Metal fabrication is a critical process in various industries, ranging from automotive and aerospace to construction and consumer electronics.
It involves cutting, bending, and assembling metal structures to create products or parts. The choice of materials in metal fabrication is essential as it impacts the final product’s strength, durability, and cost.
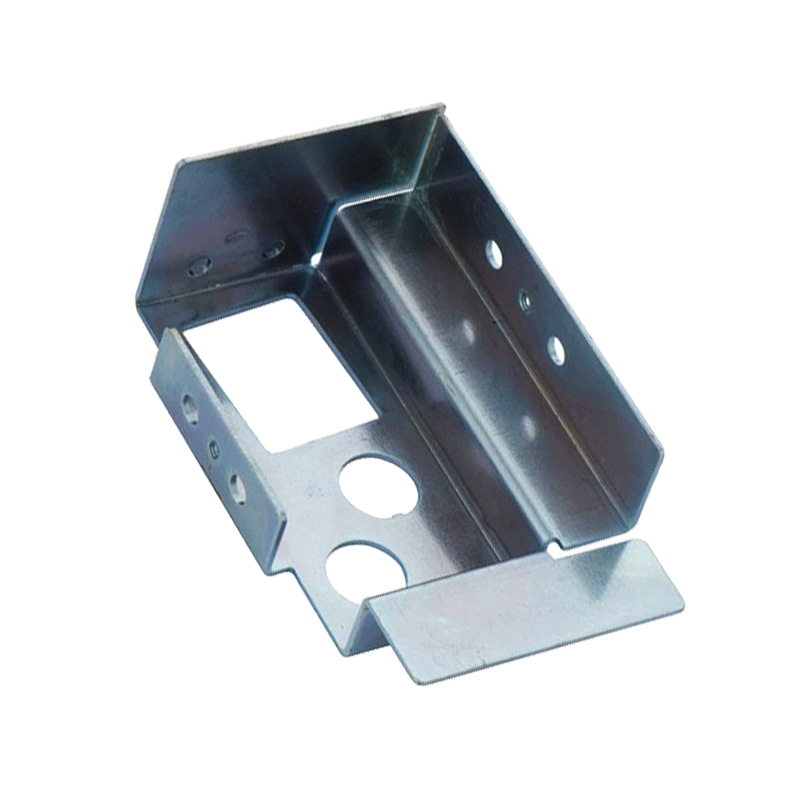
The most commonly used materials in metal fabrication are steel, aluminum, copper, and magnesium. Each of these materials offers unique properties that make them suitable for various applications.
Now, in this article, we will delve deeper into each of these materials and understand their properties and advantages in metal fabrication.
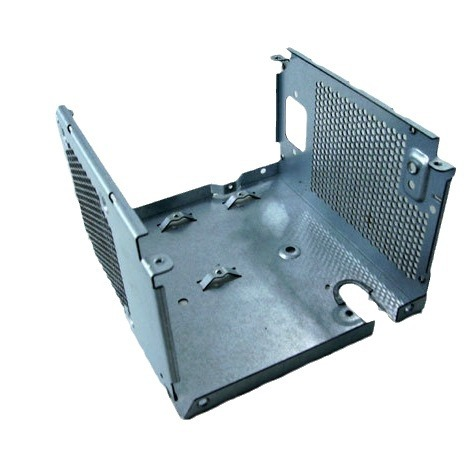
What Are Four Common Materials Used in Metal Fabrication?
The four common materials used in metal fabrication are steel, aluminum, copper, and magnesium. Each material is chosen based on its distinct properties that make it ideal for different applications.
Steel
Properties and Characteristics
Steel is a fundamental material in metal fabrication due to its exceptional strength, durability, and versatility. It is an alloy primarily composed of iron and carbon, with various other elements added to enhance its properties.
The carbon content in steel can vary, leading to different types such as low-carbon, medium-carbon, and high-carbon steel, each with distinct mechanical properties.
Additionally, alloying elements like chromium and nickel can be added to improve corrosion resistance and toughness, resulting in stainless steel and alloy steels.
Advantages and Disadvantages
The primary advantages of steel include its high tensile strength, which allows it to support heavy loads and resist deformation under stress.
It is also relatively affordable and widely available, making it a cost-effective choice for many applications.
However, steel is susceptible to corrosion if not properly treated or coated, which can limit its use in harsh environments unless corrosion-resistant grades are used.
