Stamped fixtures play a transformative role in the lighting industry, offering unmatched precision, durability, and cost-efficiency.
These components streamline production while ensuring high performance across diverse applications, from residential lighting to industrial solutions.
The growing demand for innovative, scalable, and eco-friendly designs has propelled the importance of metal stamping to the forefront of lighting manufacturing.
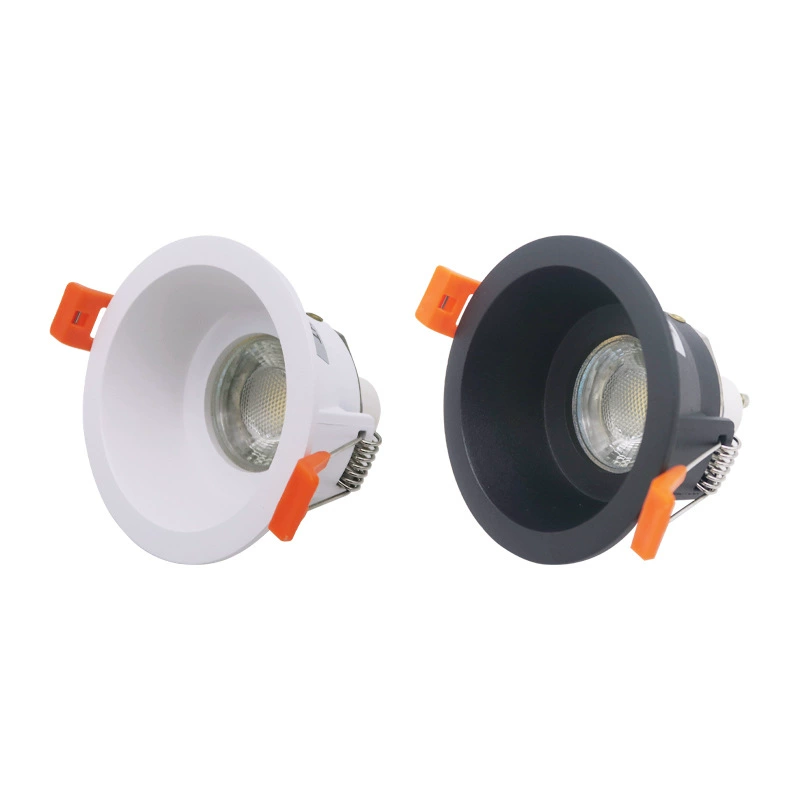
So, why are stamped fixtures indispensable?
Their ability to produce essential components like reflectors, housings, and mounting brackets at scale makes them integral to modern lighting systems.
Stamped fixtures reduce production costs and enhance the aesthetic and functional value of lighting products, ensuring they meet the market’s evolving needs.
In this article, we’ll explore the versatility of stamped fixtures, their specific applications in lighting, and how they address the unique challenges faced by manufacturers and designers.
We’ll also discuss new trends, highlighting how stamped components support innovation in the fast-evolving lighting industry.
Metal stamping allows manufacturers to create high-precision parts that meet exact design specifications efficiently.
