In CNC machining, the depth of cut is a vital parameter that directly affects machining performance.
If not optimized properly, it can lead to excessive tool wear, poor surface finishes, or even machine failure.
Understanding how depth of cut influences machining and the key factors behind it is essential for anyone seeking high-quality, efficient results.
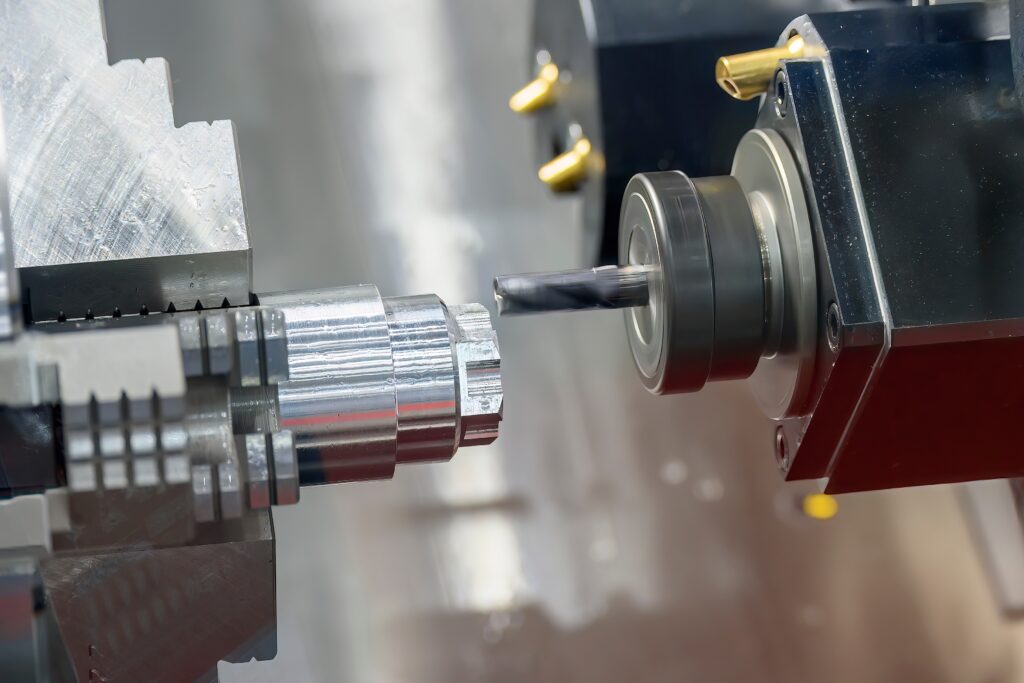
Depth of cut refers to the vertical distance a cutting tool penetrates the workpiece during a single pass.
This measurement determines how efficiently a machine can operate, influencing factors such as tool wear, surface quality, and machining time.
While deeper cuts can reduce overall machining time, they may also lead to quicker tool wear.
On the other hand, shallow cuts improve surface quality but can extend production time. Striking the right balance is critical to optimizing CNC machining performance.
Now, we’ll explore how the depth of cut affects CNC machining and provide insights into selecting the optimal depth for various applications.
-
Table Of Contents
-
1. How Does Depth of Cut in CNC Machining Impact Performance?
-
2. What is Depth of Cut in CNC Machines?
-
3. Key Factors Affecting Depth of Cut and Feed Speed
-
4. How Depth of Cut Influences Machining Performance
-
5. Recommended Depth of Cut for Different Applications
-
6. The Relationship Between Cutting Speed and Depth of Cut
-
7. Summary
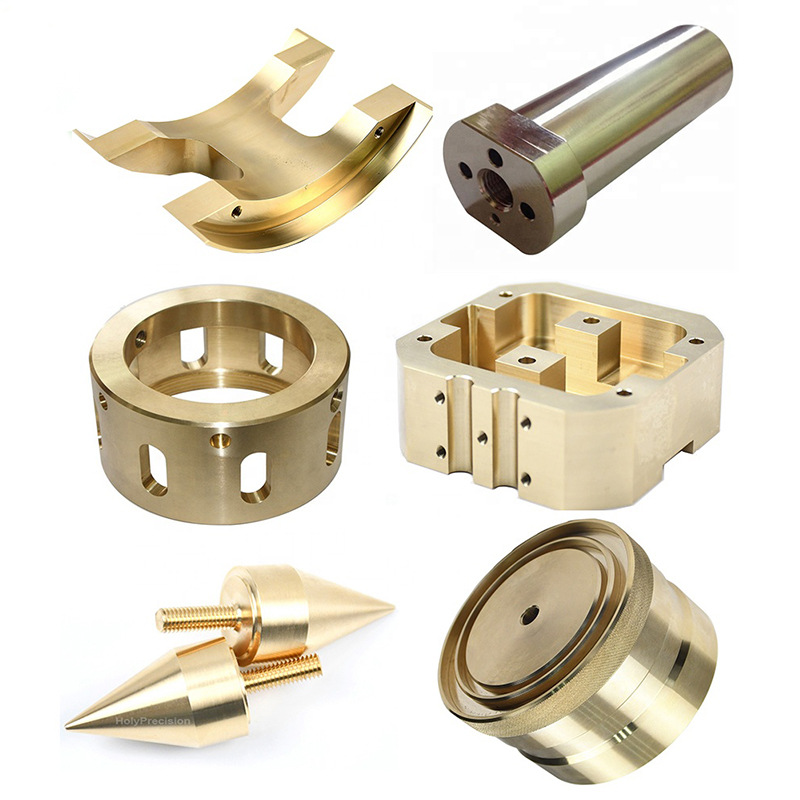
What is Depth of Cut in CNC Machines?
