Choosing the right heatsink material for LED applications is crucial for ensuring optimal performance and longevity. Aluminum, a common choice, offers several benefits that make it a preferred option among engineers and manufacturers.
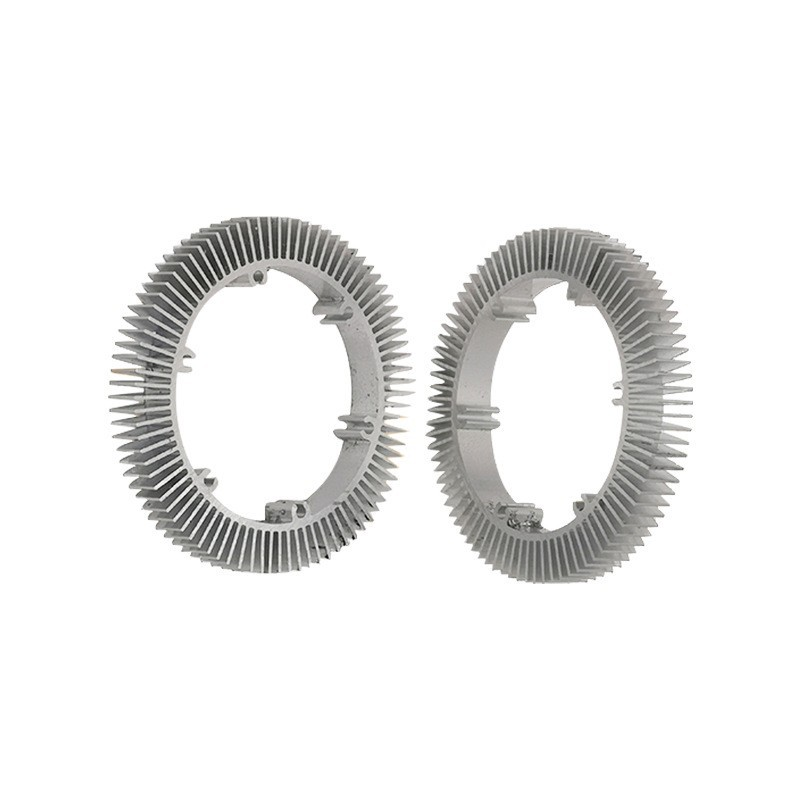
Aluminum is widely considered the best choice for LED heatsinks due to its excellent corrosion resistance, good surface treatment options, and efficient thermal conductivity.
This combination of properties makes aluminum alloys ideal for managing the heat generated by LED lights.
In this article, let’s explore why aluminum is an excellent material for LED heatsinks, compare it with other potential options, and delve into various aspects that make it suitable for this application.
