Understanding the Importance of CNC Surface Finishing
Surface finishing in CNC machining is not just a cosmetic enhancement; it plays a critical role in determining the appearance, durability, and performance of a component.
Whether you’re producing parts for aerospace, automotive, medical, or consumer products, the right surface finish can significantly impact the success of your final product.
Proper finishing enhances visual appeal and improves corrosion resistance, wear resistance, and overall longevity.
This guide will help you navigate the various types of CNC surface finishes, their roughness levels, pros and cons, and key industry standards.
By understanding your options, you can make informed decisions that ensure optimal performance in real-world applications.
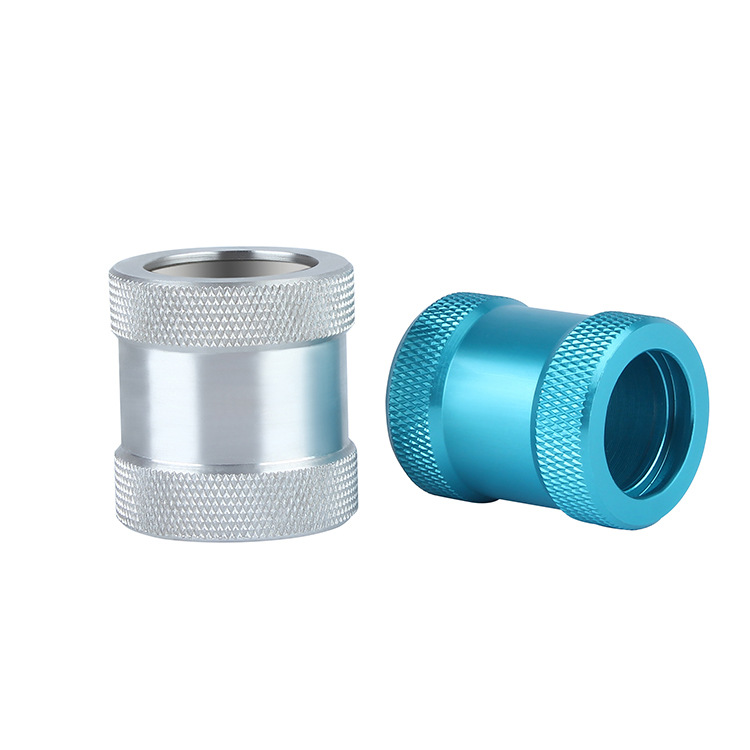
-
Table Of Contents
-
1. Understanding the Importance of CNC Surface Finishing
-
2. What Is the Standard Surface Finish for CNC?
-
3. The Significance of Surface Roughness
-
4. What Are the Advantages of Controlling Surface Roughness?
-
5. Common Surface Finishes for CNC Machined Parts
-
6. Weighing the Pros and Cons of Different CNC Surface Finishes
-
7. Summary
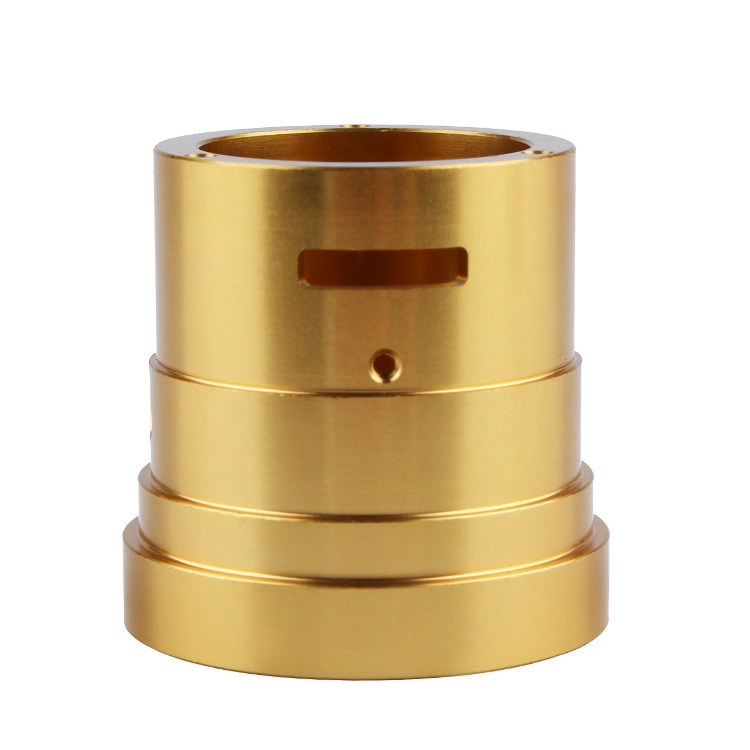
What Is the Standard Surface Finish for CNC?
