In industries where managing excessive heat is critical, choosing the right heat sink can make a significant difference in performance and reliability.
Copper skived heat sinks stand out as a top-tier solution, offering exceptional thermal conductivity, design flexibility, and durability.
Their unique skiving process ensures high efficiency, making them an essential component in applications where heat dissipation is crucial.
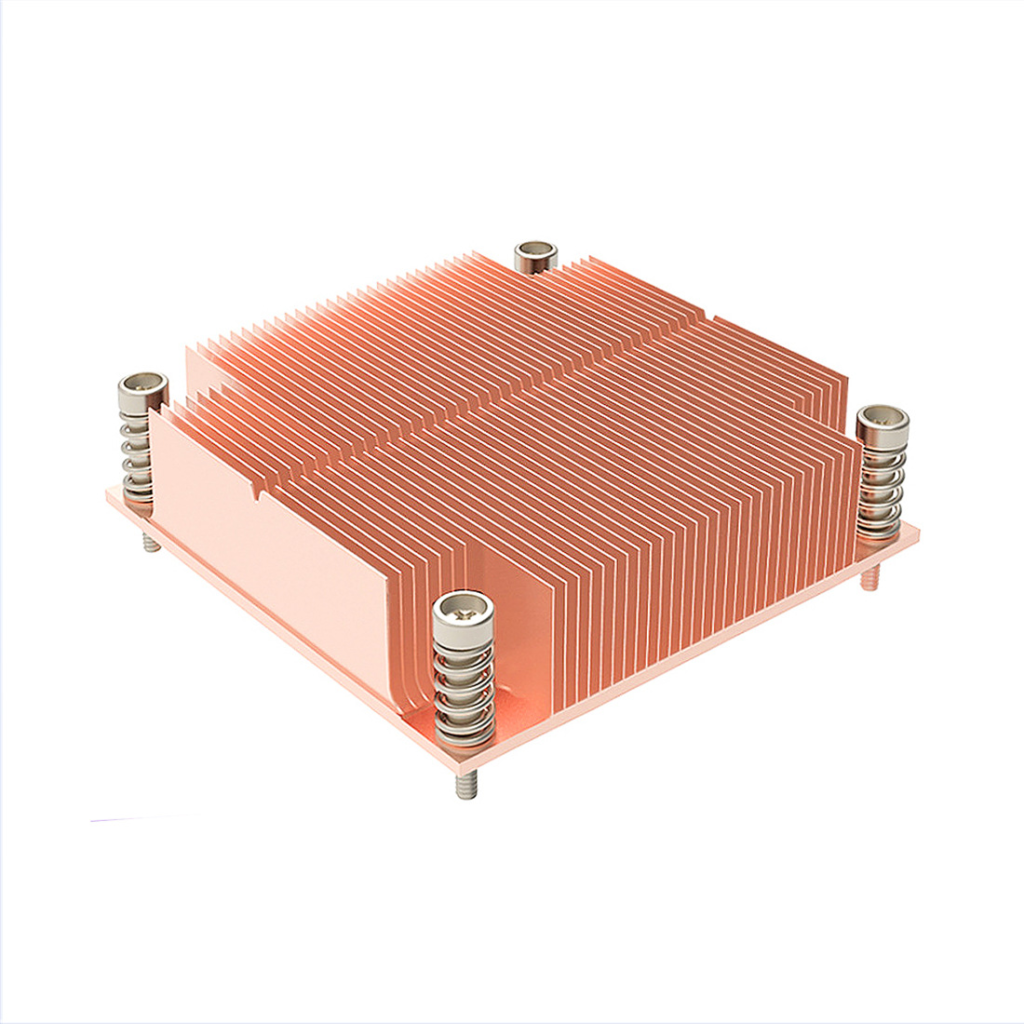
To summarize, copper skived heat sinks provide superior heat transfer, efficient airflow, and adaptability, outperforming traditional heat sinks in high-heat environments.
Whether in telecommunications, automotive, or high-performance computing, they deliver reliable cooling and extend equipment lifespan.