-
Table Of Contents
-
1. Is Aluminum a Suitable Metal for an LED Heatsink?
-
2. What Makes Aluminum a Popular Choice for Heatsinks?
-
3. Comparing Aluminum to Other Heatsink Materials
-
4. Surface Treatment Options for Aluminum Heatsinks
-
5. Corrosion Resistance of Aluminum Heatsinks
-
6. Real-world Applications of Aluminum Heatsinks in LED Technology
-
7. Future Trends in Heatsink Materials
-
8. Summary
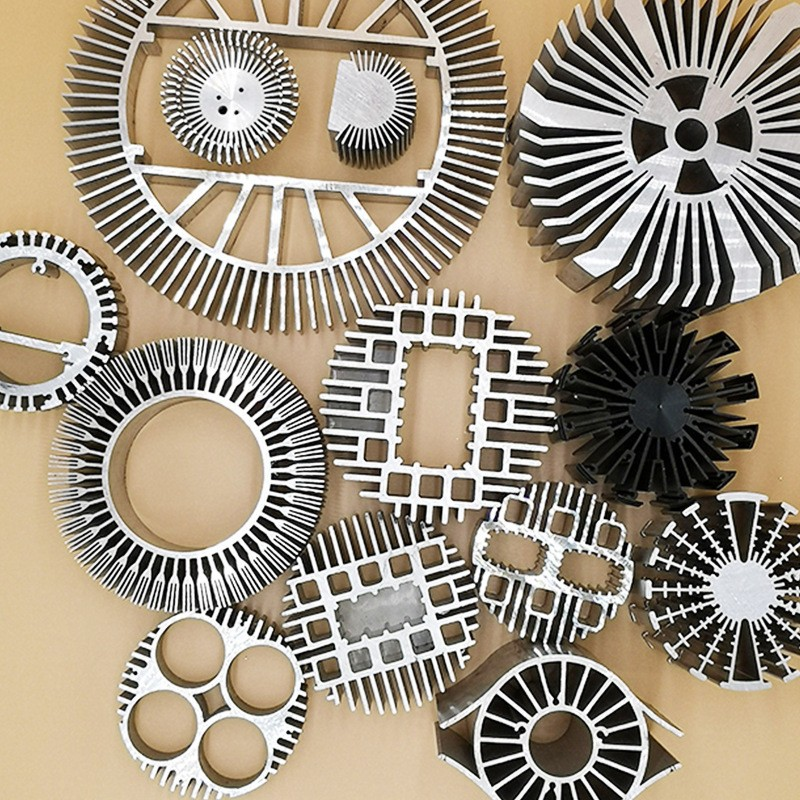
What Makes Aluminum a Popular Choice for Heatsinks?
Aluminum offers a unique combination of properties that make it an ideal material for heatsinks:
• Thermal Conductivity: Aluminum has a thermal conductivity of around 235 W/mK, which, while lower than copper, is sufficient for most LED applications. This property allows aluminum heatsinks to effectively dissipate heat away from the LED, maintaining optimal operating temperatures and preventing thermal damage.
• Lightweight: Aluminum is significantly lighter than copper, reducing the overall weight of the LED system. This is particularly important in applications where weight is a critical factor, such as in automotive and aerospace industries.
• Cost-Effective: Aluminum is cheaper than copper, making it a more economical choice for large-scale production. The cost savings can be substantial, especially when manufacturing thousands or millions of units.
• Corrosion Resistance: Aluminum naturally forms a protective oxide layer, which enhances its resistance to corrosion. This makes aluminum heatsinks durable and suitable for use in various environments, including those with high humidity or exposure to corrosive elements.
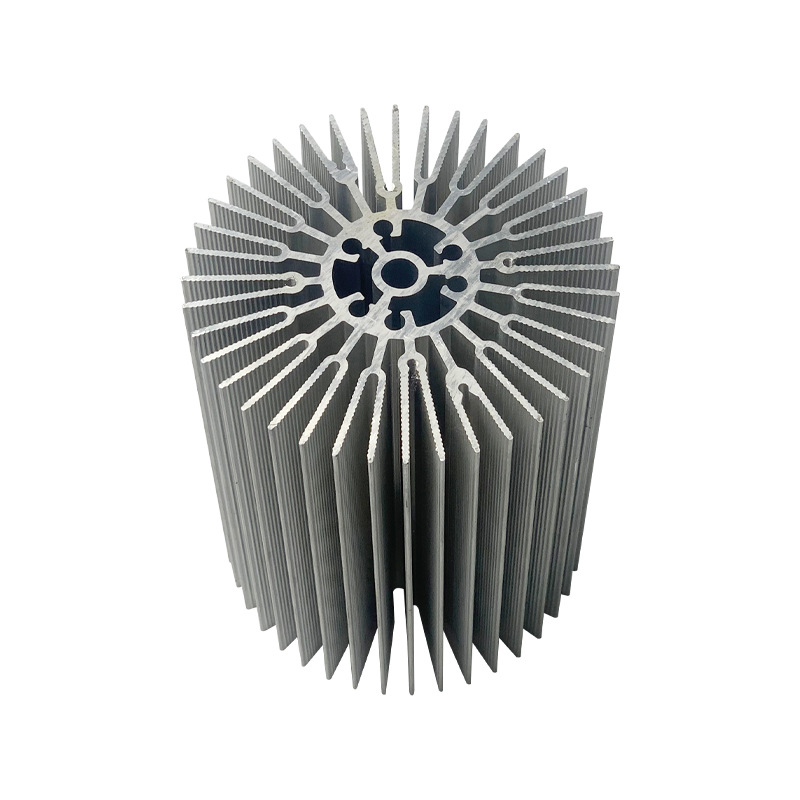
Comparing Aluminum to Other Heatsink Materials
While aluminum is a popular choice, it’s essential to compare it with other materials to understand its advantages:
• Copper: Copper has higher thermal conductivity (around 400 W/mK) but is heavier and more expensive than aluminum. It’s also more challenging to machine. Copper heatsinks are typically used in high-performance applications where maximum thermal conductivity is required, but the added weight and cost can be significant drawbacks.
