High-volume precision metal stamping is an essential technology that combines speed, accuracy, and cost-efficiency to meet the demands of modern industries.
From automotive and aerospace to electronics and medical devices, this process plays a pivotal role in creating precise, durable, and high-quality components.
But how exactly does it work, and why is it so beneficial?
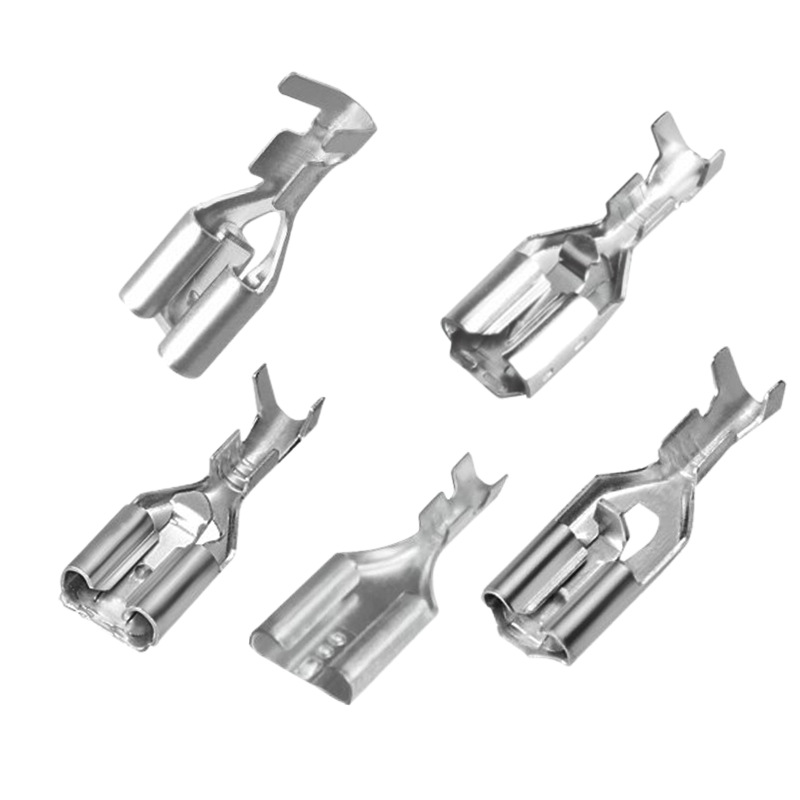
In essence, high-volume precision metal stamping involves the mass production of metal parts with consistent quality and intricate detail.
It enables businesses to produce thousands or even millions of identical parts, ensuring efficiency and cost-effectiveness.
This article explores how the process works, its applications, benefits, and how businesses can optimize it for maximum output.
If you’re looking to reduce costs, streamline operations, and meet the high demand for precision components, read on to discover why high-volume precision metal stamping is the solution you need.