Now, let’s explore their unique advantages, applications, and how they stack up against other types of heat sinks.
-
Table Of Contents
-
1. Why Are Copper Skived Heat Sinks the Top Pick for High-Heat Applications?
-
2. Why Is Copper Superior for Heat Sinks?
-
3. Key Benefits of Copper Skived Heat Sinks
-
4. How Do Copper Skived Heat Sinks Compare to Other Types?
-
5. What About Aluminum? When Is It a Better Choice?
-
6. Applications of Copper Skived Heat Sinks
-
7. Can Copper Skived Heat Sinks Save Costs in the Long Run?
-
8. How to Choose the Right Heat Sink for Your Needs?
-
9. Summary
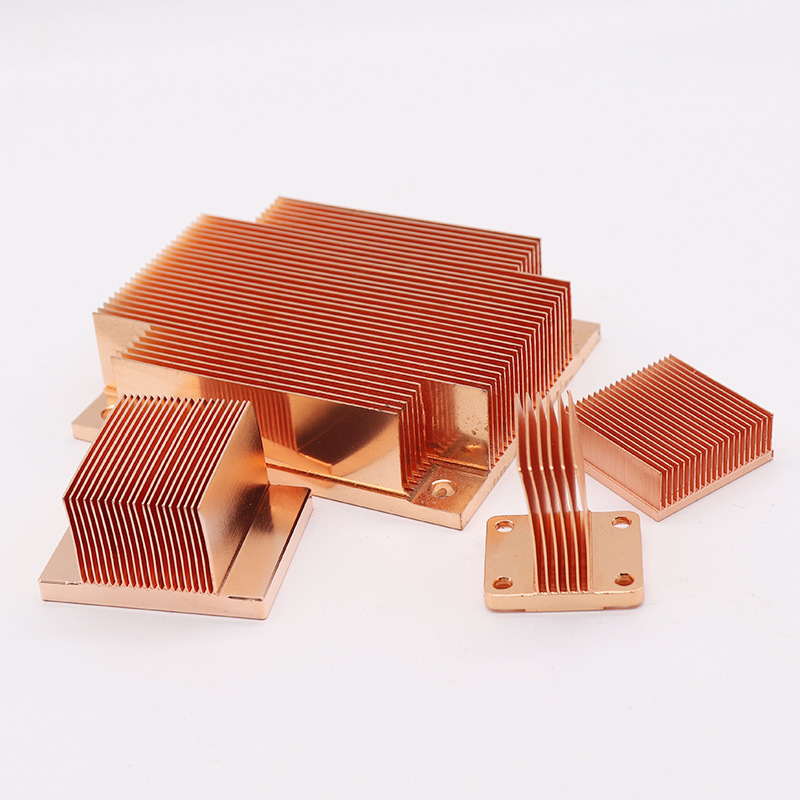
Why Is Copper Superior for Heat Sinks?
Copper is widely regarded as one of the best materials for heat sinks due to its high thermal conductivity, which enables rapid heat transfer.
Skived copper heat sinks take this inherent advantage a step further.
By employing a precise skiving process, these heat sinks create densely packed fins directly from a solid copper block.
This seamless design maximizes surface area and enhances airflow, resulting in highly efficient cooling.
Key Benefits of Copper Skived Heat Sinks
1. Exceptional Thermal Performance
Copper’s thermal conductivity (around 400 W/mK) far exceeds that of aluminum (approximately 200 W/mK). This allows for faster heat dissipation, reducing the risk of overheating in critical systems.
2. Seamless Design for Optimal Heat Transfer
The skiving process creates a direct connection between the base and fins, minimizing thermal resistance and improving heat transfer efficiency.
3. High Fin Density and Compact Size
Skived fins can be thinner and more densely packed than those in extruded heat sinks, maximizing cooling performance even in space-constrained environments.
4. Durability and Longevity
Copper’s resistance to corrosion and wear ensures a longer lifespan, particularly in harsh industrial or outdoor conditions.
