Die casting is a vital manufacturing process widely used to create complex metal parts with high precision.
Understanding its intricacies can significantly benefit manufacturing professionals, engineers, and potential buyers looking to leverage this technology for their projects.
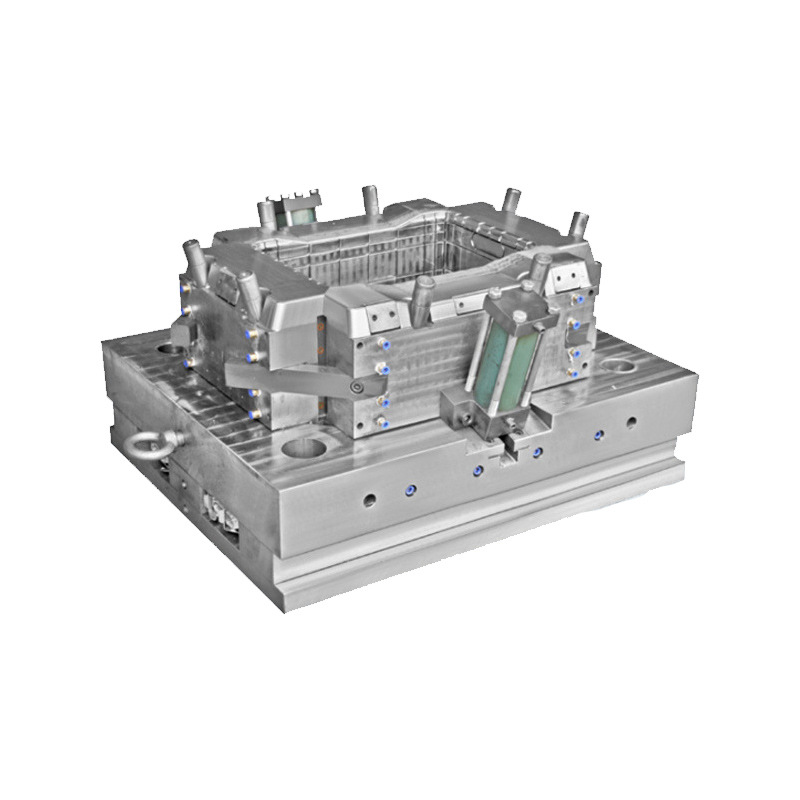
Die casting is a high-pressure metal casting process that injects molten metal into a mold.
This method yields dimensionally accurate, precision metal parts with a high-quality finish. Its capability to produce intricate details makes it ideal for mass production.
Now, let’s dive deeper into the world of die casting for reference, exploring its processes, benefits, and practical applications.
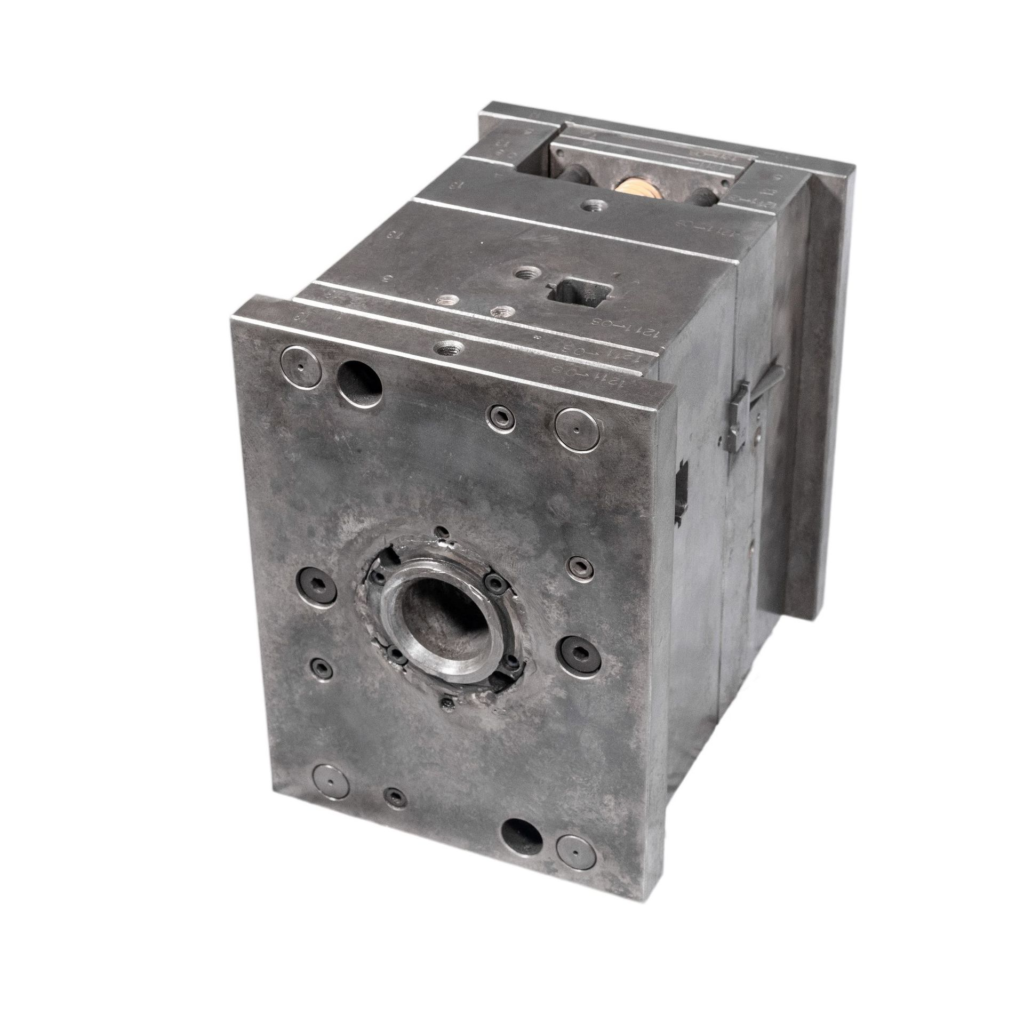
How Does Die Casting Work Step by Step?
The die casting process commonly consists of four essential steps:
1. Preparing the Mold: The mold is preheated to a specific temperature to minimize thermal shock and a lubricant is applied to facilitate part removal, control temperature, and prevent sticking.
2. Injection: Molten metal is injected into the mold cavity under high pressure, ensuring the metal fills the entire cavity and minimizing porosity. The process is controlled to maintain proper temperature and pressure.
3. Cavity Ejection: After solidification, the mold is opened and the part is ejected using ejector pins. This step is carefully timed to avoid damaging the part.
4. Shakeout: Excess metal, such as sprue and runners, is removed and typically recycled. The cast part may undergo additional finishing processes like trimming, grinding, or machining to meet final specifications.
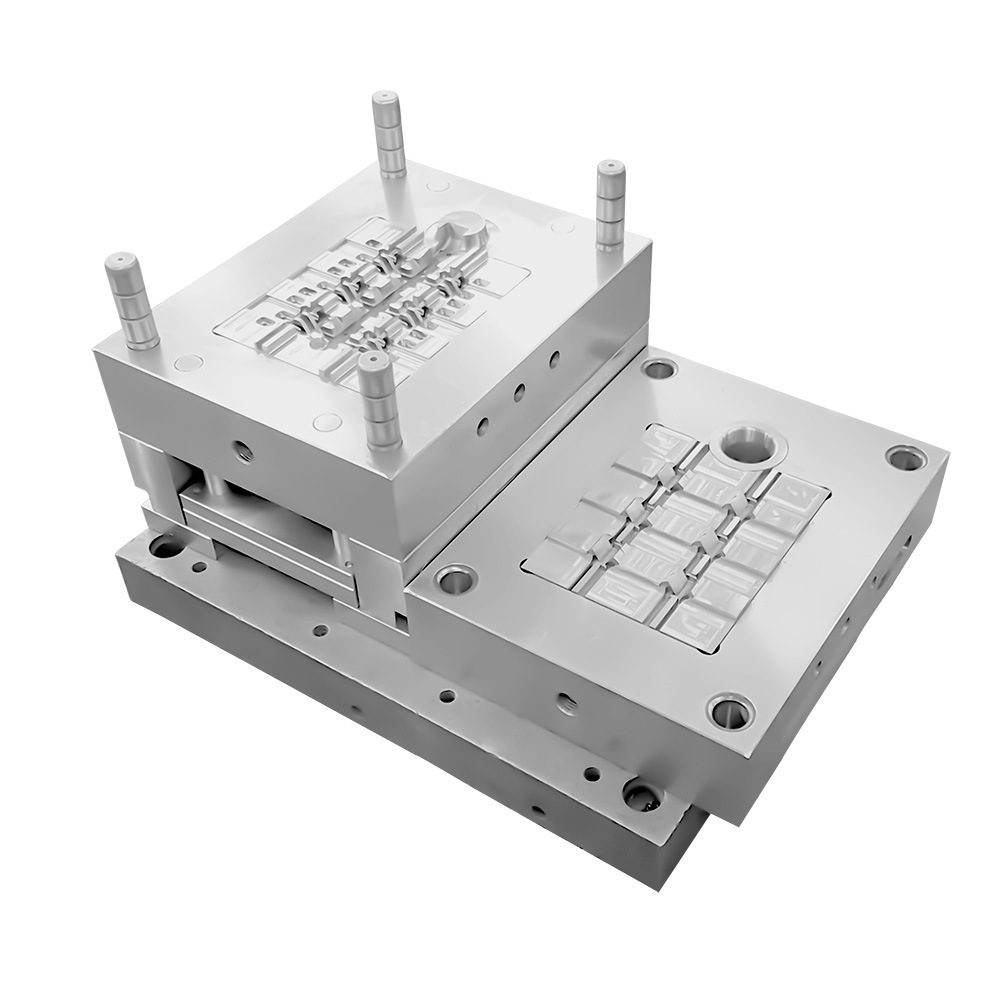
The Fundamentals of Die Casting
Three principles of die casting design are crucial for achieving optimal results:
1. Prioritize Function Over Form: Design parts based on their functional requirements rather than traditional norms. This means focusing on performance specifications and structural integrity, like using ribs and fillets to enhance strength without adding weight.
2. Ensure Sufficient Performance: The part’s performance must meet standards, even if it requires unconventional designs. Integrating multiple functions into a single part can reduce complexity and improve performance, such as combining structural and thermal management in automotive components.
3. Match material properties to specifications: Choose materials that meet the part’s performance needs. Different metals offer varying properties like strength and thermal conductivity. For instance, aluminum is favored for its lightweight and corrosion resistance in automotive and aerospace applications.
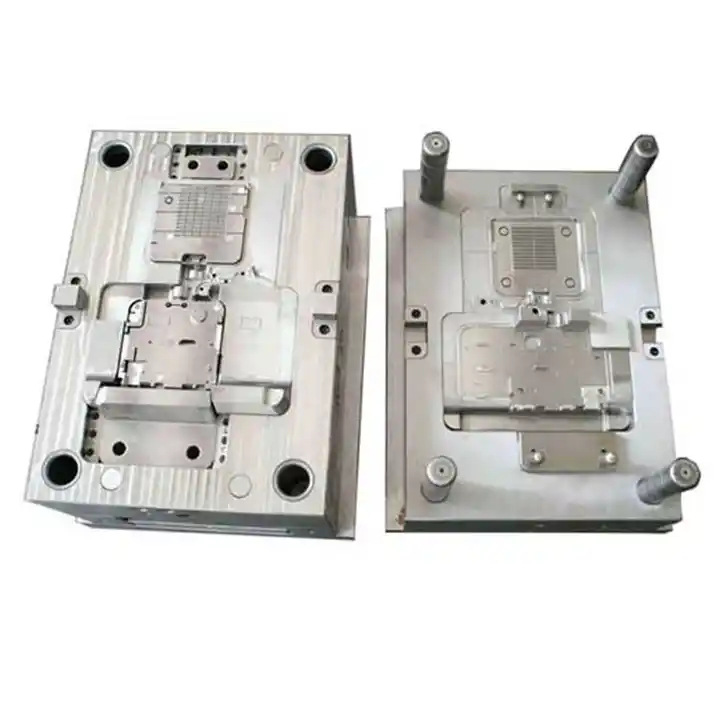
How to Make a Die Casting Mold?
