Precision-Made Extruded Aluminum Enclosures
Affordable and high-quality aluminum enclosures for manufacturing sectors.
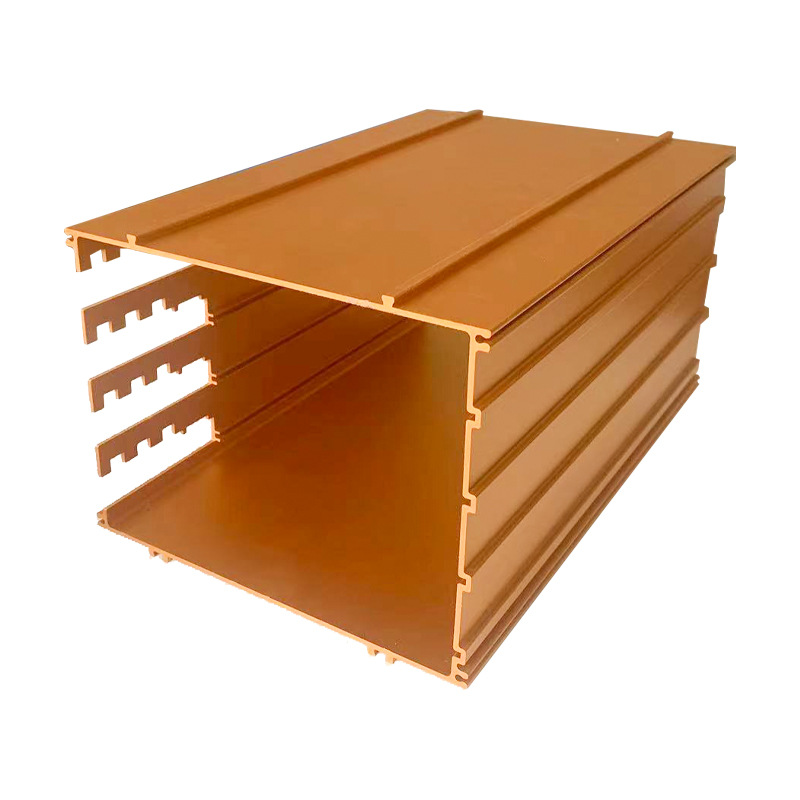
Lower MOQ, Certified Products
Annual output reaches 50,000 tons with competitive wholesale pricing. Save more and boost profits with a 200KG minimum order. ISO and EN compliant, ensuring strict production for guaranteed quality.
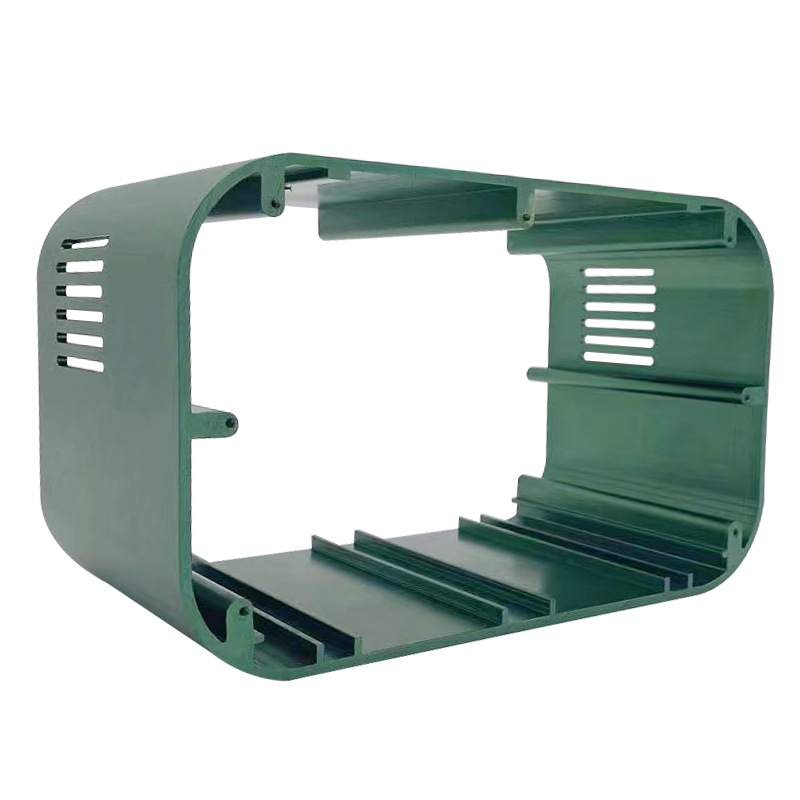
High Precision
Precision is critical in many industries, and custom Extruded Aluminum Enclosures delivers. The process allows for tight tolerances and consistent quality, ensuring that each part meets exact specifications.
