Sheet metal fabrication is crucial in various industries, from automotive to aerospace. This comprehensive article delves into the materials, methods and other factors affecting its cost.
It provides industry professionals and potential customers with the information to make informed decisions about their fabrication projects.
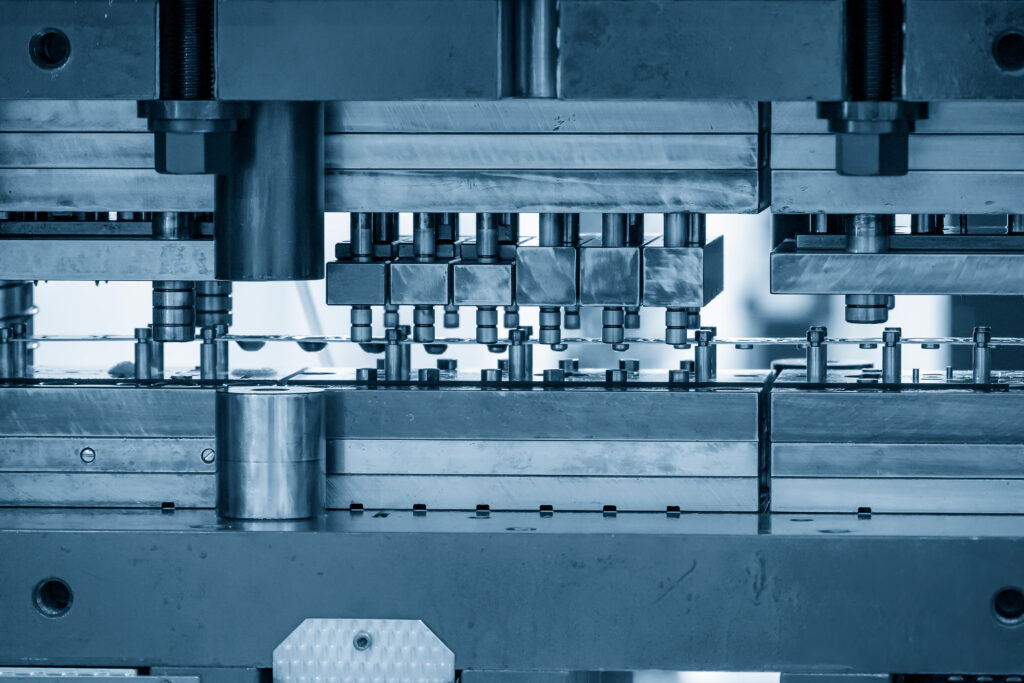
Overall, the price of sheet metal is moderately high. However, the cost of sheet metal fabrication can vary depending on material choice, project complexity, and location.
Based on our experience, projects cost around $1,616 but range from $418 to $3,212. Factors like high demand and limited supply can also drive prices higher.
Understanding the factors influencing these costs is essential for making informed decisions and optimizing your project’s budget.