1. Designing the Mold: Use CAD software to design the mold, considering part geometry, material, and production volume. Simulate molten metal flow to address potential issues and ensure consistent, high-quality parts.
2. Machining the Mold: Use precision techniques like CNC milling and EDM to machine the mold from steel, matching the exact part dimensions. Polish the surfaces for the desired finish.
3. Assembling the Mold: Align the two mold halves precisely to avoid defects. Install inserts or cores for internal features.
4. Testing and Refining the Mold: Conduct a trial run, inspect the parts, and adjust the mold or process to ensure high-quality, accurate parts.
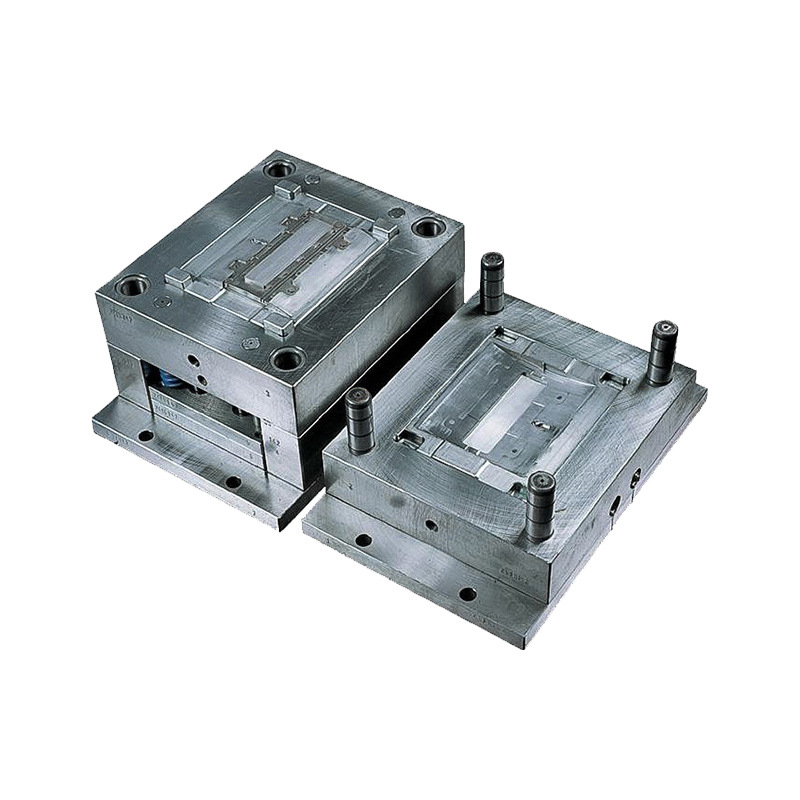
What are Advantages and Disadvantages of Die Casting?
Advantages:
• High Precision: Die casting produces parts with excellent dimensional accuracy and smooth surface finishes. This precision allows for the production of complex geometries that would be difficult or impossible to achieve with other manufacturing methods.
• Complex Shapes: The process allows for the creation of intricate and complex shapes that would be difficult to achieve with other manufacturing methods. Die casting is particularly well-suited for parts with thin walls, fine details, and intricate features.
• Cost-Effective for Large Production Runs: Once the mold is created, die casting is highly efficient and cost-effective for mass production. The high-speed injection process allows for the rapid production of large quantities of parts, reducing per-unit costs.
• Material Versatility: Die casting can be used with a variety of metals and alloys, including aluminum, magnesium, and zinc. This versatility allows manufacturers to choose the best material for their specific application, balancing factors such as weight, strength, and corrosion resistance.
