Are you considering sheet metal fabrication for your next project but unsure if it’s the right fit?
Sheet metal fabrication is a widely used manufacturing method, but like any process, it has pros and cons.
In this article, we’ll discuss the key advantages and disadvantages to help you determine if this versatile method aligns with your project’s needs.
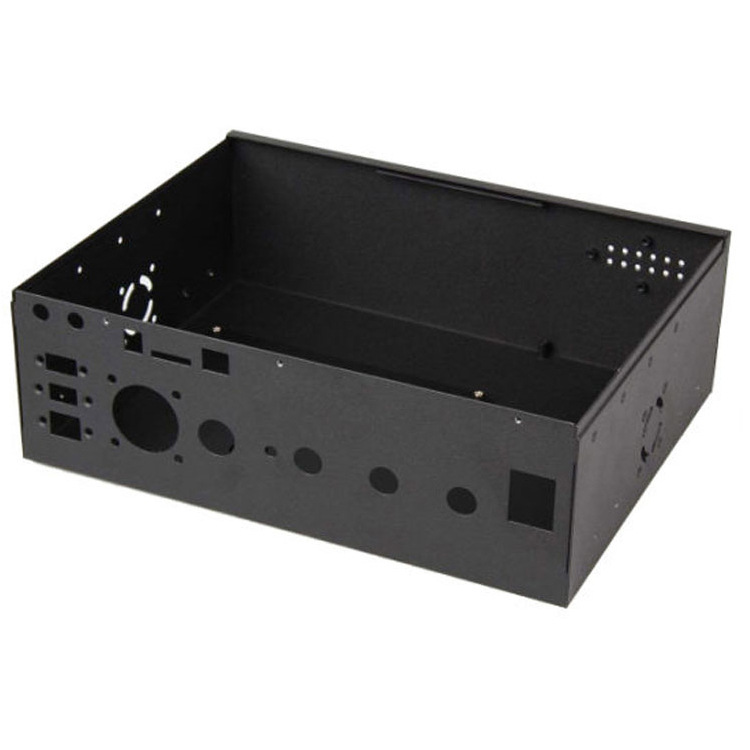
Whether you’re working in the automotive, aerospace, or electronics industry, or just curious about fabrication, read on to discover if sheet metal fabrication is the right choice for you!
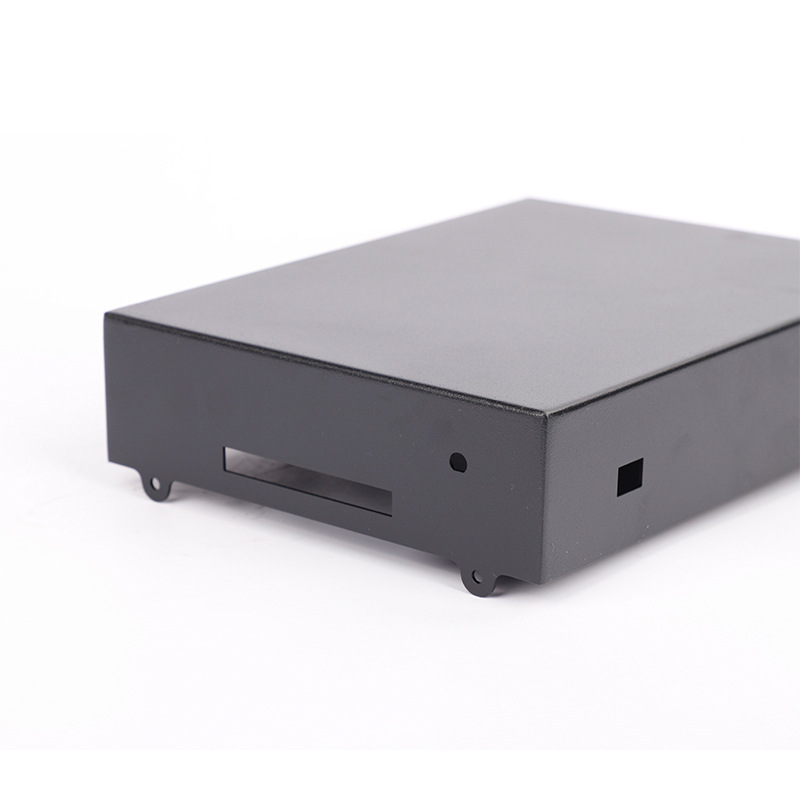
What Is Sheet Metal Fabrication?