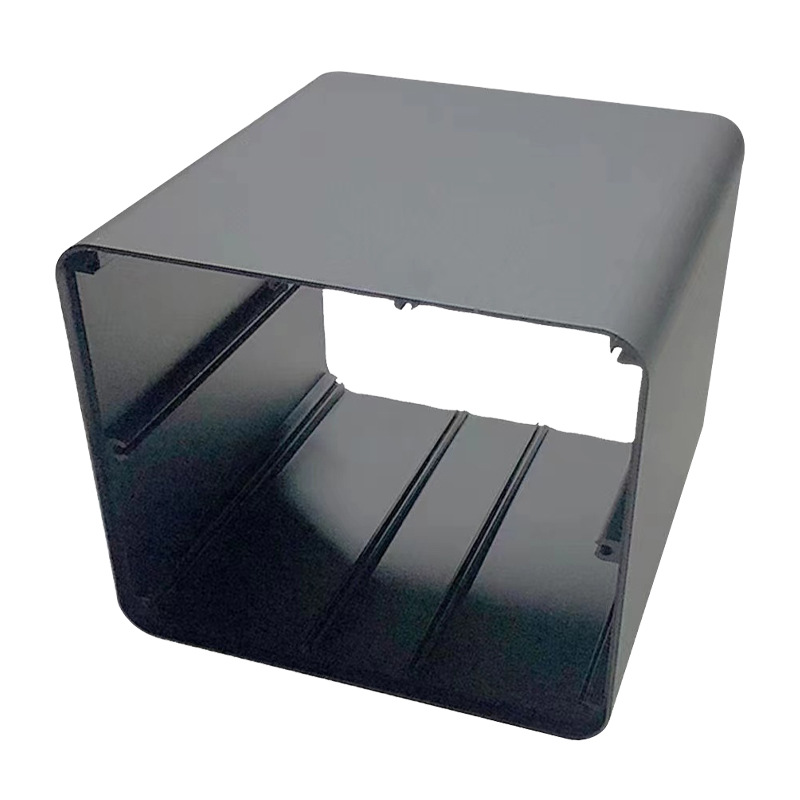
Flexibility in Design
One of the standout advantages of custom Extruded Aluminum Enclosures is the ability to produce highly complex and intricate designs. Whether it's a unique shape or a specific size, custom extrusion can accommodate a wide range of design needs.