-
Table Of Contents
-
1. Is Sheet Metal Fabrication Expensive?
-
2. How Much Does Sheet Metal Forming Cost?
-
3. Why is Sheet Metal So Expensive?
-
4. What Are the Advantages and Disadvantages of Metal Fabrication?
-
5. How Do You Calculate Metal Fabrication Cost?
-
6. How to Choose the Most Cost-Effective Material?
-
7. How Can I Reduce the Cost of My Sheet Metal Fabrication Project?
-
8. Summary
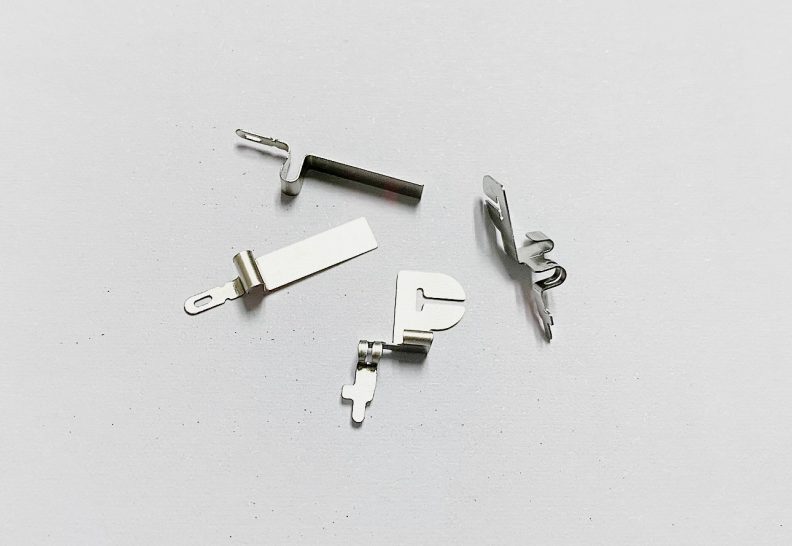
How Much Does Sheet Metal Forming Cost?
The cost of sheet metal forming can vary significantly based on material type, design complexity, precision requirements, and production volume.
On average, projects cost around $1,616, ranging from $418 to $3,212. More complex projects may cost up to $9,500 or more. Various elements contribute to these costs:
Key Cost Factors:
Material Costs: Prices for raw materials like steel, aluminium, or stainless steel can fluctuate based on market conditions, availability, and quality.
Labour Costs: Skilled labour is essential for high-quality fabrication, and rates vary based on location and task complexity.
Machinery and Tools: Advanced machinery, such as CNC machines and laser cutters, are expensive to purchase and maintain, contributing to overall costs.
Secondary Operations: Processes like welding, painting, and finishing add to total expenses.
Volume of Production: Higher production volumes can reduce per-unit costs due to economies of scale.
Accurate cost estimation requires a detailed breakdown of each production cycle aspect, including raw materials, machining, and finishing.
Why is Sheet Metal So Expensive?
Several factors contribute to the relatively high cost of sheet metal fabrication:
Market Demand: Increased demand for new construction and manufacturing projects can lead to higher prices due to supply constraints.
Raw Material Costs: Global market conditions, tariffs, and trade policies can cause raw material prices to fluctuate.
Energy Costs: Metal fabrication processes are energy-intensive, and changes in energy prices directly impact costs.
Labour Costs: Skilled labour is expensive, and training and retaining qualified workers adds to the cost.
Technology and Equipment: Advanced fabrication technologies require significant investment in equipment and maintenance.
Understanding these factors helps businesses plan projects more effectively and explore cost-mitigation strategies, such as negotiating long-term contracts for raw materials or investing in energy-efficient technologies.
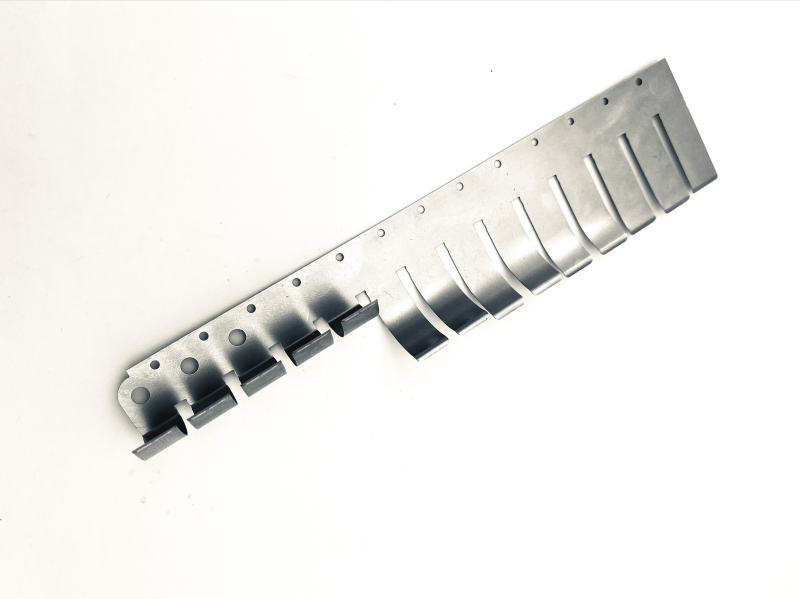
What Are the Advantages and Disadvantages of Metal Fabrication?
