Known for its precision, speed, and adaptability, CNC machining enables the production of high-quality parts with complex geometries and tight tolerances.
For engineers, product designers, and hobbyists alike, understanding the fundamental principles of CNC design is essential for creating functional, cost-effective parts.
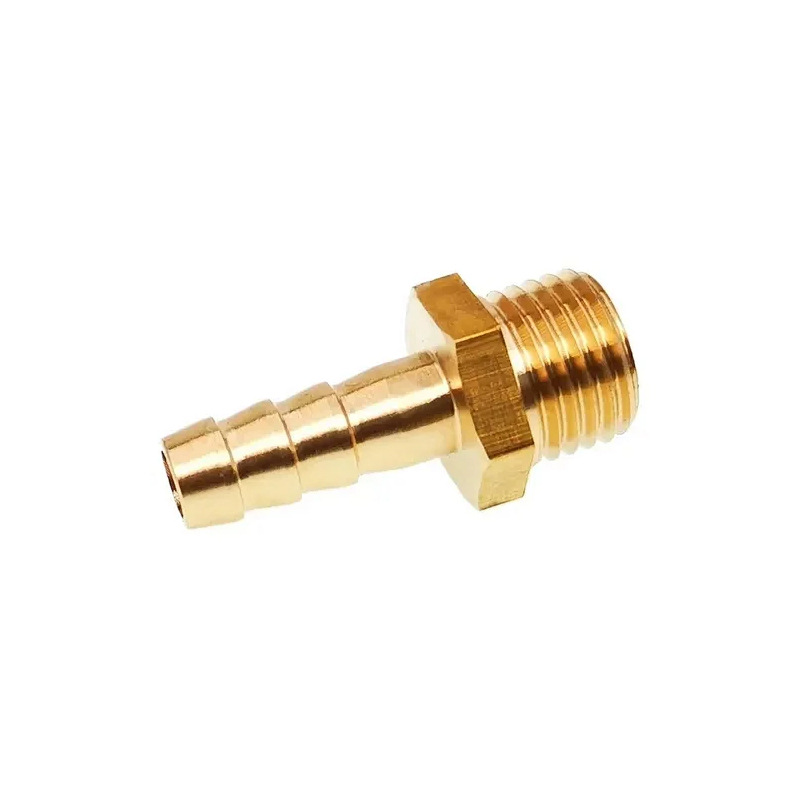
To design parts for CNC machining effectively, focus on manufacturability by avoiding thin walls, setting appropriate tolerances, and simplifying complex aesthetic features.
Choose suitable materials based on the part’s function and consider adding internal radii or fillets to ease machining.
Additionally, select relevant surface treatments for durability and follow best practices to ensure tool accessibility.
Now, let’s delve into the details of the information above.
-
Table Of Contents
-
1. How to Design Parts for CNC Machining: A Comprehensive Guide
-
2. Designing for CNC Machining: Key Considerations
-
3. Selecting the Right Material for CNC Machining
-
4. Enhancing Parts with Surface Treatments
-
5. Best Design Practices for CNC Machining
-
6. Advantages of CNC Machining
-
7. Summary
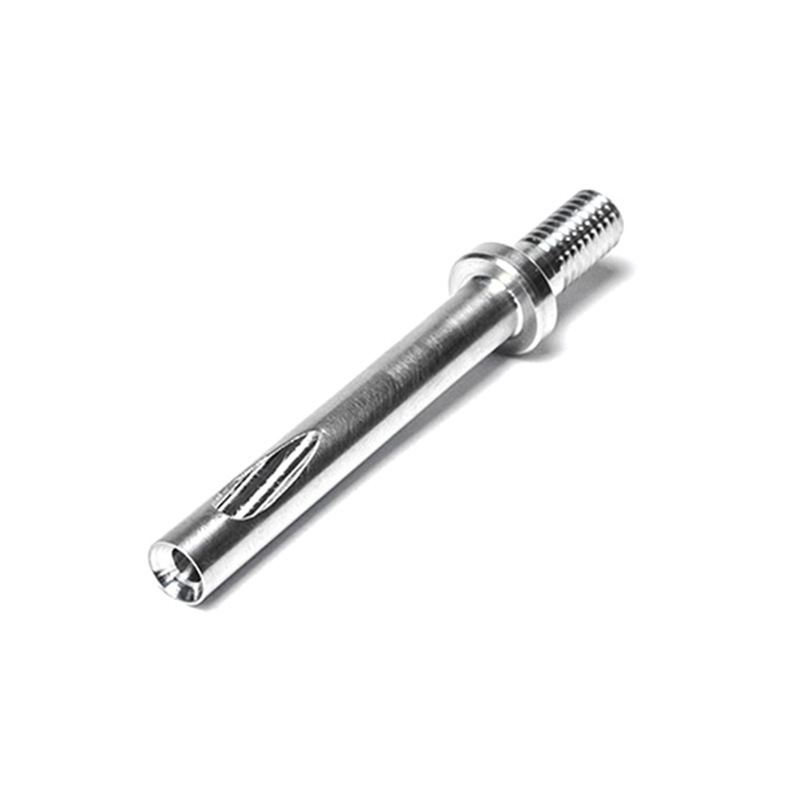
Designing for CNC Machining: Key Considerations
Designing parts for CNC machining demands a balance between manufacturability and functionality.
