Stamping die design is crucial in the manufacturing industry, especially for professionals seeking precision and efficiency.
Understanding the methods and steps involved can significantly impact the quality and cost-effectiveness of the final product.
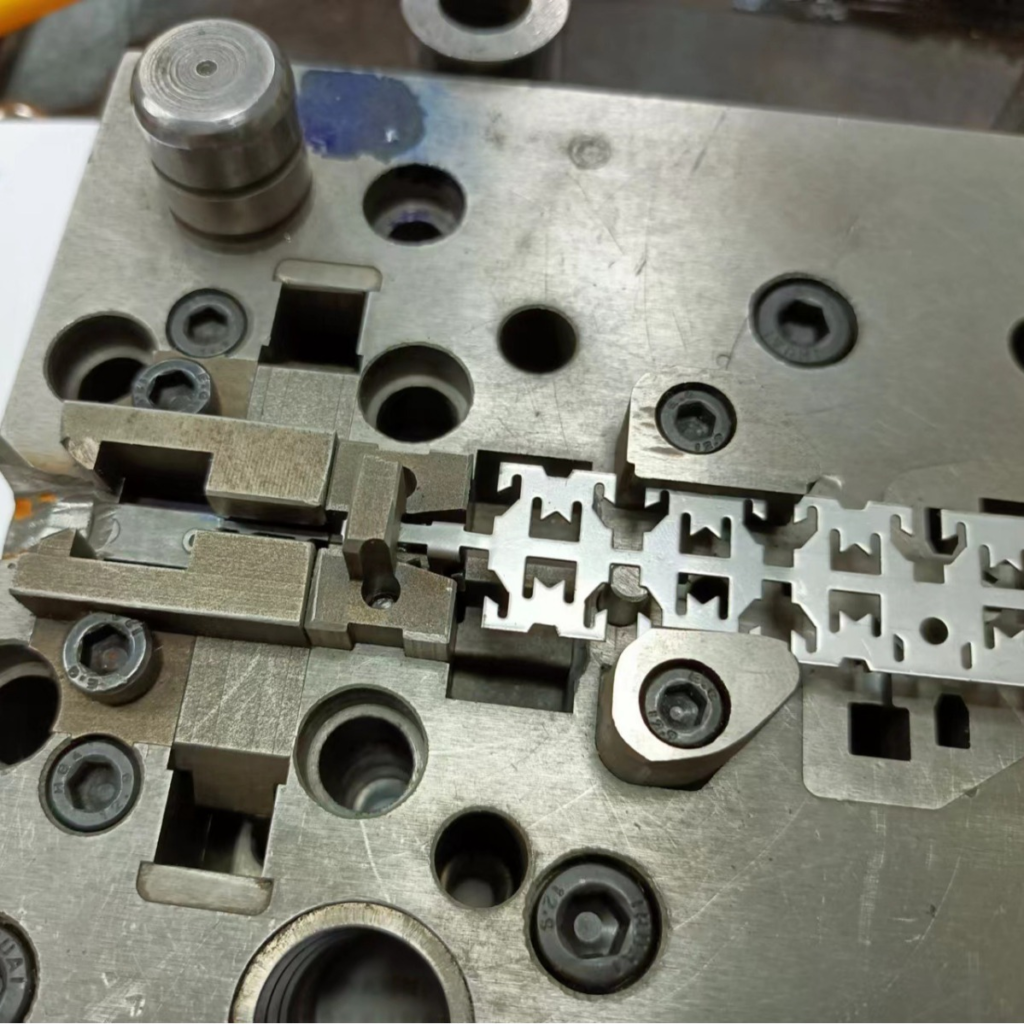
To design a stamping die, you can follow these steps: Initial Assessment and Planning, Concept development, Detailed Design and Engineering Analysis, Prototype Development, Final Design and Production.
These steps ensure precision and efficiency in the manufacturing process.
Now, let’s delve deeper into the comprehensive information for designing stamping dies, ensuring you have the knowledge to achieve optimal results.
