Selecting the ideal cutting method is crucial for achieving accuracy in complex, high-tolerance projects.
Among the available machining options, Wire Electrical Discharge Machining (Wire EDM) stands out for those seeking precision and flexibility.
Known for its non-contact, highly precise approach, Wire EDM offers significant advantages over conventional methods like laser cutting, milling, and waterjet cutting, making it an essential tool for industries with rigorous standards.
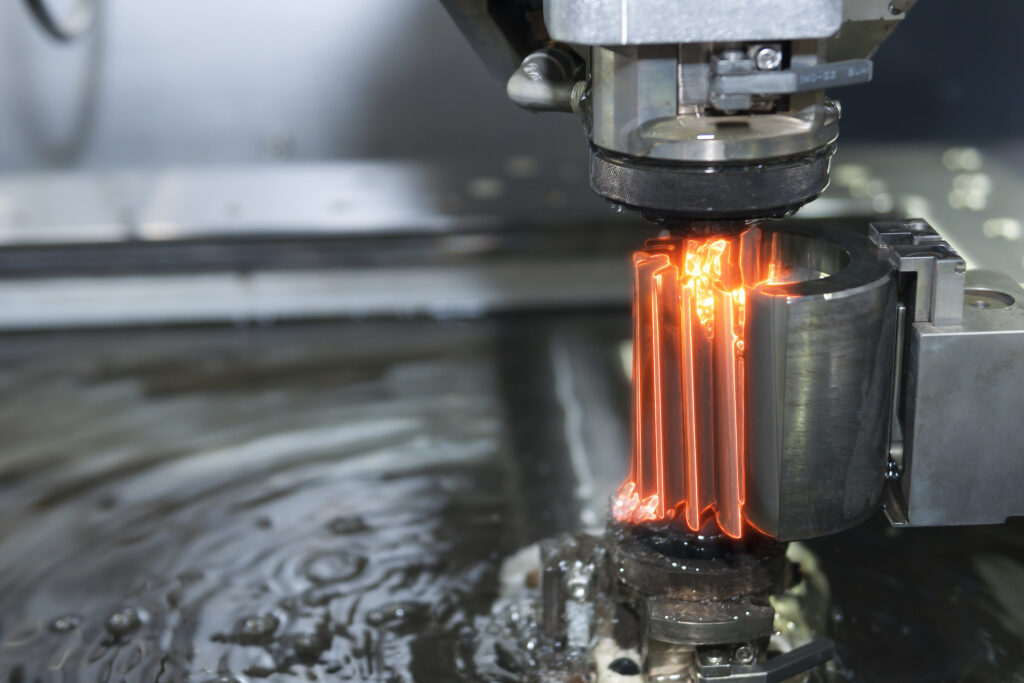
In short, Wire EDM cutting is invaluable for precision projects because it can achieve unparalleled accuracy and handle both hard and delicate materials without distortion, making it ideal for intricate, high-quality parts.
This unique capability sets Wire EDM apart as the method of choice for sectors like aerospace, automotive, and medical manufacturing.
Read on to discover how Wire EDM works, how it compares to other cutting methods, its key advantages, and why it’s ideal for high-precision applications.
