CNC machining has revolutionized the manufacturing industry, enabling engineers and designers to create complex and precise parts with incredible accuracy.
From automotive and aerospace industries to medical and electronics, CNC machined parts play a crucial role in various sectors.
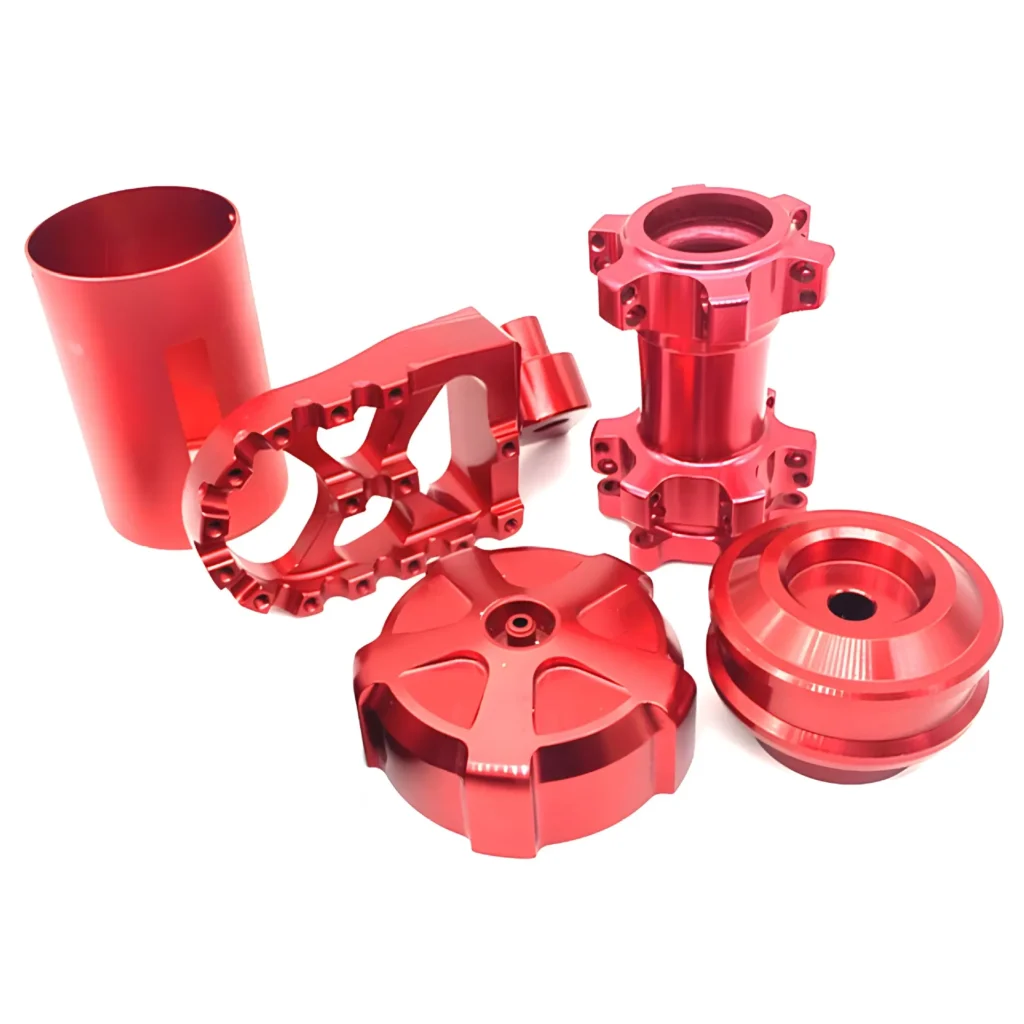
Generally, the accuracy parameters of CNC machined parts mainly include tolerance, repeatability and surface finish. And the factors that affect precision include machine quality, tooling, material properties, environmental conditions, and operator skills.
By understanding these parameters and factors, we can pay much attention to these aspects in the production process of parts and improve their quality.
In this guide, we will focus on the critical aspect of precision in CNC machined parts, exploring accuracy parameters, factors affecting precision, and methods to enhance precision.
