Graphite machining is essential for creating custom graphite parts used in various industries, including aerospace, automotive and electronics.
Despite its importance, many face challenges due to graphite’s unique properties. Understanding these challenges and the machining process can help engineers, manufacturers, and buyers achieve optimal results.
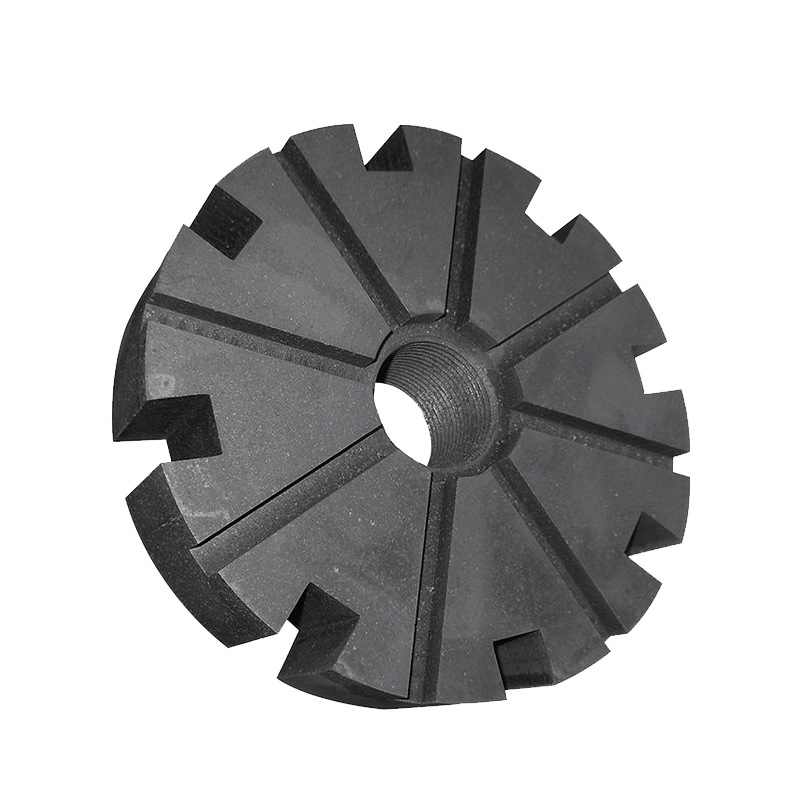
Generally, graphite machining involves precision techniques to shape graphite into custom parts. Despite its softness, graphite is difficult to machine due to its abrasive nature and tendency to chip.
Using diamond or carbide tools and proper feed rates ensures effective machining, making it suitable for applications requiring high thermal and electrical conductivity.
Now, let’s dive deeper into some aspects of mastering graphite machining for better customizing graphite parts.
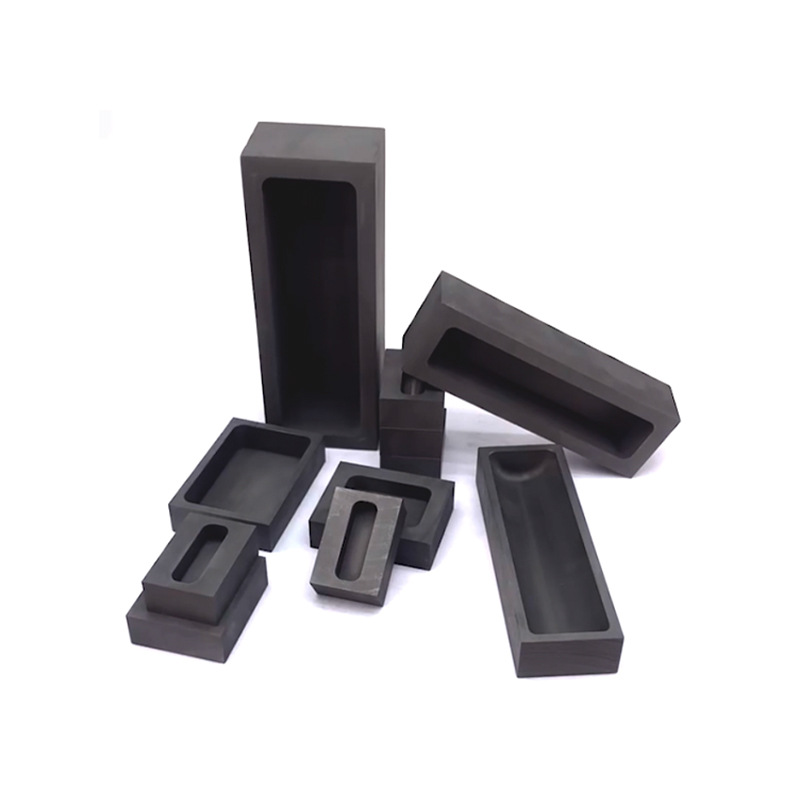
How machinable is graphite?
