Selecting the ideal material for sensor components is crucial for ensuring optimal performance, longevity, and cost-efficiency.
Manufacturers, engineers, and businesses must weigh factors such as durability, corrosion resistance, weight, and strength to determine the best fit for their applications.
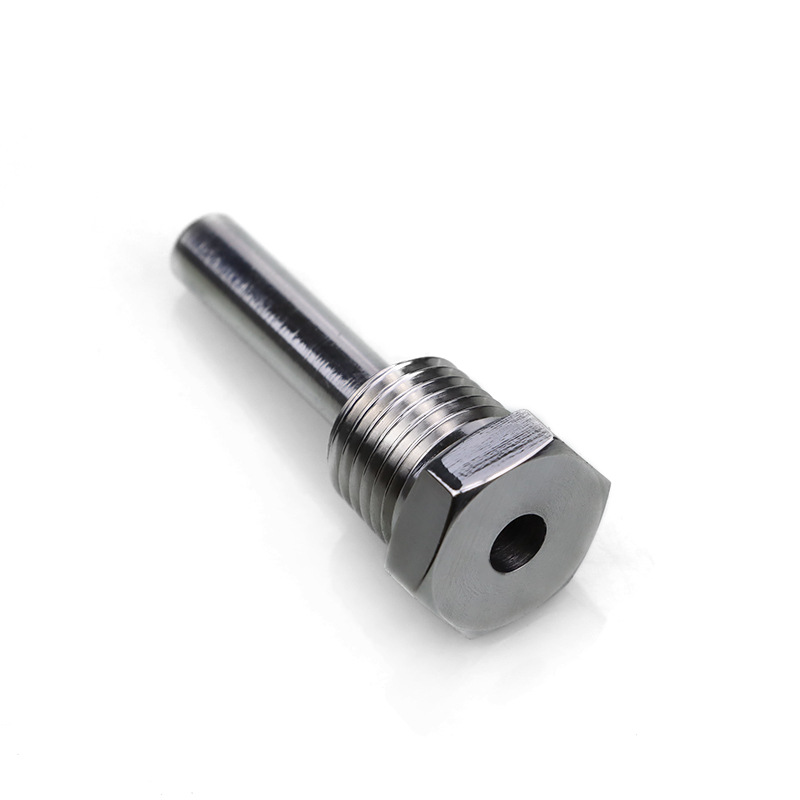
Among various materials, aluminum is one of the most versatile materials in sensor technology, known for its excellent combination of lightweight properties, strength, and corrosion resistance.
However, compared to materials like stainless steel, polymers, and other metals, it has distinct advantages and limitations that must be considered in specific applications.
In this article, we will compare the durability of aluminum with other materials commonly used in sensor components, such as stainless steel, polymers, steel, copper, and brass, to comprehensively understand their respective strengths and weaknesses.