By following essential design tips, you can ensure that your parts are CNC-ready and optimized for quality.
1. Avoid Thin Walls: Thin walls increase the risk of deflection and vibration during machining, which can result in inaccuracies.
A minimum wall thickness of 0.8mm for plastics and 1.5mm for metals is typically recommended. This thickness provides enough rigidity for effective machining without compromising on structural integrity.
2. Maintain Appropriate Tolerances: Tight tolerances can drive up production costs significantly, as they require more precise machining.
A standard tolerance of +/- 0.125mm is sufficient for most applications—reserve tighter tolerances for critical areas where precision is essential, such as mechanical fits or load-bearing parts.
3. Limit Aesthetic Features: Design elements such as sharp edges or elaborate patterns may enhance a part’s appearance but often add complexity to the machining process, extending production time.
Simplify non-essential aesthetic details to maintain the part’s functionality without adding unnecessary manufacturing costs.
4. Add Internal Radii: Sharp internal corners are difficult to machine and may introduce stress concentrations that can compromise a part’s durability.
Adding a radius to internal vertical edges reduces material stress and makes the machining process smoother and more efficient.
5. Limit Deep Cavities: For deep cavities, maintain a depth-to-width ratio of 4:1 or less to avoid tool deflection and material warping.
If deeper cavities are necessary, multiple milling passes or specialized tools may be required, though these options can add complexity and cost.
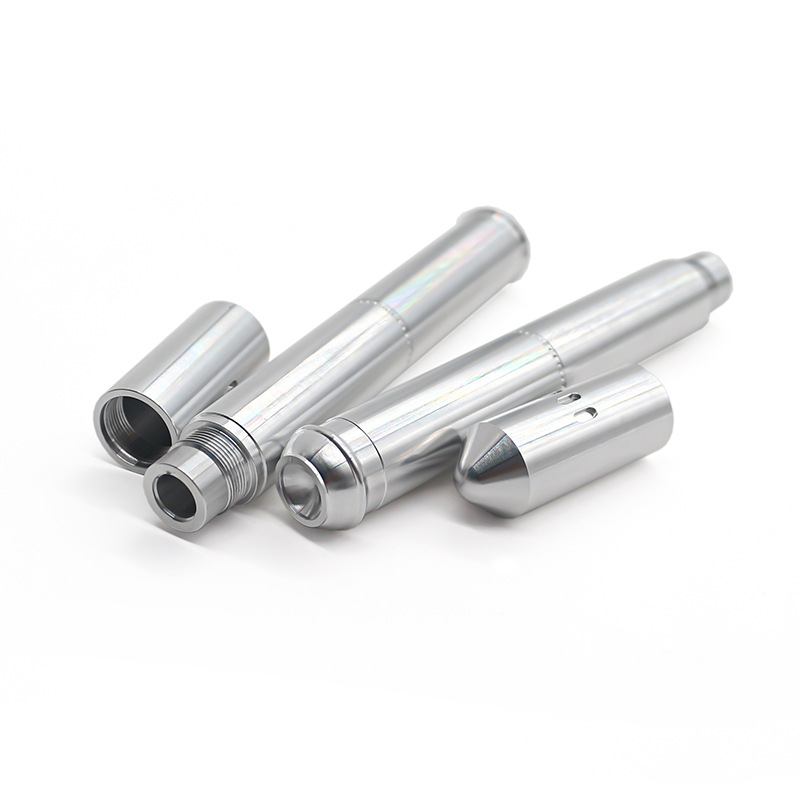
Selecting the Right Material for CNC Machining
Material selection is critical to CNC design, as each material brings distinct properties that affect a part’s performance. Here are some commonly used materials and their ideal applications:
• Aluminum: Lightweight, corrosion-resistant, and easy to machine, aluminum is a popular choice for aerospace, automotive, and consumer electronics components. It offers a balance of durability and machinability, making it suitable for precision parts.
• Steel: Known for its strength and durability, steel is ideal for parts that demand high strength-to-weight ratios, such as industrial machinery components. Its toughness, however, can make machining more challenging compared to other materials.