• Steel: Steel is less common due to its lower thermal conductivity and higher weight compared to aluminum and copper. While steel can be used in some applications, it is generally not preferred for heatsinks due to its inefficiency in heat dissipation.
• Graphite: Graphite can be used for high-end applications due to its excellent thermal conductivity, but it’s brittle and expensive. Graphite heatsinks are typically found in specialized applications where high thermal performance is required, but their fragility and cost limit their widespread use.
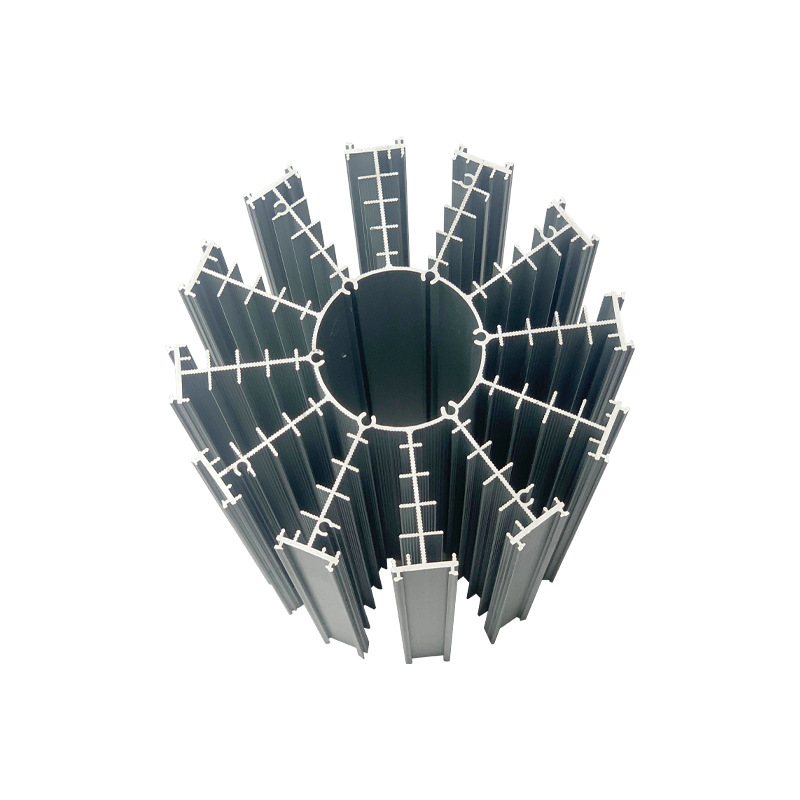
Surface Treatment Options for Aluminum Heatsinks
Surface treatments enhance the performance and durability of aluminum heatsinks. Common treatments include:
• Anodizing: This process increases corrosion resistance and allows for dyeing the heatsink in various colors. Anodized aluminum heatsinks have a hard, durable surface that can withstand harsh environments and provide better thermal performance.