-
Table Of Contents
-
1. Why Should You Choose Wire EDM Cutting for Your Precision Project?
-
2. What is Wire EDM Cutting and How Does It Work?
-
3. Wire EDM vs. Other Cutting Methods: Which is Best for Precision?
-
4. Key Advantages of Wire EDM Cutting
-
5. How to Choose the Right Wire for Your EDM Process?
-
6. Conclusion
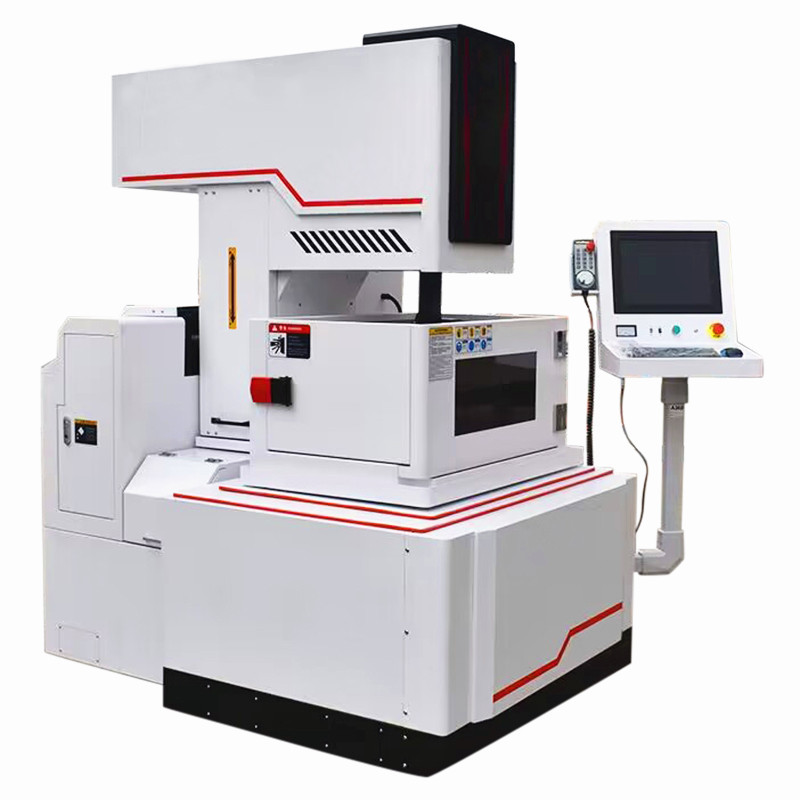
What is Wire EDM Cutting and How Does It Work?
Wire EDM is an advanced machining process that uses a thin, electrically charged wire—often made of brass or copper—to cut through conductive materials.
As electrical current passes through the wire, it generates a series of high-frequency sparks that erode the material along the defined cutting path.
Unlike conventional methods, the wire doesn’t contact the workpiece directly, eliminating physical force that could distort the material.
Industries like aerospace and medical manufacturing heavily rely on Wire EDM to produce components that demand tight tolerances and high quality.
For example, in aerospace, it’s used to make parts like turbine blades, which must withstand extreme conditions without deviation from precise specifications.
In the medical field, Wire EDM is ideal for producing delicate instruments and implants, where even slight inaccuracies could impact safety or effectiveness.
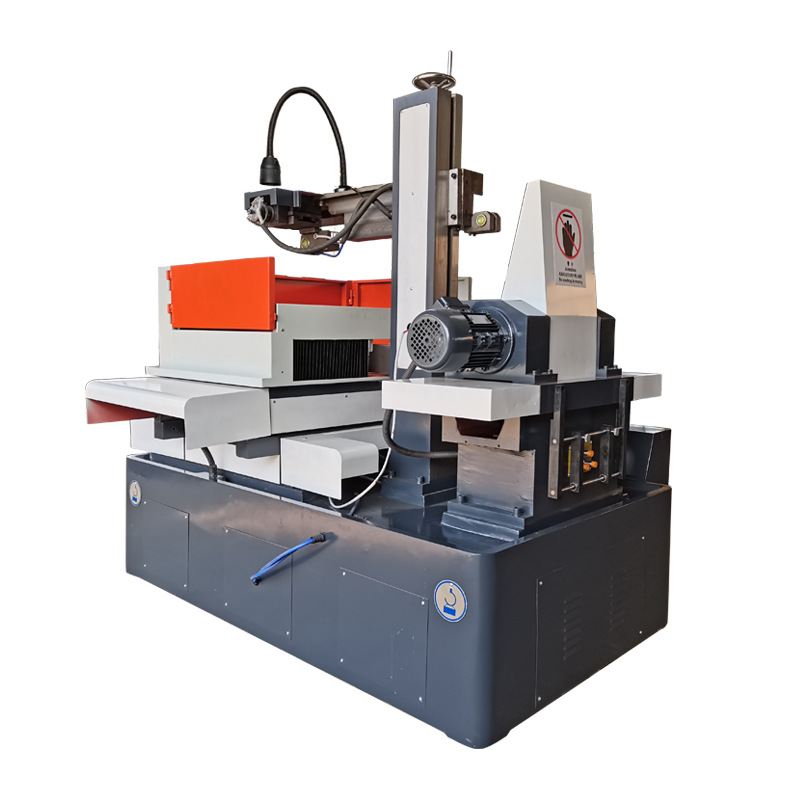
Wire EDM vs. Other Cutting Methods: Which is Best for Precision?
Wire EDM offers distinct advantages over other cutting technologies, especially for projects that require high precision and complex geometries.
Let’s examine how it compares with three common methods: laser cutting, waterjet cutting, and conventional milling.
1. Laser Cutting
Laser cutting is known for speed and efficiency, especially with thin metals.
However, it loses precision with thicker materials and can generate significant heat, which risks warping heat-sensitive components.