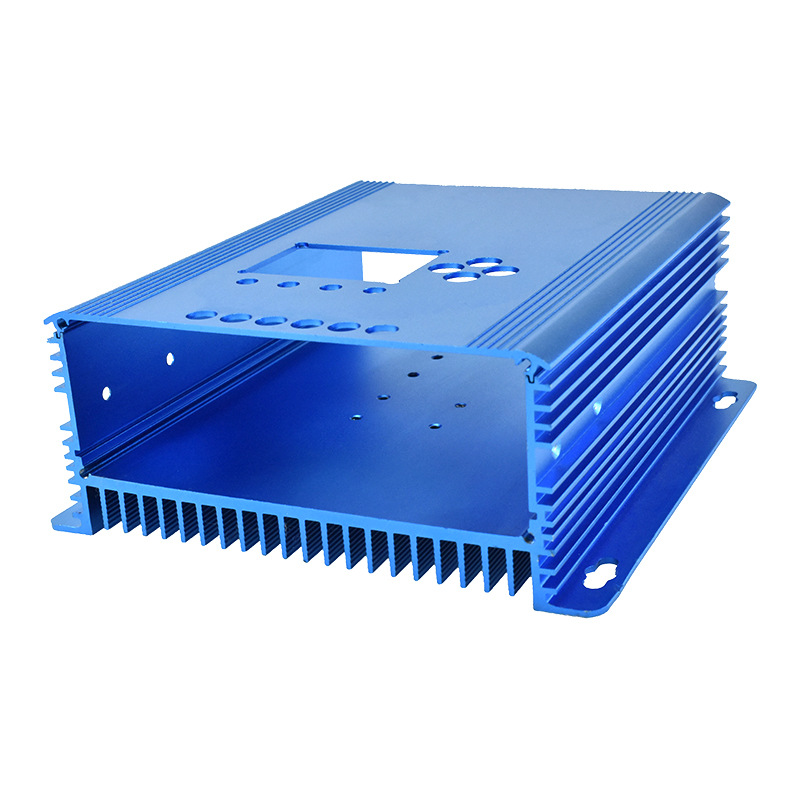
Cost-Efficiency
Compared to other manufacturing processes, custom Extruded Aluminum Enclosures can be more cost-effective, especially for large production runs. The ability to produce parts quickly and accurately reduces waste and lowers overall production costs.
Discover Our Quality Services
What is Extruded Aluminum Enclosures?
Extruded aluminum enclosures are protective housings made by forcing aluminum through a die to create long sections with specific cross-sectional profiles.
These enclosures are widely used to safeguard electronic components, provide structural support, and ensure effective heat dissipation in various applications, ranging from consumer electronics to industrial machinery.
Tailored to meet your needs
Reliable and affordable solutions
Types of Aluminum Used in Enclosures
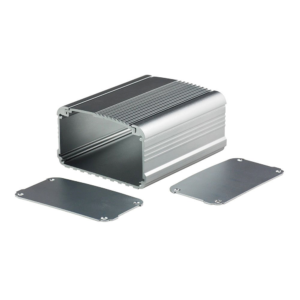
6061 Aluminum Alloy:
Properties: This alloy is known for its good mechanical properties and weldability. It offers excellent corrosion resistance and is easy to machine.
Applications: 6061 is often used in the production of extruded aluminum enclosures for consumer electronics, automotive parts, and aerospace components due to its strength and versatility.
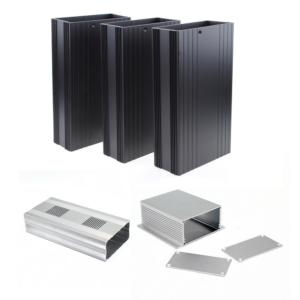
6063 Aluminum Alloy:
Properties: Known for its excellent extrudability, 6063 alloy provides a smooth surface finish and good corrosion resistance. It is slightly softer than 6061 but is ideal for complex shapes and profiles.
Applications: This alloy is commonly used in architectural applications, window frames, and complex extrusions for enclosures that require precise dimensions and high-quality surface finishes.
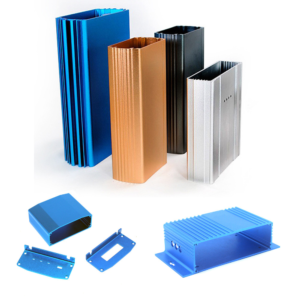
5052 Aluminum Alloy:
Properties: This alloy offers high strength and excellent resistance to corrosion, particularly in marine environments. It is also known for its good formability.
Applications: 5052 is used in the manufacturing of enclosures that require a combination of strength and resistance to harsh environments, such as marine and industrial applications.
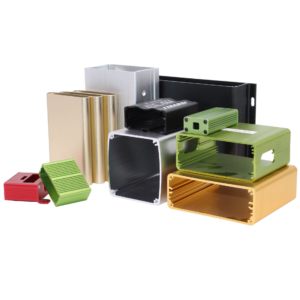
3003 Aluminum Alloy:
Properties: Known for its excellent corrosion resistance and good workability, 3003 is a popular choice for applications where moderate strength is sufficient.