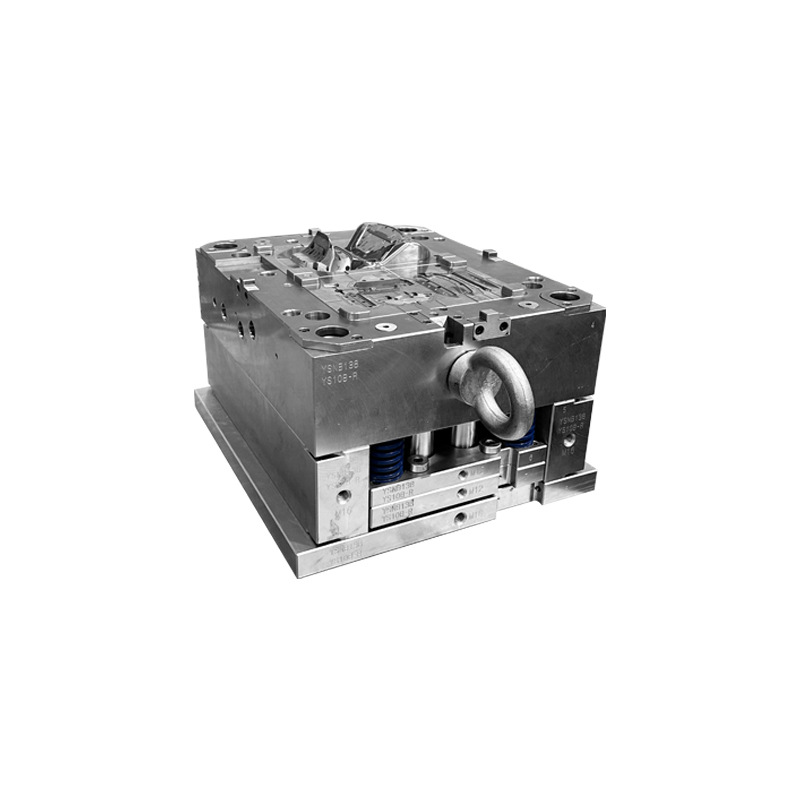
Disadvantages:
• High Initial Tooling Costs: The creation of the mold can be expensive and time-consuming, making die casting less suitable for low-volume production. The cost of designing and machining the mold is a significant upfront investment, but it can be amortized over large production runs.
• Susceptibility to Defects: Improper design or execution can lead to defects such as misruns, cold shuts, and porosity. These defects can compromise the quality and performance of the cast parts, requiring careful attention to process control and quality assurance.
• Limited Material Options: While die casting is versatile, not all metals are suitable for the process, limiting material choices. High-melting-point metals, such as steel and titanium, cannot be die cast using conventional processes, restricting the range of applications.
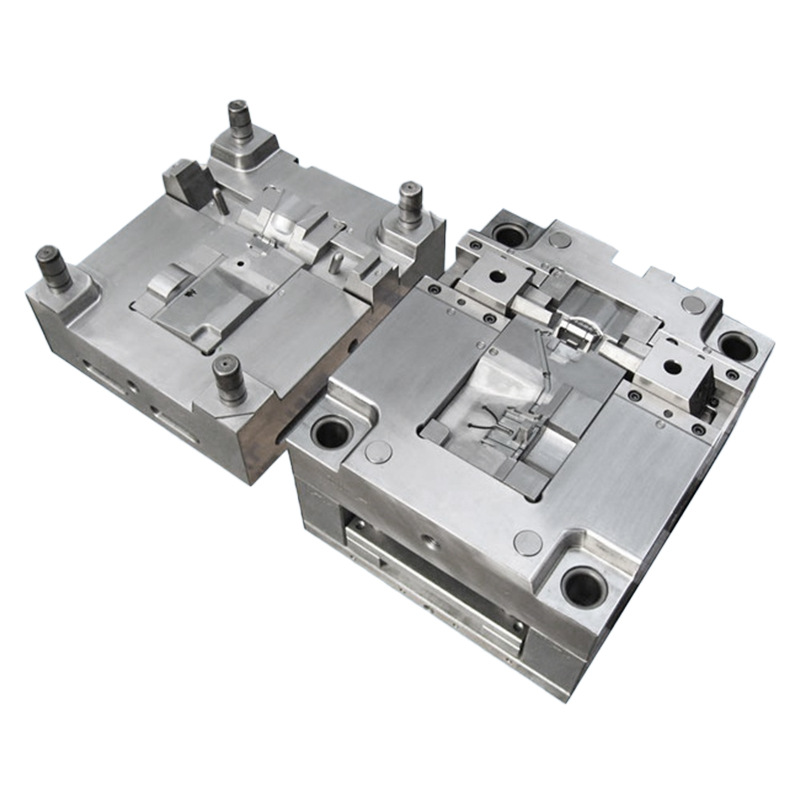
What are Types of Die Casting?
