Power supply shells protect electronic components, ensure durability, and manage heat dissipation.
Their quality directly affects the performance and longevity of devices, from consumer electronics to industrial machinery.
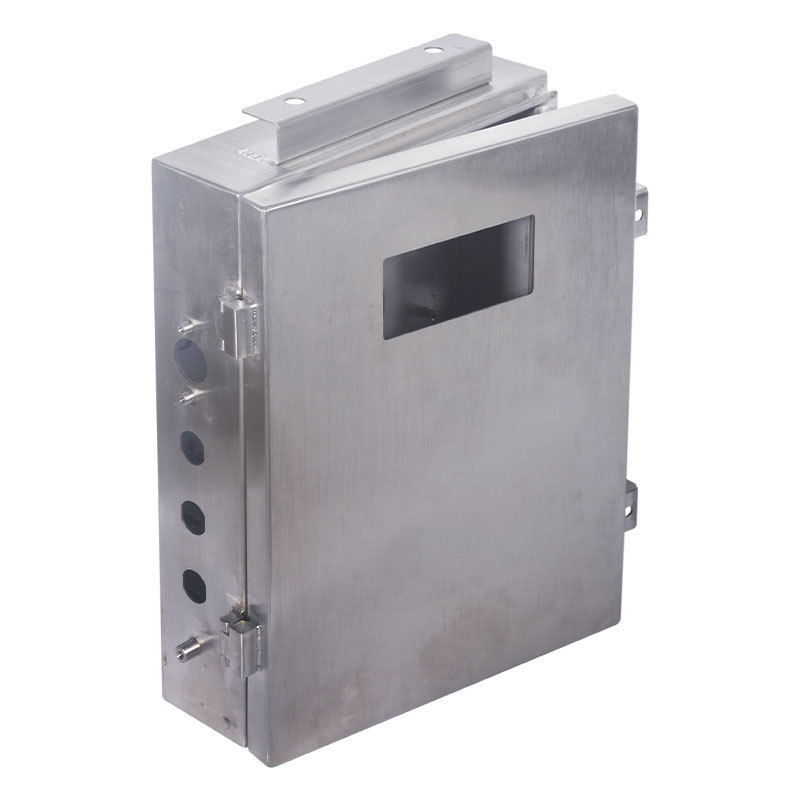
Metal stamped power supply shells are produced by shaping metal sheets into protective enclosures through high-precision stamping techniques.
This method ensures consistent, high-quality results while offering design flexibility and material efficiency.
Whether in automotive, telecommunications, or medical applications, metal stamped shells provide the durability and performance required for today’s demanding environments.
Here, we’ll explore the manufacturing process, material choices, advantages, and the latest innovations in metal stamped power supply shells, along with customization options and sustainability trends shaping the industry.
-
Table Of Contents
-
1. How Are Metal Stamped Power Supply Shells Revolutionizing Modern Electronics?
-
2. What Are Metal Stamped Power Supply Shells?
-
3. How Are Metal Stamped Shells Manufactured?
-
4. Why Choose Metal Stamping for Power Supply Shells?
-
5. Key Applications of Metal Stamped Power Supply Shells
-
6. Innovations in Metal Stamping Technology
-
7. How Metal Stamped Shells Enhance Thermal Performance
-
8. Sustainability & Eco-Friendly Manufacturing in Metal Stamping
-
9. Summary
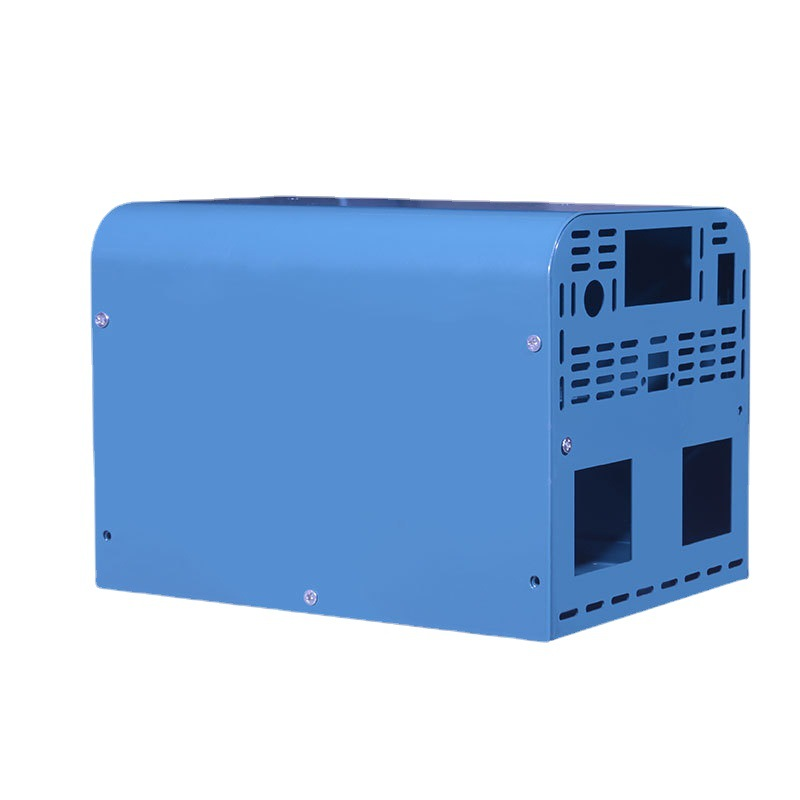
What Are Metal Stamped Power Supply Shells?