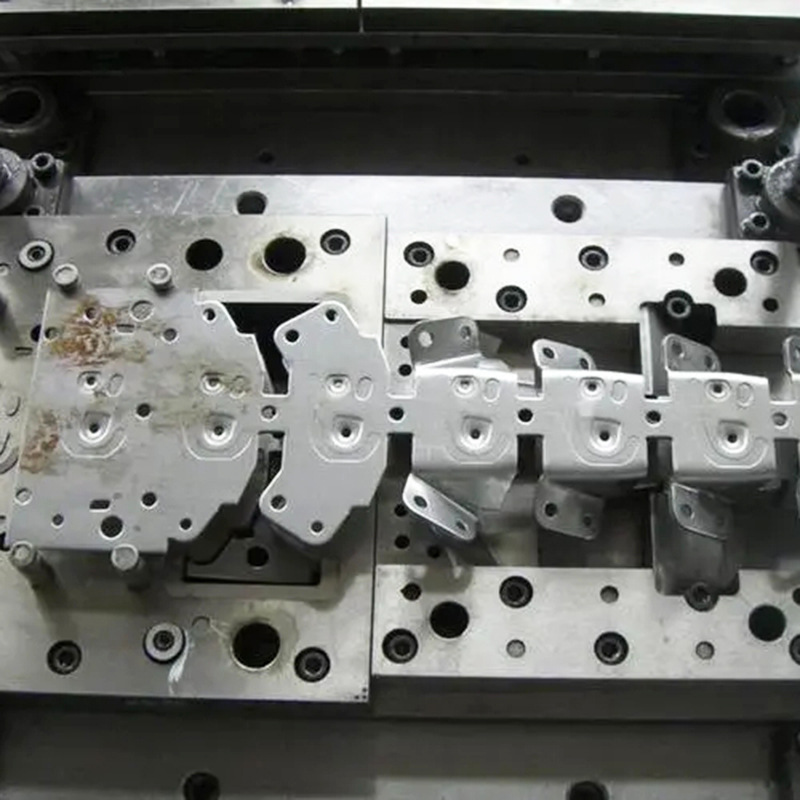
What is the Process of Designing Stamping Dies?
Designing stamping dies is a sophisticated engineering process critical in various manufacturing sectors. Generally, designing stamping dies includes the following phases:
1. Initial Assessment and Planning:
The design process begins with thoroughly assessing the part specifications that the die will produce. This includes understanding the dimensions, tolerances, and mechanical properties required of the finished parts. The production volume also plays a crucial role in influencing the die and the robustness of the design.
2. Concept development:
Designers create initial sketches and conceptual models, often using CAD software. This stage may involve multiple iterations to refine the functionality and feasibility of the die.
3. Detailed Design and Engineering Analysis:
This phase involves detailed CAD modeling and finite element analysis (FEA) to simulate the stamping process. These simulations help identify potential stress points, deformation risks, and other structural integrity concerns.
4. Prototype Development:
Before finalizing the design, a prototype die is often made. This allows for real-world testing and refinement, ensuring that the die will function as expected under operational conditions.
5. Final Design and Production:
After testing and adjustments, the final die design is completed. Production involves precise machining, assembly of die components, and rigorous quality control checks.
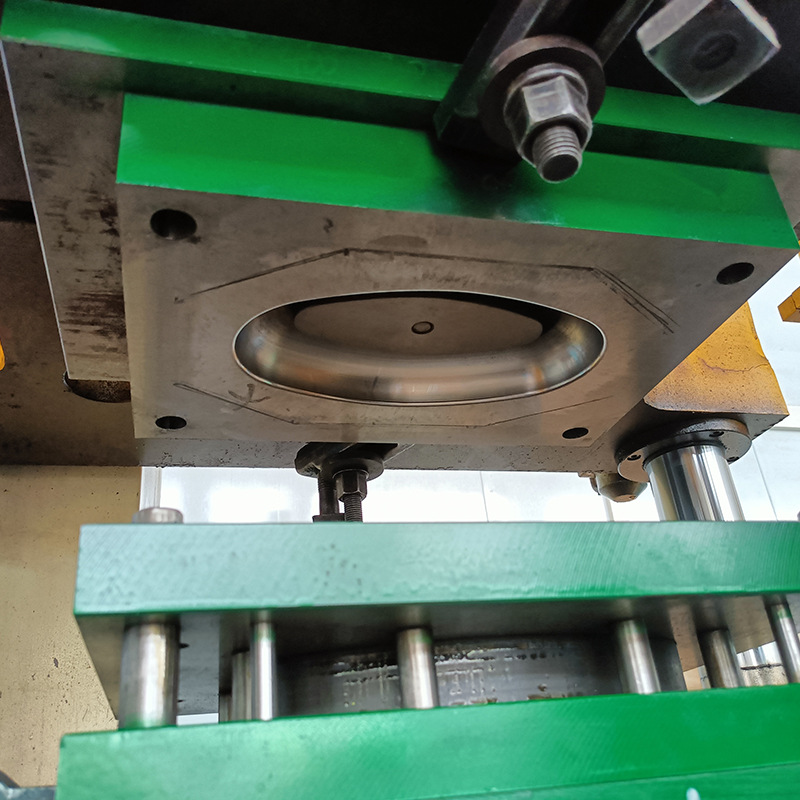
Factors to Consider before Designing Stamping Dies
1. Material Selection:
The choice of material for both the die and the workpiece is vital. Die materials must be durable and wear-resistant, typically high-carbon tool steel or carbides. The workpiece material will affect the die design, particularly regarding clearance and cutting-edge sharpness.