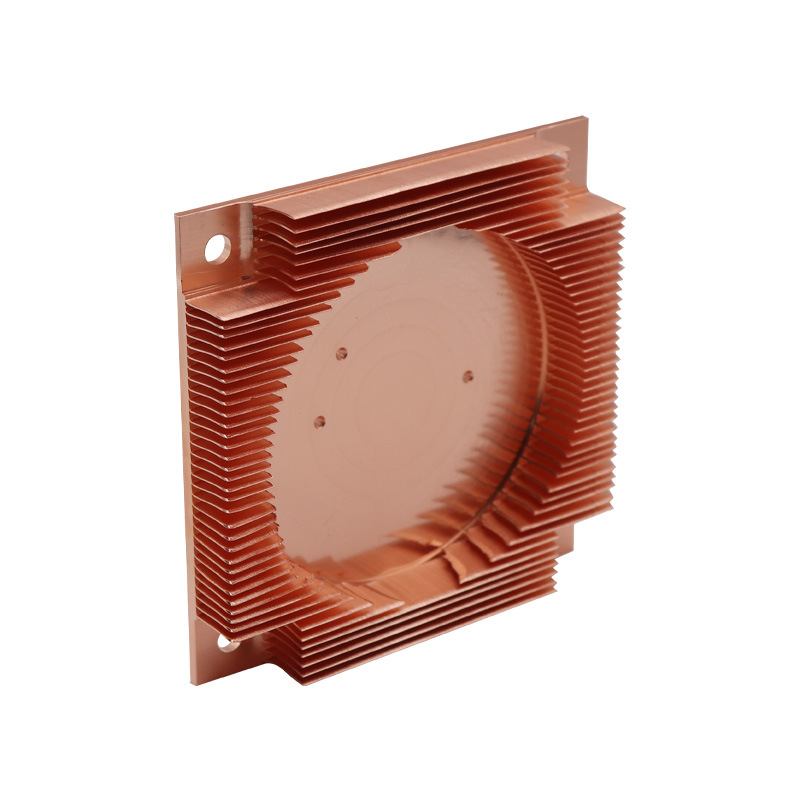
How Do Copper Skived Heat Sinks Compare to Other Types?
To better understand the unique value of copper skived heat sinks, let’s compare them to other common types, such as extruded aluminum heat sinks.
Skived vs. Extruded Heat Sinks
Feature | Skived Heat Sinks | Extruded Heat Sinks |
Material | Copper (higher thermal conductivity) | Aluminum (lower thermal conductivity) |
Thermal Performance | Superior (up to 400 W/mK) | Moderate (around 200 W/mK) |
Fin Design | Thin, densely packed fins for better heat dissipation | Thicker, less dense fins |
Manufacturing Cost | Higher per unit, but no mold costs | Lower per unit, but requires molds for production |
Design Flexibility | Highly customizable, ideal for complex cooling needs | Limited customization due to extrusion constraints |
Weight | Heavier than aluminum | Lightweight, suitable for applications with weight limits |
Durability | High corrosion resistance and longevity | Susceptible to corrosion in certain environments |
While extruded aluminum heat sinks are more cost-effective for low- to moderate-heat applications, copper skived heat sinks excel in high-performance settings where superior thermal performance and compact design are critical.