Applications: This alloy is often used in the production of general-purpose enclosures and housings that do not require high structural strength but need good corrosion resistance and formability.
Available Finishes
This finishing option is the fastest available. Parts may have visible tool marks and possibly sharp edges or burrs, removable on request.
You can use sandblasting to peel paint, smooth out rust, take bumps and mars from stuff, and basically make things clean. Ironically, you can also sandblast things to scuff them up by etching the surface and give something a little bit of ‘tooth’ so that paint will stick better.
Type II anodizing enhances corrosion resistance. It allows parts to be colored in various shades like clear, black, red, and gold, typically for aluminum. Type III provides a thicker, wear-resistant layer as well as the corrosion resistance of Type II.
This process involves spraying powdered paint onto a part, which is then heated in an oven. The result is a tough, wear- and corrosion-resistant coating, more robust than traditional paint methods. A broad range of colors is available for achieving the desired look.
Plating involves coating a conductive surface with a thin metal layer. This method is often used to prevent corrosion, enhance durability, modify surface friction, and boost aesthetics.
Can't find the finish you require? Send us an RFQ, and we'll explore a finishing solution for you.
Precision Capabilities
+/- .005mm Tolerences
Tolerances as precise as +/- .005mm on one or more dimensions of an extrusion, depending on its shape.
0.4 mm Walls
You can make walls as thin as 0.4 mm on one or more dimensions of an extrusion, depending on its the shape.
1.2 mm Holes
Few extruders can handle 1.2mm holes with +/- 0.03mm tolerances, but many trust Partzcore with this challenge.
Key Principles of Good Design

Design for Functionality

Design for Manufacturability

Design for Cost-Effectiveness
Design Considerations

Wall Thickness

Tolerances

Surface Finish
Applications of Aluminum Enclosures