-
Table Of Contents
-
1. How Can High-Volume Precision Metal Stamping Transform Your Manufacturing Process?
-
2. The Four Main Types of Metal Stamping Processes
-
3. Applications of High-Volume Precision Metal Stamping
-
4. Why Choose High-Volume Precision Metal Stamping?
-
5. Overcoming Challenges in Metal Stamping
-
6. How to Maximize Efficiency with High-Volume Precision Metal Stamping?
-
7. How to Minimize Environmental Impact in Metal Stamping?
-
8. Metal Stamping vs. Other Manufacturing Methods
-
9. The Future of Metal Stamping
-
10. Summary
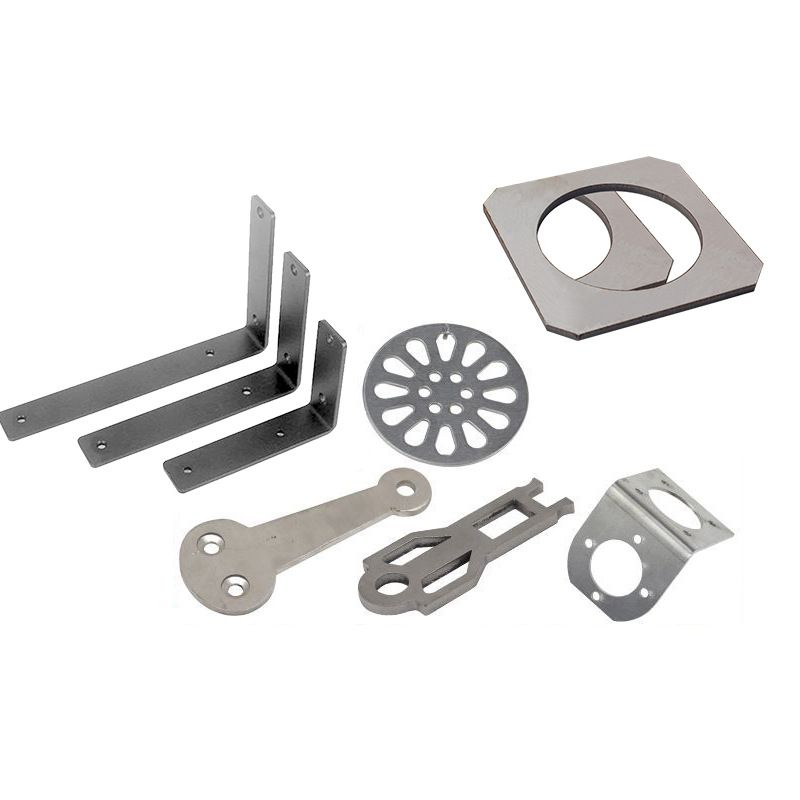
The Four Main Types of Metal Stamping Processes
To cater to diverse manufacturing needs, metal stamping employs various techniques, each offering unique advantages:
1. Progressive Die Stamping
o Process: A continuous strip of metal passes through a series of dies, each performing a specific operation like cutting, bending, or punching.
o Applications: Ideal for small, complex parts such as electrical connectors and fasteners.
o Benefits: High-speed production with consistent quality.
2. Deep Drawn Stamping
o Process: Metal sheets are drawn into die cavities to create hollow or cylindrical shapes.
o Applications: Used for making fuel tanks, medical containers, and kitchen sinks.
o Benefits: Seamless, durable, and lightweight components.
3. Transfer Die Stamping
o Process: Parts are transferred between multiple stations for various operations.
o Applications: Suited for large, complex parts like automotive body panels.
o Benefits: Greater flexibility to perform multiple operations in one setup.
4. Multi-Slide Stamping
o Process: Multiple slides work simultaneously to create intricate shapes.
o Applications: Popular for spring clips and electrical terminals.
o Benefits: Maximum design flexibility and precision.
Learn more about our advanced metal stamping services and how automation drives our manufacturing excellence.
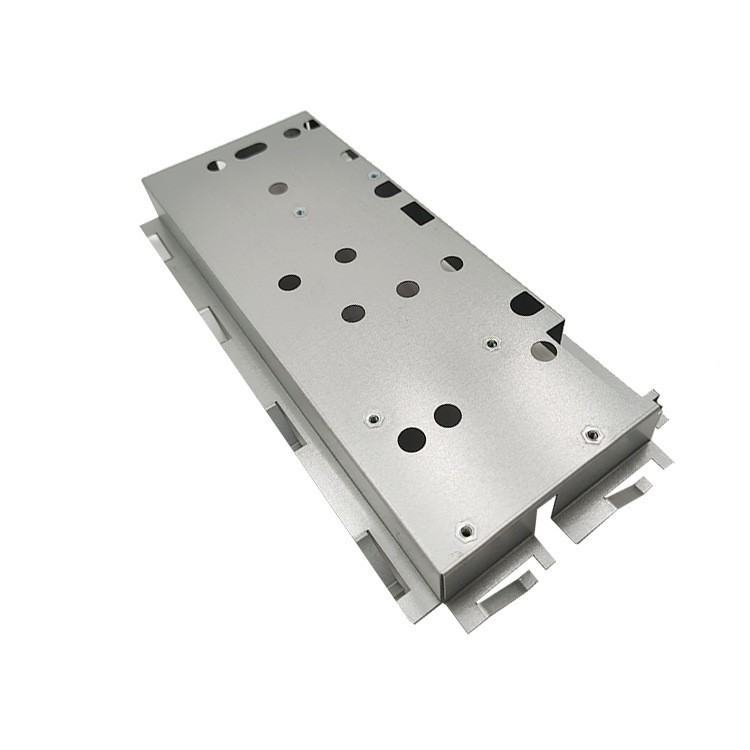
Applications of High-Volume Precision Metal Stamping
High-volume precision metal stamping supports a range of industries with unique demands. Below are key sectors where it shines:
1. Automotive Industry
o Components: Engine mounts, exhaust system parts, seatbelt clips.
o Importance: Ensures safety, durability, and performance in vehicles.