Adopting advanced technologies in sheet metal fabrication offers several benefits:
Increased Precision: CNC machining and laser cutting provide high precision, reducing material waste and ensuring consistent quality.
Efficiency: Automation increases production speed and consistency, improving overall productivity.
Cost Savings: While initial investments are high, long-term costs are lowered by reducing labour and material waste.
Flexibility: Advanced technologies offer greater flexibility in design and production.
Improved Quality: Higher quality products with better surface finishes and tighter tolerances.
Data Integration: Improved planning, scheduling, and inventory management through better data integration.
While versatile and widely used, sheet metal fabrication has some drawbacks:
Secondary Operations: Additional finishing, painting, and deburring processes are time-consuming and costly.
Skilled Labor: The need for specialized skills increases labour costs and can make finding qualified personnel challenging.
Heat Distortion: Welding or cutting generates significant heat, distorting the metal and affecting product quality.
Material Waste: Cutting and forming processes can produce considerable waste, necessitating efficient design and planning.
Complexity and Time: More complex designs increase fabrication time and costs.
Despite these disadvantages, the benefits of sheet metal fabrication—such as durability, versatility, and the ability to create precise components—often outweigh the drawbacks.
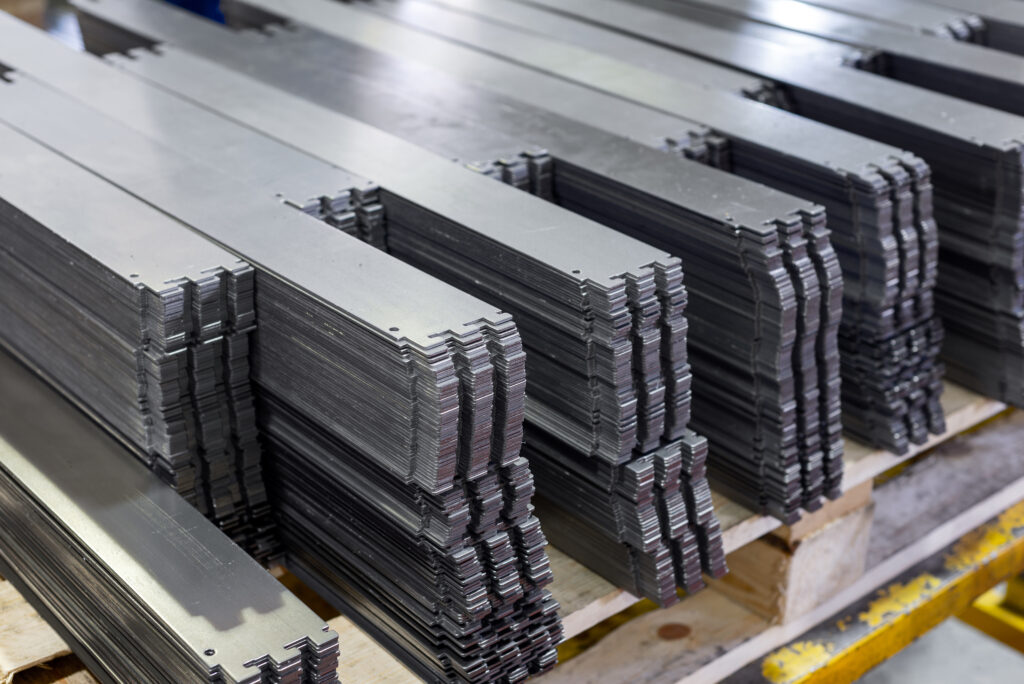
How Do You Calculate Metal Fabrication Cost?
Calculating the cost of metal fabrication involves several steps:
Production Cycle Breakdown: Divide the project into phases (design, material acquisition, cutting, forming, assembly, finishing) and consider each cost.
Raw Material Costs: Calculate the cost of all required materials based on type, grade, and quantity.
Machining Costs: Include the cost of all machining operations, such as cutting, bending, and welding.
Labour Costs: Estimate labour costs based on the hours required for each phase and hourly rates.
Additional Phases: Consider costs for finishing, painting, or assembly.
Overhead and Profit Margins: Factor overhead costs and include a profit margin.