-
Table Of Contents
-
1. What Are Stamped Fixtures Used for in the Lighting Industry?
-
2. What Is Metal Stamping Used for in the Lighting Industry?
-
3. What Are the Benefits of Using Stamped Metal for Lighting Fixtures?
-
4. What Types of Lighting Fixtures Use Stamped Components?
-
5. How Does Metal Stamping Improve Cost Efficiency for Manufacturers?
-
6. What Materials Are Commonly Used for Stamped Lighting Fixtures?
-
7. What Are the Advantages of Using Stamped Fixtures in the Lighting Industry
-
8. Trends and Innovations in Stamped Fixtures
-
9. Summary
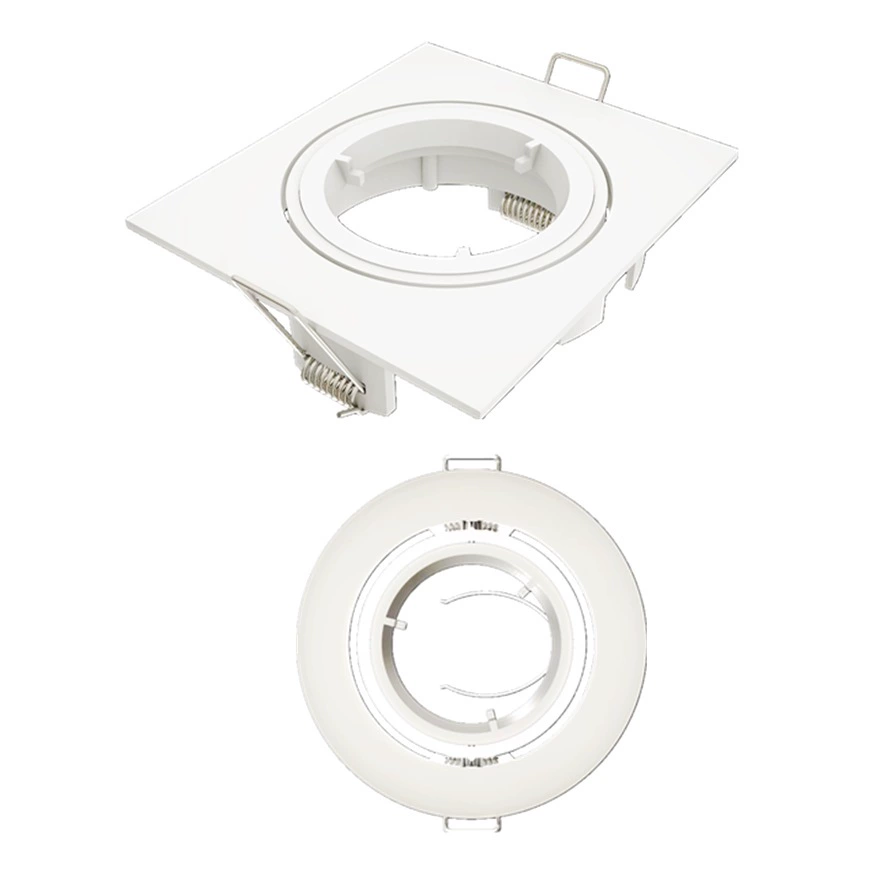
What Is Metal Stamping Used for in the Lighting Industry?
Metal stamping involves shaping flat metal sheets using specialized dies to create components with consistent precision.
This process is ideal for high-volume production and custom designs. Key applications in the lighting industry include:
• Reflectors and light shields: Direct light efficiently while minimizing glare.
• Housing components: Protect internal wiring and circuitry.
• Mounting brackets: Provide secure installations for various lighting applications.
• Decorative trims: Enhance the aesthetic appeal of fixtures.
For instance, LED lighting systems use stamped heat sinks to dissipate heat, ensuring long-lasting performance and efficiency.
This combination of versatility and precision makes metal stamping the backbone of lighting innovation.