CNC machining inherently leaves distinct marks on a part’s surface due to the nature of cutting tools.
The roughness of the surface, often referred to as Ra (average roughness), is a critical measure of texture that determines the quality and suitability of a part for its intended application.
The standard as-machined surface finish typically has a roughness of 3.2 μm (125 μin). This level is acceptable for many industrial components where aesthetics are not a primary concern.
However, numerous applications require smoother surfaces, achievable through additional finishing passes. By adding these steps, the roughness can be reduced to 1.6 μm, 0.8 μm, or even 0.4 μm for high-precision parts, such as those used in aerospace or medical devices.
It’s important to note that reducing surface roughness often increases production costs, as it involves additional machining steps, enhanced quality control, and tighter tolerances.
However, for critical applications, these extra efforts are a worthy investment, directly affecting the part’s performance and longevity.
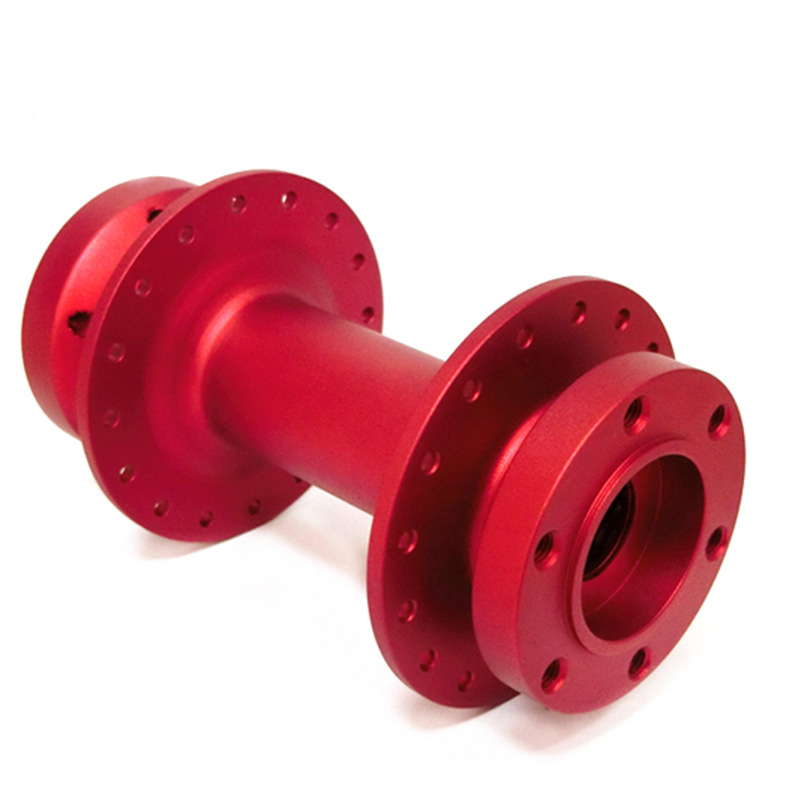
The Significance of Surface Roughness
Surface roughness is more than just a matter of looks; it significantly impacts how a part functions in its operational environment. Here are a few key considerations:
1. Friction Reduction: Smoother surfaces with lower Ra values reduce friction, improving wear resistance. This is particularly crucial for moving parts, where lower friction can prolong lifespan.
2. Corrosion Resistance: A smoother surface enhances corrosion resistance by minimizing grooves or scratches where corrosive elements might settle. This factor is vital for marine, aerospace, or chemical processing components.
3. Tailored Applications: Some applications require a rougher surface for optimal performance. For instance, parts undergoing painting or bonding may benefit from increased surface area to which coatings or adhesives can adhere.
By carefully tailoring surface roughness to match specific end-use requirements, manufacturers can ensure their parts perform effectively in their intended applications.