In CNC machining, the depth of cut is a primary factor in determining how much material is removed during each pass of the cutting tool.
It is measured as the vertical distance between the surface of the material and the tool’s tip.
For example, in CNC milling, where the cutting tool rotates while the workpiece remains stationary, the depth of cut determines how deeply the tool penetrates the material.
Typically, machinists calculate the depth of the cut relative to the tool’s diameter.
For large-diameter tools (over 20mm), the depth of cut is often around four times the diameter, while smaller tools can handle cutting depths up to ten times their diameter.
A well-optimized depth of cut ensures efficient material removal, a high-quality surface finish, and minimizes the risk of excessive tool wear.
Key Factors Affecting Depth of Cut and Feed Speed
Several factors impact the optimal selection of depth of cut and feed speed in CNC machining.
These elements must be carefully considered to ensure efficient cutting without compromising tool life or workpiece quality:
• Tool Material: Harder cutting tools can handle deeper cuts but may wear out faster if not managed correctly.
• Workpiece Material: Softer materials like aluminum can accommodate deeper cuts, while harder materials like steel may require more conservative settings.
• Tool Life: As cutting tools wear down, the depth of the cut should be adjusted to prevent tool breakage and extend its lifespan.
• Coolant Use: Adequate cooling reduces heat buildup, allowing for deeper cuts without overheating the tool or workpiece.
• Machine Rigidity: More stable CNC machines and tool holders can tolerate deeper cuts without causing tool deflection or vibration.
By accounting for these factors, machinists can balance the depth of cut and feed speed to achieve optimal results.
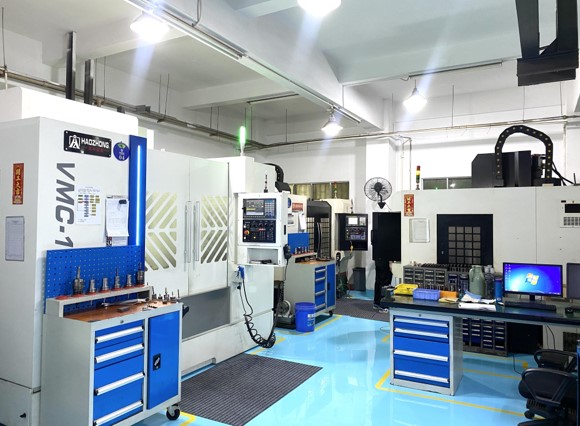
How Depth of Cut Influences Machining Performance
Depth of cut significantly affects various aspects of CNC machining performance. Properly adjusting this parameter can significantly enhance productivity and workpiece quality.
Here’s how the depth of cut impacts key areas:
• Tool Wear: Deeper cuts increase pressure and heat on the cutting tool, accelerating wear. While this speeds up material removal, it reduces the tool’s lifespan. In contrast, shallower cuts are gentler on the tool but take longer.
• Surface Finish: Shallow depths typically produce a smoother surface, as the tool exerts less force and creates finer, more accurate passes. Deeper cuts may lead to rougher finishes, often requiring additional finishing work.
• Heat Generation: Deeper cuts generate more heat, which can soften the tool and increase wear. Efficient cooling is critical when taking deeper cuts to maintain tool hardness.
• Machining Time: Deeper cuts reduce the required passes, decreasing overall machining time. However, they must be executed cautiously to avoid tool or workpiece damage.
Optimizing the depth of cut is essential to balance speed, quality, and tool longevity.