Aluminum enclosures are used in a wide range of applications due to their versatility and beneficial properties. Some common applications include:
Benefits of Using Aluminum for Enclosures
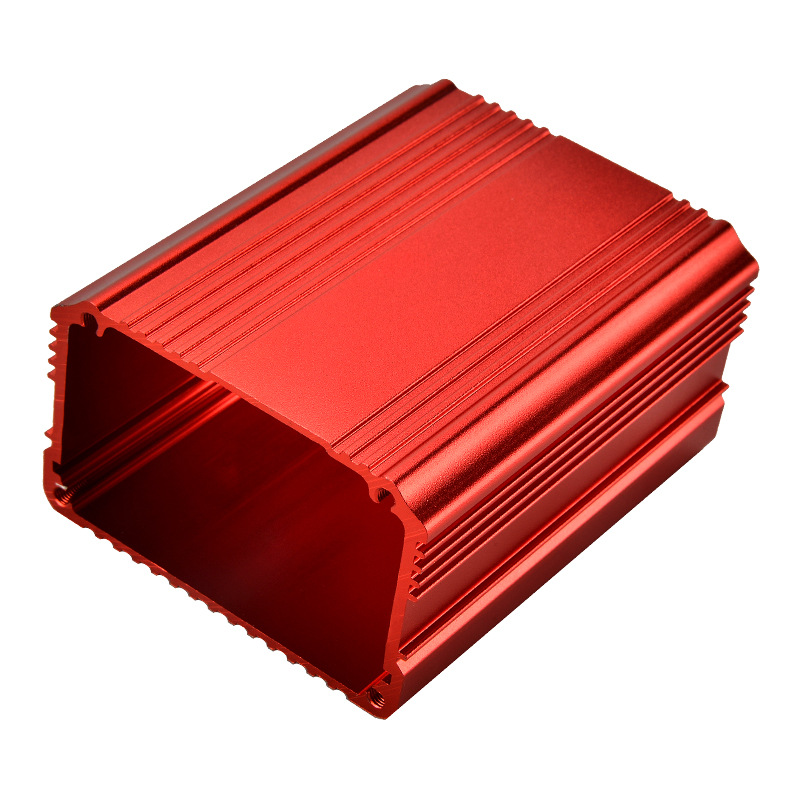
Lightweight
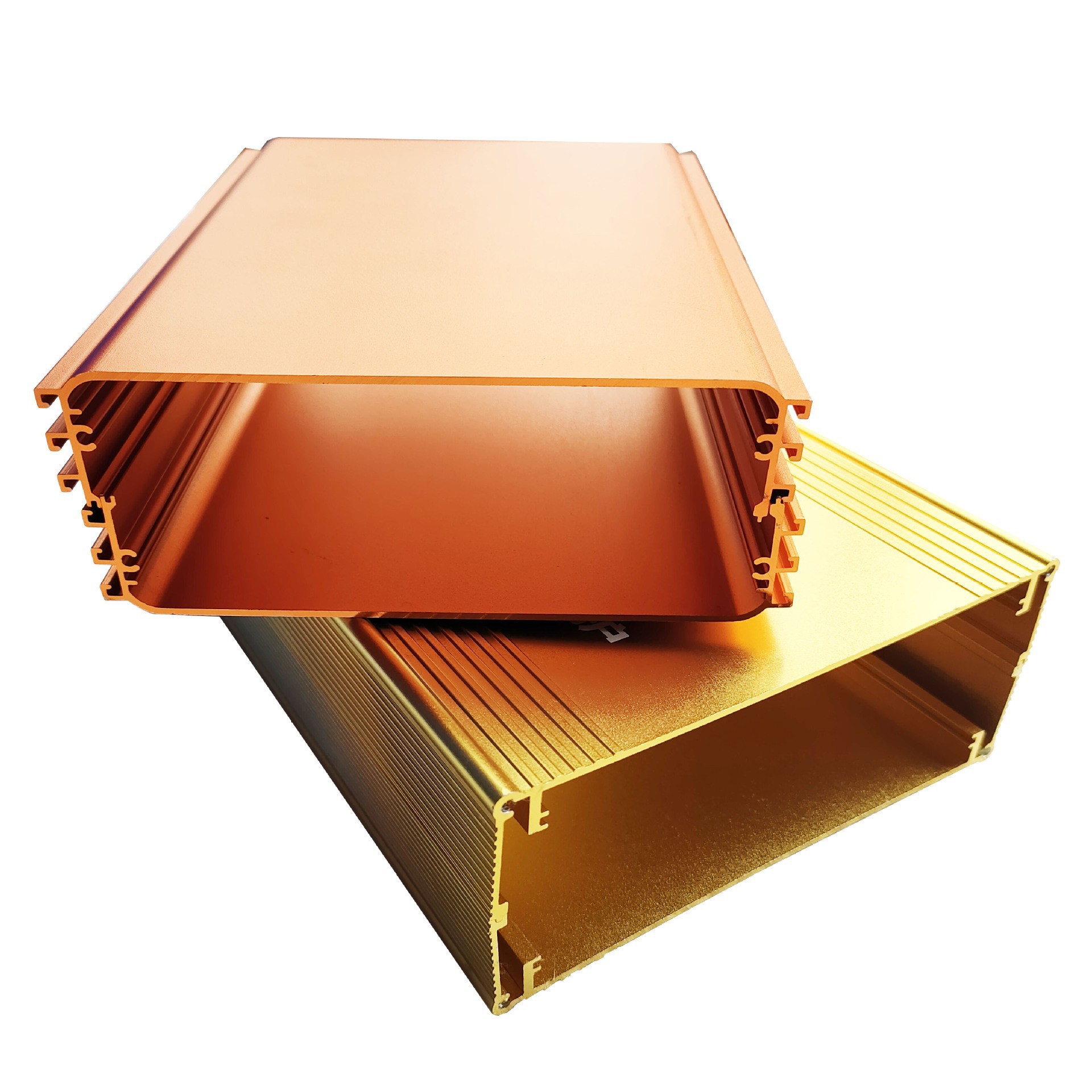
Strength and Durability
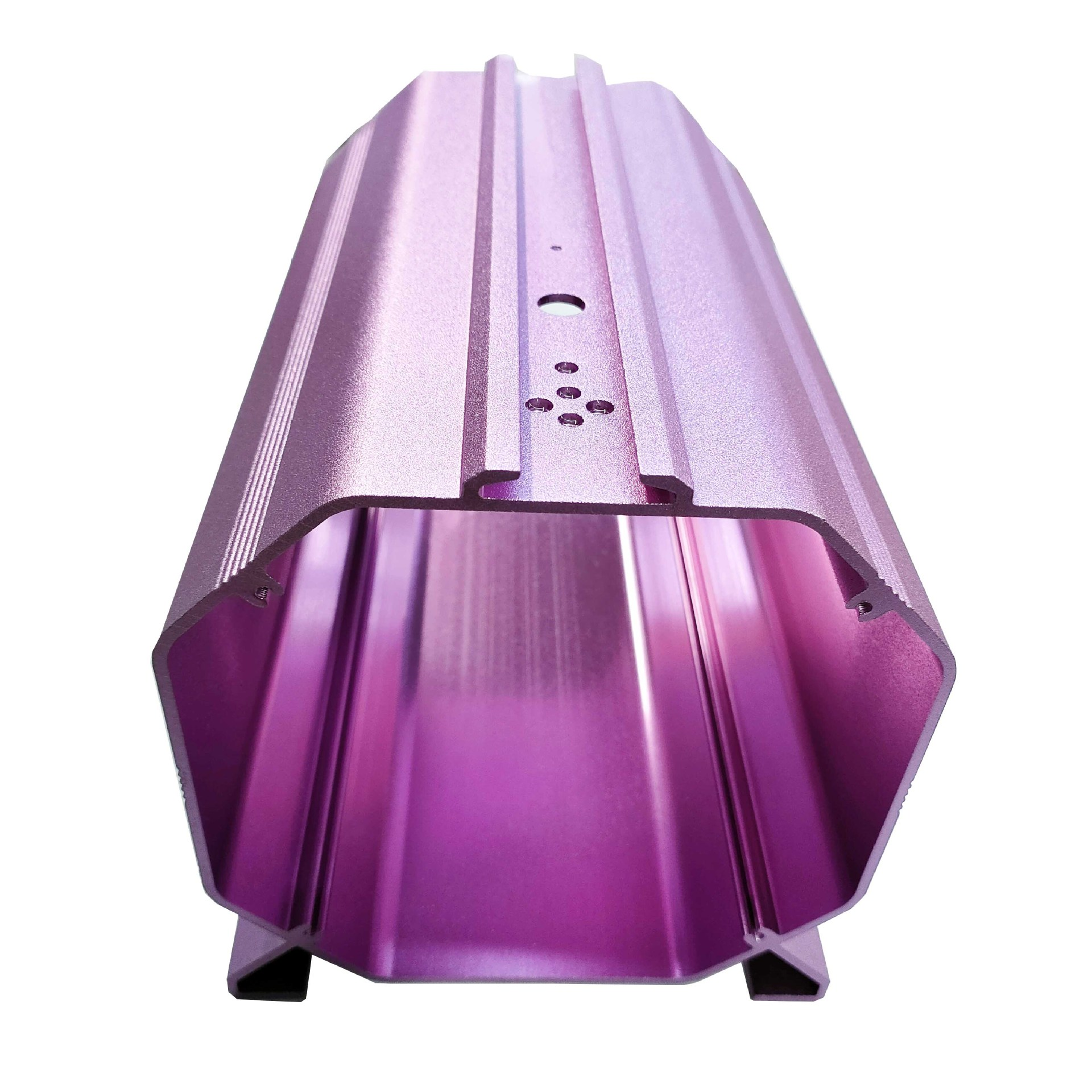
Thermal Conductivity
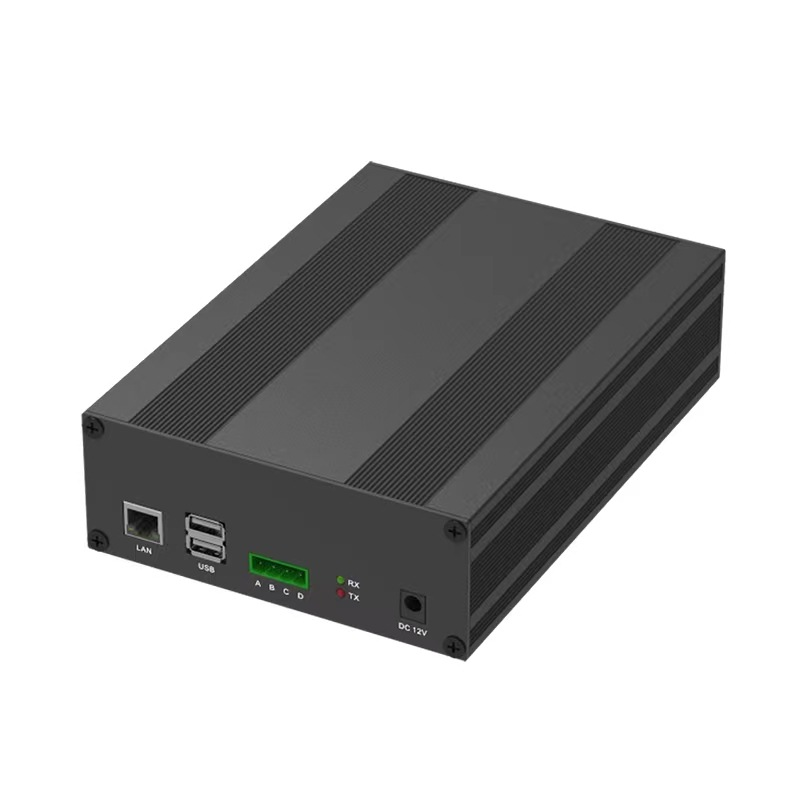
Corrosion Resistance
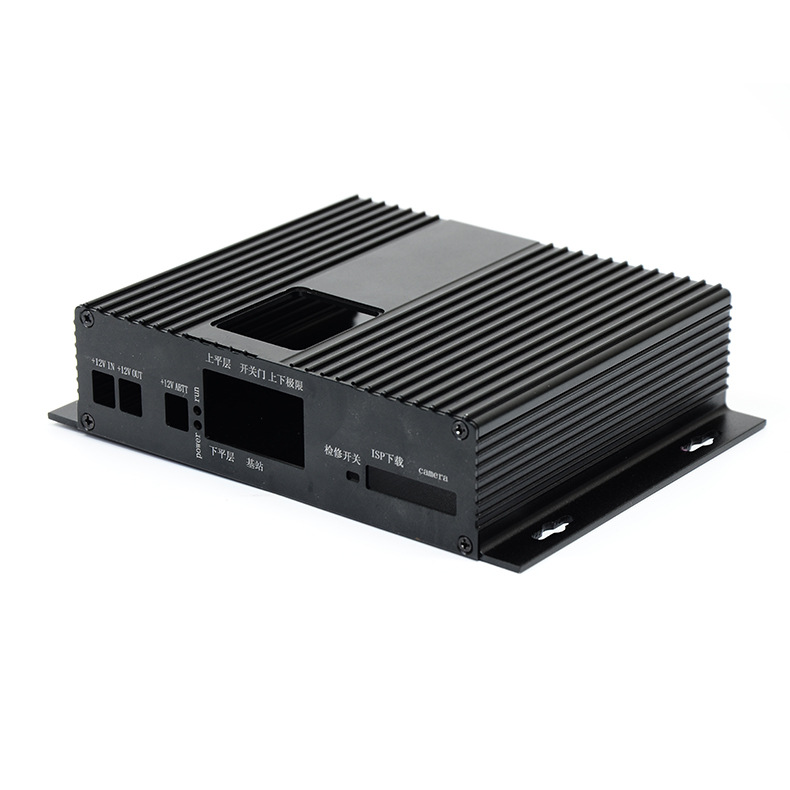
Ease of Fabrication
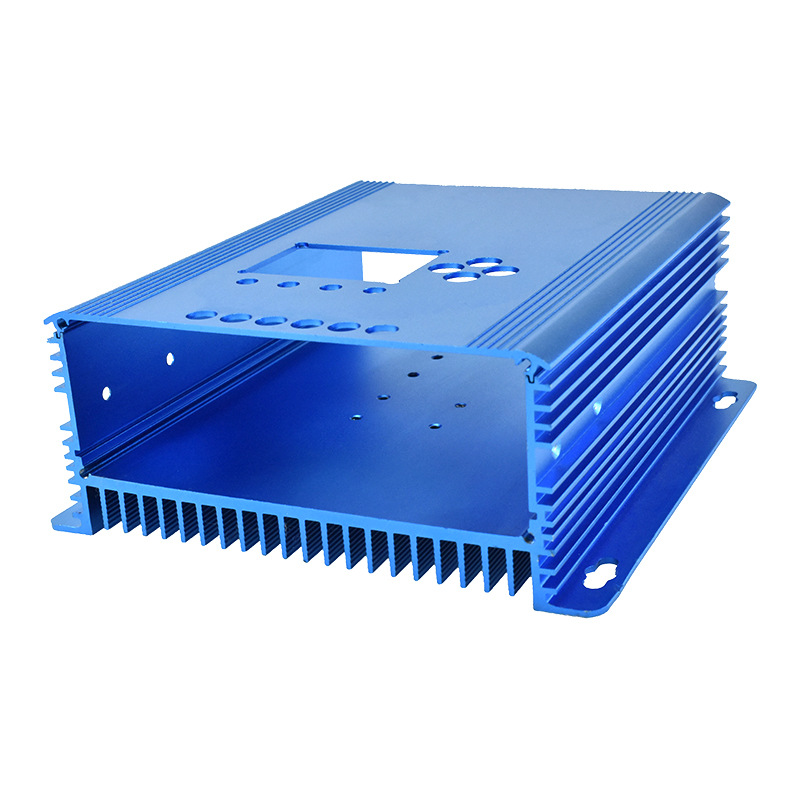
Recyclability
FAQs
Extruded aluminum enclosures are lightweight, durable, corrosion-resistant, and offer excellent thermal conductivity. They can be customized in various shapes and sizes, making them suitable for a wide range of applications.
Yes, extruded aluminum enclosures are ideal for outdoor use due to their natural corrosion resistance and the additional protection provided by anodizing and other surface treatments.
Extruded aluminum enclosures are highly customizable, allowing for specific shapes, sizes, surface finishes, colors, and additional features like holes and cutouts to meet various application needs.
