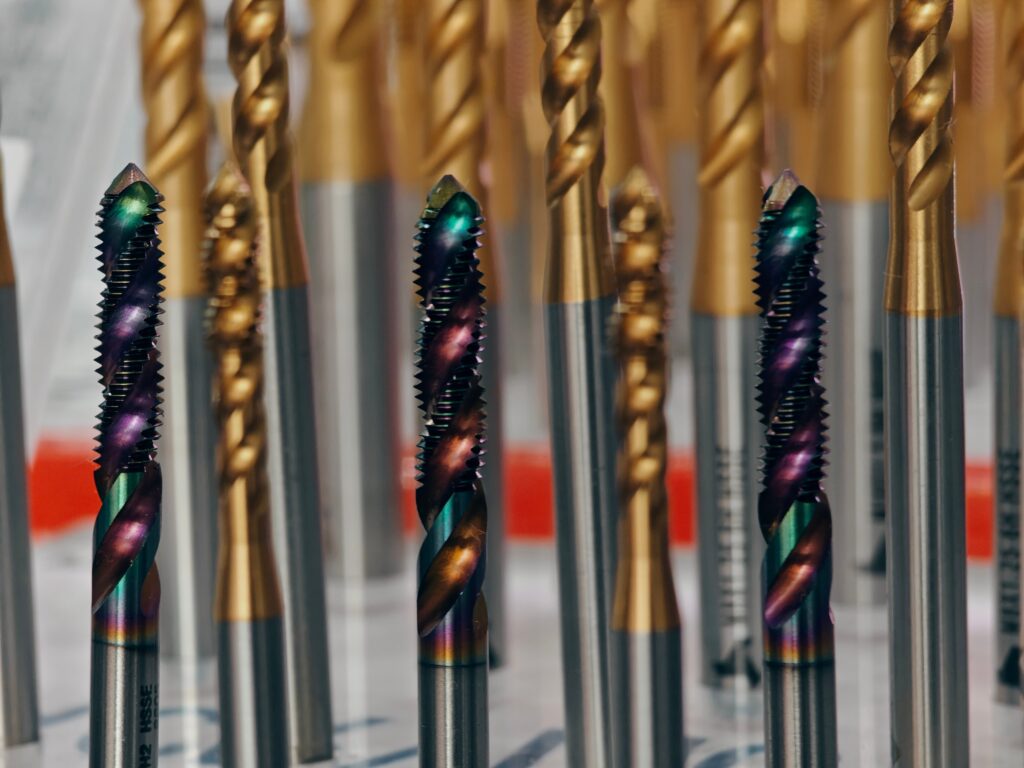
Thread millings, including single profile thread mills, full profile thread mills and indexable thread mills, offer unparalleled control over the fit of threads, allowing operators to achieve high precision with ease.
Using a high-speed rotating tool, unwanted material is removed from the metal surface, creating threads that are often superior to those made by other methods.
Precision, versatility, tool longevity, efficiency are all strengths of thread milling, while there are several weaknesses.
Next, let’s delve into what thread milling is, how it works, the different types, and its advantages and disadvantages.