-
Table Of Contents
-
1. Mastering Precision: A Comprehensive Guide to CNC Machined Parts
-
2. What are Advantages of CNC Machining?
-
3. Understanding Precision Parameters
-
4. What are the Factors Affecting Precision?
-
5. How to Enhance Precision in CNC Machining?
-
6. How to Choose the Right CNC Machining Service Provider
-
7. Summary
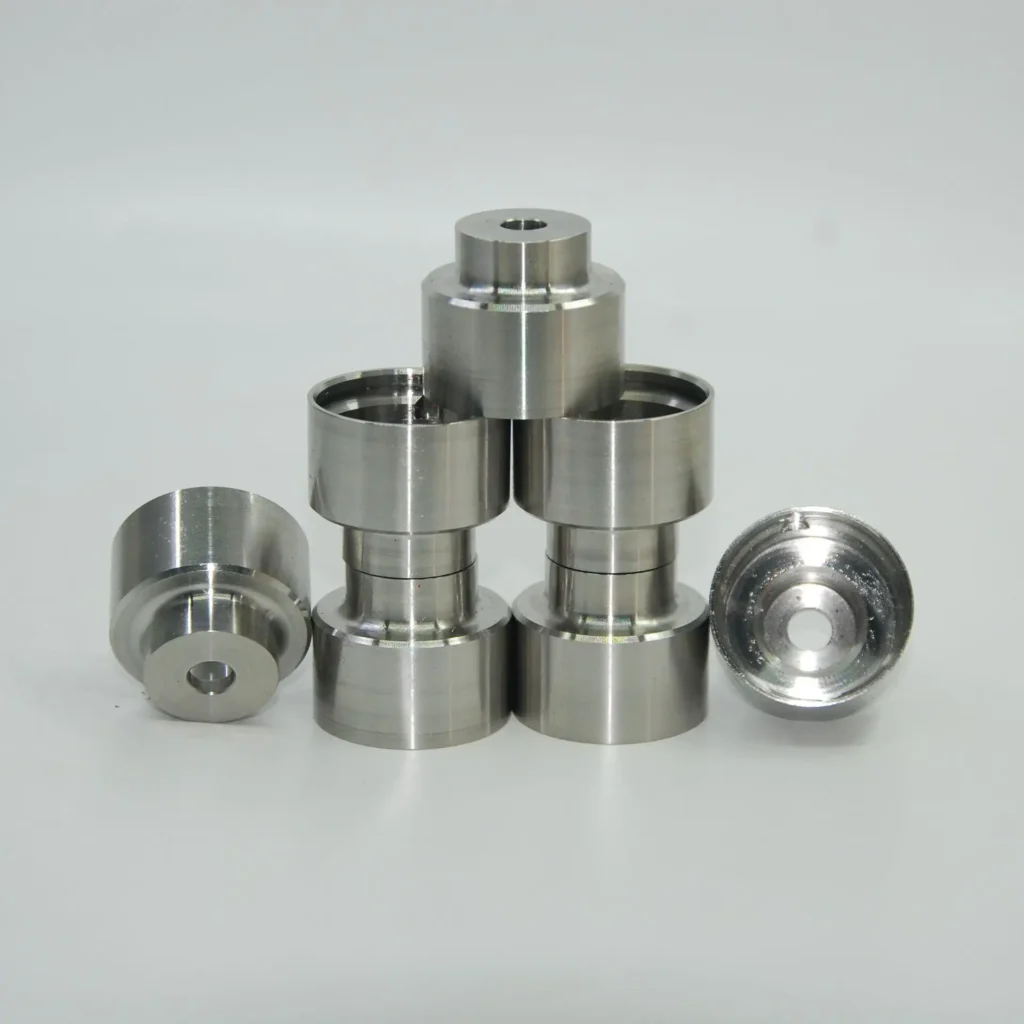
What are Advantages of CNC Machining?
CNC machining offers numerous advantages over traditional manufacturing methods. One of the key benefits is the high precision it offers. CNC machines can produce parts with incredible accuracy, often reaching tolerances as low as 0.001 inches. This level of precision is difficult to achieve with manual machining processes.
Another advantage of CNC machining is its ability to produce complex parts with ease. The use of computer programming allows for intricate designs to be executed consistently and efficiently. This capability is particularly valuable in industries such as aerospace and medical, where intricate components are often required.
Cost-effectiveness is also a significant advantage of CNC machining. While the initial investment in CNC machines may be higher than traditional machines, the long-term savings can be substantial. CNC machines can operate continuously, reducing labor costs and increasing productivity.
Understanding Precision Parameters
Precision in CNC machining refers to the degree of accuracy with which parts are manufactured. The key parameters include:
1. Tolerance: Tolerance indicates the allowable deviation from the specified dimensions. It is typically expressed in thousandths of an inch (mils) or micrometers (µm). Tight tolerances (e.g., ±0.001 inches) are crucial for high-precision components.