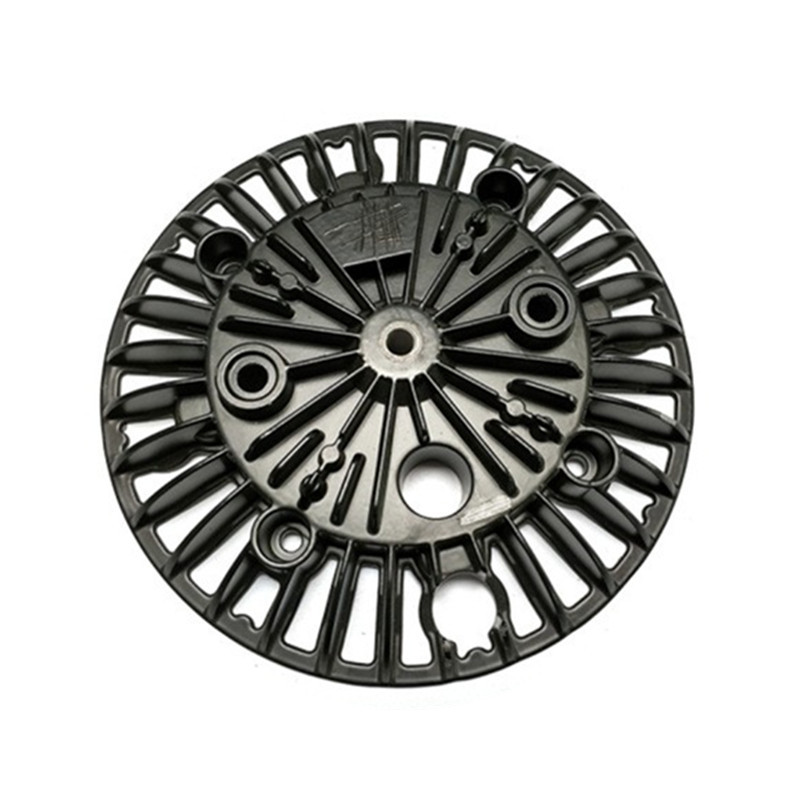
What Are the Benefits of Using Stamped Metal for Lighting Fixtures?
Using stamped metal offers a range of advantages for lighting fixture production, including:
1. Cost-Effectiveness:
Metal stamping reduces production costs by streamlining the manufacturing process.
Automated stamping minimizes labor expenses and material waste, making it an affordable choice for manufacturers.
2. Precision and Consistency:
Modern stamping presses and advanced tooling allow for intricate designs and tight tolerances, ensuring that every part meets exact specifications.
3. Durability:
Stamped metal components are robust and long-lasting, capable of withstanding residential, commercial, and industrial rigors.
4. Customization:
The process supports custom designs, enabling manufacturers to produce unique lighting solutions tailored to client needs or project requirements.
5. Scalability:
Whether producing thousands of identical components or custom pieces for a niche project, metal stamping adapts seamlessly to varying production volumes.
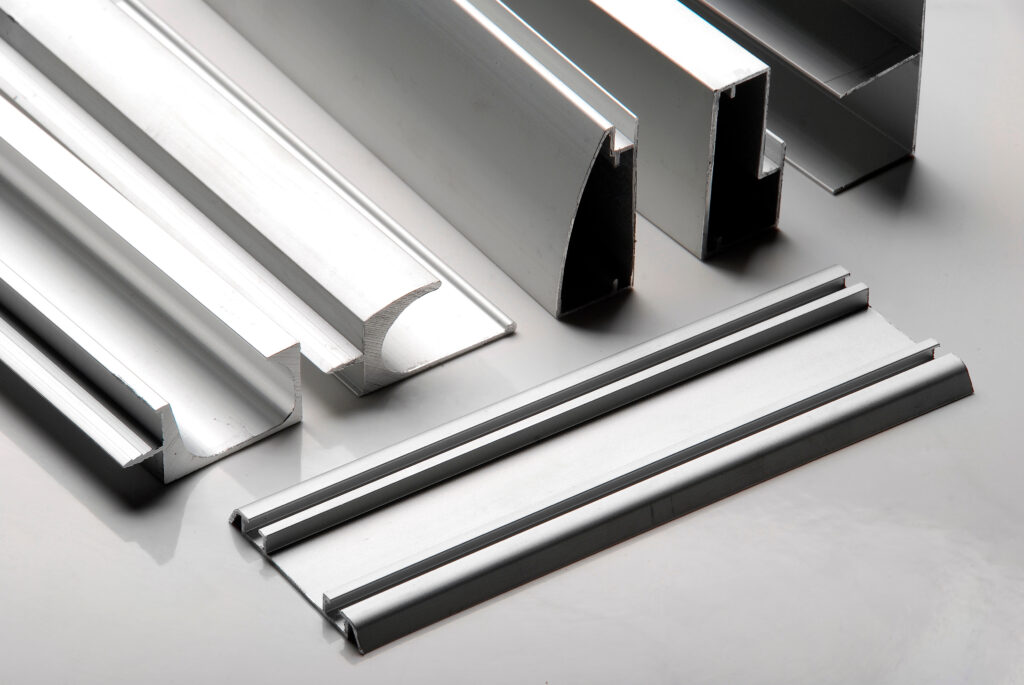
What Types of Lighting Fixtures Use Stamped Components?