2. Type of Stamping Die:
The choice between single-stage and progressive dies depends on production volume and complexity. Progressive dies are suitable for high-volume production but are more complex and costly to design and manufacture.
3. Cost Constraints:
Designing cost-effective dies involves balancing between upfront costs and operational efficiency, including maintenance and life cycle costs.
4. Safety and Compliance:
Ensuring that the die design complies with industry standards and safety regulations is crucial. This includes considering the ergonomic safety of the operators.
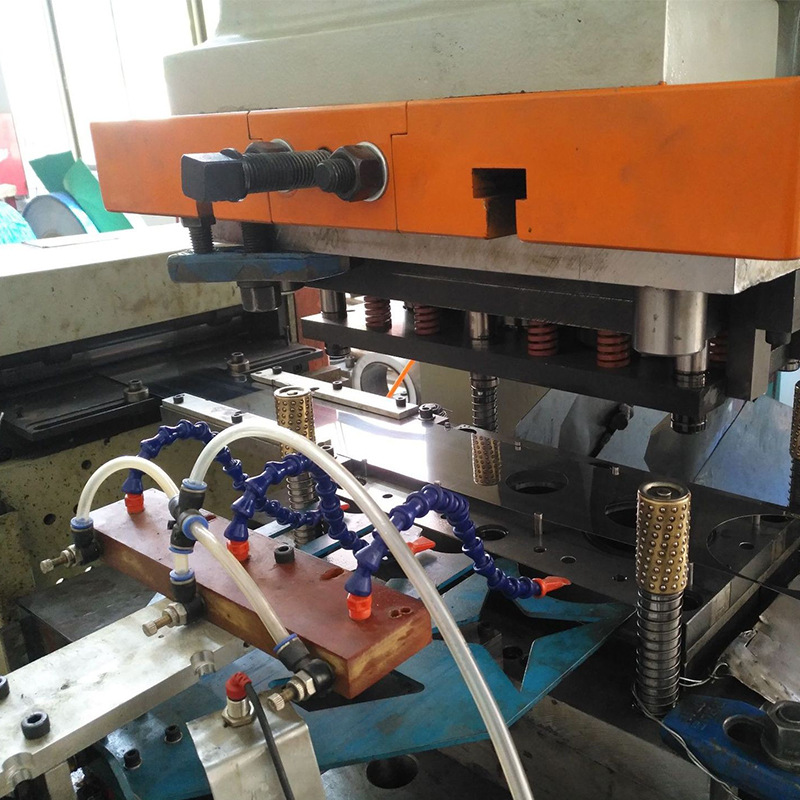
Design Considerations During the Stamping Die Process
1. Simplicity and Accessibility:
A simpler design often results in fewer manufacturing challenges and maintenance issues. It is also essential to consider the ease of access for cleaning, repairing, and replacing die components.
2. Tolerance and Precision:
Achieving the right balance of tight tolerances and manufacturability can prevent defects in mass production and ensure the longevity of the die.
3. Thermal and Mechanical Stress:
The die must withstand the thermal and mechanical stresses of operation without deforming. This requires careful analysis during the design phase, especially in high-volume or high-speed stamping operations.
4. Integration with Manufacturing Systems:
The die design should integrate seamlessly with existing or planned manufacturing systems, including presses and material handling systems.

Common Problems in Stamping Die Design
1. Premature Wear: It refers to the unexpected or accelerated degradation of die components. This usually occurs due to excessive friction, high operational loads, or inappropriate material choice.
Premature wear can lead to the loss of dimensional accuracy in produced parts, increased downtime, and higher maintenance costs.
Solution: To combat premature wear, selecting the appropriate materials for both the die and the parts being stamped is crucial. Tool steels like D2 or carbide materials may be used for their durability and resistance to wear.
Additionally, ensuring proper die maintenance and using adequate lubrication during stamping operations will help in extending the life of the die.
2. Material Springback: It occurs when the stamped material tends to revert slightly toward its original shape after being deformed in the die due to its elastic properties.
Solution: Adjusting the design of the die to over-bend or alter the bend angle can compensate for spring back.
Simulation software can be handy in predicting the degree of spring back and testing solutions before the die is manufactured.