While the initial cost of aluminum may be higher than some materials, its durability, low maintenance requirements, and recyclability often result in long-term savings.
Industries such as electronics, automotive, telecommunications, and renewable energy benefit significantly from the use of extruded aluminum enclosures due to their lightweight, durability, and excellent thermal conductivity.
Extrusion dies are relatively cheaper than die-cast molds and are easier to make. Extrusion is an adaptable and cheaper process that can be adjusted at short notice. This makes extrusion ideal for shorter production runs. In contrast, die-casting is more cost-prohibitive due to the complexity and expense of creating the molds.
Die casting involves forcing molten metal into a mold under high pressure. The molds used in die casting are typically made of hardened steel and can be very expensive to produce. Additionally, the die-casting process requires specialized equipment and can have higher operating costs compared to extrusion.
Extrusion, on the other hand, uses dies that are typically made of softer materials such as tool steel or even aluminum for short production runs. The lower cost of dies and the simplicity of the extrusion process make it a more economical option for many applications. This cost advantage is particularly significant for small to medium-sized production runs where the high initial cost of die casting molds cannot be justified.
we can help
Provide Customized Solutions
Contact Partzcore (sales@partzcore.com) to get a free quote and expert advice on custom metal parts. Our team will provide the right solution for your project.
Tell Us What You Need
Please share your specific needs with us, including drawings, reference images, and your ideas, so we can turn them into reality.
Professional Team
We will analyze your requirements and drawings to provide the optimal solution, along with a detailed quote within 24 hours.
Approve for Mass Production
Upon receiving your approval and deposit, we will proceed with mass production and manage the shipping process.