Stamped components are integral to many types of lighting fixtures, including:
1. Residential Lighting:
Stamped metal trims and frames are used in chandeliers, sconces, and pendant lights, providing structural support and enhancing aesthetic appeal.
2. Commercial Lighting:
Stamped brackets, reflectors, and housings are common in office lighting, retail spaces, and hospitality environments.
For example, recessed lighting in retail stores often relies on stamped components to ensure a sleek, unobtrusive design.
3. Industrial Lighting:
Heavy-duty stamped components are used in fixtures for warehouses, factories, and other industrial spaces.
These fixtures must withstand harsh conditions while maintaining optimal performance.
4. Outdoor Lighting:
Stamped metal housings and brackets are critical in outdoor fixtures like floodlights and streetlights.
They provide weather resistance and structural integrity, ensuring reliability in extreme conditions.
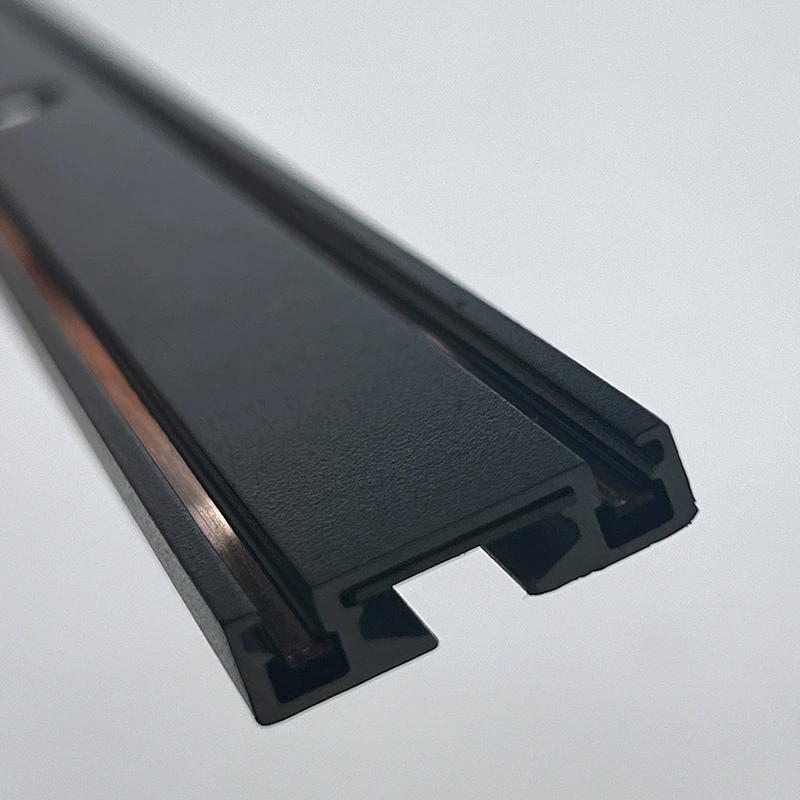
How Does Metal Stamping Improve Cost Efficiency for Manufacturers?
Cost efficiency is a major advantage of using stamped fixtures in lighting production.
Here’s how it works:
1. Efficient Material Usage:
Stamped metal processes optimize material usage, reducing waste and minimizing the cost of raw materials.
2. Reduced Labor Costs:
Automation in metal stamping eliminates the need for intensive manual labor, saving both time and money.
3. Faster Production Cycles:
High-speed stamping machines produce components in large volumes with minimal downtime, accelerating time-to-market for new products.
4. Streamlined Design Adjustments:
Tooling changes for metal stamping are more cost-effective than retooling for casting or machining, making updating designs without significant expense easier.
