Tolerances in manufacturing play a crucial role in ensuring the precision and quality of both sheet metal and machined parts.
Understanding these tolerances helps engineers, manufacturing professionals, and buyers meet the required specifications and maintain the functionality of their products.
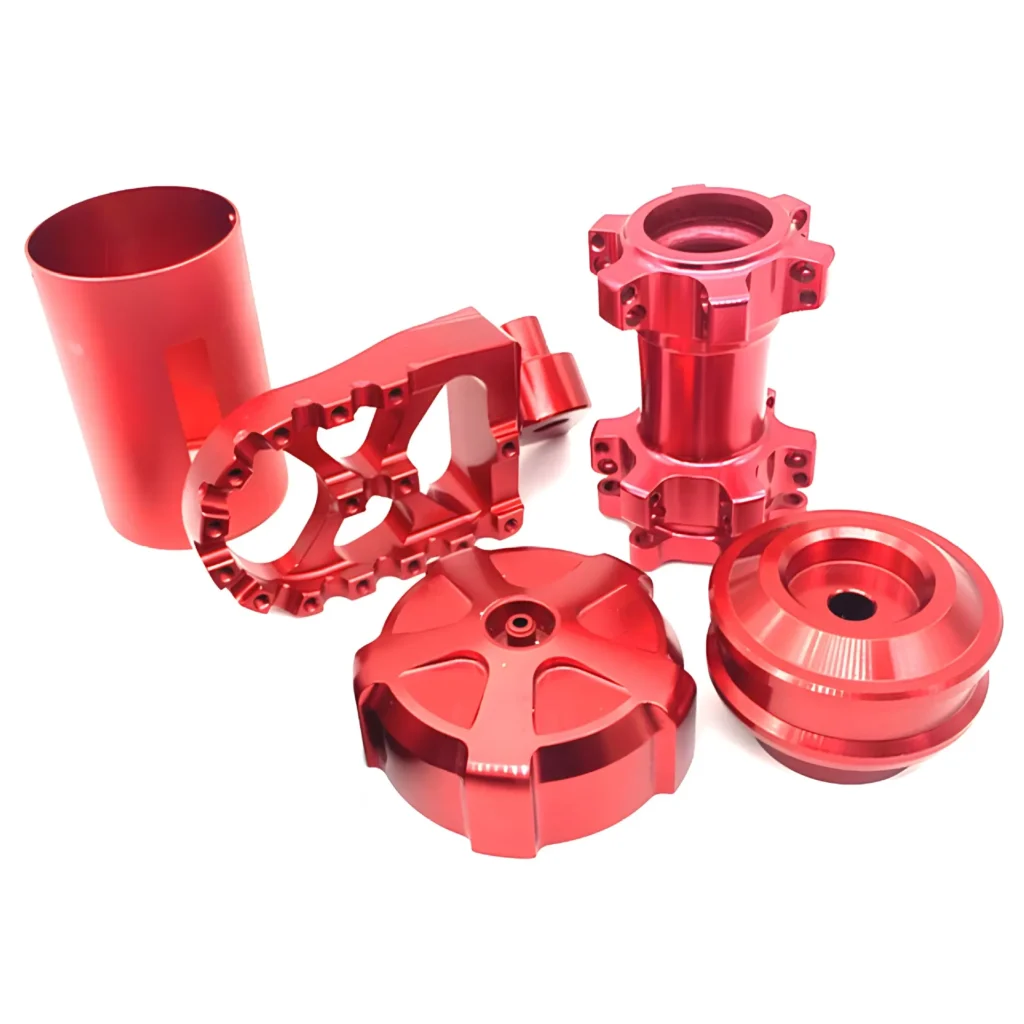
The standard tolerances for sheet metal fabrication include edge-to-edge, edge-to-hole, and hole-to-hole tolerances of ±0.127 mm (0.005″). In contrast, hole-to-hardware tolerances are ±0.254 mm (0.010″). For machined parts, the standard tolerance is typically ±0.005 in. (0.13 mm).
The standard prototype and production machining tolerance at Partzcore is +/- 0.005 (0.13mm). This tolerance ensures that any part feature’s location, width, length, thickness, or diameter will not deviate by more than this amount from the nominal.
Now, Let’s dive deeper into the various aspects of tolerances, including their types, applications, and the importance of adhering to these standards.