Metal stamped power supply shells are protective enclosures formed using high-precision stamping techniques.
These shells serve as the structural foundation for power supply units in various electronic devices, providing:
1. Physical Protection – Shields sensitive components from external damage.
2. Heat Management – Enhances thermal dissipation for optimal performance.
3. Electromagnetic Shielding – Prevents interference with other electronic devices.
The manufacturing process involves multiple steps, including blanking, punching, bending, and piercing, ensuring high accuracy and uniformity across production batches.
With industries demanding lightweight, durable, and cost-efficient solutions, metal stamped shells have become the preferred choice for power supply enclosures.
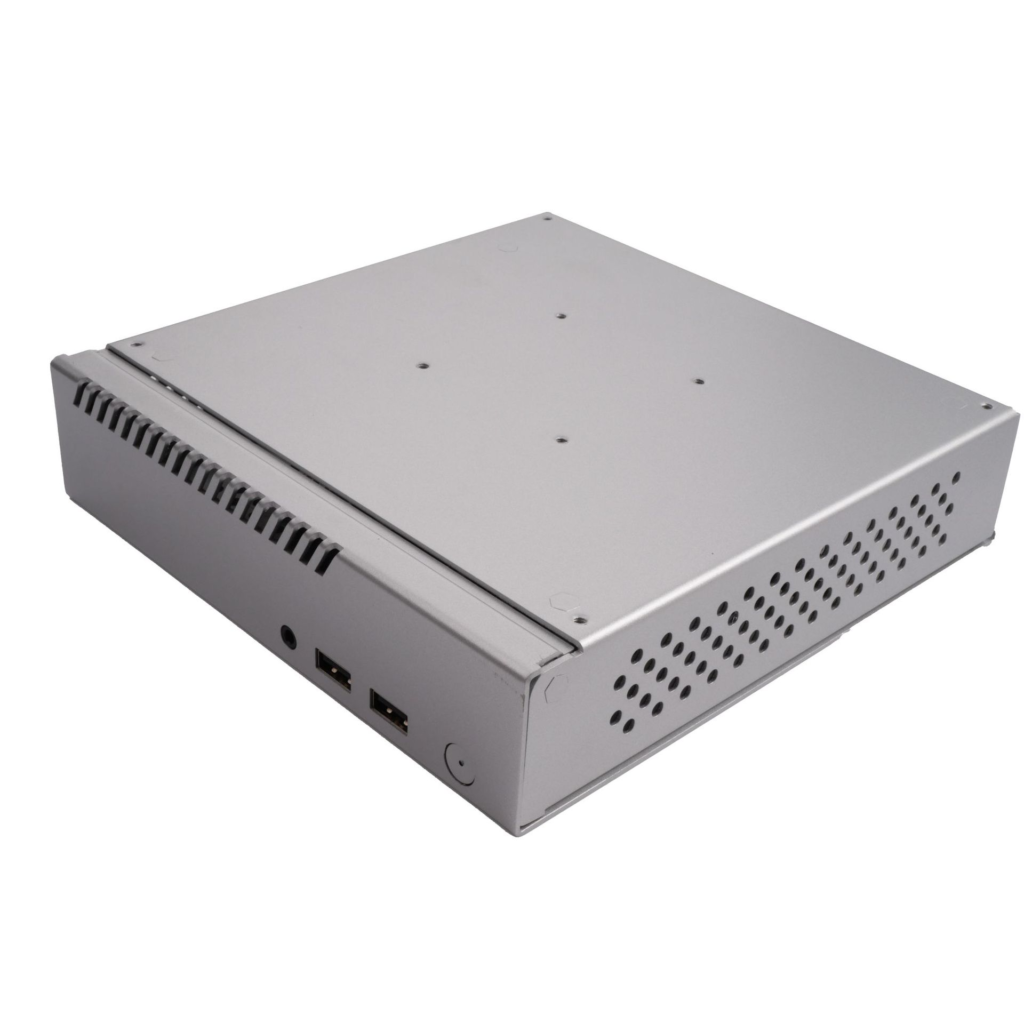
How Are Metal Stamped Shells Manufactured?