Graphite’s unique properties, such as its crystalline structure, contribute to its machinability challenges. The structure makes it strong yet brittle, prone to chipping under mechanical stress. Additionally, its high thermal conductivity can affect machining processes, requiring specialized tools and techniques.
Its abrasive nature leads to rapid tool wear. To mitigate this, machinists use diamond-coated or carbide tools, which offer higher durability. Regular maintenance and monitoring of tools are essential to maintain machining precision and avoid defects in the final parts.
Using coolant in graphite machining is a double-edged sword. While it can reduce heat and prolong tool life, it also introduces the risk of contamination. Most graphite machining processes are performed dry, with dust control systems in place to manage graphite dust, which can be hazardous if inhaled.
Can you CNC graphite?
CNC graphite works. However, it is hard on tools due to its abrasive nature. Using coated or carbide bits minimizes wear, especially for small batches. Maintaining low cutter feed speeds is crucial to control graphite dust, ensuring precision and safety during the CNC milling process.
Diamond-coated tools are preferred for their hardness and wear resistance. Additionally, carbide tools with specific coatings can handle graphite’s abrasive nature effectively, ensuring longer tool life and better surface finishes.
Optimizing CNC parameters, such as cutting speed, feed rate, and depth of cut, is essential for efficient graphite machining. Machinists must balance these parameters to achieve desired accuracy and surface finish while minimizing tool wear. Advanced CNC software can assist in fine-tuning these parameters for optimal performance.
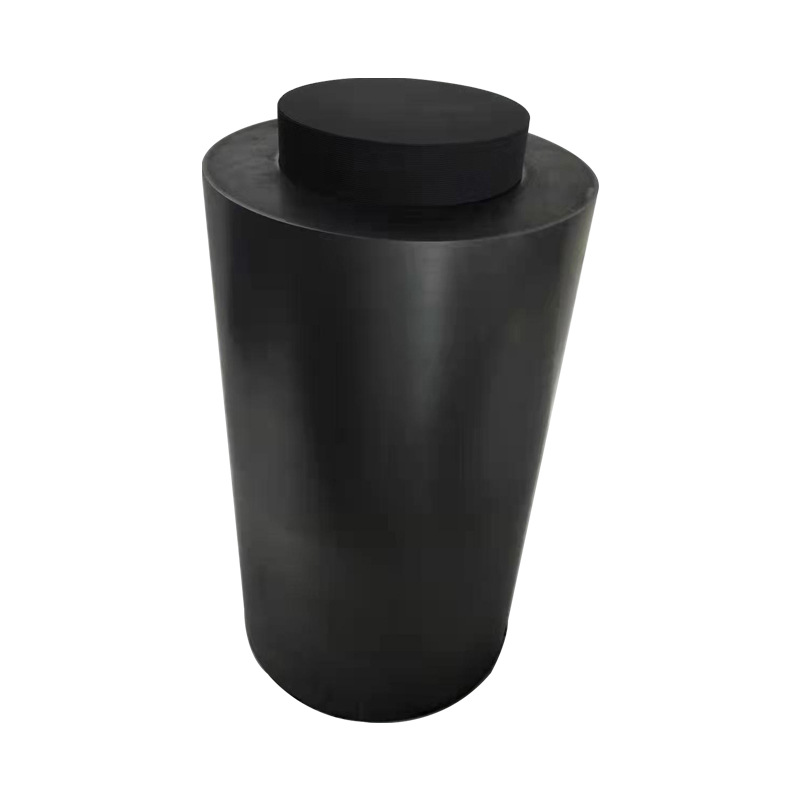
How do you machine carbon graphite?
Machining carbon graphite requires specialized tools and techniques. Graphite and carbon are typically machined dry, without cutting fluids, to prevent contamination. Proper handling and machining protocols ensure high-quality custom graphite parts.
Differences Between Graphite and Carbon Graphite
Understanding the differences between graphite and carbon graphite is crucial for effective machining. While both materials share similar properties, carbon graphite has higher density and strength, making it suitable for more demanding applications. Machining techniques may vary slightly based on the specific material being used.
Diamond Tools for Machining
Diamond tools are the preferred choice for machining carbon graphite due to their exceptional hardness and wear resistance. These tools can withstand the abrasive nature of graphite, ensuring precise cuts and longer tool life. Investing in high-quality diamond tools is essential for efficient carbon graphite machining.