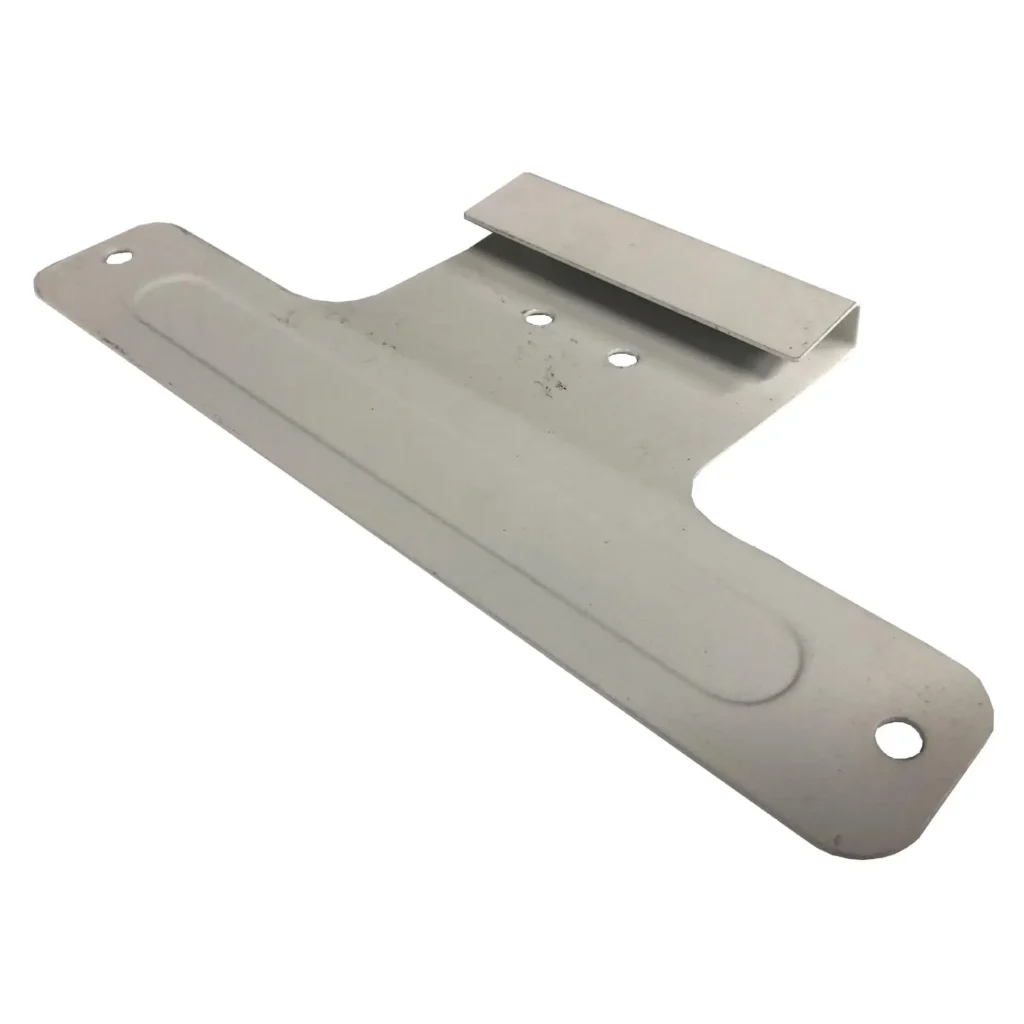
Understanding Tolerances in Manufacturing
Tolerance in manufacturing refers to the permissible limit or limits of variation in a physical dimension. Tolerances specify the allowable deviation from a specified dimension, ensuring that the parts function as intended, even with minor variations. These deviations can be in the form of size, shape, position, or orientation.
Types of Tolerances
1. Dimensional Tolerances: These refer to the allowable variations in the physical dimensions of a part, such as length, width, height, and diameter.
2. Geometric Tolerances: These refer to the allowable variations in the shape and position of a part’s features, such as flatness, straightness, roundness, and parallelism.
3. Angular Tolerances refer to the permissible variations in the angles of a part’s features.
4. Surface Tolerances: These refer to the allowable variations in the surface finish of a part.
Each type of tolerance plays a crucial role in ensuring that parts fit together correctly and perform their intended function without failure.