2. Repeatability: This measures the machine’s ability to produce the same part multiple times with minimal variation. High repeatability ensures consistent quality in batch production.
3. Surface Finish: The smoothness of a part’s surface is vital in applications where friction or aesthetics are important. Surface finish is measured in microinches (µin) or micrometers (µm), with lower values indicating smoother surfaces.
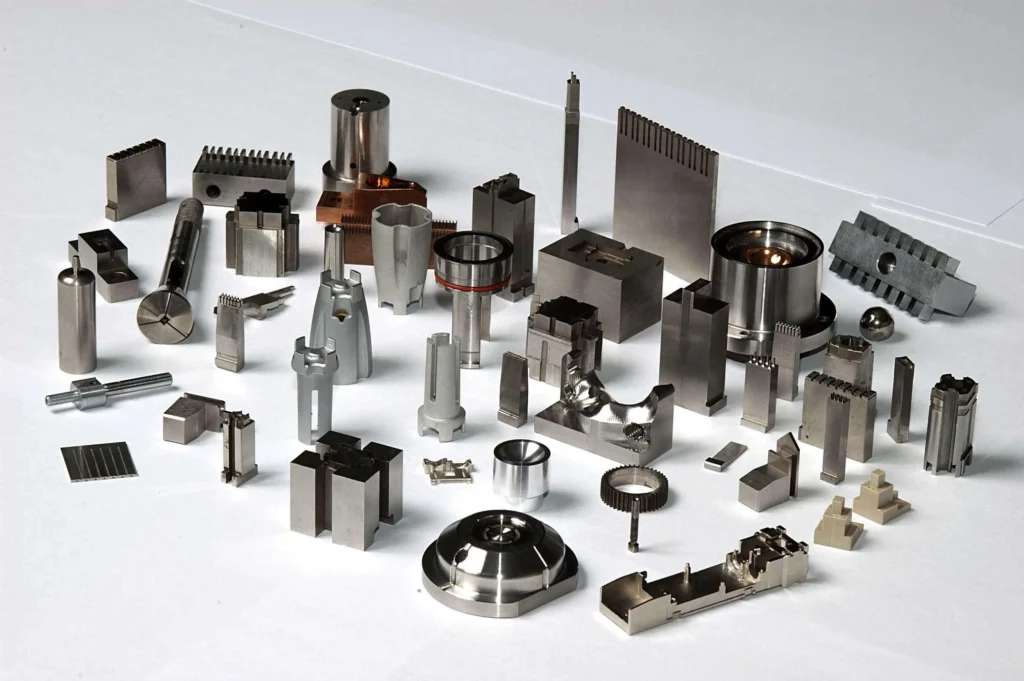
What are the Factors Affecting Precision?
Several factors can affect the precision of CNC machined parts:
1. Machine Quality: The build and maintenance of the CNC machine significantly impact precision. High-quality machines with rigid structures and accurate positioning systems offer better precision.
2. Tooling: The selection and condition of cutting tools affect the accuracy of the machined parts. Sharp, high-quality tools with appropriate coatings reduce errors and improve surface finish.
3. Material Properties: Different materials react differently to machining processes. For instance, metals like aluminum and steel have distinct hardness and thermal properties that influence machining precision.
4. Environmental Conditions: Temperature fluctuations and vibrations can lead to dimensional changes and affect precision. Controlled environments minimize these impacts.
5. Operator Skill: Skilled operators with a deep understanding of CNC programming and machine operation can optimize settings and troubleshoot issues, enhancing precision.
How to Enhance Precision in CNC Machining?
To achieve high precision in CNC machined parts, consider the following methods:
1. Machine Calibration and Maintenance: Regular calibration ensures that the machine’s axes and spindle are accurately aligned. Routine maintenance, including lubrication and component checks, prevents wear and tear that can degrade precision.
2. Advanced Tooling: Using high-quality, coated cutting tools designed for specific materials can improve precision. Additionally, employing tool holders that reduce vibration and deflection enhances accuracy.
3. Optimized Programming: Advanced CNC programming techniques, such as high-speed machining and trochoidal milling, reduce tool pressure and heat generation, resulting in more precise parts.
4. Environmental Control: Maintaining a stable temperature and minimizing vibrations in the machining environment helps maintain dimensional stability.
5. Inspection and Feedback: Implementing rigorous inspection protocols using coordinate measuring machines (CMMs) and other metrology tools ensures parts meet specified tolerances. Feedback from inspection results can guide adjustments to the machining process.