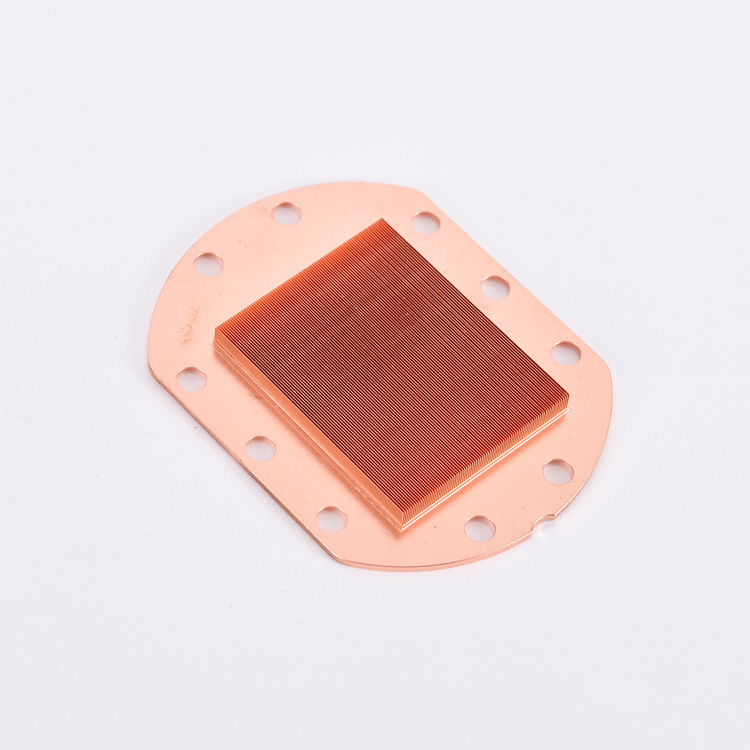
What About Aluminum? When Is It a Better Choice?
While copper skived heat sinks dominate high-heat scenarios, aluminum heat sinks still hold a place in specific applications.
Aluminum is lightweight and cost-effective, making it suitable for low- to moderate-heat environments where budget constraints and portability are priorities.
For instance, consumer electronics and LED lighting often employ aluminum heat sinks due to their lower cost and sufficient thermal performance.
Applications of Copper Skived Heat Sinks
The versatility and efficiency of copper skived heat sinks make them indispensable across various industries. Here are some key applications:
1. Telecommunications
With the rise of 5G networks, telecom equipment generates more heat than ever. Copper skived heat sinks ensure reliable cooling for routers, servers, and signal processors, maintaining system stability during peak loads.
2. Automotive Electronics
Modern vehicles are equipped with advanced electronics, such as infotainment systems and powertrain components. Copper skived heat sinks help prevent overheating, ensuring the safety and performance of these critical systems.
3. High-Performance Computing (HPC)
In data centers and gaming systems, CPUs and GPUs generate significant heat. Copper skived heat sinks provide efficient cooling, minimizing the risk of thermal throttling and ensuring optimal performance.
4. Medical Devices
Medical imaging and diagnostic equipment require precise temperature control to maintain accuracy. Copper skived heat sinks play a vital role in ensuring the reliability of these devices.
5. Power Electronics
Inverters, converters, and other power electronics generate intense heat due to high energy throughput. Copper skived heat sinks help manage this heat, enhancing the durability and efficiency of these systems.
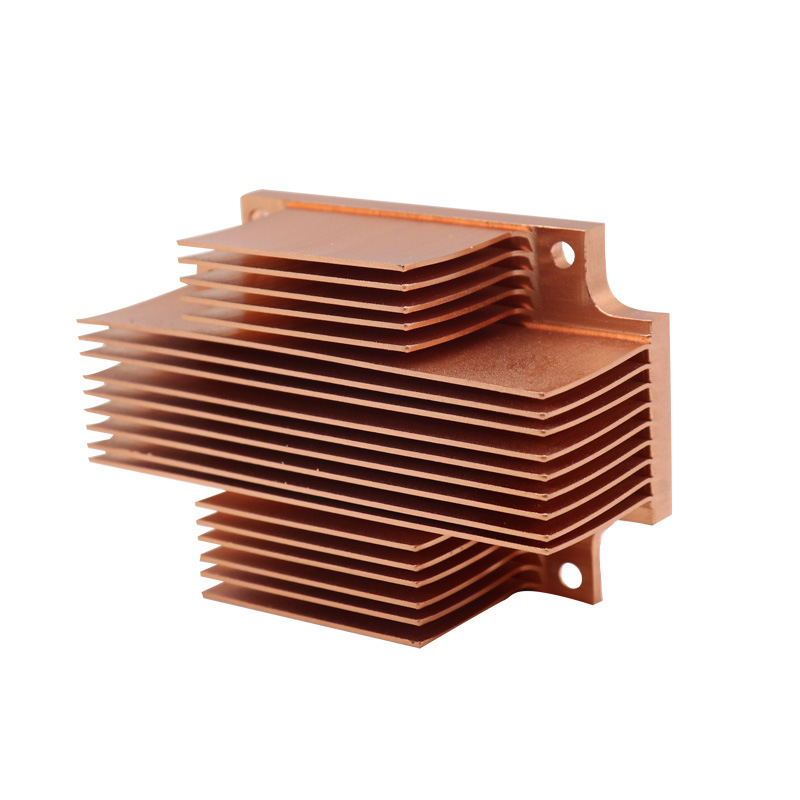
Can Copper Skived Heat Sinks Save Costs in the Long Run?