Sheet metal fabrication refers to the process of transforming flat metal sheets into various products through cutting, bending, and assembling.
Whether it’s small components like electronic enclosures or larger industrial parts, this method is valued for its efficiency and versatility.
Key Steps in Sheet Metal Fabrication:
• Cutting: Precision is achieved through tools like laser cutters or shears.
• Bending: Metal is shaped using press brakes or similar equipment.
• Assembly: Parts are fastened, welded, or riveted to form a final product.
While the process is widely used, it’s important to weigh both the benefits and challenges before selecting it for your manufacturing needs.
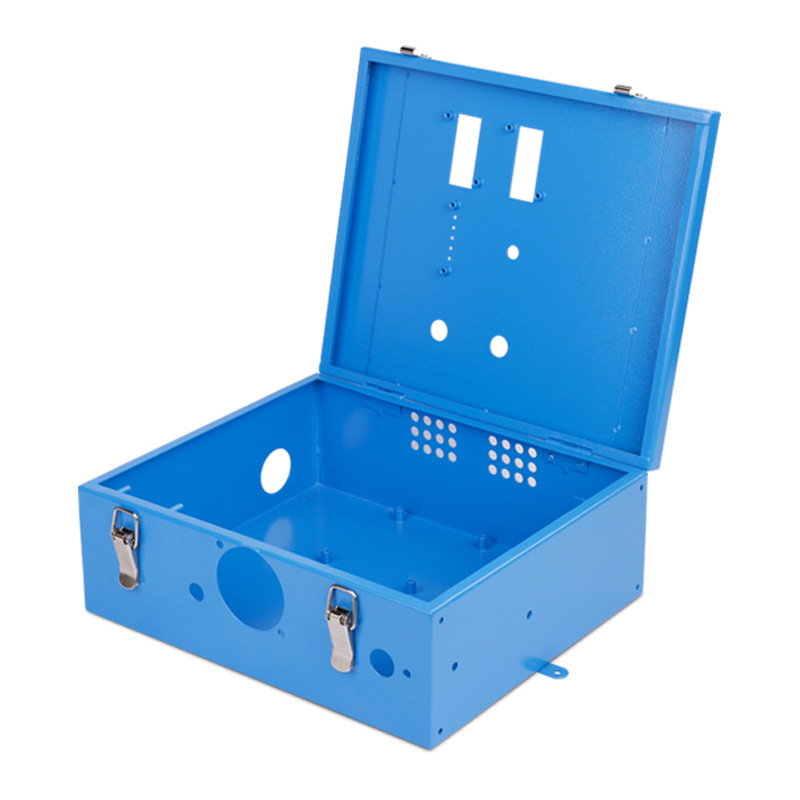
Advantages of Sheet Metal Fabrication
1. Cost-Effectiveness for Large-Scale Production
Sheet metal fabrication shines in high-volume production.
Mass production becomes highly efficient once setup costs are covered, significantly reducing the price per unit. This makes it ideal for industries that require consistent quality in large quantities, such as automotive and construction.
Example: Automotive manufacturers save money by producing millions of parts at a lower cost per unit once the initial setup is complete.
2. Versatility in Materials and Processes
From aluminum to steel, sheet metal can be molded into various shapes and sizes, accommodating many different needs. This flexibility makes it suitable for various applications, from small electronics to large industrial structures.
Example: Need corrosion-resistant parts for outdoor use? Stainless steel or aluminum can be chosen based on your project’s specific requirements.
3. Strength and Durability
Metals like steel and aluminum offer high strength and durability, making sheet metal fabrication ideal for industries where reliability is a priority. Products made through this process can withstand extreme conditions, whether in construction or aerospace.
Example: Aluminum’s high strength-to-weight ratio makes it a key material in the aerospace industry.
