In today’s manufacturing world, precision and efficiency are paramount. CNC milling, a computer-controlled subtractive manufacturing process, revolutionizes how we produce intricate parts.
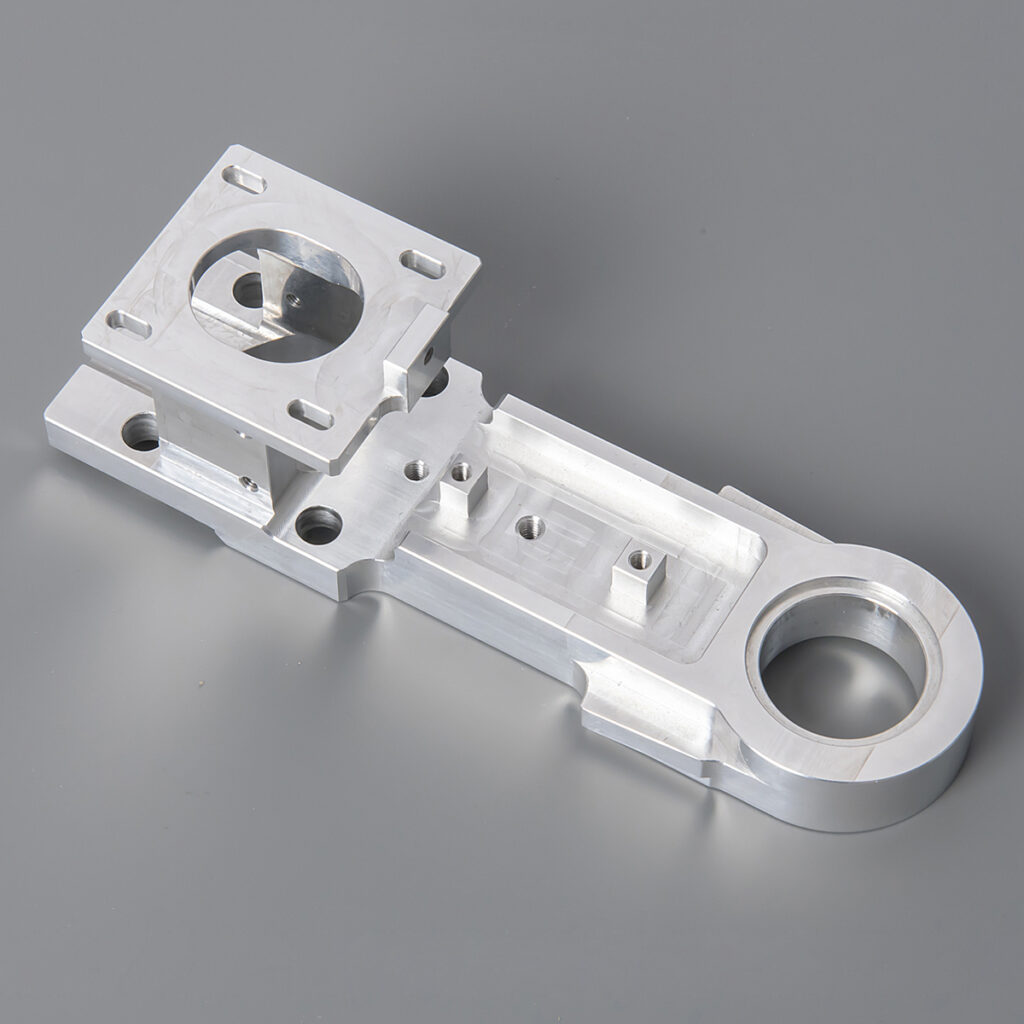
CNC, or Computer Numerical Control, milling is a versatile process used in various industries and it is an automated, subtractive manufacturing technology designed to remove material in a controlled, pre-programmed manner to produce parts.
CNC milling machines can be programmed to cut intricate designs with exacting precision, making them ideal for producing parts with tight tolerances.
Here, we offer a comprehensive guide covering everything you need to know about CNC milling, from its inception to its applications, benefits, and comparisons with other machining processes.
Whether you’re a production manager, buyer, or engineer, understanding the intricacies of CNC milling can significantly enhance your production capabilities and output quality.