-
Table Of Contents
-
1. How does the durability of aluminum compare to other materials in sensor components?
-
2. General comparison between aluminum and other common materials
-
3. How does aluminum compare to stainless steel in durability?
-
4. How does aluminum compare to polymers in sensor components?
-
5. How does aluminum perform against steel in sensor?
-
6. Aluminum vs. other non-ferrous metals: copper, brass, and titanium
-
7. Factors to consider: cost, weight, and corrosion resistance
-
8. Summary
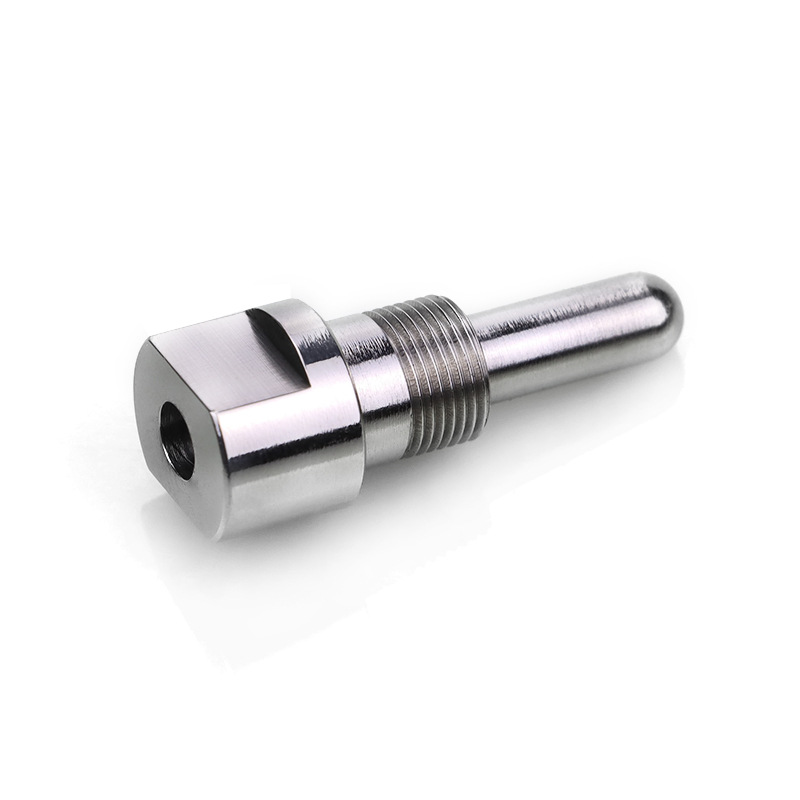
General comparison between aluminum and other common materials
Aluminum is a versatile sensor technology material, offering a remarkable balance between weight, strength, and conductivity.
Compared to traditional materials like stainless steel and copper, aluminum presents unique advantages that make it increasingly popular in various industrial applications.
Material | Corrosion Resistance | Strength (MPa) | Typical Use Cases | Longevity (Years) |
Aluminum | Moderate | 70-700 | Automotive, aerospace, electronics | 10-20 |
Stainless Steel | High | 500-900 | Harsh environments, food industry | 15-30 |
Copper | Low | 210-400 | Electrical applications | 5-10 |
Plastic | Varies | 30-100 | Consumer electronics | 3-7 |
“In precision manufacturing, material selection is about finding the perfect balance between performance, cost, and durability.” – Partzcore Engineering Team
Although aluminum may not always have the best performance in terms of corrosion resistance, strength, and lifespan, overall, it is most suitable for use in manufacturing precision instruments such as sensors.
At Partzcore’s CNC Machining Service, we firmly believe that material selection is an art and a science. Our experts carefully evaluate each component’s requirements for maximum durability and performance.
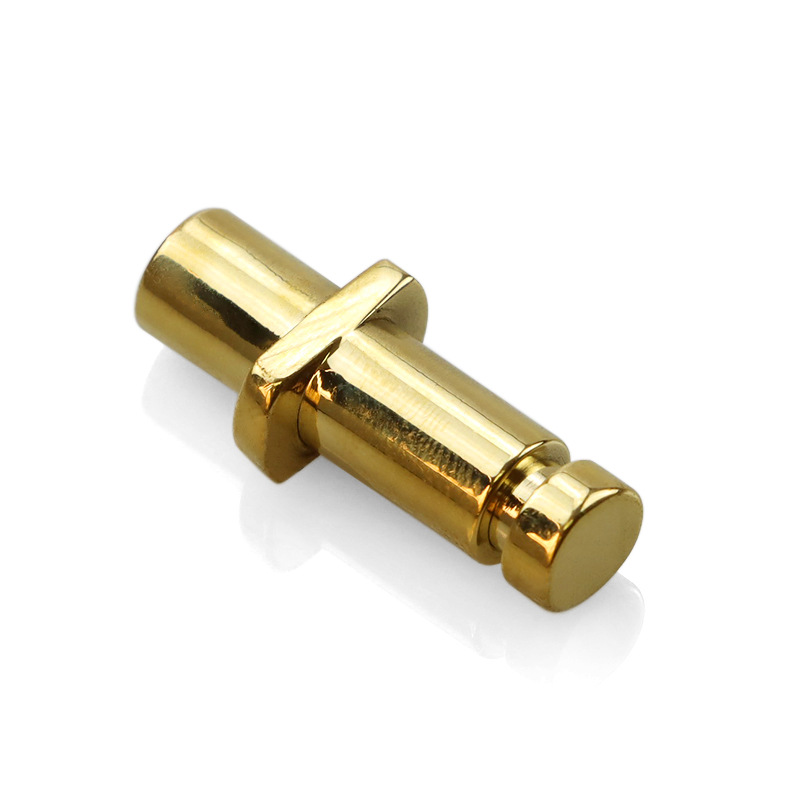
How does aluminum compare to stainless steel in durability?