The manufacturing process of metal stamped power supply shells follows a structured approach that ensures precision, efficiency, and durability.
Here’s how it works:
1. Material Selection
Choosing the right metal is crucial for the shell’s strength, conductivity, and corrosion resistance. Common materials include:
Aluminum – Lightweight, excellent heat dissipation, corrosion-resistant.
Steel – High strength, cost-effective, widely used in industrial applications.
Copper – Superior electrical conductivity, often used in high-performance electronics.
Alloys – Custom compositions tailored for specific industry needs.
2. Die Design & Preparation
The stamping die acts as a precise mold for shaping the metal.
Progressive dies (for multi-step operations) and compound dies (for single-step operations) are designed based on the complexity of the shell’s shape.
3. Stamping Process
Metal sheets are fed into high-tonnage stamping presses, where the die applies controlled pressure to shape the shell.
Key operations include:
Blanking – Cutting raw metal sheets into predefined shapes.
Bending & Forming – Shaping the metal without breaking its structural integrity.
Piercing & Embossing – Adding features like ventilation holes or branding elements.
4. Secondary Processing
Post-stamping, the shells undergo trimming, deburring, and surface finishing to ensure smooth edges and defect-free surfaces.
Additional treatments may include:
Powder Coating & Plating – Enhancing corrosion resistance.
Anodization (for aluminum shells) – Strengthening the surface and improving aesthetics.
5. Quality Inspection & Testing
Every stamped shell is subjected to rigorous quality checks, including:
Dimensional Accuracy Testing – Using laser scanning for precision verification.
Strength & Durability Tests – Ensuring the shell withstands environmental stresses.
Thermal Performance Evaluation – Assessing heat dissipation efficiency.
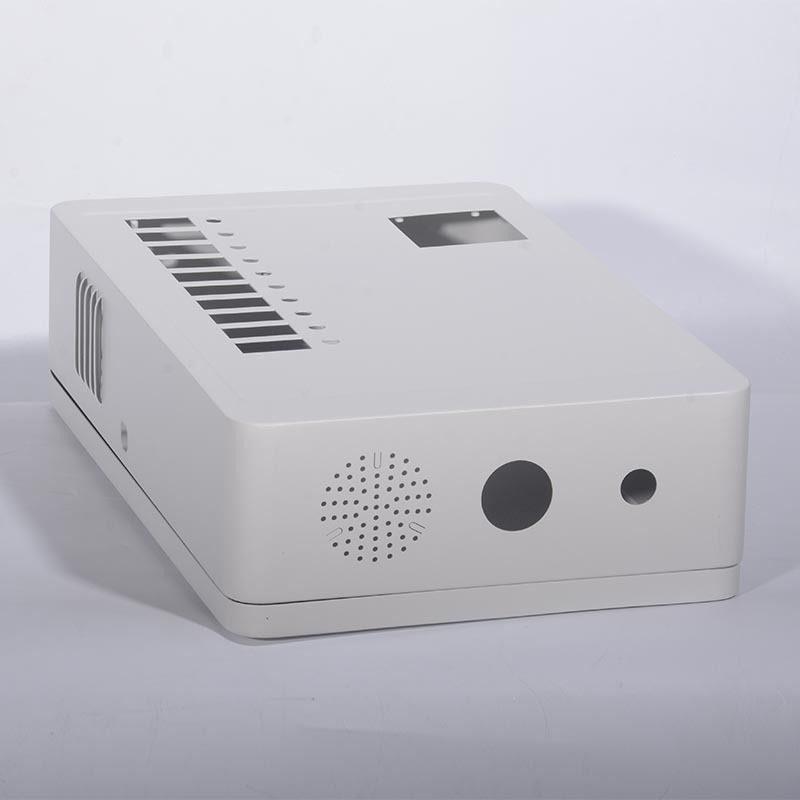
Why Choose Metal Stamping for Power Supply Shells?