-
Table Of Contents
-
1. Everything You Need to Know About CNC Milling
-
2. Who Invented CNC Milling?
-
3. How Does CNC Milling Work?
-
4. What Are the Various CNC Milling Methods?
-
5. What is the Equipment Used in the CNC Milling Process?
-
6. What Are the Applications of CNC Milling?
-
7. What Are the Benefits of CNC Milling?
-
8. Comparison with Other Machining Processes
-
9. Summary
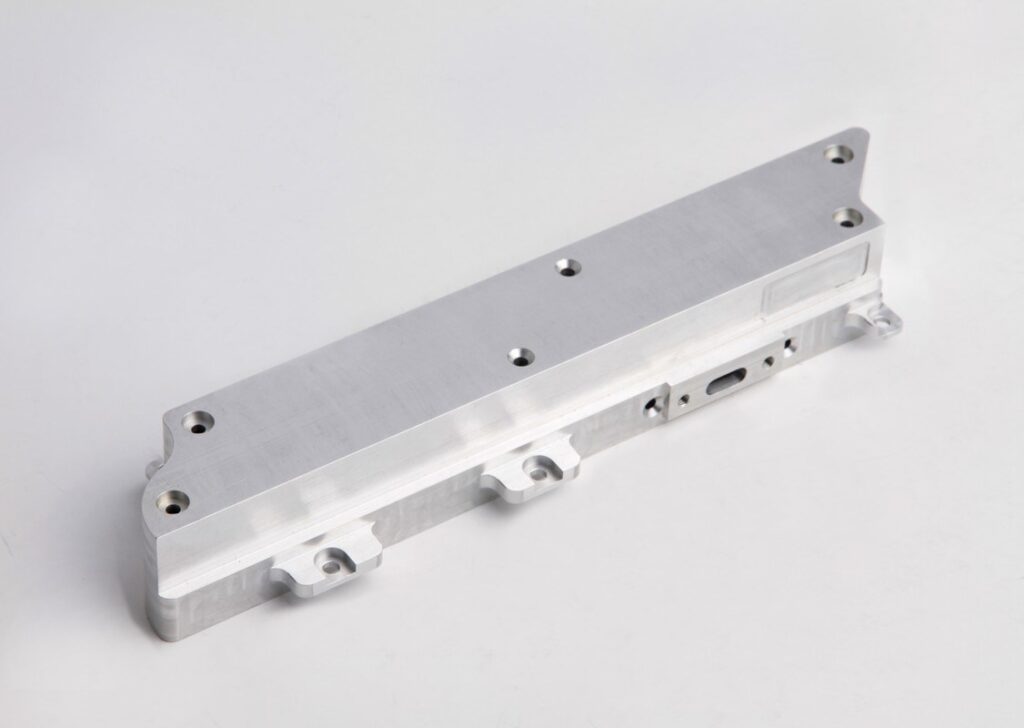
Who Invented CNC Milling?
The history of CNC milling dates back to the mid-20th century. John T. Parsons, along with his colleague Frank L. Stulen, is credited with pioneering CNC technology. Their work in the 1940s and 1950s laid the foundation for the modern CNC milling machines we use today.
Parsons and Stulen developed a method to control machine tools using punched cards, which eventually evolved into the use of computers for machine control. This innovation marked the beginning of a new era in manufacturing, allowing for greater precision and automation in the production process.
How Does CNC Milling Work?
CNC milling operates through precise commands from computer numerical control (CNC) systems. The process begins with a CAD (Computer-Aided Design) model, which is then translated into G-code.
This code instructs the milling machine on how to move the cutting tool, ultimately shaping the material into the desired form. The accuracy and repeatability of CNC milling make it an essential tool in manufacturing.
CNC milling involves several key steps:
1. Design Phase: The process starts with creating a 3D model of the part to be machined using CAD software. This model serves as the blueprint for the milling operation.
2. Programming Phase: The CAD model is converted into a CNC-compatible file format (G-code) using CAM (Computer-Aided Manufacturing) software. The G-code contains instructions for the machine’s movements and operations.
3. Setup Phase: The milling machine is set up with the appropriate cutting tools and fixtures. The workpiece is securely clamped in place on the machine’s worktable.
4. Machining Phase: The CNC machine executes the G-code instructions, precisely moving the cutting tool along the programmed path to remove material and create the desired shape.