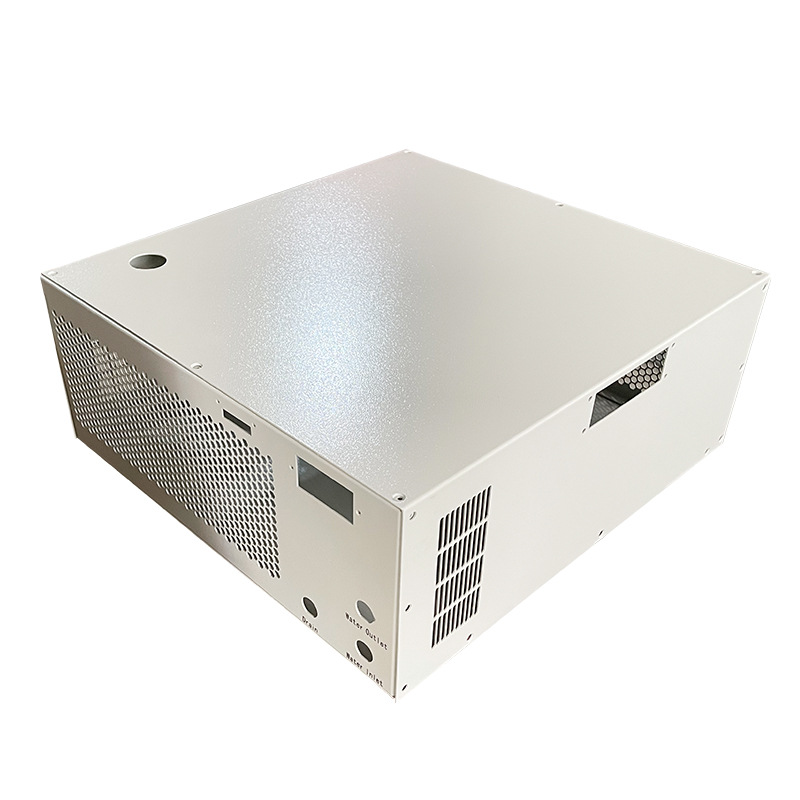
4. Precision with Modern Technology
With advancements like CNC machining and laser cutting, manufacturers can achieve near-perfect precision, reducing material waste and ensuring that every piece meets exact specifications.
Example: CNC machines can produce components with tolerances as tight as ±0.001 inches, ensuring that even complex designs are manufactured accurately.
5. Rapid Prototyping
Modern fabrication techniques allow for quick prototyping, which helps industries stay competitive by speeding up the design process and reducing time-to-market.
Example: An automotive company can produce a working prototype in just days, allowing for faster testing and iteration.
6. Lightweight and Easy to Handle
Metals like aluminum offer strength without the weight, making them easier to transport and work with during the fabrication process. This feature is precious in industries where weight is critical, such as aerospace.
Example: Lighter materials lead to more fuel-efficient airplanes without compromising structural integrity.
7. Environmentally Friendly
Many metals, including aluminum and steel, are fully recyclable, making sheet metal fabrication a sustainable choice for eco-conscious industries.
Example: Recycling metals reduces the need for raw material extraction, lowering environmental impact and conserving resources.
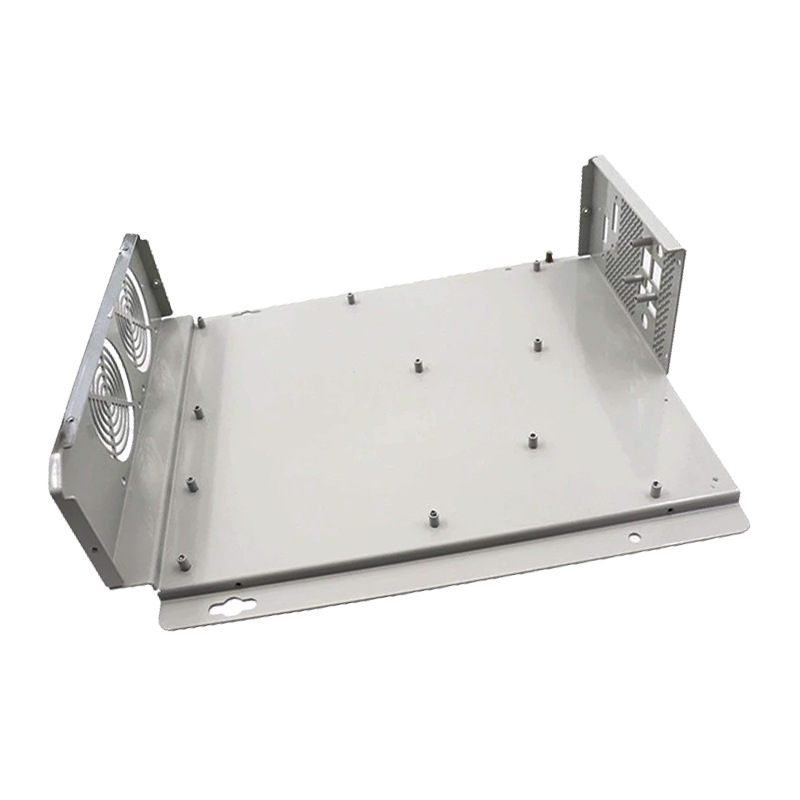
Disadvantages of Sheet Metal Fabrication
Before diving into the potential drawbacks, it’s important to note that no manufacturing process is without its challenges.