What Materials Are Commonly Used for Stamped Lighting Fixtures?
The choice of material depends on the application and specific requirements of the lighting fixture. Common materials include:
1. Aluminum:
Lightweight, corrosion-resistant, and highly reflective, ideal for reflectors and housings.
2. Steel:
Durable and strong, commonly used in industrial lighting.
3. Copper:
Excellent for heat sinks due to its thermal conductivity.
4. Brass:
Adds aesthetic value to high-end decorative fixtures.
5. Stainless Steel:
Perfect for outdoor applications due to its weather resistance.
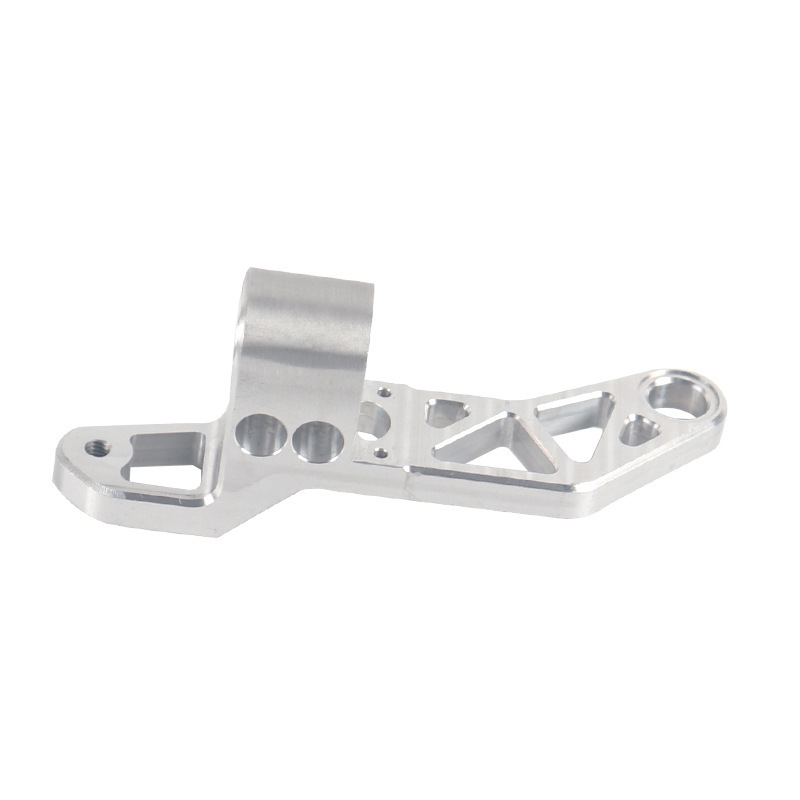
What Are the Advantages of Using Stamped Fixtures in the Lighting Industry
The use of stamped fixtures brings numerous advantages to manufacturers and end users alike:
1. Improved Quality Control:
Precision tooling ensures consistent quality across all production runs.
2. Faster Turnaround:
Efficient production methods reduce lead times, enabling manufacturers to meet tight deadlines.
3. Environmental Benefits:
Metal stamping generates less waste than other manufacturing methods, making it a more sustainable option.
4. Regulatory Compliance:
Stamped components are designed to meet strict industry standards, ensuring safety and reliability.
5. Versatility Across Applications:
Stamped fixtures cater to various lighting needs, from decorative trims to heavy-duty industrial parts.
Trends and Innovations in Stamped Fixtures
The lighting industry continues to evolve, and stamped fixtures are adapting to meet new demands. Trends include:
• Lightweight Designs: Stamped aluminum components create ultra-light fixtures for modern interiors.
• Sustainability: Recycled metals are increasingly used in stamped components to support green manufacturing initiatives.
• Advanced Finishes: New coating technologies improve stamped parts’ aesthetic and functional properties, such as corrosion resistance and enhanced reflectivity.
Manufacturers investing in advanced stamping techniques are better positioned to meet the demands of a rapidly changing industry.
The lighting industry is experiencing remarkable growth.