1. Hot Chamber Die Casting: This method is used for metals with low melting points, such as zinc, magnesium, and lead. In hot chamber die casting, the injection mechanism is submerged in the molten metal, making the process faster and more efficient. This type of die casting is ideal for high-volume production of small to medium-sized parts, offering excellent surface finish and dimensional stability.
2. Cold Chamber Die Casting: Suitable for metals with higher melting points, such as aluminum and copper. In cold chamber die casting, the molten metal is ladled into the injection system from an external furnace, providing better control over the casting process. This method is used for producing larger parts with higher strength requirements, such as automotive engine components and structural parts.
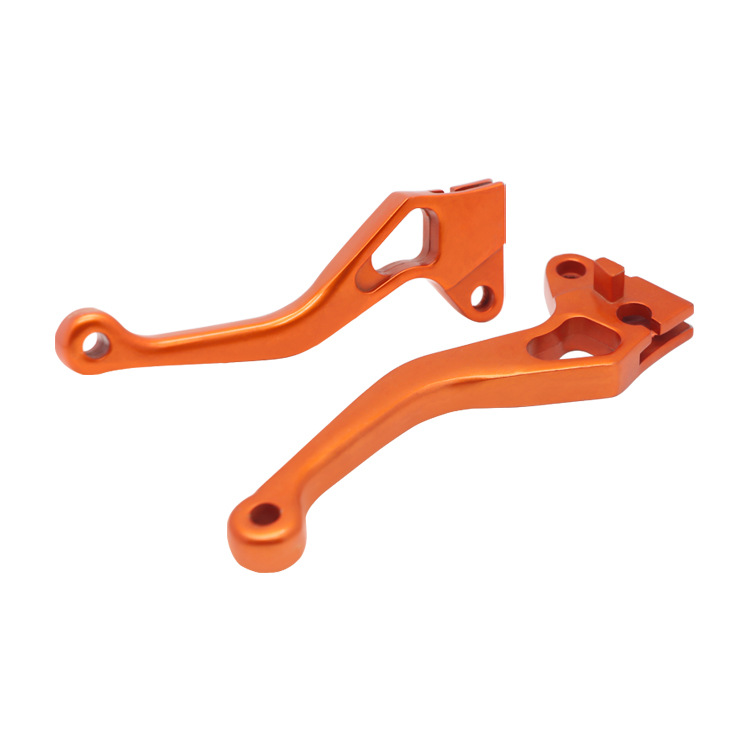
Summary:
Understanding die casting can revolutionize your approach to manufacturing metal parts.
This comprehensive guide aims to provide you with the knowledge needed to make informed decisions about using die casting in your projects.
By mastering the fundamentals, processes, and applications of die casting, you can achieve high-quality, precision parts that meet the demands of modern manufacturing.
Die casting offers numerous advantages, including high precision, the ability to produce complex shapes, etc. However, it also comes with challenges such as high initial tooling costs and susceptibility to defects.
By carefully considering these factors and implementing best practices, you can leverage die casting to its fullest potential, ensuring the success of your manufacturing endeavors.