While sheet metal fabrication offers significant benefits in terms of cost, precision, and versatility, it’s essential to consider the limitations that may impact its suitability for specific projects.
Understanding both sides will provide a more balanced perspective, helping you make a more informed decision. Let’s now take a closer look at some of the disadvantages of sheet metal fabrication.
1. High Initial Tooling Costs
The setup for sheet metal fabrication can be expensive, especially for smaller production runs. Custom dies, and moulds increase the upfront investment, making this method less ideal for low-volume projects.
Tip: Consider CNC machining or 3D printing for smaller runs to minimize initial costs.
2. Corrosion Risks
While some metals are resistant to corrosion, others require protective coatings or treatments to prevent rust, which adds to the cost and time of production.
Solution: Choose materials like stainless steel or apply coatings to increase durability in harsh environments.
3. Design Limitations
While sheet metal can be shaped into many forms, it has limitations regarding highly intricate designs. More complex geometries may require additional processes, driving up production costs.
Tip: Explore alternative methods such as CNC machining or 3D printing for highly detailed designs.
4. Post-Fabrication Processes Required
After fabrication, additional steps such as polishing, painting, or anodizing may be necessary to improve the product’s appearance or durability, increasing both cost and production time.
Example: A visible part may need extra finishing processes to meet aesthetic or functional requirements.
5. Higher Scrap Rates
Cutting complex shapes from metal sheets often increases material waste, increasing costs. Although some scrap can be recycled, it’s still a factor to consider.
Tip: Optimize designs to reduce material waste and improve overall production efficiency.
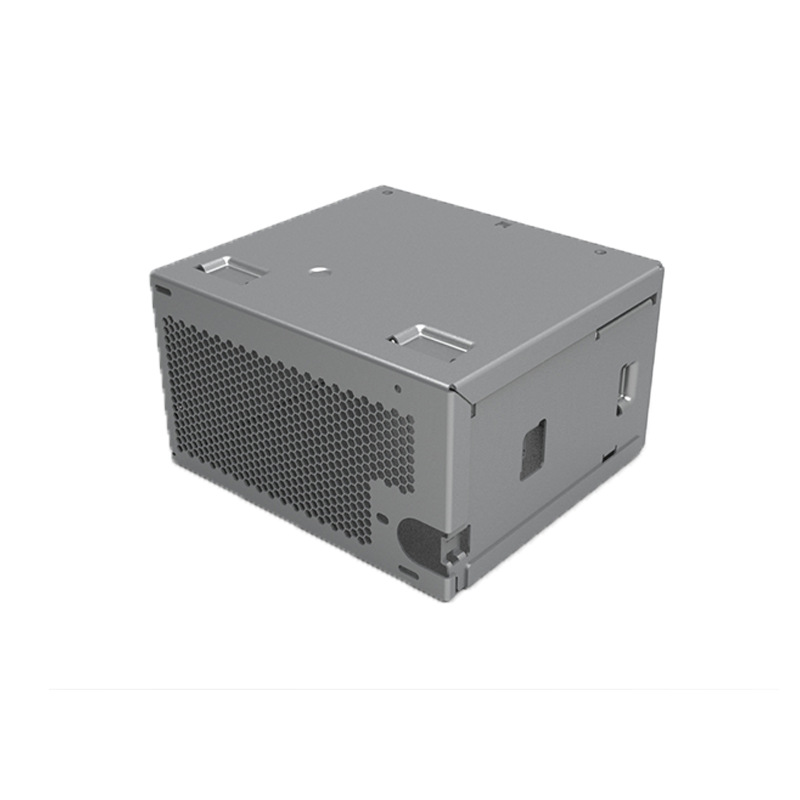
Conclusion:
If you’re looking for a manufacturing method that offers strength, precision, and cost-efficiency for large-scale production, sheet metal fabrication is a strong contender.
However, be mindful of the high setup costs, potential corrosion risks, and design limitations, especially if your project involves small production runs or intricate designs.
For high-volume projects that require durability and precision, sheet metal fabrication remains one of the top choices.
However, if you’re dealing with low-volume, complex designs, CNC machining or 3D printing might be better suited to your needs.
Have questions or need further guidance on whether sheet metal fabrication is right for you? Feel free to reach out—we’d love to help you make the best decision for your project!