From design to metal fabrication, LED technology is driving significant market expansion.
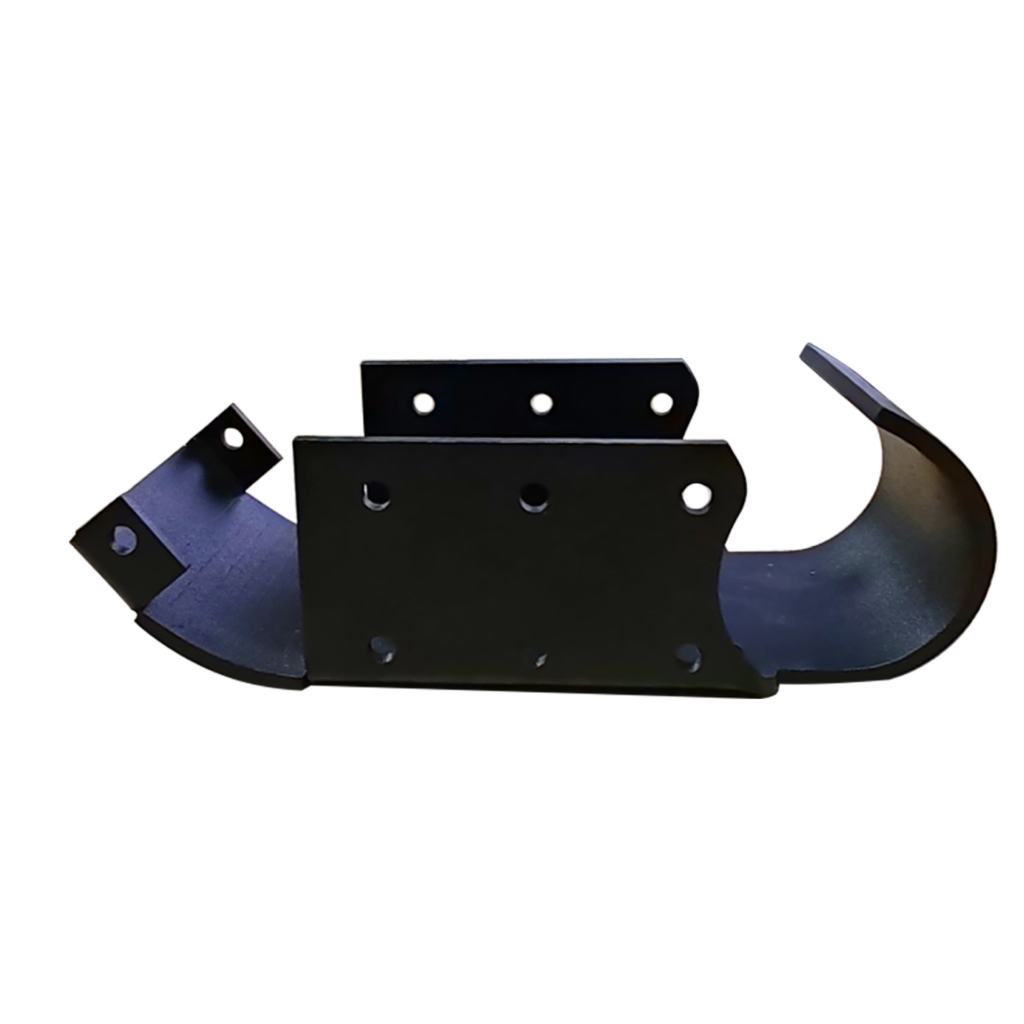
Conclusion
Stamped fixtures are reshaping the lighting industry by providing cost-effective, durable, and customizable solutions for component production.
From residential designs to industrial installations, stamped components cater to a wide range of needs, making them a cornerstone of modern lighting innovation.
By leveraging the benefits of metal stamping, manufacturers can meet the demands of a rapidly evolving market while maintaining efficiency, sustainability, and quality.
Whether you’re a manufacturer or lighting designer, partnering with a trusted stamping provider can help you achieve your goals precisely and efficiently.