• Plastics: Common options include ABS, polycarbonate, and nylon, which are used for prototypes and consumer products. Plastics are lightweight, easy to machine, and often cost-effective, though they may lack the durability of metals in some applications.
When selecting a material, consider factors such as hardness, machinability, weight, and application-specific requirements, as these characteristics will impact the machining process and the part’s performance in its intended environment.
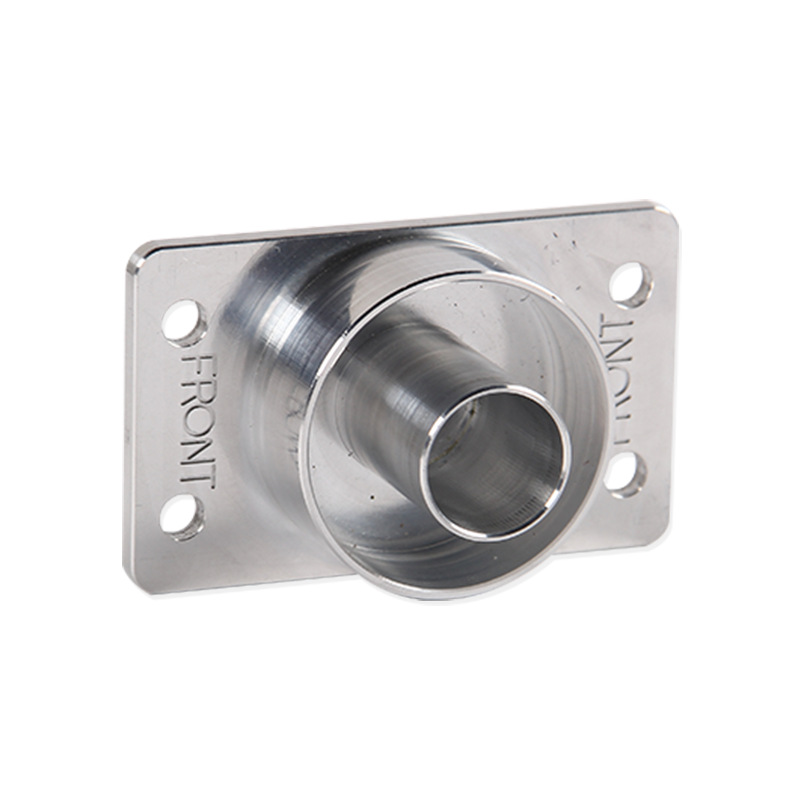
Enhancing Parts with Surface Treatments
Surface treatments improve the appearance, durability, and functionality of CNC-machined parts.
Choosing the proper surface treatment depends on the part’s use, required aesthetics, and environmental exposure. Here are a few popular options:
1. Anodizing: This treatment is commonly applied to aluminum, enhancing corrosion resistance and adding color. Anodized finishes are popular in consumer electronics and automotive parts for both protection and visual appeal.
2. Powder Coating: Powder coating adds a durable, protective layer to parts exposed to harsh environments. It’s widely used in outdoor products and machinery components where resilience to wear and weather is essential.
3. Polishing: For parts that require a smooth, high-gloss finish, polishing removes surface imperfections, improving both aesthetics and surface quality. Polishing is often seen in consumer products and decorative elements.
4. Electroplating: Electroplating a thin metal layer can increase wear resistance and electrical conductivity. This treatment is frequently used for electronic components.
Each surface treatment offers unique advantages, so it’s essential to consider the part’s end-use requirements when selecting the appropriate finish.
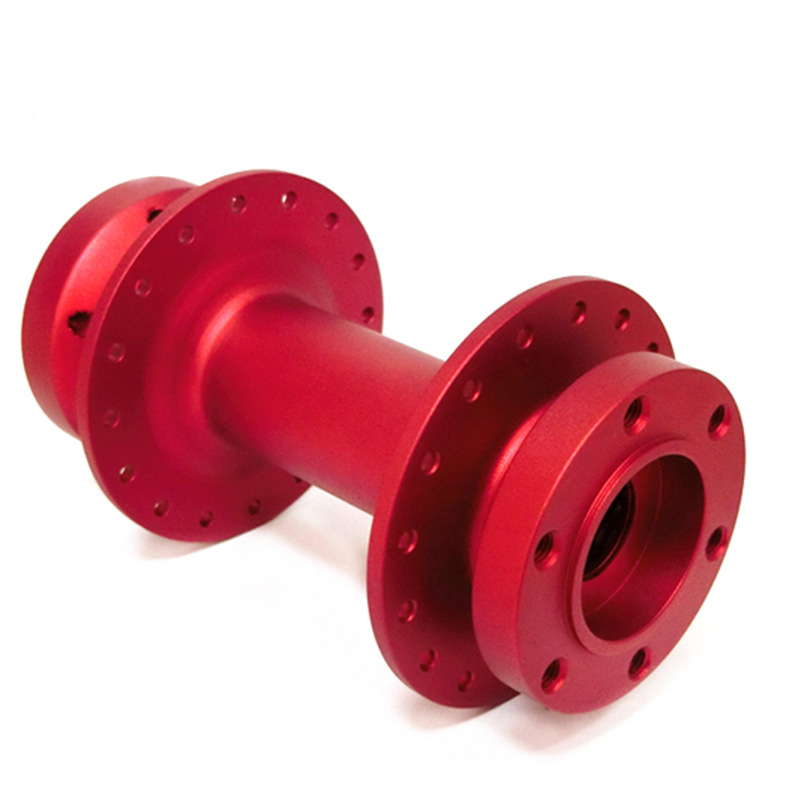
Best Design Practices for CNC Machining
Following best practices during the design phase can streamline the CNC machining process and enhance part quality:
• Avoid Unmachinable Features: Complex features like undercuts, sharp internal corners, and deep pockets are challenging to machine. Simplify designs to ensure all features are within the machine’s capabilities.