• Powder Coating: Provides a durable finish that can improve the heatsink’s aesthetic and protective qualities. Powder-coated aluminum heatsinks are resistant to chipping, scratching, and fading, making them suitable for use in various applications.
• Electroplating: Adds a thin layer of another metal, such as nickel, to improve corrosion resistance and thermal conductivity. Electroplated aluminum heatsinks can offer enhanced performance and durability, making them ideal for demanding applications.
These surface treatments not only enhance the appearance and durability of aluminum heatsinks but also contribute to their thermal performance.
By choosing the appropriate surface treatment, manufacturers can tailor the properties of aluminum heatsinks to meet specific application requirements.
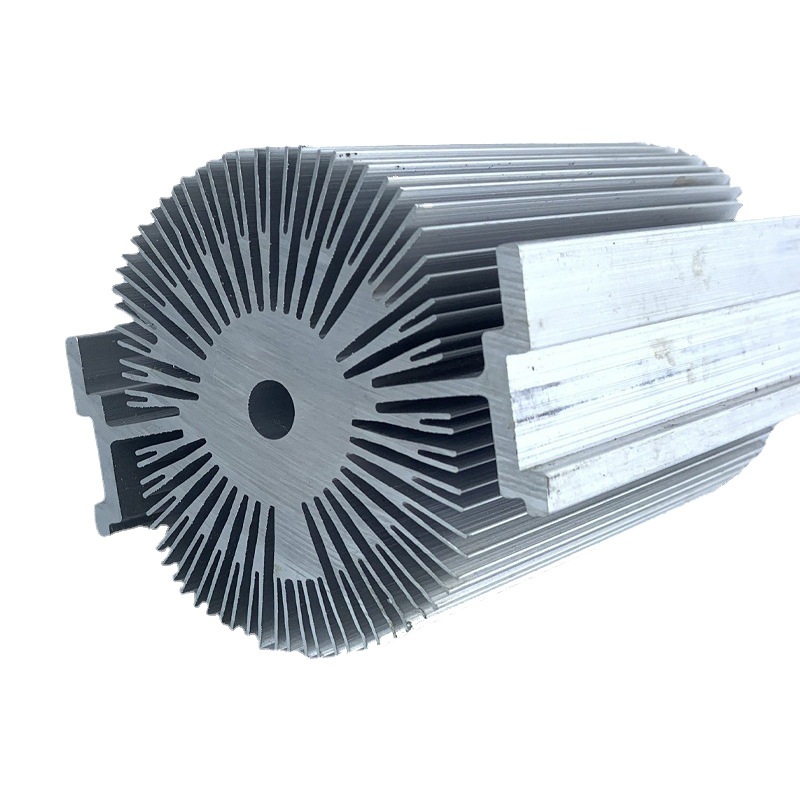
Corrosion Resistance of Aluminum Heatsinks
Aluminum’s natural oxide layer provides inherent corrosion resistance, which can be further enhanced through surface treatments.
This property ensures that aluminum heatsinks remain effective and maintain their appearance over time, even in harsh environments.
Corrosion resistance is particularly important in applications where the heatsink may be exposed to moisture, chemicals, or other corrosive elements.
For example, in outdoor lighting applications, aluminum heatsinks must withstand rain, humidity, and pollution without degrading.
The corrosion resistance of aluminum makes it a reliable choice for such applications, ensuring long-term performance and durability.