Common Applications
Steel’s robustness and versatility make it suitable for a wide range of applications, from structural components in buildings and bridges to automotive parts and machinery.
It is also used in pipelines, rail tracks, and manufacturing tools due to its ability to withstand high stress and wear.
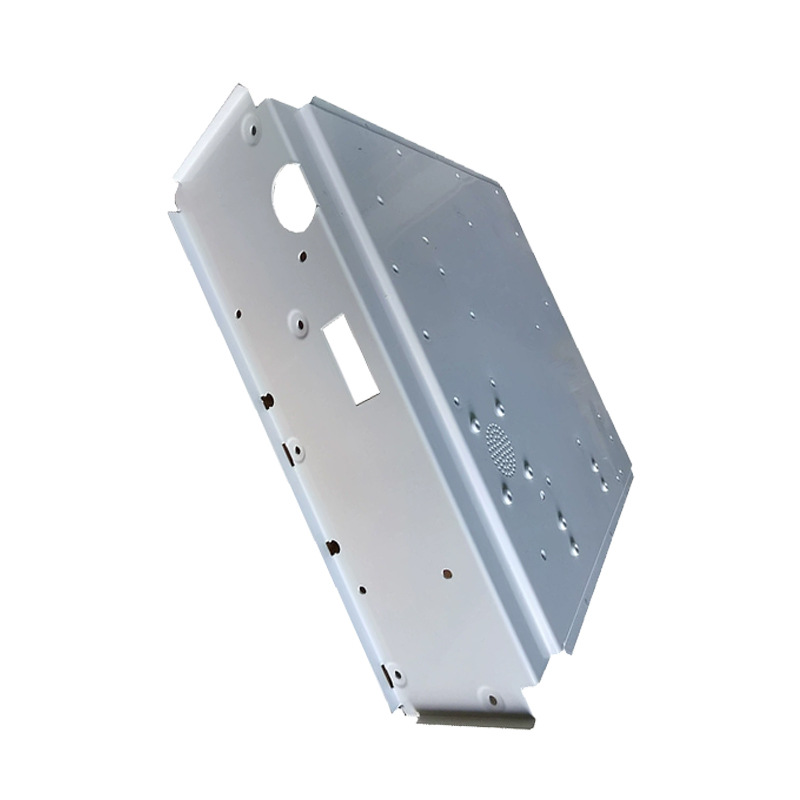
Aluminum
Properties and Characteristics
Aluminum is a lightweight metal known for its excellent corrosion resistance and high thermal and electrical conductivity. It is characterized by its low density, which makes it a preferred material where weight reduction is crucial.
Aluminum is also highly malleable, allowing it to be easily extruded, rolled, or cast into various shapes and forms. Its natural oxide layer provides protection against corrosion, extending its lifespan in many environments.
Advantages and Disadvantages
The primary advantage of aluminum is its low weight, which contributes to increased fuel efficiency in vehicles and aircraft. It is also resistant to corrosion, making it suitable for outdoor and marine applications.
However, aluminum has lower strength compared to steel and can be more expensive, particularly in its alloyed forms. Additionally, its lower hardness means it is less suitable for applications requiring high wear resistance.
Common Applications
Aluminum is extensively used in the aerospace industry for aircraft components, in the automotive industry for lightweight parts, and in construction for window frames and siding.
It is also used in consumer electronics, packaging materials, and heat exchangers due to its excellent thermal conductivity.