Metal stamping is widely preferred due to its efficiency, precision, and scalability.
Here’s why manufacturers opt for this method:
1. Cost-Effective Mass Production
Metal stamping is ideal for high-volume manufacturing, significantly reducing production costs compared to machining or casting.
2. High Precision & Consistency
With advanced die technology, metal stamping ensures identical dimensions across thousands of units, maintaining strict tolerances required in electronics.
3. Durability & Structural Integrity
Stamped shells withstand mechanical stress, temperature variations, and environmental exposure, making them suitable for demanding applications.
4. Material Versatility
Metal stamping supports a wide range of metals and alloys, allowing customization based on application needs.
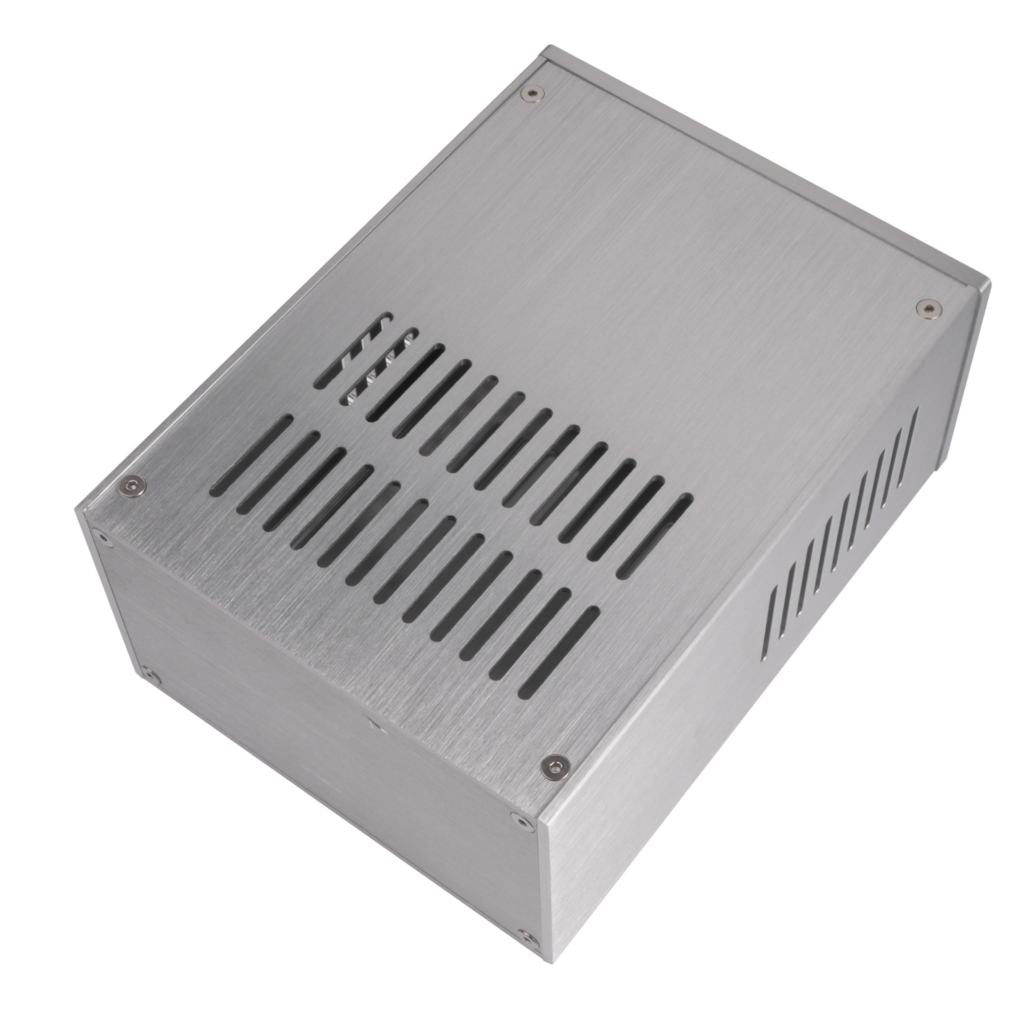
Key Applications of Metal Stamped Power Supply Shells
Metal stamped shells are integral to various industries, ensuring the reliability of power supply units in:
1. Consumer Electronics
Power supply enclosures for laptops, gaming consoles, and smart devices. Lightweight yet durable designs improve portability and longevity.
