Computer Numerical Control (CNC) turning has become essential in modern manufacturing for producing high-quality parts with precision and efficiency.
Whether you’re an engineer, manufacturing professional, or hobbyist, understanding when to use CNC turning can enhance production processes.
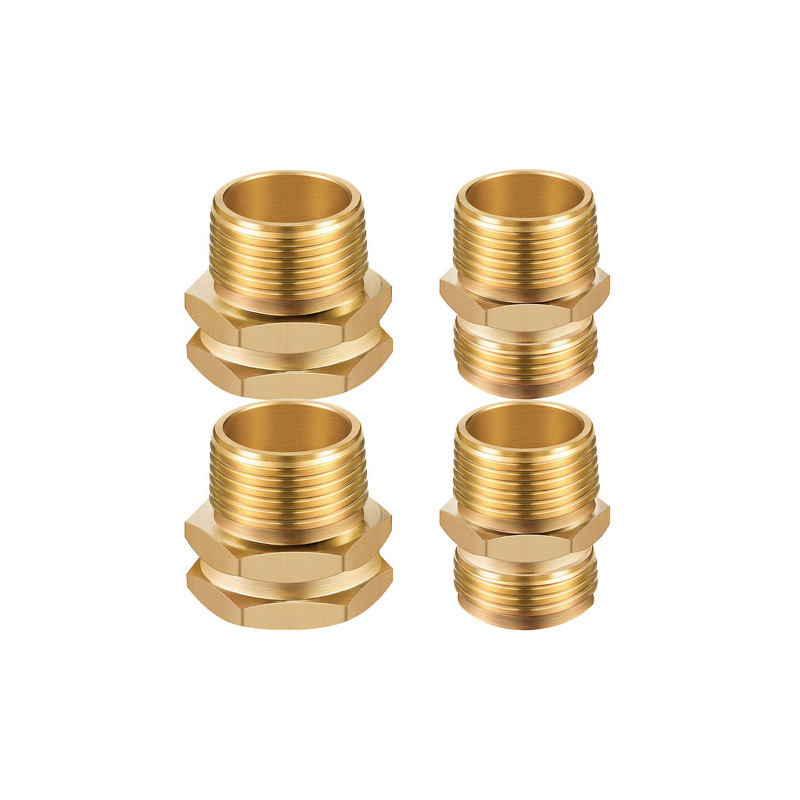
To determine if a part is best suited for CNC turning, focus on its geometry, material, size, and production volume.
Parts with rotational symmetry, such as shafts and bushings, are ideal candidates.
Materials like metals and durable plastics, manageable sizes, and medium-to-high production volumes also make CNC turning a cost-effective choice.
This method is widely used in automotive, aerospace, medical, and electronics industries due to its precision, efficiency, and ability to produce consistent, high-quality parts.
This guide covers what CNC turning is, identifies parts that benefit from this method. Now, let’s dive into it.
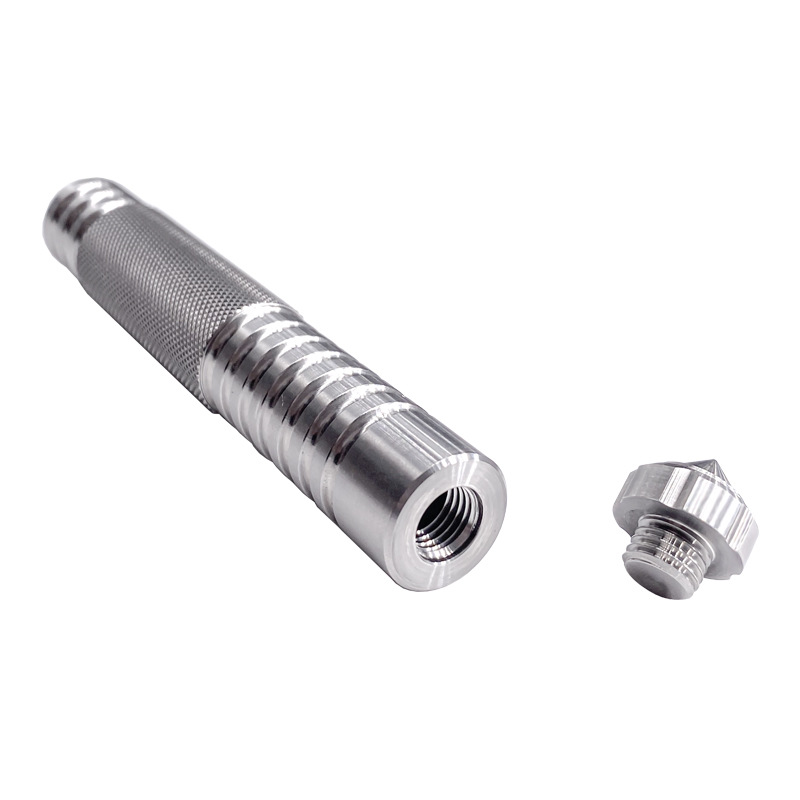
Key Criteria for CNC Turning Suitability
To determine if a part should be made using CNC turning, examine factors like geometry, material, size, and production volume.