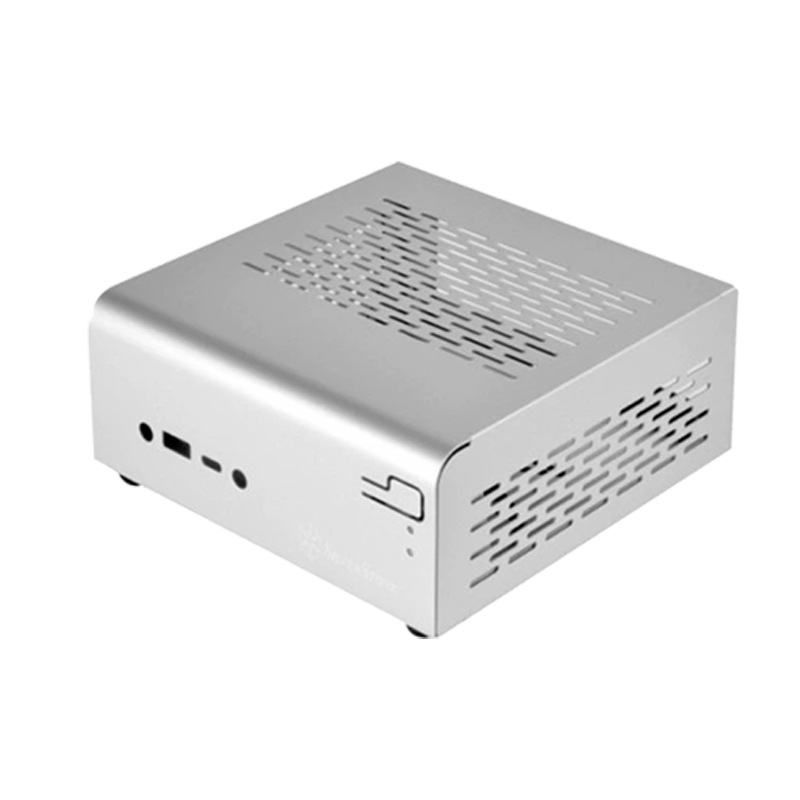
Copper
Properties and Characteristics
Copper is renowned for its superior electrical and thermal conductivity, making it an essential material in electrical and electronic applications.
It is a ductile and malleable metal, allowing it to be drawn into wires or formed into sheets with ease. Copper also possesses natural antimicrobial properties, which make it useful in medical and healthcare applications.
Advantages and Disadvantages
The main advantages of copper include its excellent conductivity, which enhances its performance in electrical wiring and thermal management.
It is also highly durable and resistant to corrosion, particularly in its pure form. However, copper is relatively expensive compared to other metals and can be prone to tarnishing, which may require regular maintenance or coating.
Common Applications
Copper is widely used in electrical wiring, plumbing, and roofing materials. Its alloys, such as brass and bronze, are utilized in decorative applications, musical instruments, and marine hardware. Its antimicrobial properties also make it suitable for use in touch surfaces in healthcare environments.
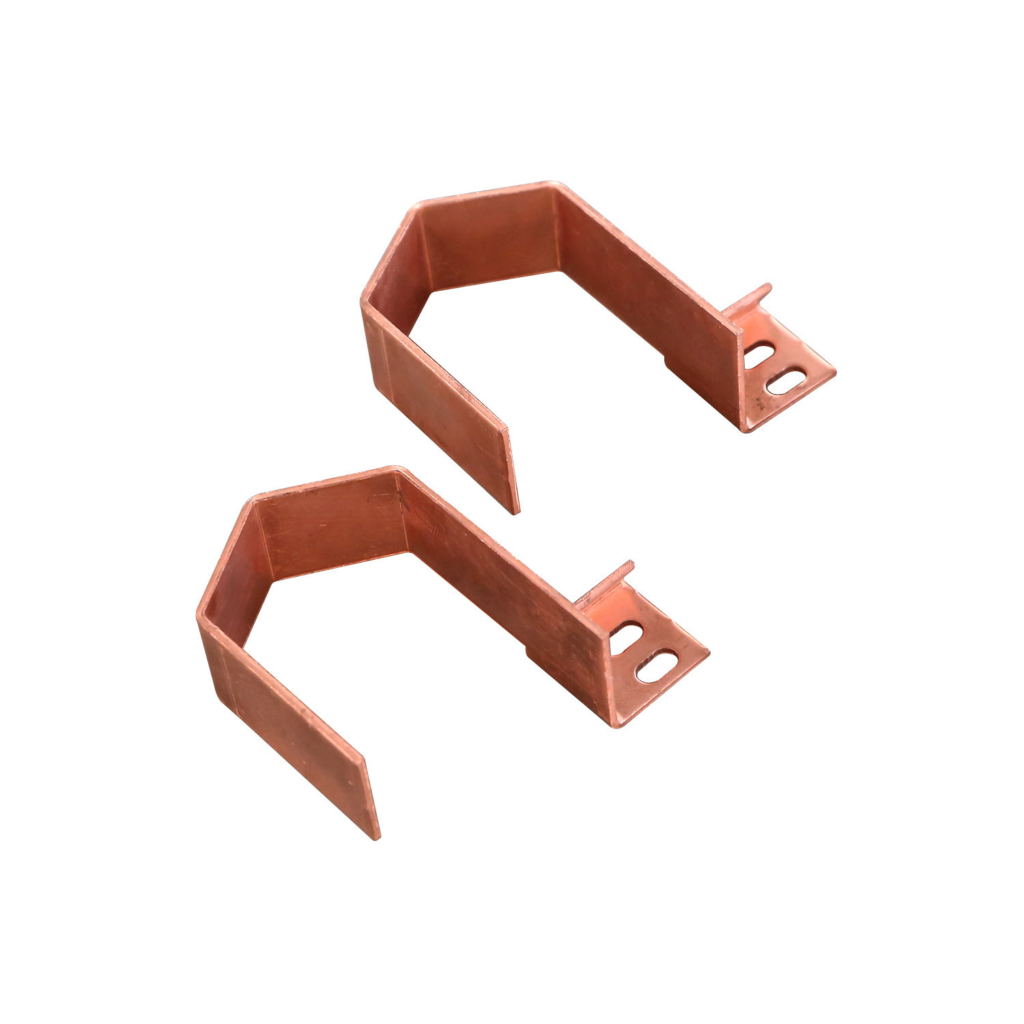
Magnesium
Properties and Characteristics
Magnesium is the lightest structural metal, known for its high strength-to-weight ratio. It is also highly machinable, which facilitates the production of complex shapes and precision parts.