When discussing durability, aluminum and stainless steel stand out as two of the most commonly used materials, but they serve different purposes depending on the application.
• Aluminum:
While lightweight and corrosion-resistant, aluminum is softer than stainless steel and can be more prone to physical damage, such as dents or scratches over time.
It performs well in environments where weight is a primary concern, such as in aerospace sensors or portable electronic devices.
• Stainless Steel:
On the other hand, stainless steel is much stronger and more resistant to wear and tear. It performs better in high-stress applications and environments with extreme heat or chemical exposure.
For example, 316-grade stainless steel is commonly used in marine and industrial sensor applications because of its resistance to rust and ability to withstand harsh environments.
In conclusion, stainless steel outperforms aluminum in high-stress applications due to its higher tensile strength and impact resistance.
For lightweight designs, aluminum’s superior strength-to-weight ratio makes it a more practical choice.
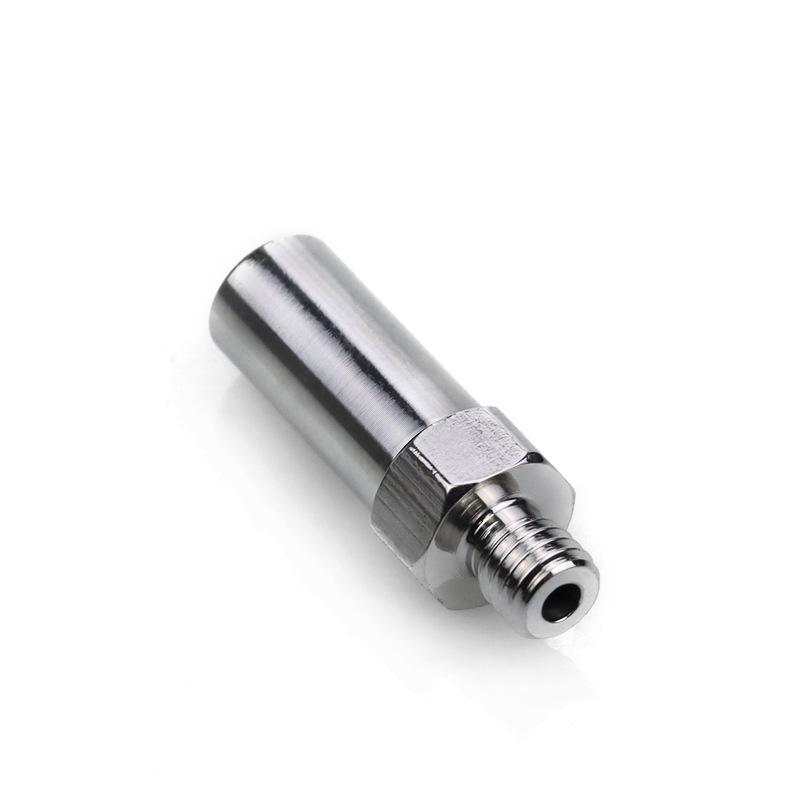
How does aluminum compare to polymers in sensor components?
Polymers, including plastics and composite materials, are increasingly used in sensor components due to their low cost and flexibility.
However, they differ significantly from aluminum in terms of durability and functionality:
Polymers:
• Advantages
o Lightweight and easy to mold into complex shapes.
o Cost-effective for mass production, especially in low-stress applications.
o Electrical insulation properties, making them suitable for electronics.
• Limitations
o Prone to degradation under UV light and chemical exposure.
o Lower tensile strength and impact resistance compared to aluminum.
o Susceptible to thermal deformation at high temperatures.