Wire EDM, in contrast, generates minimal heat, preventing material deformation.
Additionally, Wire EDM handles materials that lasers may struggle with, such as high-strength alloys, making it better for precise cuts in challenging materials.
2. Waterjet Cutting
Waterjet cutting, which uses high-pressure water mixed with abrasive particles, is versatile but lacks the fine precision that Wire EDM offers.
Waterjets are better suited to large-scale cuts, but they’re less effective for intricate shapes or delicate parts where fine detail is critical.
Wire EDM, however, is highly precise and capable of producing complex, small details.
Its accuracy and ability to cut with no heat or physical contact make it ideal for high-precision applications where waterjet methods might fall short.
3. Conventional Milling
Milling removes material using a rotating cutting tool, which works well for many applications but has limitations when cutting hard or delicate materials.
Physical contact between the tool and material in milling can lead to distortion or wear.
Wire EDM eliminates these issues by relying on electrical discharges rather than physical contact, reducing the risk of mechanical stress or tool wear.
It’s ideal for fragile parts or intricate details, offering a level of precision that milling cannot easily achieve.
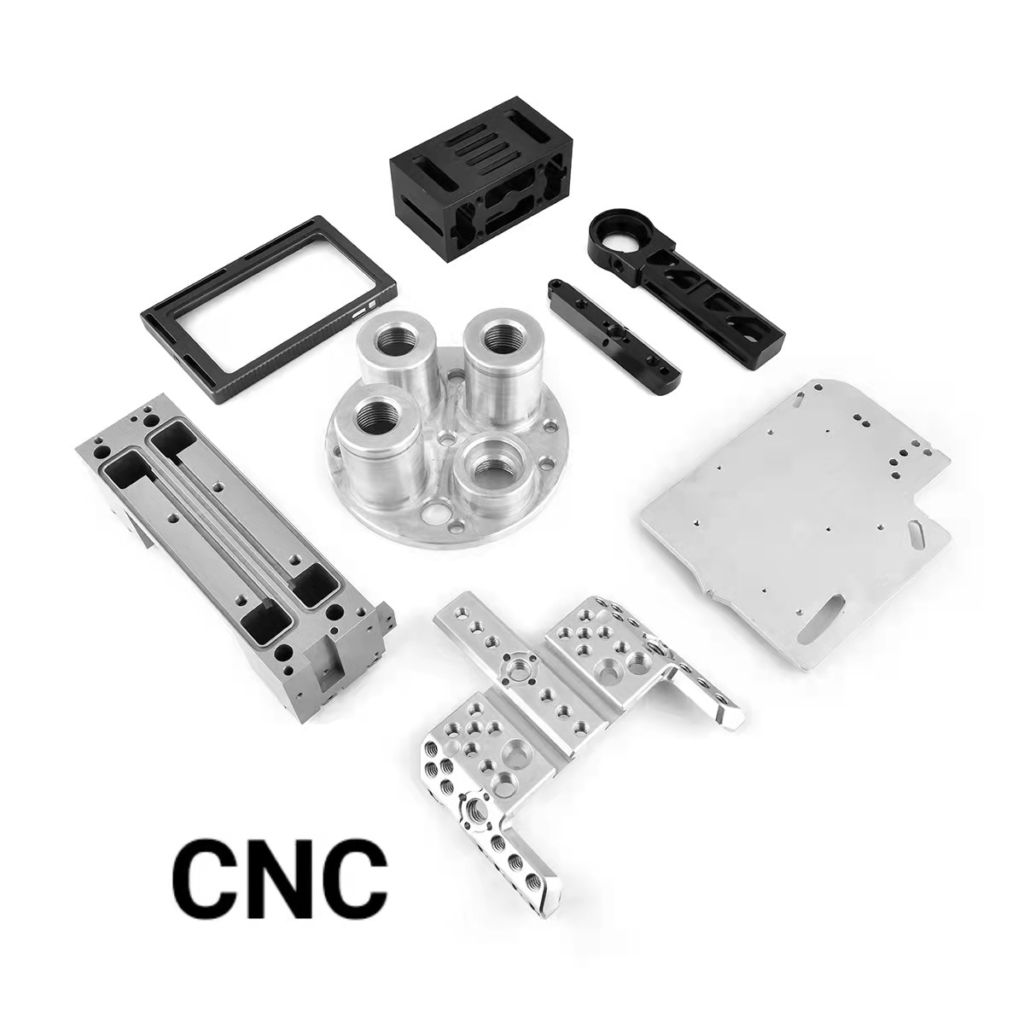
Key Advantages of Wire EDM Cutting
Wire EDM brings numerous advantages to precision manufacturing, including extreme accuracy, the ability to handle various materials, and the flexibility to cut complex shapes with minimal distortion.