Magnesium alloys are often used in applications where weight reduction is a key consideration. Additionally, magnesium has good thermal conductivity and is less prone to fatigue compared to some other metals.
Advantages and Disadvantages
The primary advantage of magnesium is its low density, which significantly reduces the weight of components and structures. This characteristic is particularly beneficial in the automotive and aerospace industries.
However, magnesium is less resistant to corrosion compared to other metals and can be more prone to flammability if not handled properly. Its relatively high cost compared to some other metals also limits its use in certain applications.
Common Applications
Magnesium is used in the automotive industry for manufacturing lightweight engine components and transmission cases.
It is also employed in consumer electronics for housings and frames, and in aerospace applications where reducing weight is crucial. Additionally, magnesium alloys are used in sporting equipment and military applications.
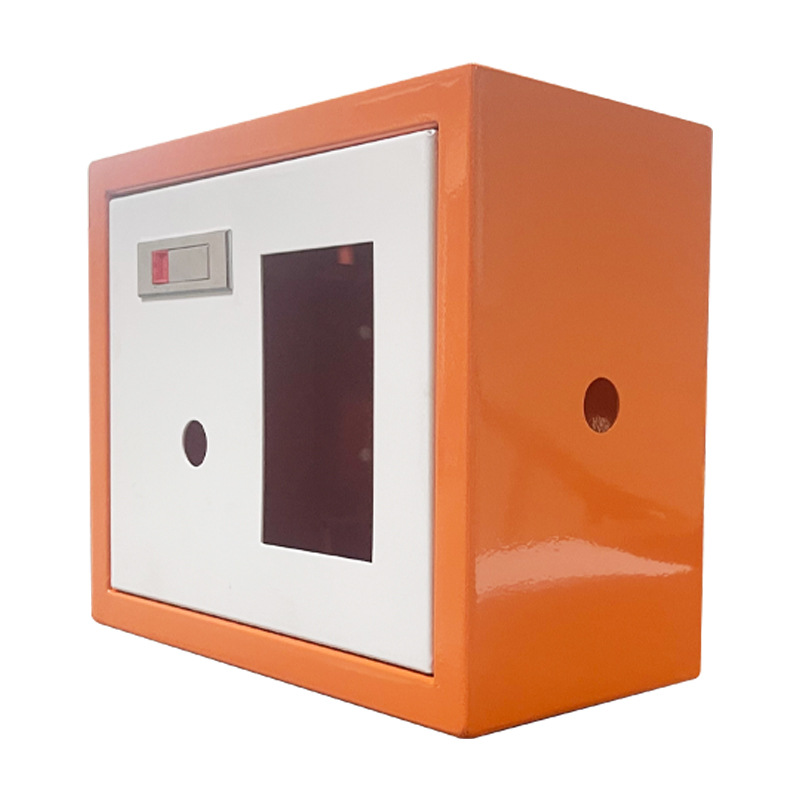
Summary:
In conclusion, the choice of material in metal fabrication is influenced by the specific requirements of the application, including strength, weight, corrosion resistance, and cost.
Steel, aluminum, copper, and magnesium are among the most commonly used materials, each offering unique properties that make them suitable for different industries and applications.
Understanding these materials’ characteristics and advantages is essential for fabricators to make informed decisions and produce high-quality products that meet the demands of modern engineering and manufacturing.