1. Geometry and Symmetry
Rotational symmetry is the primary characteristic suited for CNC turning.
Parts like cylinders, shafts, bushings, and rings benefit from turning, as they can be rotated around a central axis without altering their profile. For example:
• Shafts in engines or machinery need precise diameters and lengths for optimal fit and function, achievable through CNC turning.
• Bushings reduce friction between moving parts, and CNC turning can provide the smooth finish they require.
2. Material Considerations
CNC turning accommodates various materials, from metals to plastics, each suited to specific applications. Key options include:
• Metals like steel, stainless steel, aluminum, and brass are known for their strength and durability. For instance, aluminum’s lightweight nature and machinability make it popular in aerospace and automotive sectors.
• Plastics such as ABS, nylon, and polycarbonate offer chemical resistance and durability, making them suitable for medical devices and electronic components.
3. Size and Complexity
While CNC turning can handle parts of different sizes, it is best for small to medium-sized pieces.
More significant parts may exceed the lathe’s swing and length capacity.
CNC turning can be combined with milling for complex parts with additional features. Features like drilling, threading, and grooving are compatible with CNC turning, enabling efficient multi-feature part production in a single setup.
4. Production Volume
CNC turning’s automation makes it ideal for high-volume production runs.
When manufacturing identical parts with rotational symmetry, CNC turning ensures consistent quality.
For instance, automotive parts like pulleys and gears benefit from the repeatability and efficiency of CNC turning.
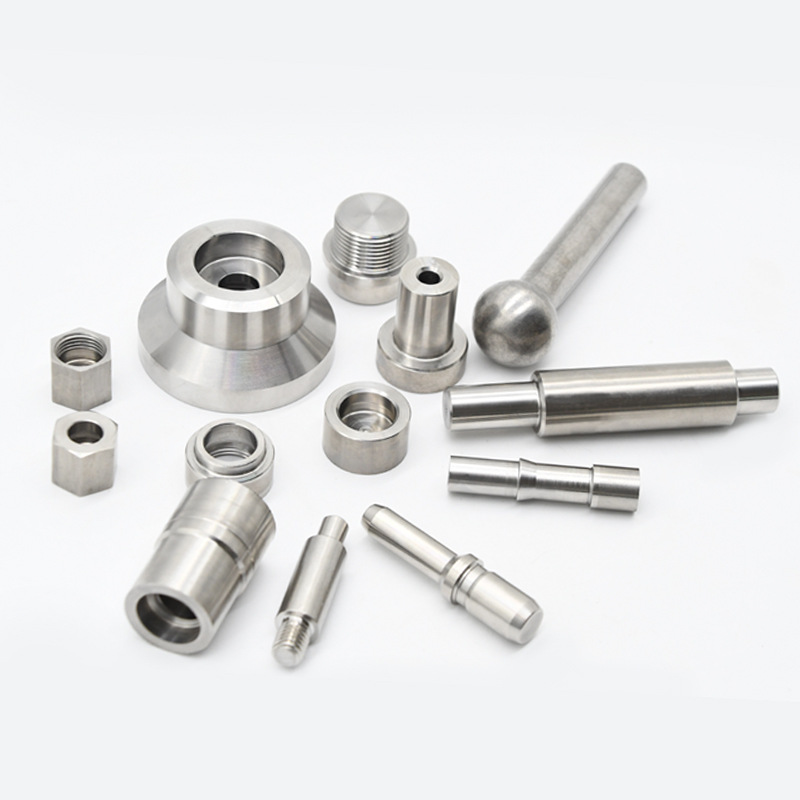
Advantages of CNC Turning
1. Precision and Accuracy
CNC turning offers high precision, producing parts with tolerances up to 0.01mm. This is vital in aerospace and medical devices industries, where minor deviations can cause failures.
2. Speed and Efficiency
Once programmed, CNC turning produces parts quickly, which is cost-effective for high-volume runs. Automation minimizes human error, reducing waste and maintaining efficiency.
3. Consistency
CNC turning’s repeatability allows the production of identical parts, which is essential in sectors like automotive, where part compatibility is crucial.