1. Unparalleled Precision
Wire EDM can achieve tolerances as tight as +/- 0.00004 inches (0.001mm), a level of precision that’s often unattainable with other methods.
This is critical for industries such as aerospace and medical device manufacturing, where even the smallest deviation can have serious consequences.
2. Complex Geometries
Wire EDM’s versatility allows it to cut tight radii, sharp corners, and other intricate shapes that conventional methods struggle with.
Multi-axis Wire EDM machines can even create complex 3D geometries, making it an indispensable tool for industries that require detailed, multi-plane components.
3. No Material Hardness Limits
Wire EDM is not limited by material hardness, allowing it to cut both soft metals like copper and extremely hard alloys like tungsten or molybdenum.
This flexibility makes it ideal for projects involving challenging materials that other cutting methods may struggle with.
4. Minimal Distortion and No Mechanical Stress
Since Wire EDM doesn’t physically contact the workpiece, there’s no risk of mechanical stress or distortion.
This is particularly beneficial for delicate materials or components that require high precision.
5. No Tool Wear
Unlike conventional cutting, Wire EDM doesn’t experience tool wear in the traditional sense.
The electrically charged wire is expendable and replaced as it wears down, ensuring consistent, repeatable results and reducing downtime from tool changes.
This results in a more efficient process with reduced operating costs, making it a reliable choice for high-volume projects that demand precision.
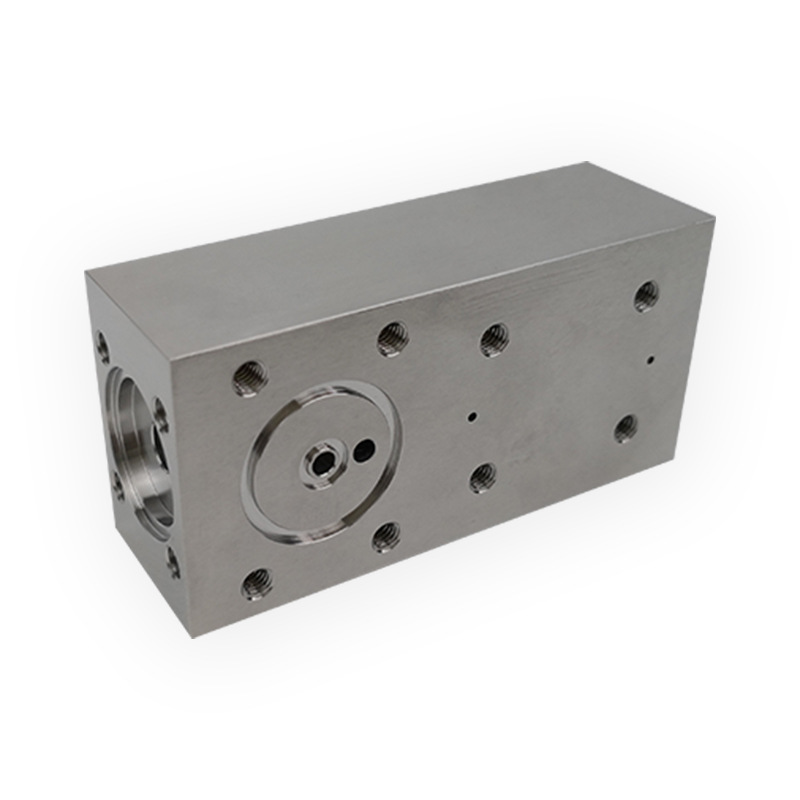
How to Choose the Right Wire for Your EDM Process?
Selecting the appropriate wire is crucial for achieving optimal results. Wire types, such as brass, coated brass, and copper, offer different benefits:
• Brass Wire: Ideal for general applications, providing a balance of speed and precision.
• Coated Brass Wire: Enhanced cutting speeds and reduced wear make it suitable for high-volume production.
• Copper Wire: Preferred for ultra-precise applications due to its superior conductivity.
Matching the wire type to your project needs can significantly improve machining efficiency and output quality.
Conclusion
Wire EDM is ideal for precision projects because it offers unmatched accuracy, allows for intricate shapes and complex geometries, and can handle materials of varying hardness without deformation.
Its non-contact process ensures minimal wear and tear on both the tools and the workpiece, making it the preferred choice for industries that prioritize quality and precision.