• Use Standard Tool Sizes: Standardizing tool sizes reduces the need for custom tooling, saving time and expense. When designing holes, for example, using common drill bit sizes minimizes production time and cost.
• Design for Tool Accessibility: Ensure that all areas of the part are easily accessible to the cutting tool. Features that require long-reach tools or complex setups can lead to inaccuracies and increased production times.
• Include Fillets: Adding fillets (rounded corners) reduces stress concentrations and facilitates smoother machining, helping to prevent tool breakage and enhance material durability.
Advantages of CNC Machining
CNC machining offers significant benefits over traditional manufacturing processes:
• High Precision: CNC machines produce parts with extremely tight tolerances, ensuring consistent quality in each production run.
• Repeatability: Once a design is programmed, a CNC machine can produce the same part with identical accuracy, ideal for mass production.
• Scalability: From prototyping to full-scale production, CNC machining is highly adaptable, suitable for projects of various sizes.
• Efficiency: CNC machines operate at high speeds, enabling faster production than manual methods, especially for large runs.
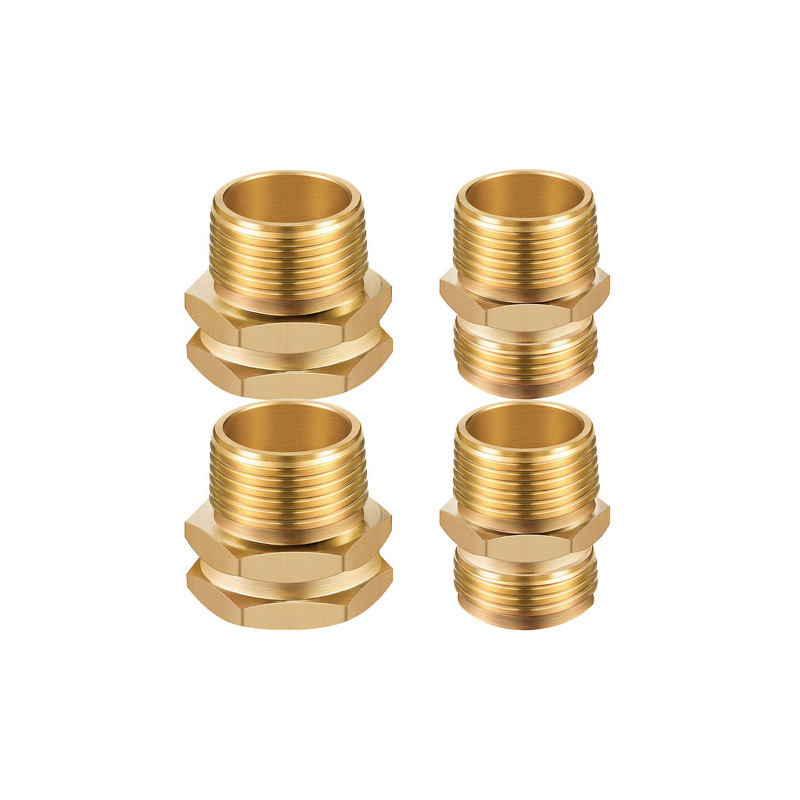
Conclusion
Designing parts for CNC machining requires a well-rounded approach that considers functionality, manufacturability, and cost-effectiveness.
By selecting appropriate materials, applying necessary surface treatments, setting realistic tolerances, and following best design practices, you can ensure high-quality, efficient CNC production.
Whether you’re an experienced engineer or a newcomer, applying these strategies will improve your designs and streamline the CNC machining process, paving the way for successful project outcomes.