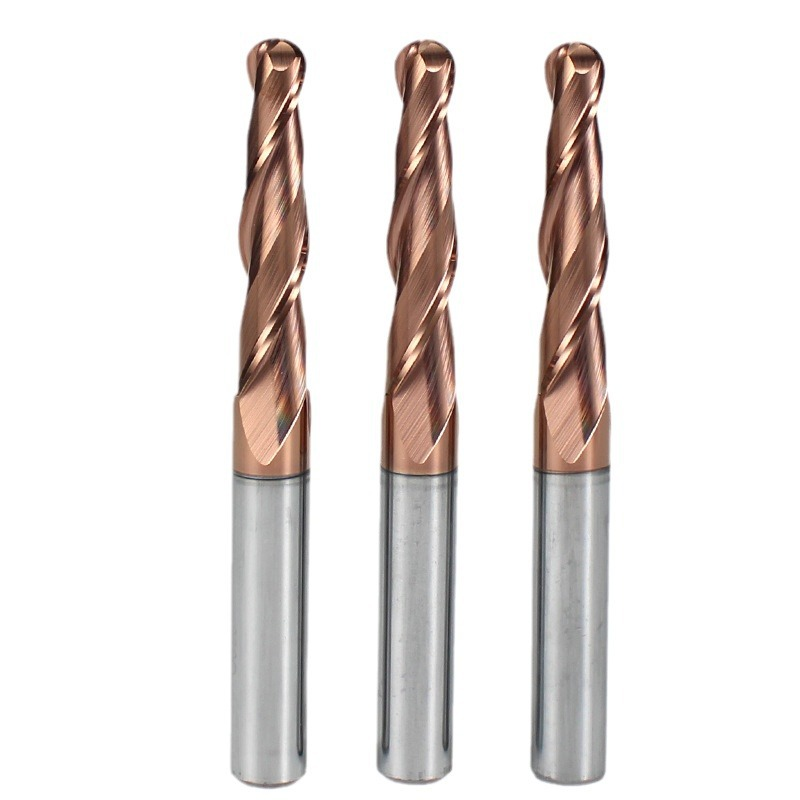
Recommended Depth of Cut for Different Applications
The ideal depth of cut varies depending on the material being machined and the specific requirements of the project. Here are some general guidelines:
• Soft Materials (e.g., Aluminum): These materials typically allow for deeper cuts, ranging from 0.5mm to 1mm or more. This helps reduce production time without significantly impacting tool life.
• Hard Materials (e.g., Steel): Harder materials require more conservative cutting parameters, with depths between 0.1mm and 0.5mm to preserve tool life and ensure accuracy.
• High Precision Work: Shallower depths of cut are preferred for projects that demand tight tolerances. This approach provides finer control and minimizes tool deflection.
Understanding the material properties and machining requirements is key to selecting the appropriate depth of cut.
The Relationship Between Cutting Speed and Depth of Cut
Depth of cut and cutting speed are closely related, and together, they significantly impact tool geometry and wear patterns.
Higher cutting speeds and deeper cuts strain the cutting tool, increasing the risk of accelerated wear. At lower speeds, a built-up edge (BUE) can form on the tool, compromising surface quality and reducing tool effectiveness.
The forces exerted on the tool’s cutting edges increase with larger depths of cut, which can lead to deflection and reduce the precision of the machined part.
Selecting the optimal combination of speed and depth of cut is crucial for preserving tool geometry and ensuring consistent machining performance.
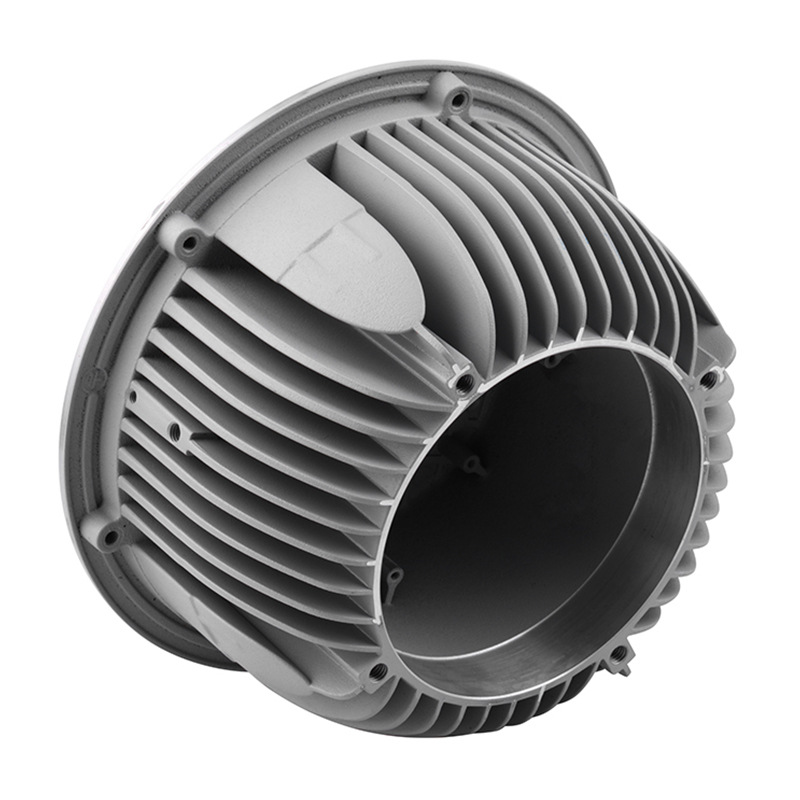
Conclusion
The depth of cut plays a pivotal role in CNC machining, influencing tool wear, surface finish, and overall machining time.
By understanding how this parameter affects performance and considering factors like material type, tool geometry, and machine rigidity, machinists can optimize the cutting process for better results.
A well-balanced depth of cut enhances productivity, extends tool life, and delivers high-quality machining outcomes.
Whether you’re dealing with soft or hard materials, the right depth of cut can make a significant difference in achieving efficient, cost-effective CNC machining operations.