Machining Techniques and Parameters
Machining carbon graphite involves careful control of machining parameters. Factors such as cutting speed, feed rate, and tool geometry must be optimized to achieve desired results. Machinists must also account for the material’s tendency to generate fine dust, necessitating effective dust extraction systems.
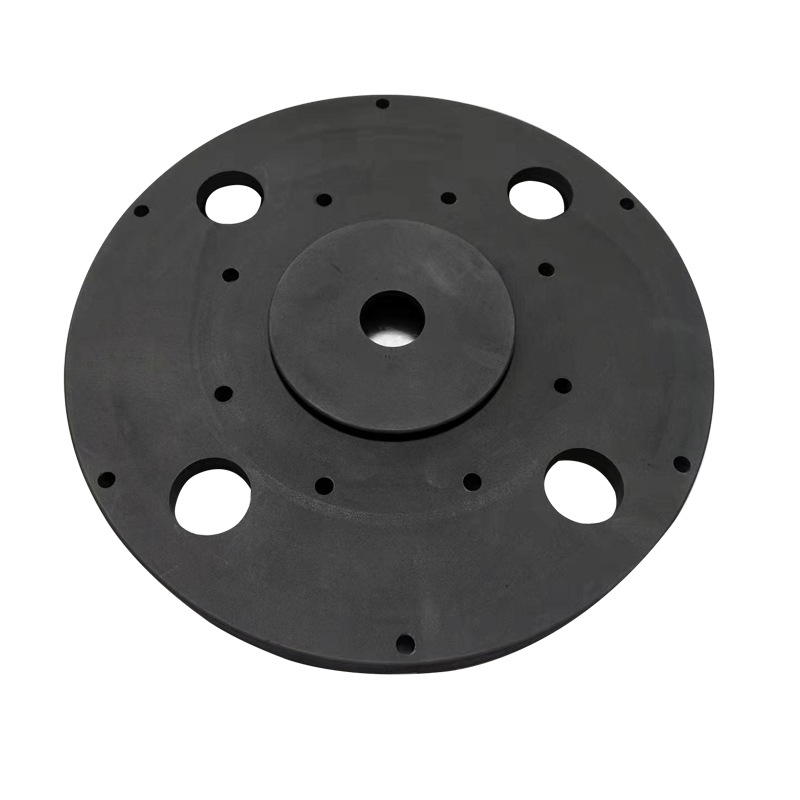
Applications of Custom Graphite Parts
Custom graphite parts are used in various industries, including aerospace, automotive, and electronics. They are essential in creating components like electrodes, heating elements, and molds due to graphite’s excellent thermal and electrical conductivity. The ability to machine graphite into precise shapes makes it invaluable in these applications.
Aerospace Industry
In the aerospace industry, custom graphite parts are used in high-temperature applications such as rocket nozzles, heat shields, and jet engine components. Graphite’s thermal stability and resistance to thermal shock make it ideal for these demanding environments, ensuring reliable performance under extreme conditions.
Automotive Industry
The automotive industry utilizes custom graphite parts in various applications, including brake linings, gaskets, and battery components. Graphite’s lubricating properties and electrical conductivity enhance the performance and longevity of these components, contributing to overall vehicle efficiency and reliability.
Electronics Industry
In the electronics industry, custom graphite parts are used for manufacturing electrodes, conductive plates, and heat sinks. Graphite’s excellent electrical conductivity and thermal management capabilities make it essential for producing high-performance electronic devices, ensuring efficient heat dissipation and reliable electrical connections.
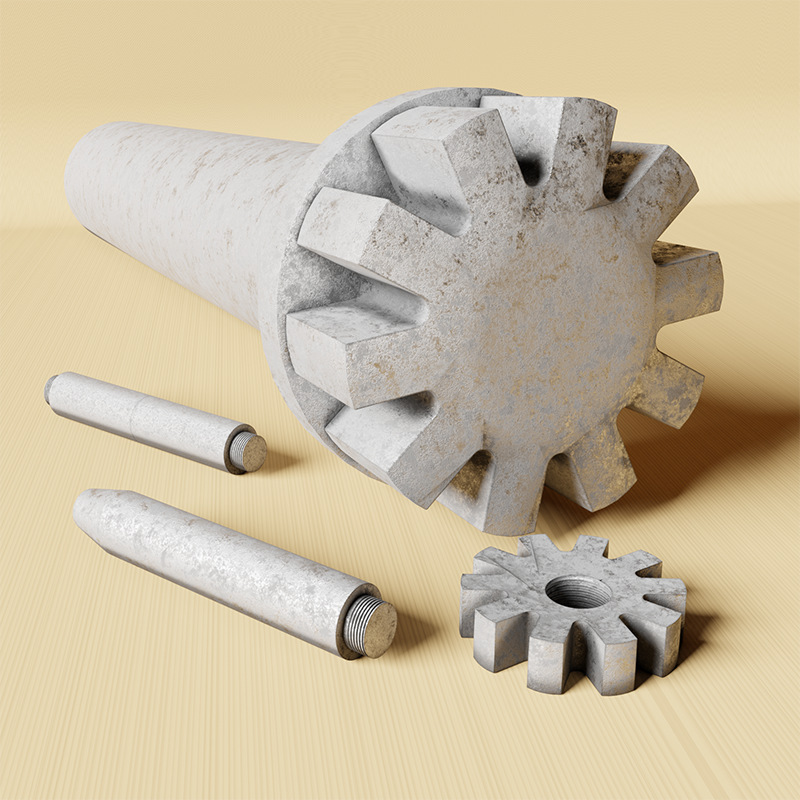
Benefits of Graphite Machining
Graphite machining offers numerous benefits, including high thermal resistance, electrical conductivity, and chemical stability. These properties make graphite ideal for applications requiring high-temperature environments and electrical components. Additionally, graphite’s machinability allows for the creation of complex, custom parts tailored to specific needs.