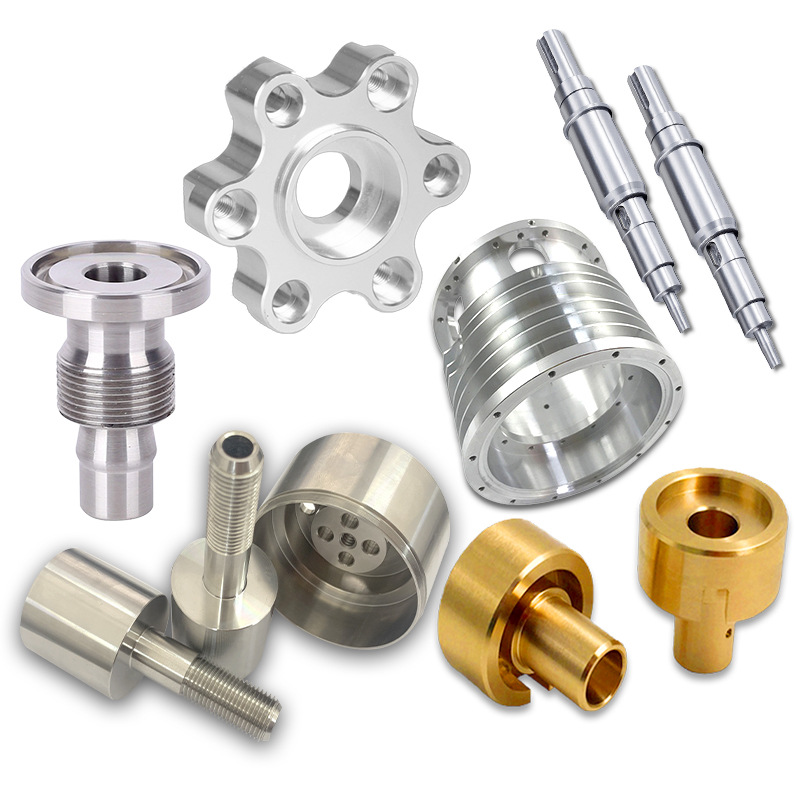
What Are the Advantages of Controlling Surface Roughness?
Controlling surface roughness in CNC machined parts brings numerous benefits:
1. Improved Durability: Smoother finishes typically enhance durability, reducing wear and extending component life.
2. Enhanced Corrosion Resistance: Smooth surfaces leave fewer areas for moisture and corrosive materials, making them ideal for sensitive environments.
3. Visual Appeal: Surface roughness significantly influences the aesthetics of consumer products or visible components. A polished or smooth surface can elevate a product’s appeal and market value.
4. Improved Adhesion: While smoother finishes are desirable for many applications, rougher surfaces may be essential for adhesives, paints, or coatings to bond effectively.
5. Sealing and Fit: Smooth surfaces can ensure tight fits between components, which is essential in high-pressure environments or when effective sealing is required.
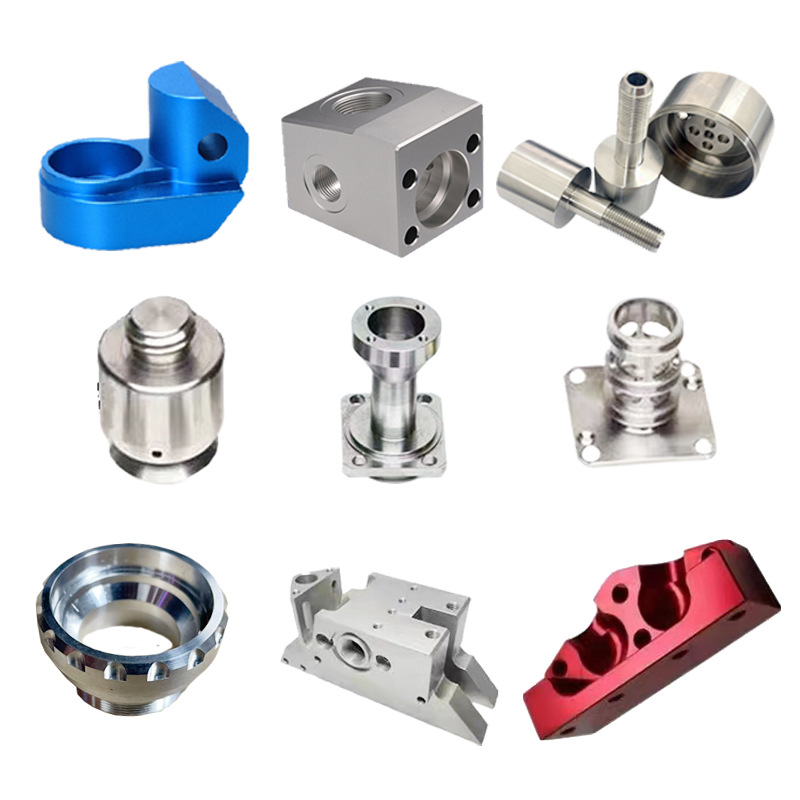
Common Surface Finishes for CNC Machined Parts
The choice of surface finish applied to CNC machined parts depends on various factors, including material type, intended application, and desired appearance. Here are the most commonly used surface finishes in CNC machining:
1. As-Machined Finish:
Description: This finish reflects the part’s state right off the machine, showcasing visible tool marks without additional processing.