2. Electronics and Electrical Components
o Components: Connector pins, heat sinks, switch brackets.
o Importance: Supports miniaturized devices with precise, reliable parts.
3. Medical Equipment
o Components: Surgical tools, implantable devices, diagnostic equipment.
o Importance: Guarantees precision for critical healthcare applications.
4. Consumer Goods
o Applications: Kitchen appliances, furniture, power tools.
o Importance: Combines cost-efficiency with durability.
5. Aerospace Industry
o Components: Structural supports, brackets, lightweight panels.
o Importance: Delivers lightweight and precise parts to meet strict standards.
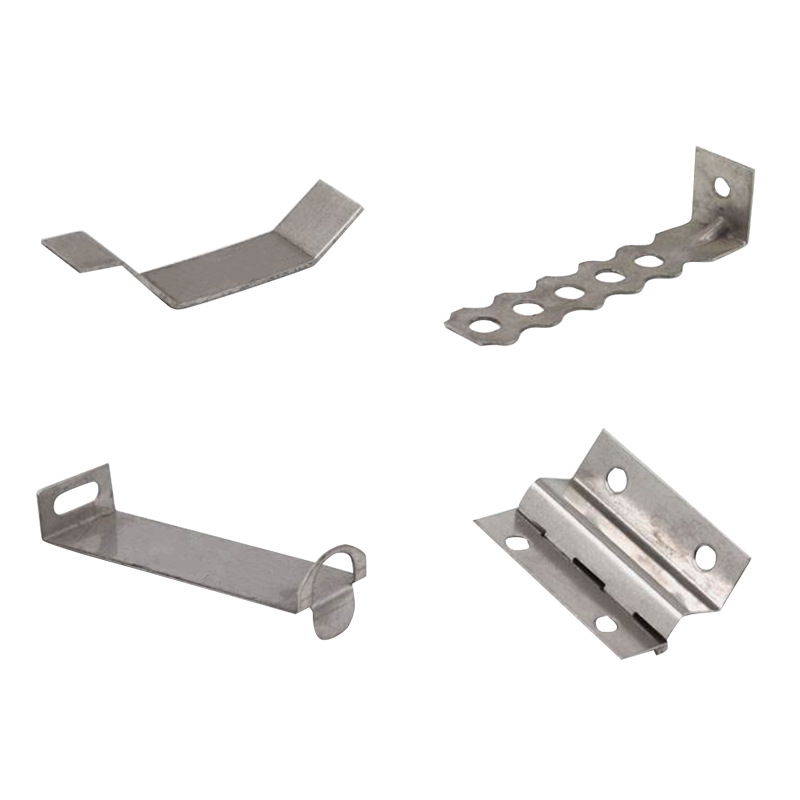
Why Choose High-Volume Precision Metal Stamping?
1. Cost Efficiency for Mass Production
Once the dies are prepared, the cost per unit decreases significantly, making this process ideal for large-scale orders.
2. Consistency and Accuracy
Tight tolerances ensure that every part meets exact specifications, reducing waste and ensuring quality.
3. Scalability
The process adapts to varying production volumes, from small custom batches to millions of identical parts.
4. Durable Tooling
High-quality dies are designed to endure extensive use, reducing downtime and maintenance costs.
Overcoming Challenges in Metal Stamping
While advantageous, the process does come with challenges:
1. High Initial Costs
Tooling and die setup require significant investment but become cost-effective for large runs.
2. Material Limitations
Thin metals may wrinkle, while thick metals need more force and specialized dies.
3. Complexity in Designs
Intricate shapes may demand advanced tooling and longer lead times.
Solution Tip: Collaborate with experienced stamping partners early in the design phase to address these challenges effectively.
Curious about material selection? Check out our guide on choosing the right metal for sheet metal fabrication.