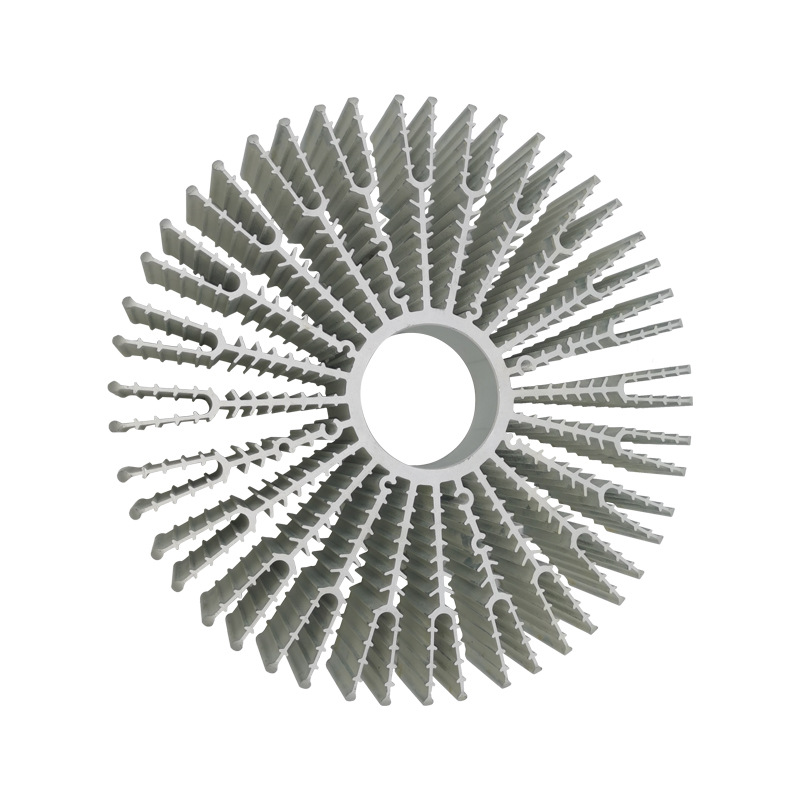
Real-world Applications of Aluminum Heatsinks in LED Technology
Aluminum heatsinks are widely used in various LED applications, from household lighting to industrial and automotive lighting systems.
Their ability to efficiently dissipate heat ensures the LEDs operate within safe temperature ranges, enhancing their lifespan and performance.
In household lighting, aluminum heatsinks are used in LED bulbs and fixtures to manage the heat generated during operation. By maintaining optimal temperatures, these heatsinks help ensure the LEDs provide consistent light output and have a long operational life.
In industrial applications, such as in factories and warehouses, aluminum heatsinks are used in high-power LED lighting systems. These environments often require robust and reliable lighting solutions, and aluminum heatsinks provide the necessary thermal management to keep the LEDs operating efficiently.
In automotive lighting, aluminum heatsinks are used in LED headlights, taillights, and interior lighting. The lightweight and corrosion-resistant properties of aluminum make it an ideal choice for automotive applications, where durability and performance are critical.
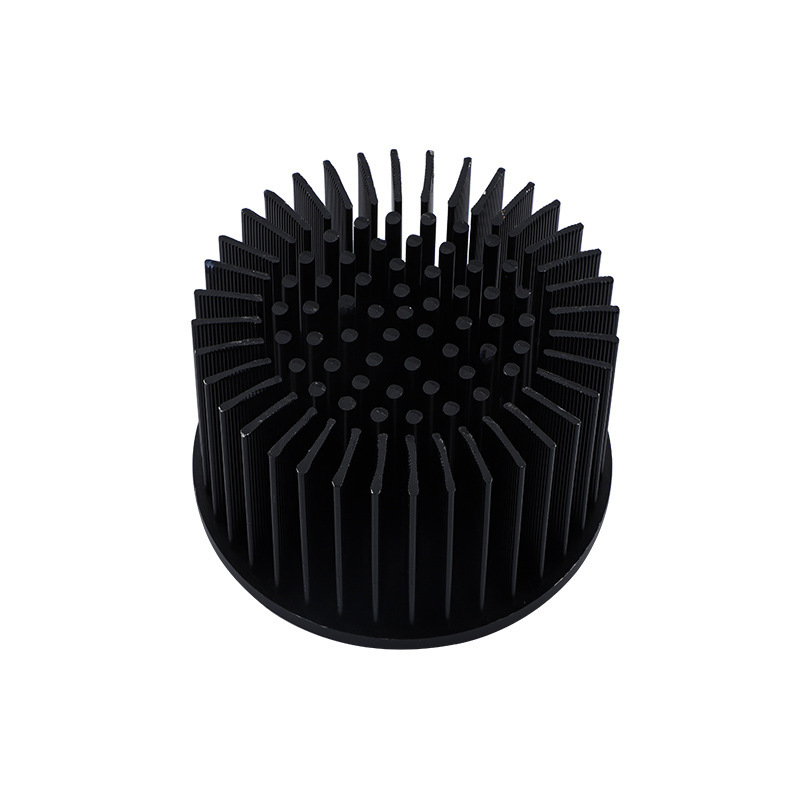
Future Trends in Heatsink Materials
While aluminum remains a dominant material, research is ongoing to develop advanced materials and composites that offer improved thermal management.