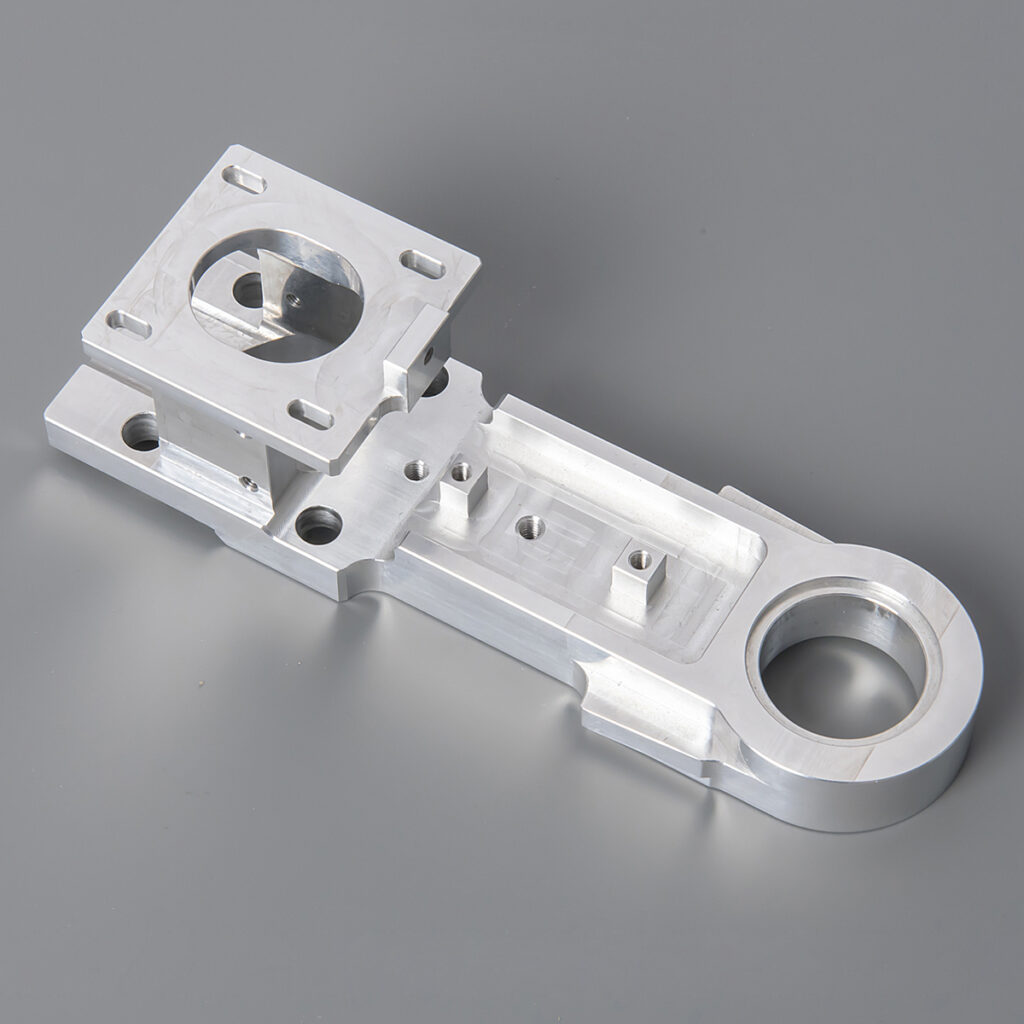
Importance of Tolerances in Manufacturing
1. Interchangeability: Tolerances ensure that parts manufactured in different batches or by other suppliers can fit together and function as intended.
2. Quality Control: By specifying tolerances, manufacturers can control the quality of their products and ensure consistency.
3. Cost Efficiency: Proper tolerances help reduce waste and rework, saving costs.
4. Functionality: Ensuring that parts meet the required tolerances is essential for their proper functioning and longevity.
Factors Affecting Machining Tolerances
1. Material Properties: Different materials have different properties that can affect machining tolerances. For example, metals like aluminium and steel typically allow for tighter tolerances than plastics due to their rigidity and stability.
2. Machining Process: The machining process (e.g., CNC milling, turning, drilling) can also affect tolerances. CNC machines generally offer higher precision compared to manual machining.
3. Tool Wear: The condition of the cutting tools used in machining can impact tolerances. Worn tools may produce parts with more significant deviations.
4. Machine Calibration: Regular calibration of machining equipment is crucial for maintaining tight tolerances. Misaligned or poorly calibrated machines can result in parts not meeting the specified tolerances.