Applications: Ideal for internal components or prototypes where aesthetics are not crucial.
Pros: Cost-effective with fast production times.
Cons: Visible tool marks and no corrosion protection.
2. Bead Blasting:
Description: Bead blasting involves propelling fine beads or abrasives onto the part’s surface to create a smooth, matte finish.
Applications: Commonly used in consumer products and electronics casings requiring a non-reflective surface.
Pros: Smooth, uniform texture that hides minor imperfections.
Cons: Limited durability and no inherent corrosion protection.
3. Anodizing:
Description: This electrochemical process forms a protective oxide layer on metals, particularly aluminum, and allows for dye coloring.
Applications: Ideal for components requiring corrosion resistance, such as in electronics or automotive parts.
Pros: Excellent corrosion resistance, available in various colors, and durable.
Cons: Limited to specific materials and more expensive than simpler methods.
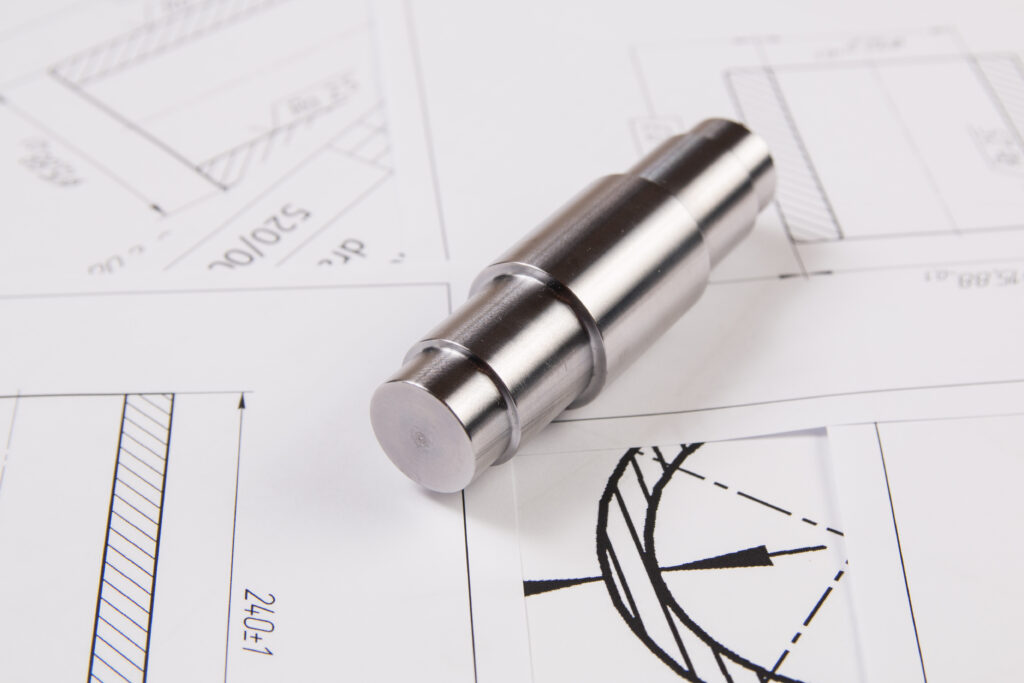
4. Powder Coating:
Description: A thick, protective layer applied through electrostatic deposition and cured in an oven, resulting in a strong, wear-resistant finish.