5. Finishing Phase: After the initial machining is complete, additional operations such as deburring, polishing, or surface treatment may be performed to achieve the final specifications.
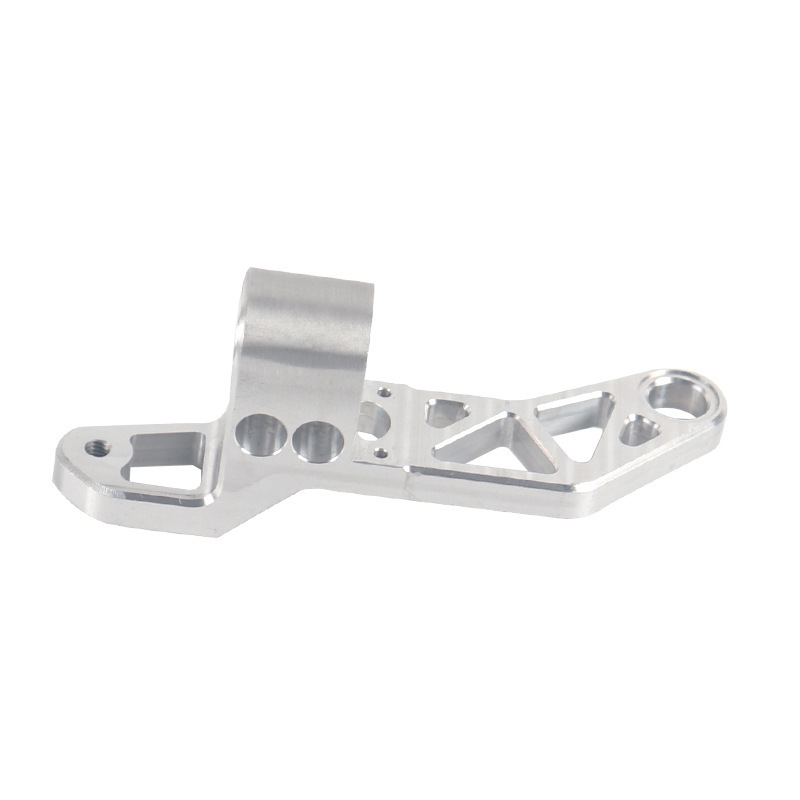
What Are the Various CNC Milling Methods?
There are several CNC milling methods, each suited for different tasks and materials:
• Plain Milling (Surface Milling): Involves cutting a flat surface parallel to the axis of rotation of the cutting tool. This method is commonly used to produce flat surfaces on workpieces.
• Face Milling: Produces a flat surface at right angles to the cutter’s axis. This method is ideal for creating large, flat surfaces with a high degree of accuracy.
• Angular Milling: Cuts at an angle other than 90 degrees. This method is used to create angular features such as chamfers, bevels, and angled slots.
• Form Milling: Creates complex contours by using a specially shaped cutting tool. This method is used to produce intricate shapes and profiles that require precise control over the cutting tool’s geometry.
• Profile Milling: Follows a curved or irregular path to produce contoured surfaces. This method is commonly used to create complex shapes and patterns on workpieces.