-
Table Of Contents
-
1. What Is Thread Milling and How Does It Work?
-
2. What Are the Functions of Thread Milling?
-
3. What Are the Applications of Thread Milling?
-
4. What Are the Different Types of Thread Mills?
-
5. How Does Thread Milling Work?
-
6. What Are the Advantages and Disadvantages of Thread Milling?
-
7. Summary
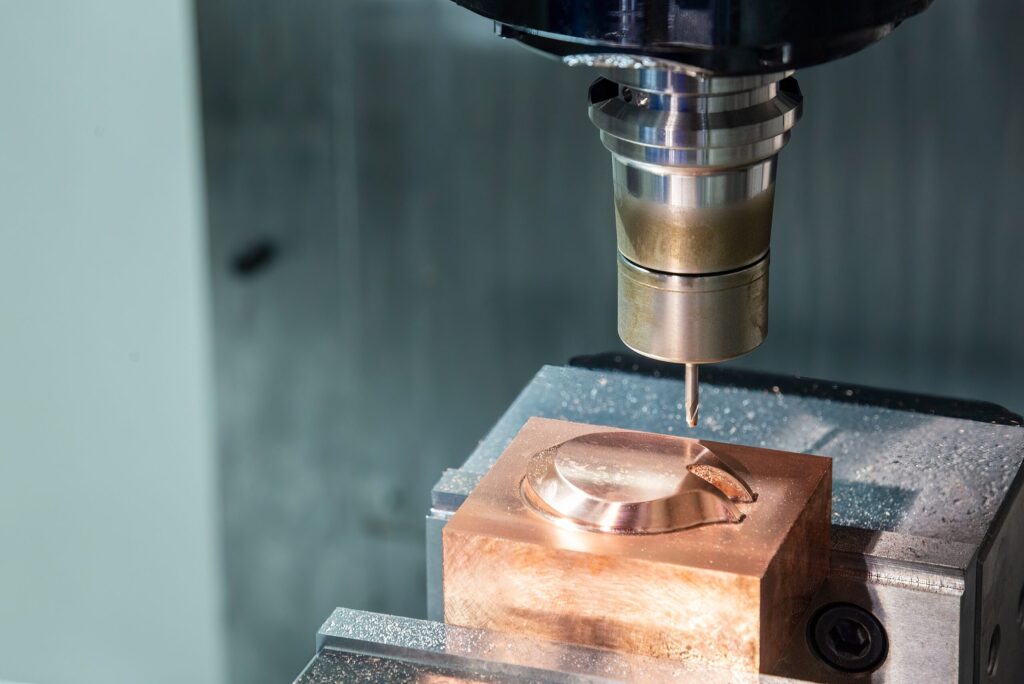
What Is Thread Milling?
Thread milling is a method for cutting threads into a part or workpiece using a specialized tool.
Unlike tapping, which uses a tool resembling a screw, thread milling employs a tool that resembles an end mill. This tool moves in a helical path around the inside of a pre-drilled hole, gradually forming the thread.
What Are the Functions of Thread Milling?
The primary function of thread milling is to create threads in a workpiece with high precision.
This process is particularly useful for creating threads in hard materials where traditional tapping might fail or produce suboptimal results.
Thread milling also allows for the creation of large diameter threads and special thread forms that would be challenging with other methods.
Thread milling provides flexibility in manufacturing. Operators can easily adjust the thread size and fit by modifying the tool path or changing the tool itself.
This adaptability is particularly valuable in applications where thread specifications might vary or when working with custom thread forms.
What Are the Applications of Thread Milling?
Thread milling is used in various applications across different industries, particularly where precision and flexibility are critical. Common uses include:
• Creating Internal and External Threads: Thread milling can produce both internal and external threads, making it a versatile choice for different types of components.
• Producing Threads in Hard Materials: Materials like hardened steel, titanium, and Inconel, which are difficult to machine using traditional methods, can be threaded efficiently with thread milling.
• Manufacturing Components for Aerospace, Automotive, and Medical Industries: High-precision threads are essential in these industries, and thread milling ensures the required accuracy and quality.
• Creating Custom Thread Forms and Large Diameter Threads: Thread milling can produce non-standard thread forms and large diameter threads that are often required in specialized applications.
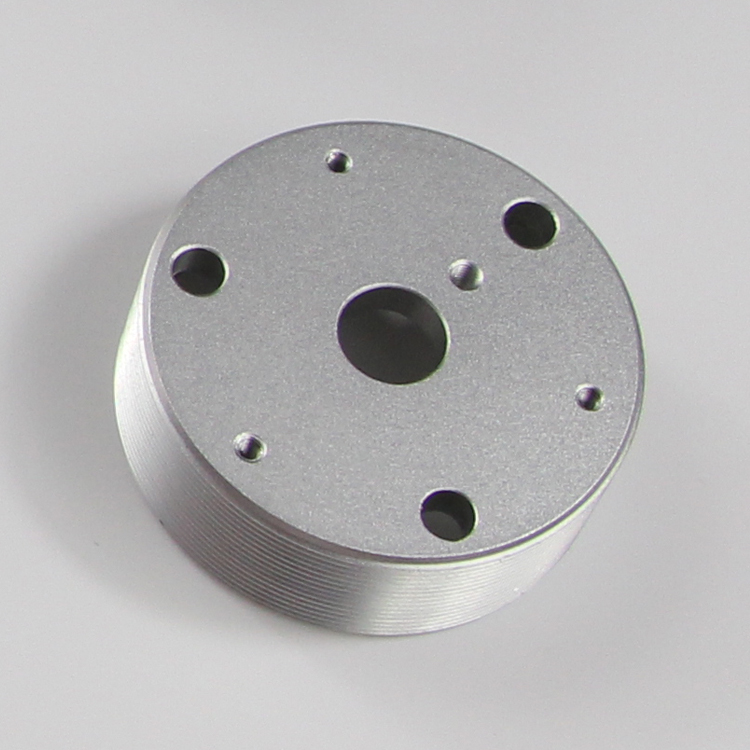
What Are the Different Types of Thread Mills?