Applications: Common in outdoor equipment, automotive parts, and heavy-duty machinery.
Pros: Durable, corrosion-resistant, and available in a wide range of colors.
Cons: Adds thickness, potentially affecting tight tolerances.
5. Polishing:
Description: Mechanical buffing produces a mirror-like, reflective surface, offering high aesthetic appeal but reduced scratch resistance.
Applications: Often used in decorative components and luxury products.
Pros: High aesthetic value and smooth, reflective surface.
Cons: Prone to scratching and less protective against corrosion.
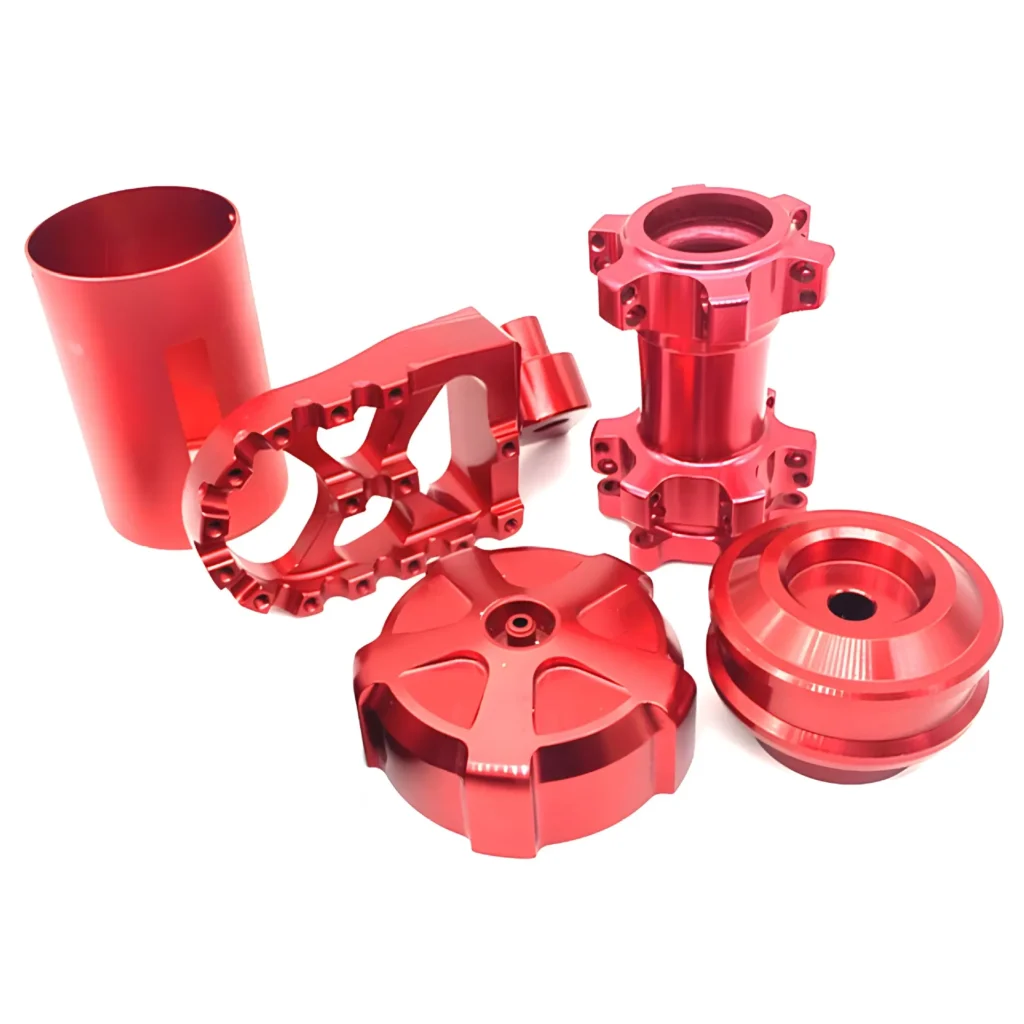
Weighing the Pros and Cons of Different CNC Surface Finishes
Finish | Pros | Cons |
As-Machined | Cost-effective, no additional processing | Visible tool marks, no protection |
Bead Blasting | Smooth, matte texture | Limited durability, no corrosion resistance |