This detailed approach helps identify cost-saving opportunities and ensures comprehensive project accounting.
How to Choose the Most Cost-Effective Material?
Selecting the suitable material is crucial for balancing cost and performance:
Steel: Generally the most cost-effective due to its availability and lower price. Offers good strength and durability.
Aluminium: More expensive but lightweight and corrosion-resistant. Ideal for the aerospace and automotive industries.
Stainless Steel: More expensive due to superior corrosion resistance and strength. Suitable for applications requiring high durability and aesthetic appeal.
Match material properties to project needs to optimize performance and cost.
How Can I Reduce the Cost of My Sheet Metal Fabrication Project?
Strategic planning and efficient execution can help minimize expenses:
Optimize Design: Simplify designs to reduce material use and machining time.
Material Selection: Choose cost-effective materials that meet project requirements.
Advanced Technology: Use technologies like CNC machining and laser cutting to increase efficiency and reduce labour costs.
Efficient Production: Streamline production to minimize downtime and increase throughput.
Outsource Non-Core Activities: Consider outsourcing tasks like finishing and painting to specialized vendors.
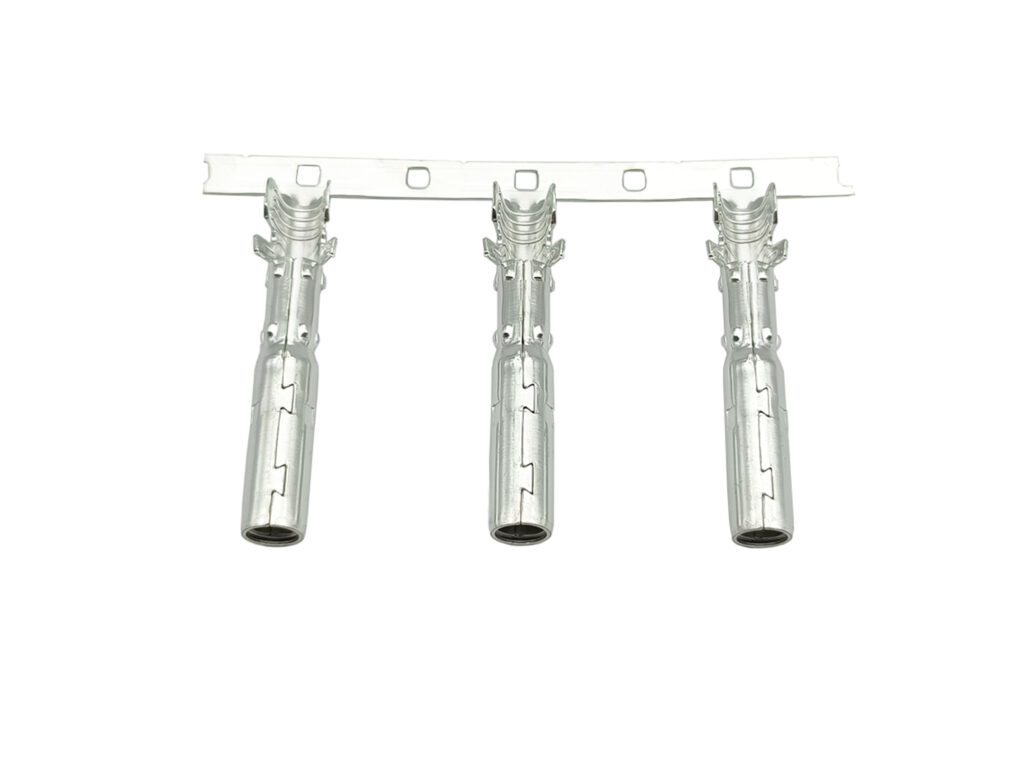
Summary:
Understanding the costs associated with sheet metal fabrication is essential for industry professionals and potential customers. By considering factors such as material choice, project complexity, and whether to outsource or handle fabrication in-house, you can make informed decisions that balance quality and cost.
Advanced technologies and strategic design optimizations can help manage and reduce overall expenses. With careful planning and execution, sheet metal fabrication can be efficient and cost-effective, ensuring the success of your projects.