Innovations in manufacturing processes, such as 3D printing, also promise to enhance the design and efficiency of heatsinks.
Future trends in heatsink materials may include the use of advanced composites that combine the best properties of multiple materials, such as high thermal conductivity, lightweight, and durability.
3D printing is another promising technology that can revolutionize heatsink design and production. By allowing for complex geometries and customized designs, 3D printing can produce heatsinks with optimized thermal performance and reduced weight.
This technology also offers the potential for rapid prototyping and on-demand production, reducing lead times and costs.
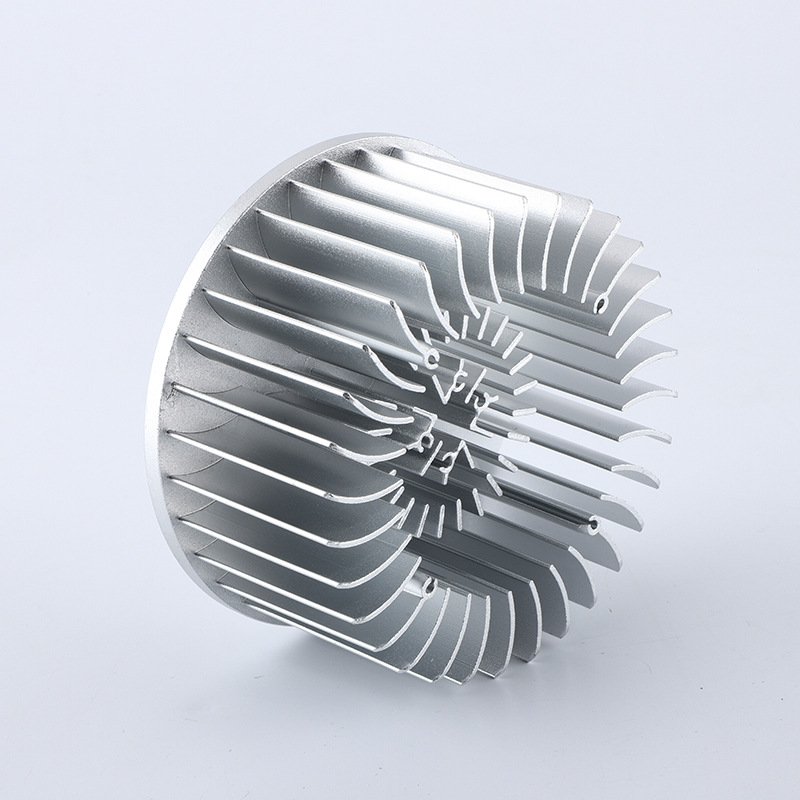
Summary:
Aluminum’s versatility and performance make it a reliable choice for various LED applications, ensuring that LEDs operate efficiently and have a long operational life.
By understanding the benefits and limitations of aluminum heatsinks, you can make informed decisions that optimize the performance and durability of their LED systems.