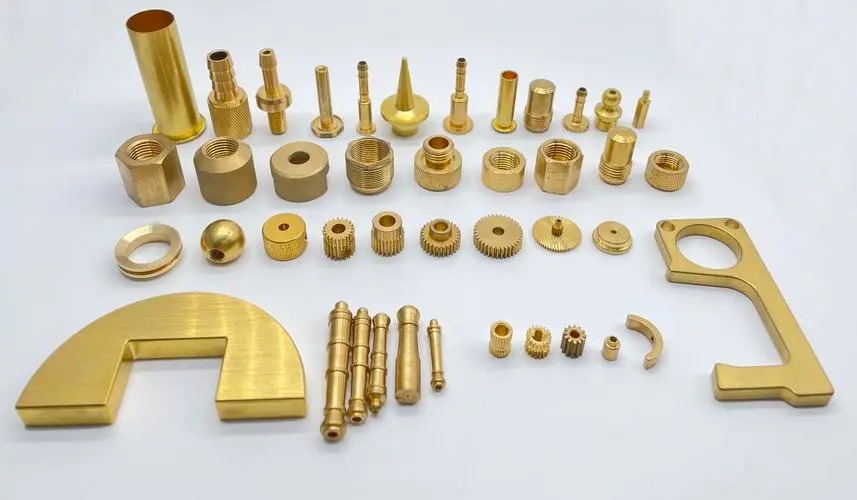
How to Choose the Right CNC Machining Service Provider
When it comes to CNC machining, choosing the right service provider is essential for achieving high-quality results. Here are some factors to consider when selecting a CNC machining service provider:
1. Experience and expertise: Look for a service provider with extensive experience in CNC machining and a track record of delivering high-quality parts. Experienced providers are more likely to have the knowledge and skills to tackle complex projects effectively.
2. Capabilities and equipment: Evaluate the provider’s capabilities and equipment to ensure they can handle your specific project requirements. Consider factors such as the types of CNC machines they have, the range of materials they can work with, and their capacity for production.
3. Quality control processes: Inquire about the provider’s quality control processes to ensure that they have robust systems in place to maintain consistent quality standards. Ask about their inspection procedures, documentation practices, and any certifications they have obtained.
4. Communication and collaboration: Effective communication and collaboration are vital for successful CNC machining projects. Choose a service provider that is responsive, transparent, and willing to work closely with you throughout the process.
5. Cost and timeline: While cost should not be the sole determining factor, it is important to consider the provider’s pricing structure and ensure it aligns with your budget. Additionally, inquire about their lead times to ensure they can meet your project deadlines.
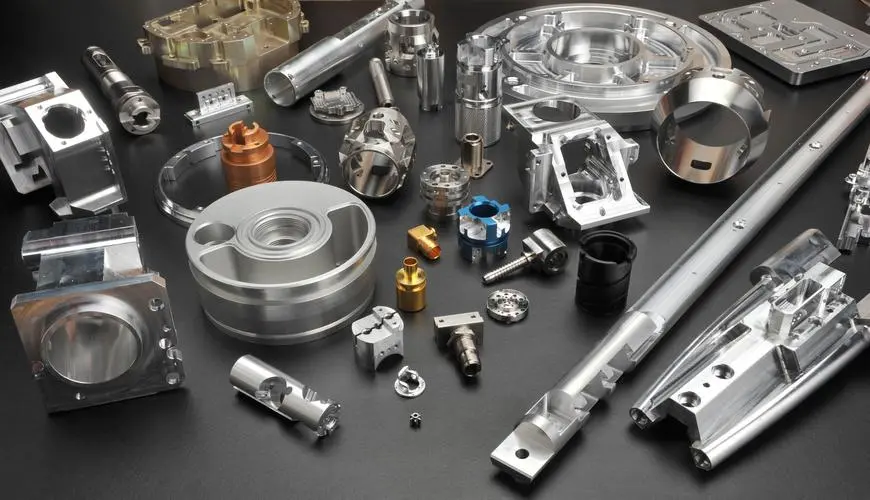
Summary:
Precision is the cornerstone of CNC machining, influencing the functionality and quality of the final product. By understanding and controlling the parameters and factors affecting precision, manufacturers can produce parts with exceptional accuracy.
Regular machine maintenance, advanced tooling, optimized programming, and rigorous inspection are essential practices for mastering precision in CNC machined parts. Whether you’re a novice or an experienced professional, focusing on precision will help you achieve superior results in CNC machining projects.