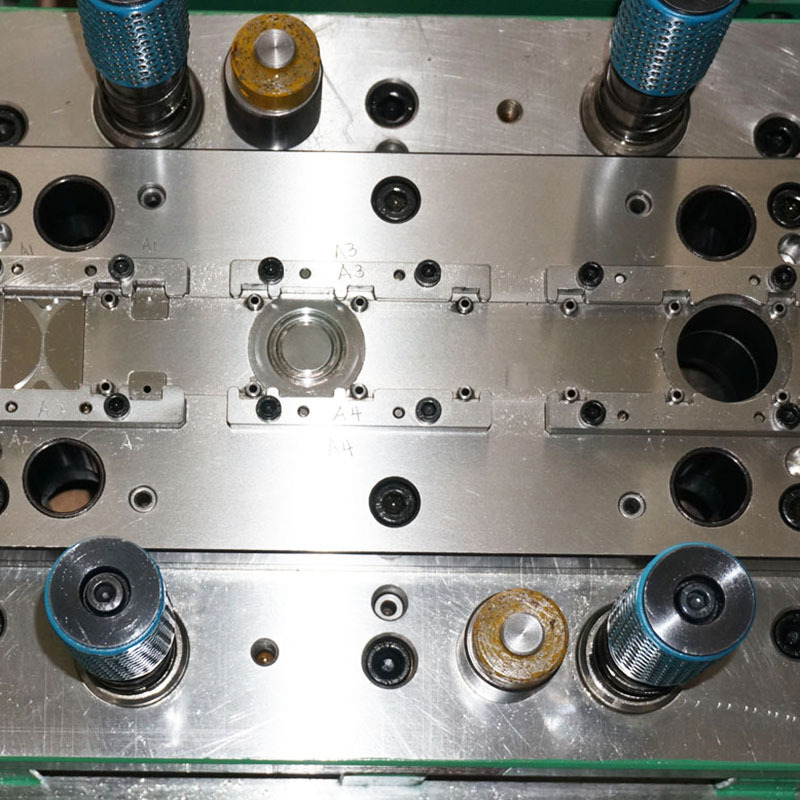
3. Misalignment and Jamming: Description: Misalignment in a die can result from improper installation, wear of components, or accumulation of debris.
This can lead to jamming, where parts do not move smoothly through the die, causing stoppages and potential damage to the die and parts.
Solution: Regular maintenance and precise calibration of the die setup are essential.
Using high-quality materials and components that can withstand operation stresses will reduce wear and misalignment. Cleaning the die regularly to remove debris also helps prevent jamming.
4. Die Galling: Description: Galling is a form of wear caused by adhesion between sliding surfaces, commonly seen in the punching and trimming operations in die processes.
This can severely affect the finish and dimensional integrity of the stamped parts.
Solution: Material choice is crucial in preventing galling; using dissimilar metals for the die and the workpiece can reduce adhesion.
Additionally, applying lubricants or using surface coatings like Chromium Nitride (CrN) can provide a barrier that minimizes direct metal-to-metal contact.
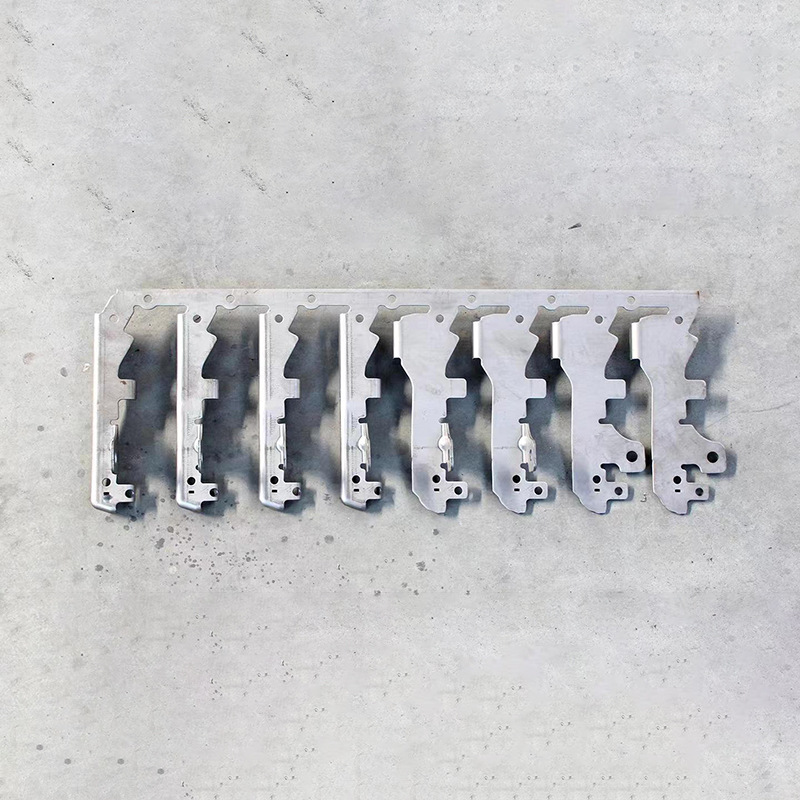
Summary
The process of designing stamping dies is intricate and requires a meticulous approach to ensure efficiency, durability, and precision in production.
By understanding the essential steps, considering key factors, and addressing common design challenges, we can develop effective stamping dies that meet the rigorous demands of modern manufacturing.
This approach not only ensures the production of high-quality parts but also enhances the overall operational efficacy of manufacturing processes.