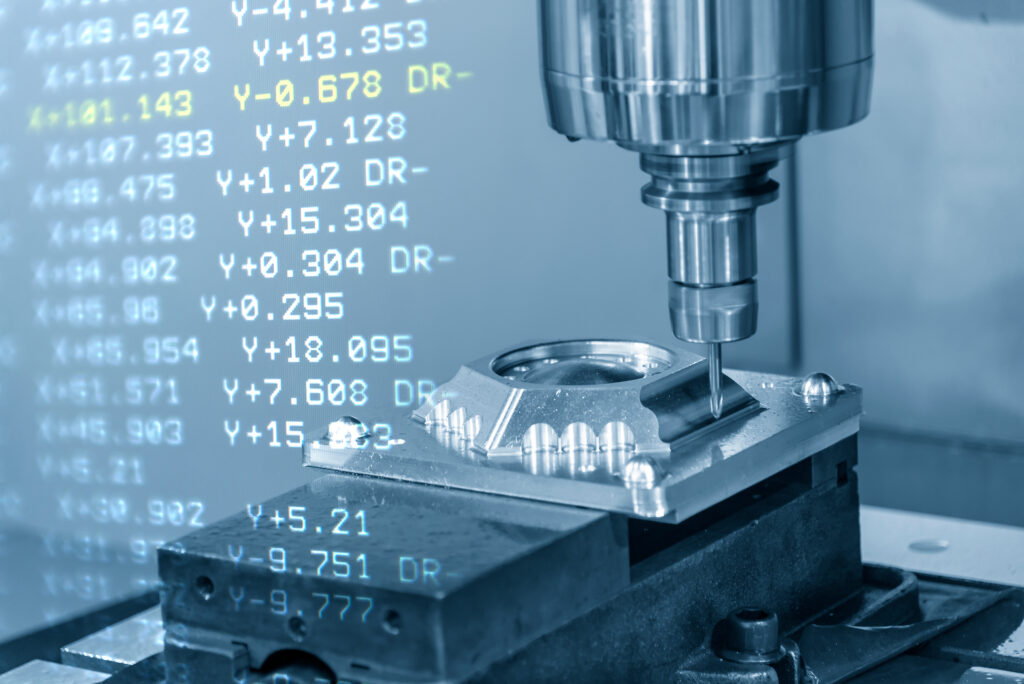
What is the Equipment Used in the CNC Milling Process?
The primary equipment used in CNC milling includes:
• Milling Machine: The main component of the CNC milling process, which houses the spindle and cutting tool. CNC milling machines come in various configurations, including vertical and horizontal machining centers.
• Cutting Tools: Various tools like end mills, face mills, and ball cutters. The selection of cutting tools depends on the material being machined and the desired geometry of the part.
• Workholding Devices: Fixtures that secure the material in place during machining. Common workholding devices include vises, clamps, and specialized fixtures designed for specific applications.
• Coolant Systems: Maintain the temperature of the tool and workpiece, preventing overheating and prolonging tool life. Coolant systems deliver a continuous flow of coolant to the cutting zone, reducing friction and removing chips from the work area.
• Control Panel: Interfaces with the CNC system to manage operations. The control panel allows operators to input commands, monitor machine performance, and make adjustments as needed.
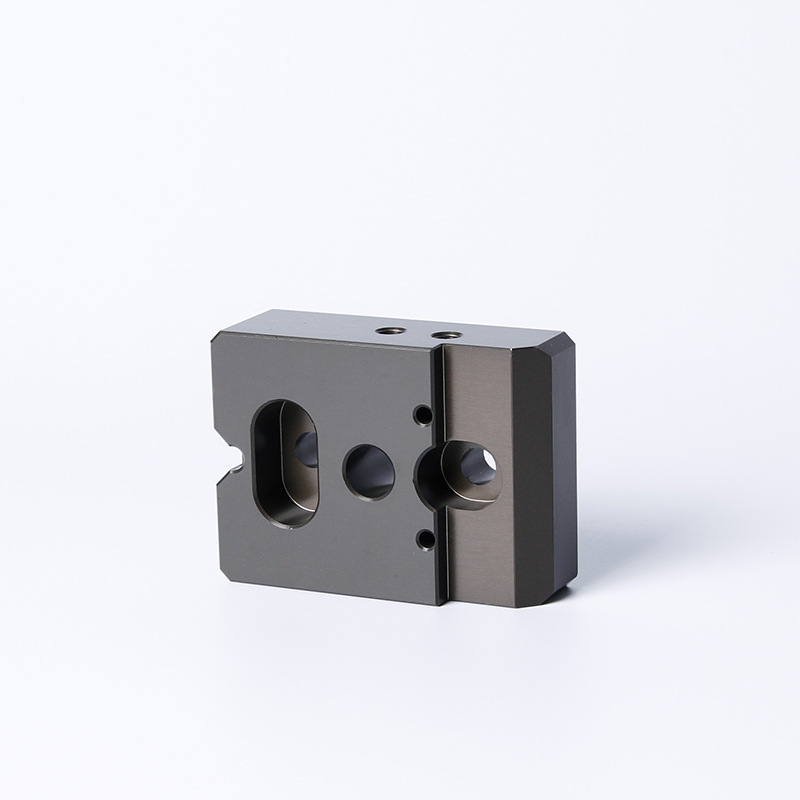
What Are the Applications of CNC Milling?