Thread milling can be categorized into several types based on the tool design and the thread cutting process. Each type has its specific applications and benefits:
• Single Profile Thread Mills: These have a single tooth and cut one thread at a time, offering high precision. They are ideal for custom thread forms or where space is limited.
• Full Profile Thread Mills: These cut the entire thread profile in one pass, making them faster but requiring more machine power. They are suitable for high-volume production.
• Indexable Thread Mills: These have replaceable cutting inserts, combining the benefits of single and full profile mills. Indexable thread mills offer a cost-effective solution by allowing the replacement of worn inserts instead of the entire tool.
How Does Thread Milling Work?
Thread milling works by using a high-speed rotating tool to remove unwanted material from the metal surface. The tool, guided by the machine’s control system, follows a helical path to cut the threads.
The process begins with drilling a hole to the required diameter. The thread milling tool is then positioned at the hole’s center, and the machine starts the tool’s rotation at high speed. As the tool rotates, it follows a helical path around the inside of the hole, gradually cutting the thread profile.
The tool’s movement is precisely controlled to ensure the threads are cut to the desired depth and pitch.
The high-speed nature of thread milling allows for efficient material removal and quick thread production.
This efficiency is particularly beneficial in high-volume manufacturing environments where time and cost savings are crucial.
What Are the Advantages and Disadvantages of Thread Milling?
The advantages of thread milling are numerous and make it a preferred method for many machining applications:
• High Precision: Capable of producing precise cuts and threads, essential in applications requiring tight tolerances.
• Versatility: Suitable for a wide range of materials and thread forms, from soft aluminum to hard superalloys.
• Tool Longevity: Thread milling tools often last longer than taps, reducing tool costs.
• Reduced Risk of Breakage: Less contact area between the tool and the workpiece reduces the risk of tool breakage.
• Efficiency: High-speed operations can reduce production time, translating to cost savings and higher throughput.
• Flexibility: Can be used to create both internal and external threads, making it a go-to solution for various threading needs.
However, thread milling is not suitable for all scenarios. There are several disadvantages as listed below:
• Setup Time: Requires significant setup time for each operation. The time spent on setup can impact overall productivity, especially in low-volume production.
• Maintenance: Regular maintenance is necessary to keep the machine in optimal condition. Maintenance costs and downtime can affect the overall efficiency of the manufacturing process.
• Cost: Milling machines can be expensive to purchase and maintain. The initial investment and ongoing maintenance expenses need to be justified by the machine’s capabilities and production needs.
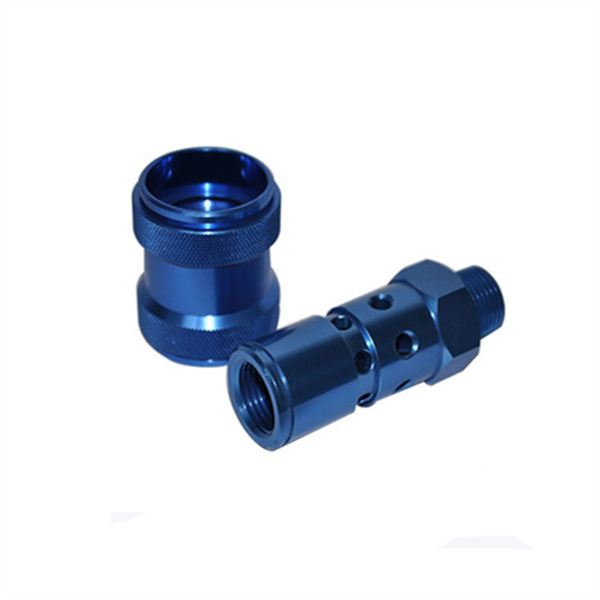
Summary
Thread milling is an advanced machining process that offers precision, versatility, and efficiency. By understanding the functions, applications, and types of thread mills, industry professionals can make informed decisions that enhance their manufacturing processes.
Whether you’re creating threads in hard materials or seeking precise control over thread fit, thread milling is a technique worth considering.