Aluminum:
• Advantages
o Aluminum provides far greater structural strength than polymers, allowing it to endure physical stress and environmental challenges.
o It remains stable in a wider temperature range, making it suitable for sensors used in high-heat or freezing conditions.
o Unlike polymers, aluminum does not become brittle over time or lose its properties in harsh environments.
In brief, polymers are best suited for applications requiring lightweight, non-load-bearing components, such as casings for handheld sensors.
Aluminum excels in structural components that demand greater strength and thermal stability.
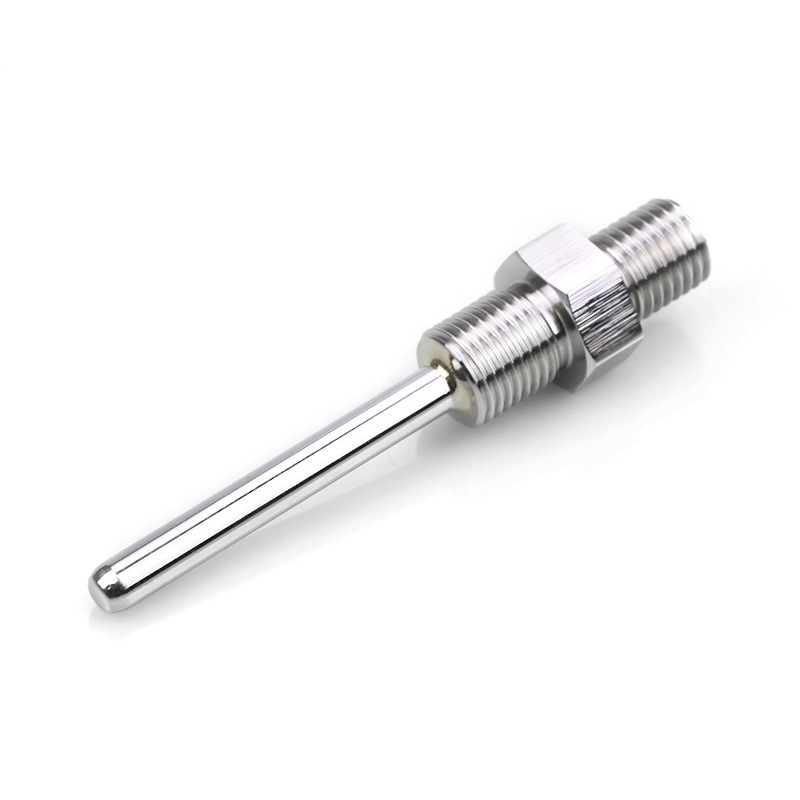
How does aluminum perform against steel in sensor?
Steel is another popular choice in industrial applications, but how does it measure up against aluminum in durability and utility?
Strength Comparison:
• Tensile Strength: Steel typically has a tensile strength of 400–500 MPa, while aluminum varies from 70 to 700 MPa. This means steel can bear significantly greater loads before failure.
• Impact Resistance: Steel’s hardness and resistance to deformation give it a clear edge over aluminum in impact-heavy applications.
Advantages of Aluminum Over Steel:
1. Weight: Aluminum is roughly three times lighter than steel. This weight reduction can lead to lower energy consumption in transportation and easier handling during manufacturing.
2. Corrosion Resistance: Unlike steel, which requires protective coatings to resist rust, aluminum forms a natural oxide layer that prevents corrosion.
3. Thermal Conductivity: Aluminum is approximately four times more thermally conductive than steel. This property makes it particularly useful in sensor components that require efficient heat dissipation.
Steel is ideal for heavy-duty applications such as structural supports and high-load environments. Aluminum shines in applications where weight savings, thermal management, or corrosion resistance are essential, such as aerospace, electronics, and marine industries.