• Automotive: Manufacturing engine components, transmission parts, and custom accessories. CNC milling is used to produce high-precision parts that meet the stringent requirements of the automotive industry.
• Aerospace: Producing intricate parts for aircraft, including structural components, turbine blades, and landing gear. CNC milling allows aerospace manufacturers to create lightweight, high-strength parts with tight tolerances.
• Medical: Creating precision instruments, implants, and prosthetic devices. CNC milling is used to produce medical devices that require a high degree of accuracy and biocompatibility.
• Electronics: Fabricating enclosures, housings, and circuit boards. CNC milling is used to create intricate designs and patterns on electronic components, ensuring precise fit and functionality.
• Art and Design: Crafting intricate patterns, sculptures, and custom pieces. CNC milling allows artists and designers to create complex shapes and detailed designs with a high level of precision.
What Are the Benefits of CNC Milling?
• High Precision: Ensures accurate and consistent results, making it ideal for producing parts with tight tolerances and complex geometries.
• Efficiency: Reduces production time and labor costs by automating the machining process. CNC milling machines can operate continuously, producing parts quickly and efficiently.
• Versatility: Capable of working with various materials, including metals, plastics, and composites. CNC milling can be used to create a wide range of parts for different applications.
• Scalability: Ideal for both prototyping and mass production. CNC milling allows manufacturers to quickly produce small quantities of prototypes or scale up production to meet high-volume demands.
• Automation: Minimizes human error and increases repeatability, ensuring consistent quality across multiple production runs. CNC milling machines can be programmed to perform complex operations with a high degree of accuracy.
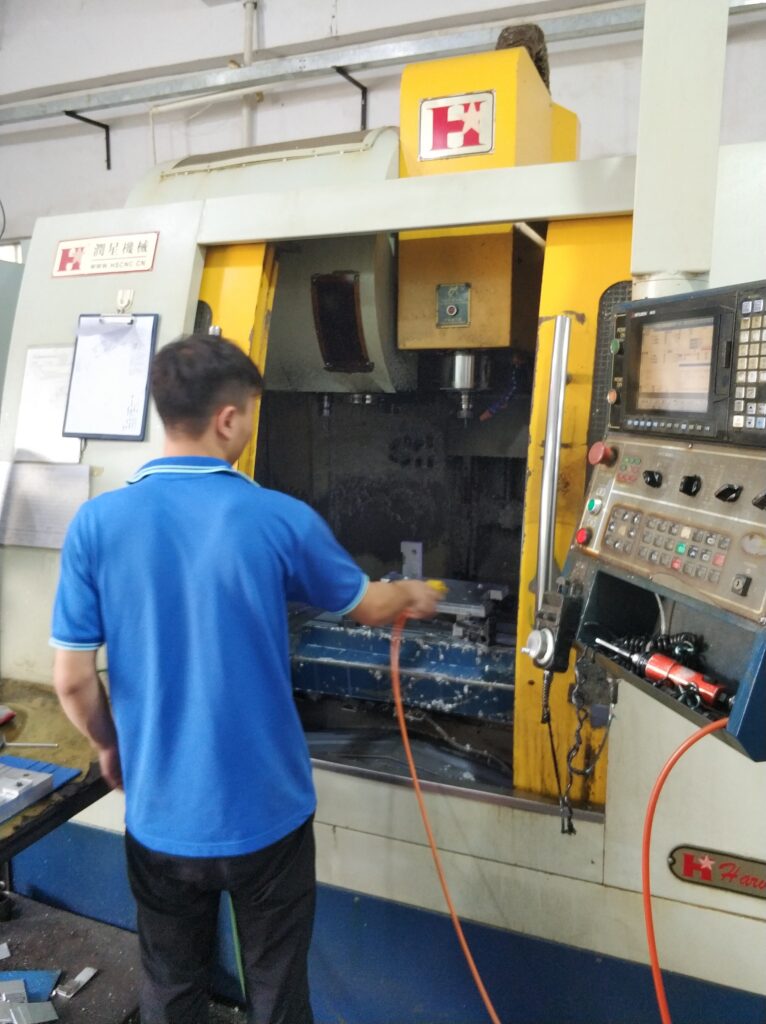
Comparison with Other Machining Processes
Compared to traditional machining, CNC milling provides superior precision, efficiency, and flexibility. While manual milling requires skilled labor and is time-consuming, CNC milling automates the process, allowing for complex designs and faster production times.