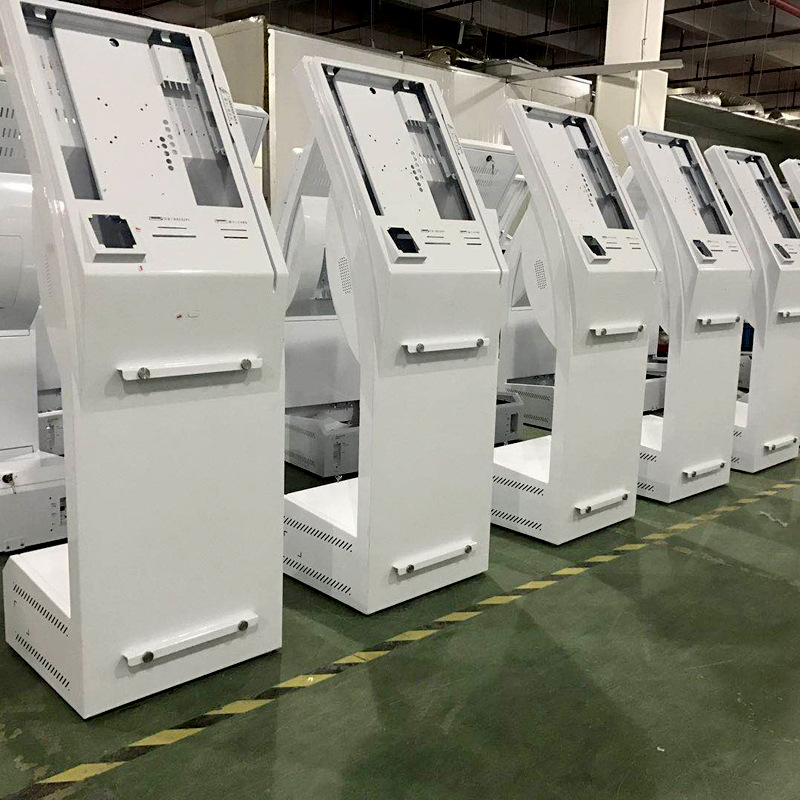
How to Maximize Efficiency with High-Volume Precision Metal Stamping?
Optimizing the process is essential to fully leverage the benefits of high-volume precision metal stamping.
Here are some practical tips:
1. Invest in Progressive Die Stamping
Progressive die stamping is ideal for large-scale production, offering efficiency and consistency by performing multiple operations in a single pass.
2. Use Quality Materials
Selecting durable and high-performing metals like stainless steel or aluminum ensures better results and reduces wear on the dies, extending their lifespan.
3. Automate Where Possible
Incorporating automation technologies, such as robotic feeders or real-time monitoring systems, can enhance speed, minimize human error, and reduce downtime.
4. Partner with Skilled Engineers
Working with experts during the design phase ensures dies are tailored to your specific needs, improving product quality and reducing costs in the long run.
With high-volume stamping processes, these strategies help businesses achieve greater precision, scalability, and cost-effectiveness.
Wondering about die longevity? Explore our insights on metal stamping die lifespan.
How to Minimize Environmental Impact in Metal Stamping?
Sustainability is becoming a top priority in manufacturing. Businesses can adopt several practices to reduce the environmental footprint of metal stamping:
• Material Optimization: Use recyclable metals and minimize scrap.
• Eco-Friendly Lubricants: Switch to biodegradable or low-impact alternatives.
• Energy Efficiency: Invest in high-efficiency presses to lower energy consumption.
These steps benefit the environment and reduce costs in the long run.