Anodizing | Corrosion-resistant, durable, colorful | Limited to specific materials, higher cost |
Powder Coating | Durable, protective, wide color range | Adds thickness, precision issues |
Polishing | High aesthetic quality | Easily scratched, less durable |
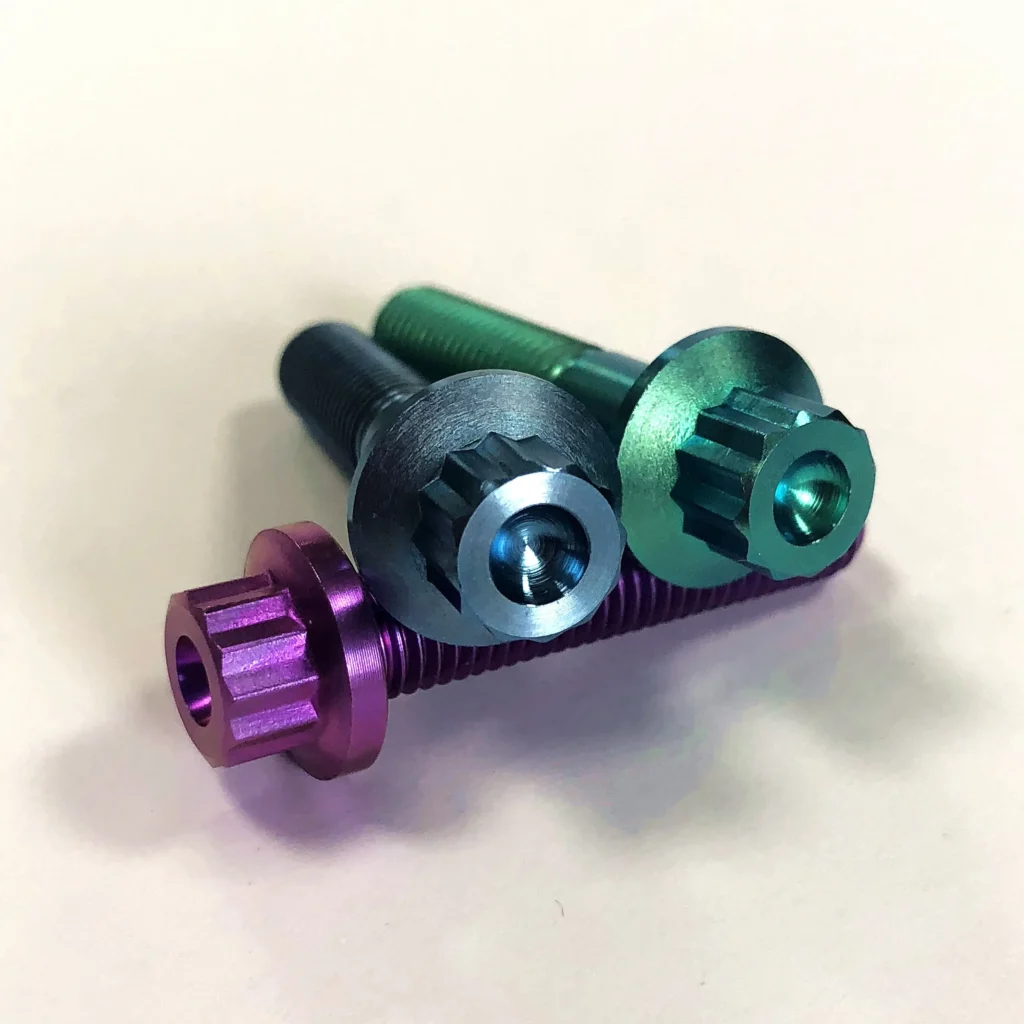
Conclusion
Surface finishing is a critical consideration in CNC machining that directly influences the final part’s appearance, performance, and durability.
Whether opting for a cost-effective as-machined finish or the corrosion resistance of anodizing, understanding your options allows you to optimize your parts for their intended use.
Balance technical requirements with aesthetic needs when selecting a surface finish, and always adhere to industry standards to ensure top-notch quality in your CNC machined components.
By making informed choices, you can enhance your products’ functionality and appeal, ensuring they stand out in the competitive market.