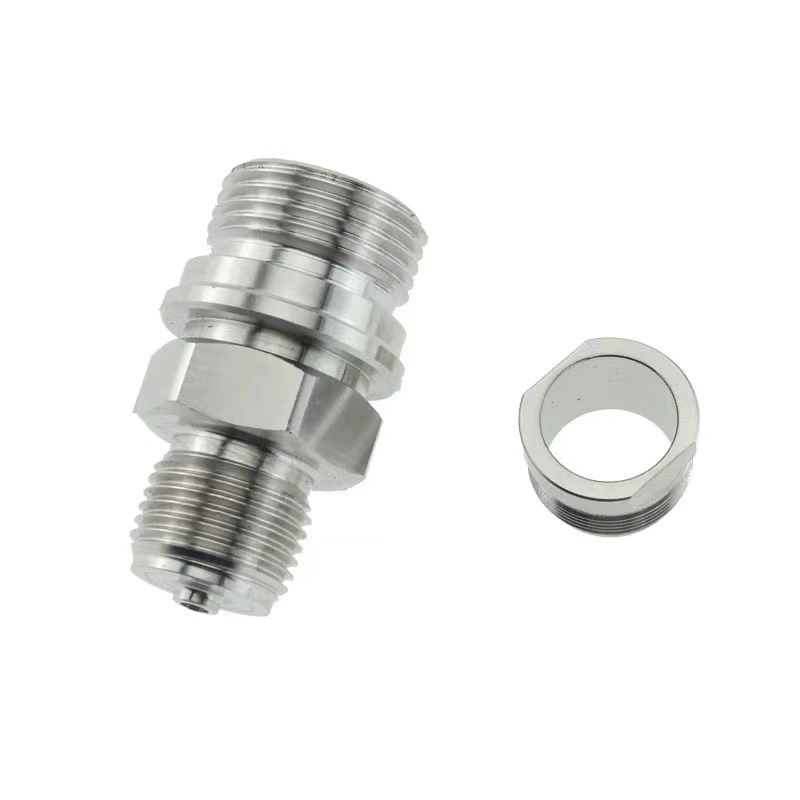
Aluminum vs. other non-ferrous metals: copper, brass, and titanium
Other non-ferrous metals, such as copper, brass, and titanium, also compete with aluminum in various applications. Let’s explore how aluminum compares:
Aluminum vs. Copper:
• Advantages of Copper:
o Superior electrical and thermal conductivity.
o Excellent corrosion resistance, especially in marine environments.
• Advantages of Aluminum:
o Much lighter and more affordable than copper.
o While copper is better for conductivity, aluminum’s lower cost makes it more practical for large-scale applications, such as heat sinks or housings for electrical components.
Aluminum vs. Brass:
• Advantages of Brass:
o High machinability and moderate corrosion resistance.
o Often used for decorative or functional components due to its aesthetic appeal.
• Advantages of Aluminum:
o Aluminum is far lighter and less expensive than brass, making it better suited for applications requiring mobility or large-scale production.
Aluminum vs. Titanium:
• Advantages of Titanium:
o Exceptional strength-to-weight ratio and biocompatibility.
o Superior corrosion resistance, especially in harsh chemical environments.
• Advantages of Aluminum:
o Titanium is significantly more expensive than aluminum, limiting its use to specialized industries like aerospace and medical devices.
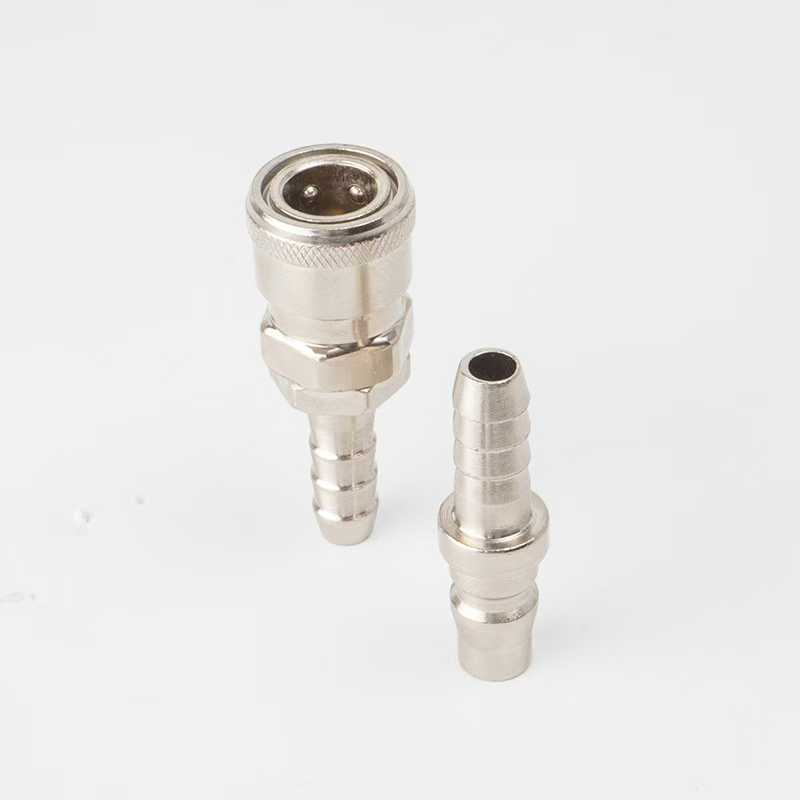
Factors to consider: cost, weight, and corrosion resistance
Choosing the right material involves balancing multiple factors:
1. Cost: Aluminum is more cost-effective than stainless steel, copper, or titanium, making it a preferred choice for budget-conscious projects.