High Thermal Resistance
High Thermal Resistance: Graphite’s high thermal resistance makes it suitable for applications involving extreme temperatures. It can withstand temperatures up to 3000°C without melting or degrading, making it ideal for use in furnaces, heat exchangers, and other high-temperature environments.
Electrical Conductivity
Electrical Conductivity: Graphite’s excellent electrical conductivity makes it a preferred material for electrical applications. It is used in electrodes, batteries, and conductive coatings, where efficient electrical transfer is essential. Graphite’s conductivity can be tailored by adjusting its density and composition, offering flexibility for various applications.
Chemical Stability
Chemical Stability: Graphite’s chemical stability allows it to resist corrosion and chemical reactions, even in harsh environments. This property makes it suitable for use in chemical processing equipment, where exposure to aggressive chemicals is common. Graphite components maintain their integrity and performance over extended periods.
Machinability and Precision
Graphite’s machinability allows for the creation of complex, custom parts with high precision. Advanced machining techniques enable the production of intricate shapes and fine details, meeting the specific requirements of various industries. This flexibility makes graphite a versatile material for diverse applications.
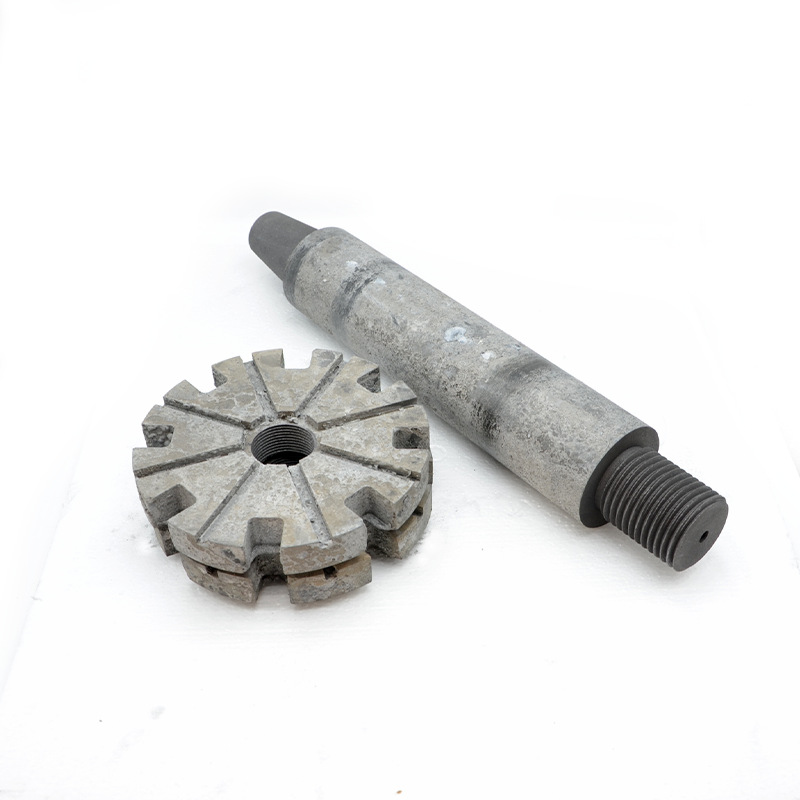
Summary
Graphite machining is a complex yet rewarding process, essential for creating custom parts with unique properties. By understanding and addressing the challenges of machining graphite, engineers and manufacturers can leverage its benefits in various applications. Explore the potential of graphite machining to meet your specific needs.