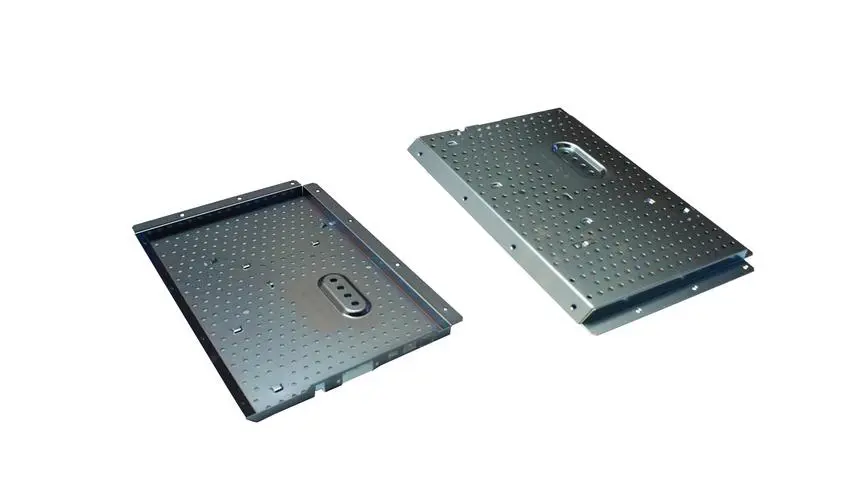
What are the Tolerances for Modern Machining?
Modern CNC machining typically adheres to a tolerance limit of +/-. 005″ (0.127 mm). For reference, the thickness of a human hair is approximately 0.002″ (0.05 mm), highlighting the precision required in machining processes.
Such tight tolerances are necessary for high-accuracy components, such as aerospace, automotive, and medical device manufacturing.
Advancements in CNC Machining
1. Improved Precision: Advances in CNC technology have significantly improved the precision and accuracy of machined parts. Modern CNC machines can achieve tolerances as tight as ±0.001″ (0.025 mm).
2. Enhanced Repeatability: CNC machines offer high repeatability, meaning that parts can be produced consistently within the specified tolerances across multiple production runs.
3. Complex Geometries: CNC machining allows for producing complex geometries with tight tolerances, which would be challenging or impossible to achieve with manual machining.
Tolerances in Sheet Metal Fabrication
Tolerances in sheet metal fabrication include edge-to-edge, edge-to-hole, and hole-to-hole measurements. These tolerances ensure that the parts fit together accurately during assembly. For example, edge-to-edge and edge-to-hole tolerances are typically ±0.127 mm (0.005″), while hole-to-hardware tolerances are ±0.254 mm (0.010″).
Adhering to these tolerances is essential to prevent misalignment and ensure the structural integrity of the assembled parts.
Common Tolerances in Sheet Metal Fabrication
1. Edge to Edge: ±0.127 mm (0.005″)
2. Edge to Hole: ±0.127 mm (0.005″)
3. Hole to Hole: ±0.127 mm (0.005″)
4. Hole to Hardware: ±0.254 mm (0.010″)
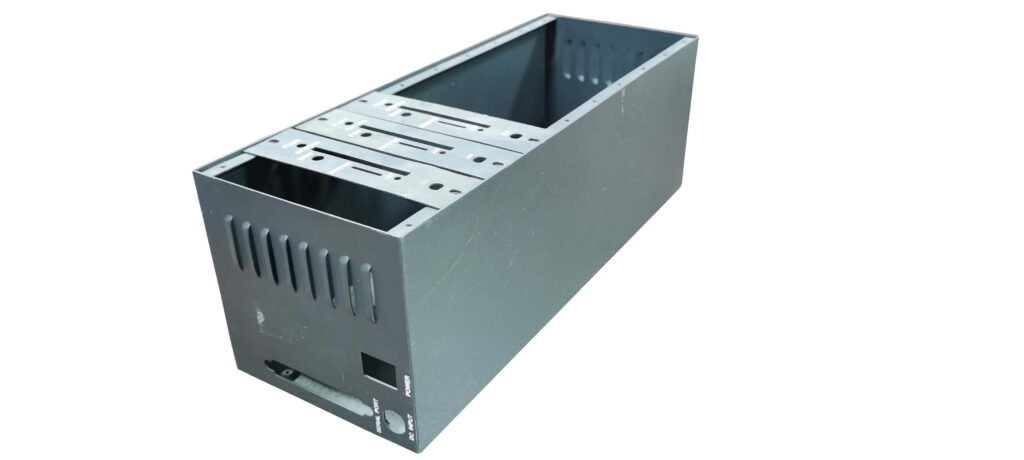
Factors Affecting Sheet Metal Tolerances
1. Material Thickness: Thicker materials generally require looser tolerances compared to thinner materials.
2. Cutting Method: The method used to cut the sheet metal (e.g., laser cutting, waterjet cutting, punching) can affect the achievable tolerances.