2. Automotive Industry
Power distribution modules in electric vehicles (EVs). High-strength steel shells enhance impact resistance and thermal performance.
3. Industrial Equipment
Heavy-duty power enclosures for factories and automation systems. Corrosion-resistant coatings extend lifespan in harsh environments.
4. Telecommunications & Networking
Power supply units in data centers, network servers, and telecom towers. Electromagnetic shielding minimizes interference for stable connections.
5. Medical Devices
Power supply casings for diagnostic and monitoring equipment. Non-toxic coatings ensure compliance with medical industry standards.
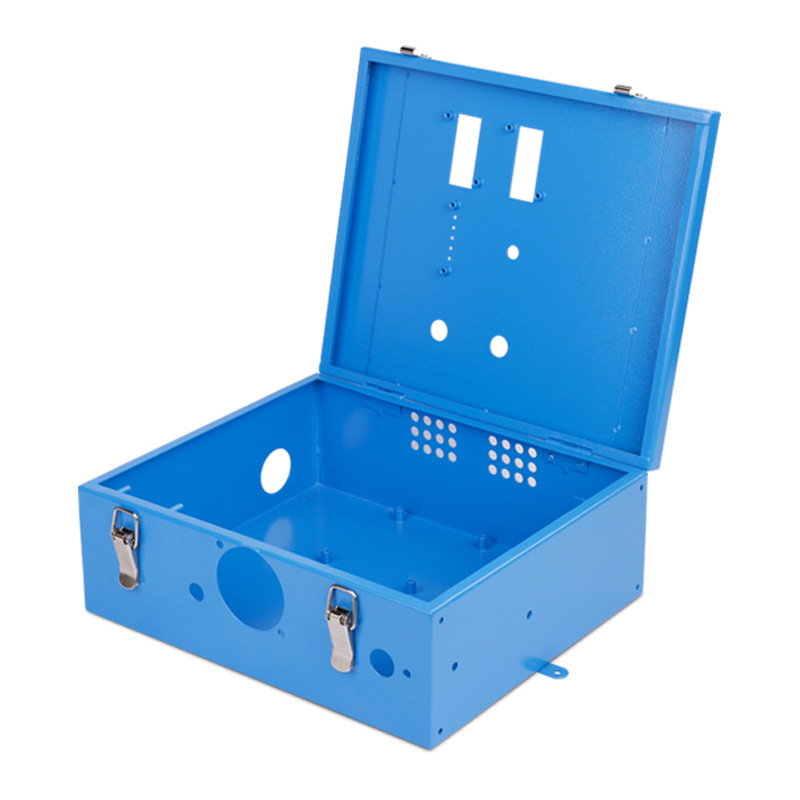
Innovations in Metal Stamping Technology
1. Progressive Die Stamping
Allows multiple operations in a single press cycle, improving efficiency. Ideal for complex, high-volume production.
2. Deep Drawing Techniques
Creates cylindrical and enclosed shapes with high structural integrity. Used in sealed power supply enclosures.
3. Automated & AI-Powered Stamping
Reduces human error and increases production speed. Real-time monitoring ensures quality consistency.
4. Hybrid Manufacturing
Combines laser cutting and stamping for customized designs. Suitable for low-volume, high-precision applications.
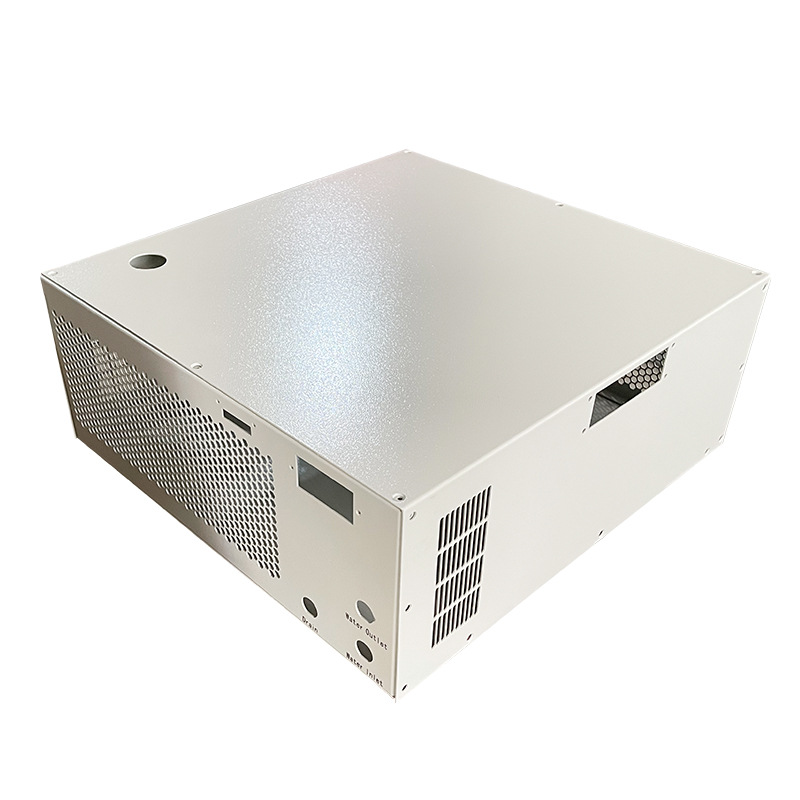
How Metal Stamped Shells Enhance Thermal Performance
One often overlooked aspect of metal stamped power supply shells is their thermal management capabilities.