Additionally, CNC milling can operate continuously, further enhancing productivity.
Traditional Machining vs. CNC Milling
Traditional Machining:
• Requires manual operation and skilled labor.
• Limited to simpler geometries and lower precision.
• Slower production times and higher labor costs.
• Greater risk of human error and variability in quality.
CNC Milling:
• Automated operation with computer-controlled precision.
• Capable of producing complex geometries with high accuracy.
• Faster production times and lower labor costs.
• Consistent quality and repeatability across production runs.
CNC Milling vs. CNC Turning
CNC Milling:
• Uses a rotating cutting tool to remove material from a stationary workpiece.
• Suitable for creating flat surfaces, contours, and complex shapes.
• Ideal for parts with intricate details and varying geometries.
CNC Turning:
• Uses a stationary cutting tool to remove material from a rotating workpiece.
• Suitable for creating cylindrical shapes and symmetrical parts.
• Ideal for parts with consistent diameters and smooth finishes.
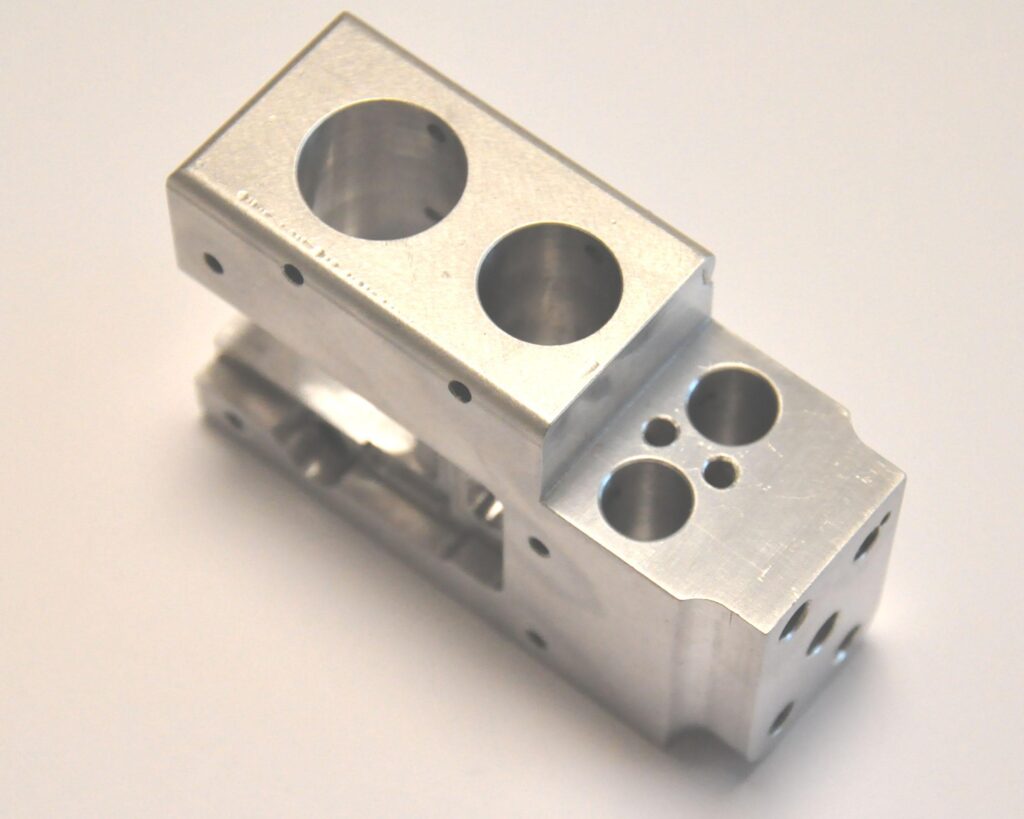
Summary
CNC milling is a cornerstone of modern manufacturing, offering unparalleled precision and efficiency. From automotive parts to medical instruments, its applications are vast and varied.
Embracing CNC milling technology can significantly enhance production capabilities and output quality.
Whether you are a production manager, buyer, or engineer, understanding CNC milling is essential in today’s industrial landscape.