2. Weight: Aluminum’s lightweight nature makes it indispensable in applications where weight reduction is critical, such as drones, robotics, and portable sensors.
3. Corrosion Resistance: Aluminum’s natural oxide layer provides excellent corrosion resistance, though stainless steel still outperforms it in environments with high salt or chemical exposure.
4. Environmental Impact: Aluminum is recyclable and energy-efficient to process, making it a sustainable choice.
By leveraging advanced CNC milling techniques, manufacturers can enhance aluminum’s natural properties, creating sensors that withstand challenging environments.
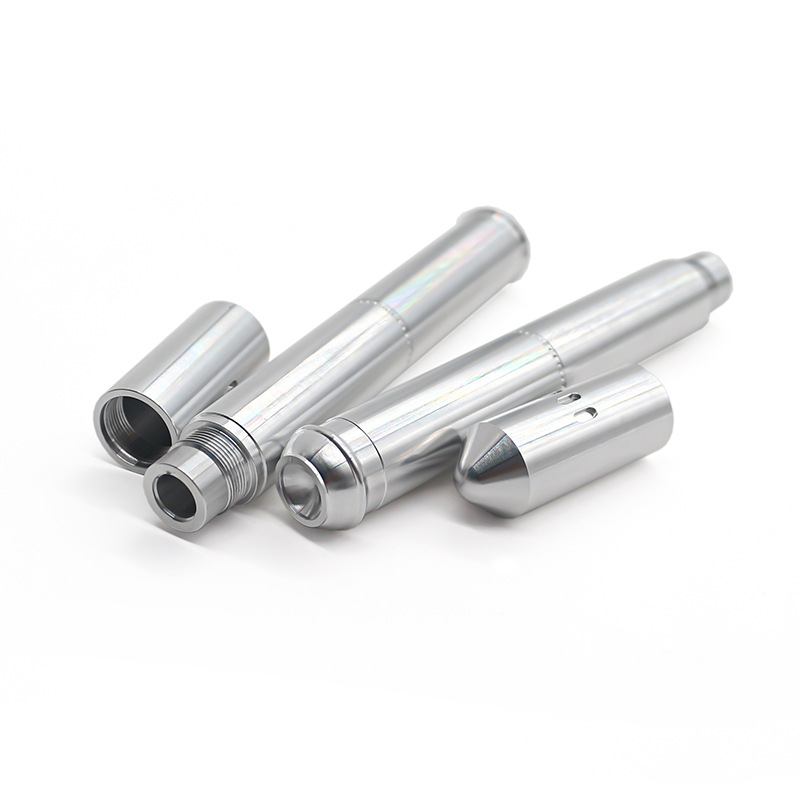
Conclusion
In summary, aluminum offers a compelling balance of durability, weight savings, and corrosion resistance, making it an excellent choice for sensor components.
While stainless steel, polymers, steel, and other materials have advantages, aluminum often provides the best combination of performance and cost-effectiveness.
When selecting a material, it is crucial to consider the specific application requirements, including strength, environmental conditions, and budget.
By understanding the unique properties of each material, manufacturers and engineers can make informed decisions that optimize performance and longevity.