4. Superior Surface Finish
CNC turning achieves smooth, polished finishes, often eliminating the need for secondary processes like grinding or sanding. This is crucial for bearings and bushings requiring a high-quality finish.
5. Versatility in Materials and Applications
CNC turning’s ability to handle various materials and applications—from aerospace turbine parts to medical implants—demonstrates its adaptability to diverse industries.
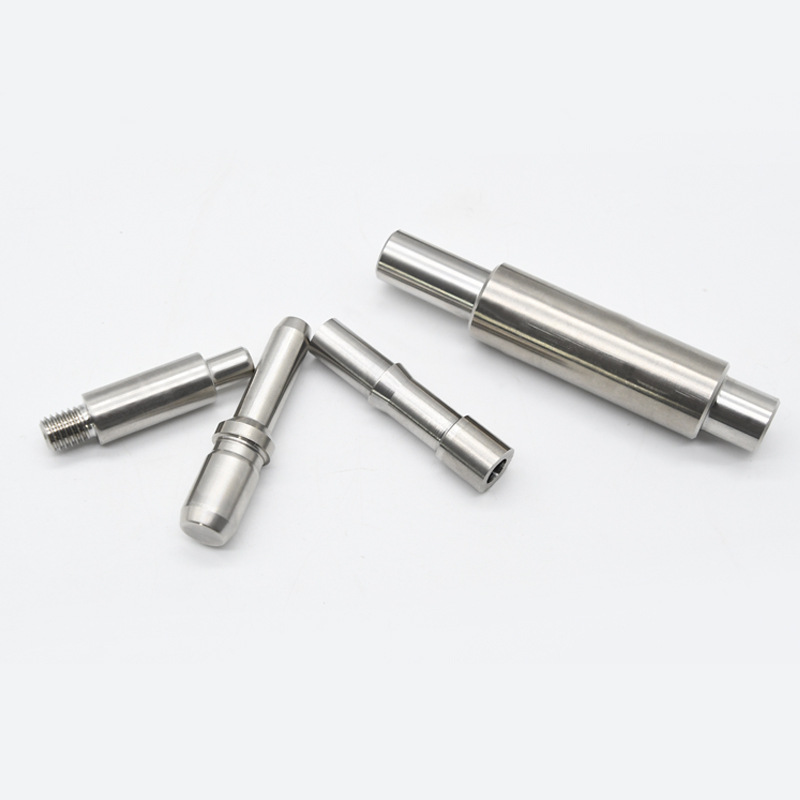
Potential Applications and Optimized Design in CNC Turning
1. AI-Based Process Optimization
Recently, AI technology has been introduced in CNC machining to optimize cutting paths and parameters and reduce material waste while improving precision.
Using AI to predict tool wear can minimise machining errors, enhancing production efficiency—especially crucial in high-precision sectors like medical and aerospace manufacturing.
2. Integration of Smart Sensor Technology
Advanced CNC equipment can be equipped with intelligent sensors to monitor temperature, vibration, and pressure in real time during machining.
This data assists operators in tracking the cutting process, detecting early signs of tool wear, and even automatically adjusting parameters to ensure machining stability and consistency.
This is particularly useful in producing high-precision components, like engine parts or surgical instruments.
3. Hybrid Manufacturing Applications
Combining CNC turning with other manufacturing methods (such as additive manufacturing or CNC milling) is an innovative trend in complex part production.
For instance, additive manufacturing (3D printing) can create base shapes, while CNC turning performs finishing and material removal—ideal for parts with complex geometries and multi-functional designs.
This approach is instrumental in medical implants and aerospace structures, enhancing material utilization and reducing lead time.