3. Bending and Forming: Processes like bending and forming can introduce variations in the part’s final dimensions, impacting tolerances.
Metric vs. Imperial Tolerances
In many industries, metric tolerances are preferred due to their simplicity and ease of use.
However, imperial tolerances are still commonly used in some regions, such as the United States. Understanding both systems and converting between them is essential for international manufacturing and trade.
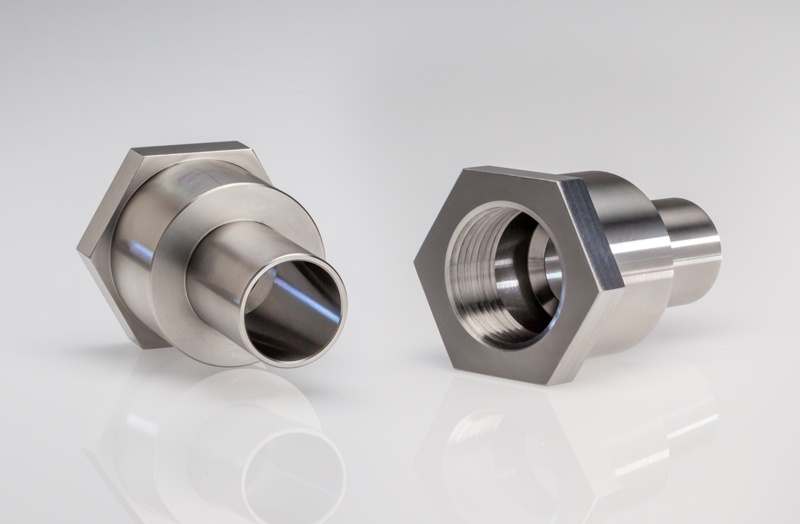
CNC Tolerance Standards
CNC machining tolerance standards define the acceptable degree of variation in part dimensions.
These standards ensure consistency and reliability in the manufacturing process. For instance, CNC machining typically adheres to a tolerance of ±0.005″ (0.127 mm), guaranteeing high precision and accuracy in produced parts.
Importance of CNC Tolerance Standards
1. Consistency: CNC tolerance standards ensure that parts produced in different batches or by other manufacturers are consistent in quality and dimensions.
2. Quality Assurance: Adhering to established standards helps maintain high quality and reduces the risk of defects.
3. Efficiency: By following standardized tolerances, manufacturers can streamline their processes and reduce the time and effort required for quality control.
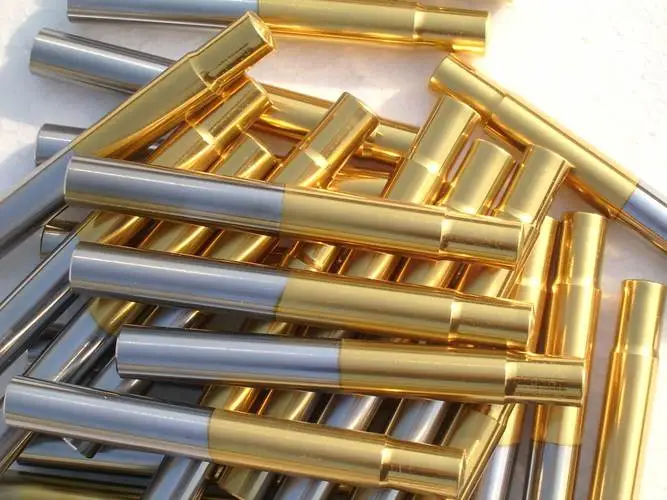
Summary:
In summary, tolerances are a fundamental aspect of manufacturing that ensures parts fit together correctly and function as intended.
Whether you are working with sheet metal or machined parts, understanding and adhering to tolerance standards is essential for maintaining quality, reducing costs, and ensuring the success of your manufacturing projects.