Efficient heat dissipation is crucial to preventing overheating, component degradation, and system failures.
1. Material Selection – Metals like aluminum and copper offer superior heat conductivity.
2. Ventilation Features – Stamped ventilation holes and cooling fins improve airflow.
3. Surface Treatments – Heat-resistant coatings help manage high-temperature environments.
4. Structural Design – Optimized designs facilitate better heat dissipation in confined spaces.
Thermal considerations are critical in applications such as EVs, data centers, and industrial equipment, where excessive heat can lead to operational inefficiencies or device failures.
Sustainability & Eco-Friendly Manufacturing in Metal Stamping
The metal stamping industry is embracing sustainable practices to reduce its environmental impact:
1. Recycled Metals – Using recycled aluminum and steel minimizes resource consumption.
2. Energy-Efficient Presses – New stamping machines reduce power usage.
3. Eco-Friendly Coatings – Non-toxic finishes eliminate hazardous chemicals.
With increasing regulatory pressures and consumer demand for green manufacturing, sustainability is a key consideration for manufacturers.
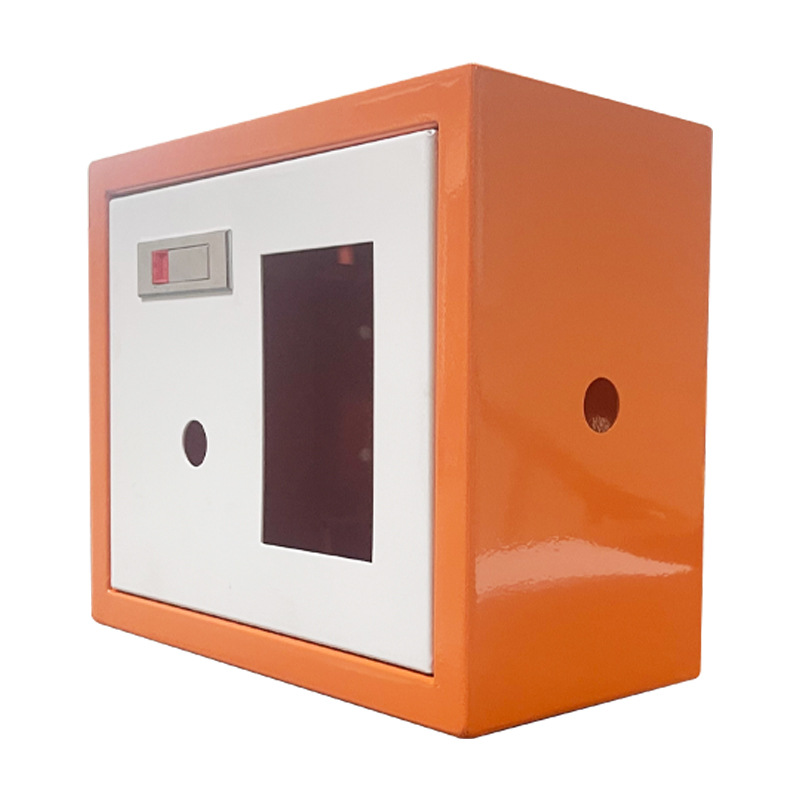
Conclusion
Metal stamped power supply shells offer unparalleled durability, precision, and efficiency, making them a cornerstone of modern electronics.
With advancements in AI-driven automation, hybrid manufacturing, and sustainable practices, the industry is poised for further innovation and growth.
Looking for a customized power supply shell solution? Work with expert manufacturers to optimize design, material selection, and cost efficiency.