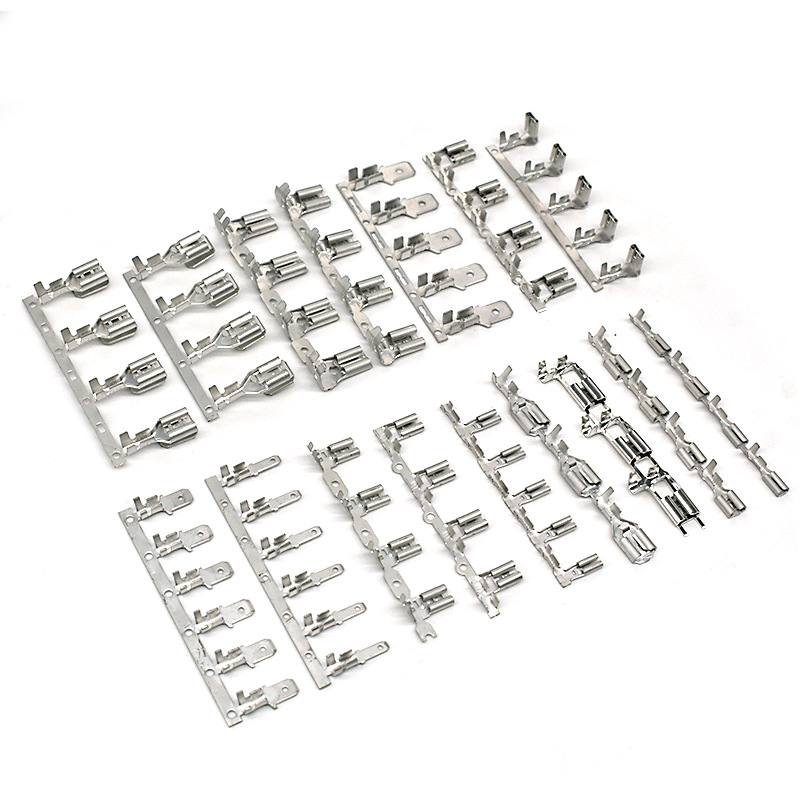
Metal Stamping vs. Other Manufacturing Methods
1. Stamping vs. Machining
• Stamping excels in speed and cost-efficiency for high-volume production.
• Machining is better for prototypes or small, intricate batches.
2. Stamping vs. 3D Printing
• Stamping is ideal for mass production and structural strength.
• 3D printing is suited for low-volume, highly complex parts.
The Future of Metal Stamping
Innovations are reshaping metal stamping:
• IoT and Smart Manufacturing: Real-time monitoring to enhance efficiency.
• Hybrid Methods: Combining traditional stamping with 3D printing for unique applications.
• Green Manufacturing: Increased use of sustainable materials and practices.
These trends promise even greater accuracy, efficiency, and sustainability.
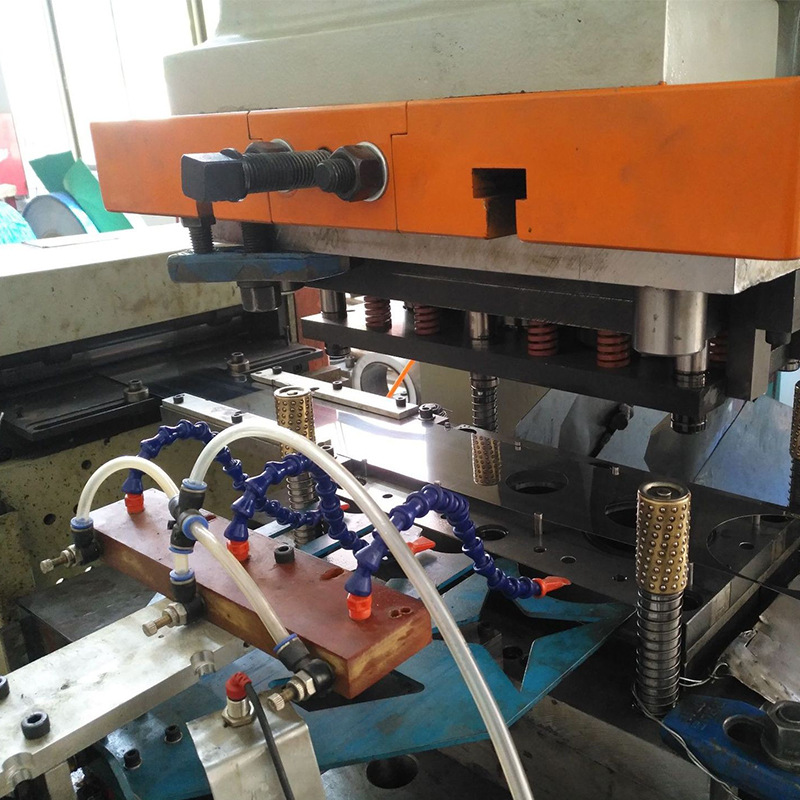
Conclusion
High-volume precision metal stamping is a cornerstone of efficient manufacturing.
Its ability to balance speed, accuracy, and cost makes it invaluable across industries.
By understanding its processes, applications, and future potential, businesses can make informed decisions that drive success.
High-volume precision metal stamping is the answer for those seeking to elevate their production capabilities.