Despite their higher initial cost, copper skived heat sinks offer long-term cost benefits, particularly in high-performance applications. Here’s how:
1. Reduced Maintenance and Downtime
Their durability and superior cooling capabilities prevent system failures and extend the lifespan of components, reducing maintenance costs and downtime.
2. Energy Efficiency
By maintaining optimal operating temperatures, copper skived heat sinks improve the efficiency of electronic devices, leading to energy savings over time.
3. Customizable for Specific Needs
Skived designs eliminate the need for expensive molds, making them cost-effective for custom or small-batch production runs.
How to Choose the Right Heat Sink for Your Needs?
Selecting the optimal heat sink depends on several factors, including your application’s heat dissipation requirements, budget, and space constraints. Here’s a quick guide:
• For High-Heat, Space-Constrained Applications:
Copper skived heat sinks are ideal, offering unmatched thermal performance and compact design.
• For Moderate Heat with Budget Constraints:
Extruded aluminum heat sinks provide a balance between cost and performance.
• For Custom Designs or Prototypes:
Skived heat sinks offer greater flexibility, enabling unique shapes and configurations tailored to specific devices.
By assessing these factors, you can choose a heat sink that maximizes performance while aligning with your project’s goals.
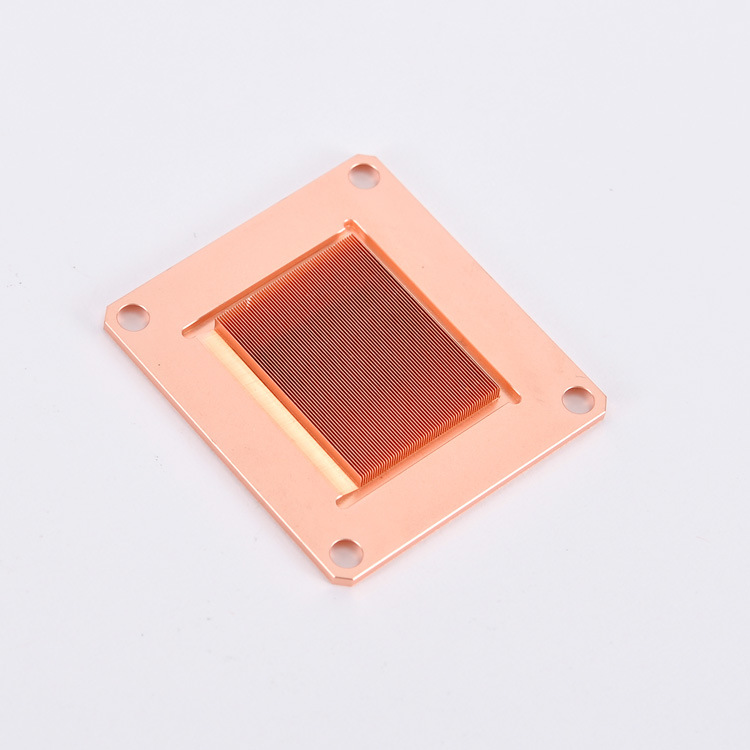
Conclusion
Copper skived heat sinks provide a premium solution for industries that demand efficient and reliable heat management.
From telecommunications to high-performance computing, their exceptional thermal performance, design flexibility, and long-term durability make them the best choice for high-heat applications.
Although their upfront cost may be higher than alternatives, their efficiency and longevity offer significant savings in the long run, making them an invaluable investment for critical cooling needs.