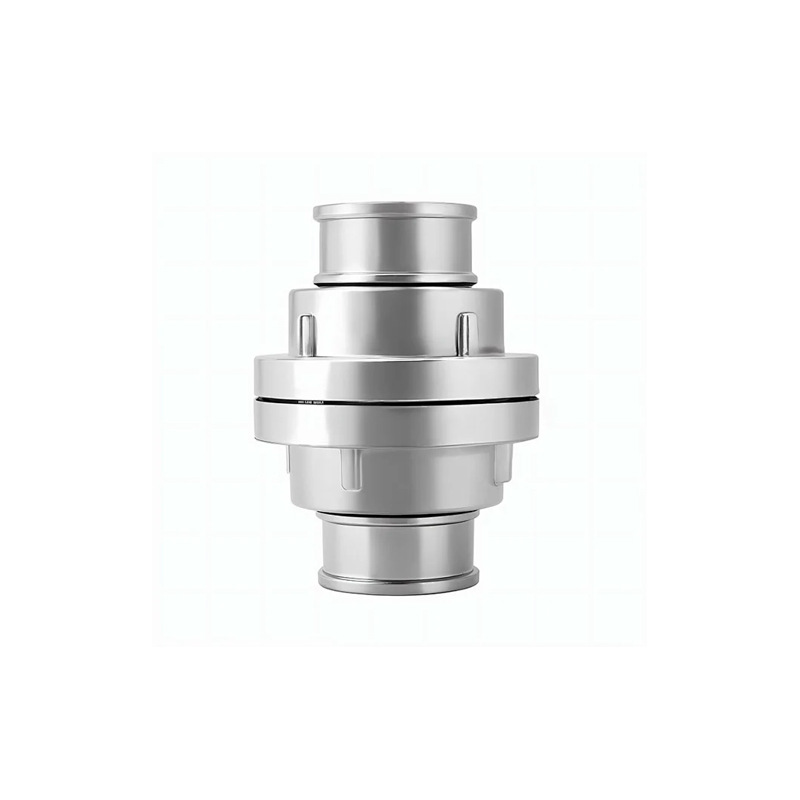
4. Sustainable Material Selection
As manufacturing shifts toward sustainability, using environmentally friendly materials is becoming a priority.
Biodegradable plastics and recyclable alloys are increasingly adopted to reduce manufacturing waste.
Using sustainable materials in combination with CNC turning’s efficiency makes the production process more eco-friendly, offering new design possibilities for sectors like medical devices and consumer electronics.
5. Micro-machining in Medical Applications
The miniaturization of CNC turning technology is well-suited for producing minimal precision components, such as micro-implants and microfluidic devices.
CNC turning requires precise control systems to achieve sub-millimetre machining accuracy in these cases.
Micro CNC turning allows medical device manufacturers to produce ergonomically tailored micro-implants, further advancing personalized treatment.
6. Data-Driven Adaptive Machining
Leveraging data collection and analysis, CNC machines can auto-adjust parameters during machining, enabling adaptive manufacturing.
For instance, machines can optimize cutting speed, feed rate, and tool paths based on real-time monitoring, thus enhancing machining efficiency.
This adaptive technology is especially beneficial in the aerospace and automotive industries, as it maintains part precision and consistency while reducing processing time.
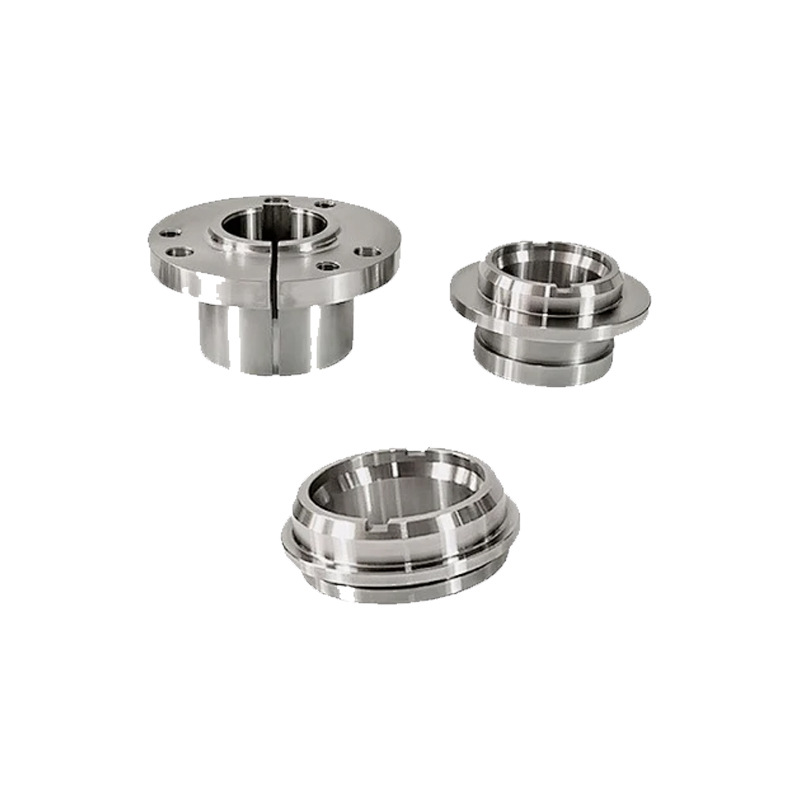
Conclusion
CNC turning is a versatile, precise, and efficient manufacturing process that excels at producing parts with rotational symmetry.
Whether in automotive, aerospace, medical, or electronics, CNC turning provides the consistency, accuracy, and surface quality required for high-performance parts.
You can leverage CNC turning to optimize manufacturing efficiency and ensure quality across production processes by carefully evaluating part geometry, materials, and production needs.