Defects in machined parts remain a persistent issue for manufacturers, leading to higher costs, production delays, and dissatisfied customers.
Whether it’s dimensional inaccuracies or surface flaws, traditional quality control methods often fall short due to limitations in precision and consistency.
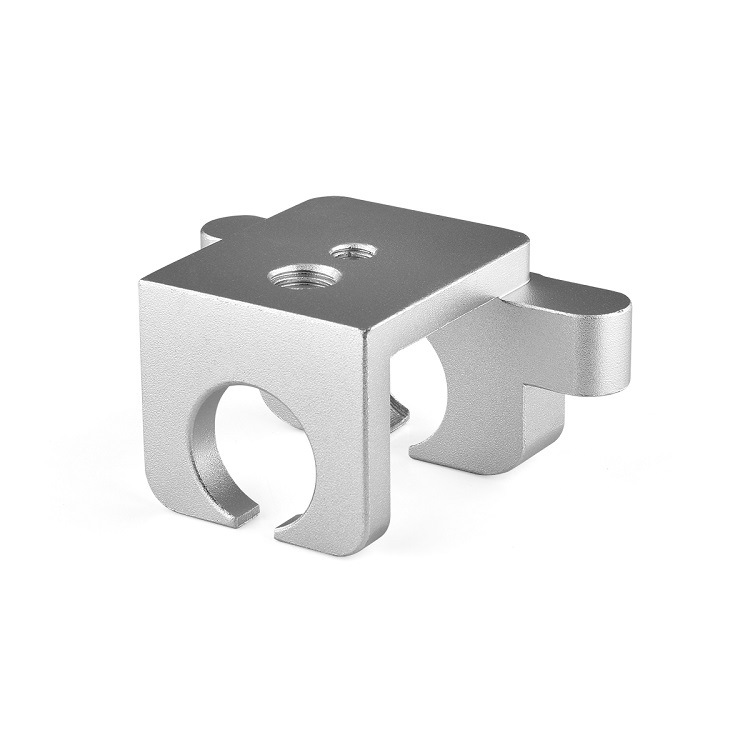
Nowadays, AI has emerged as a transformative solution to this problem.
So, can AI really reduce defects in machined parts? The answer is a resounding yes.
By leveraging machine learning, computer vision, and predictive analytics, AI enhances defect detection and prevention.
These advanced technologies empower manufacturers to achieve greater accuracy, reduce waste, and ensure product reliability.
Doubtlessly, AI can’t be ignored in the CNC machining industry.
In order to comprehensively understand the application of AI in this industry, now we will delve into how AI is reshaping manufacturing processes, its benefits, challenges, practical applications and many other concerns about AI.
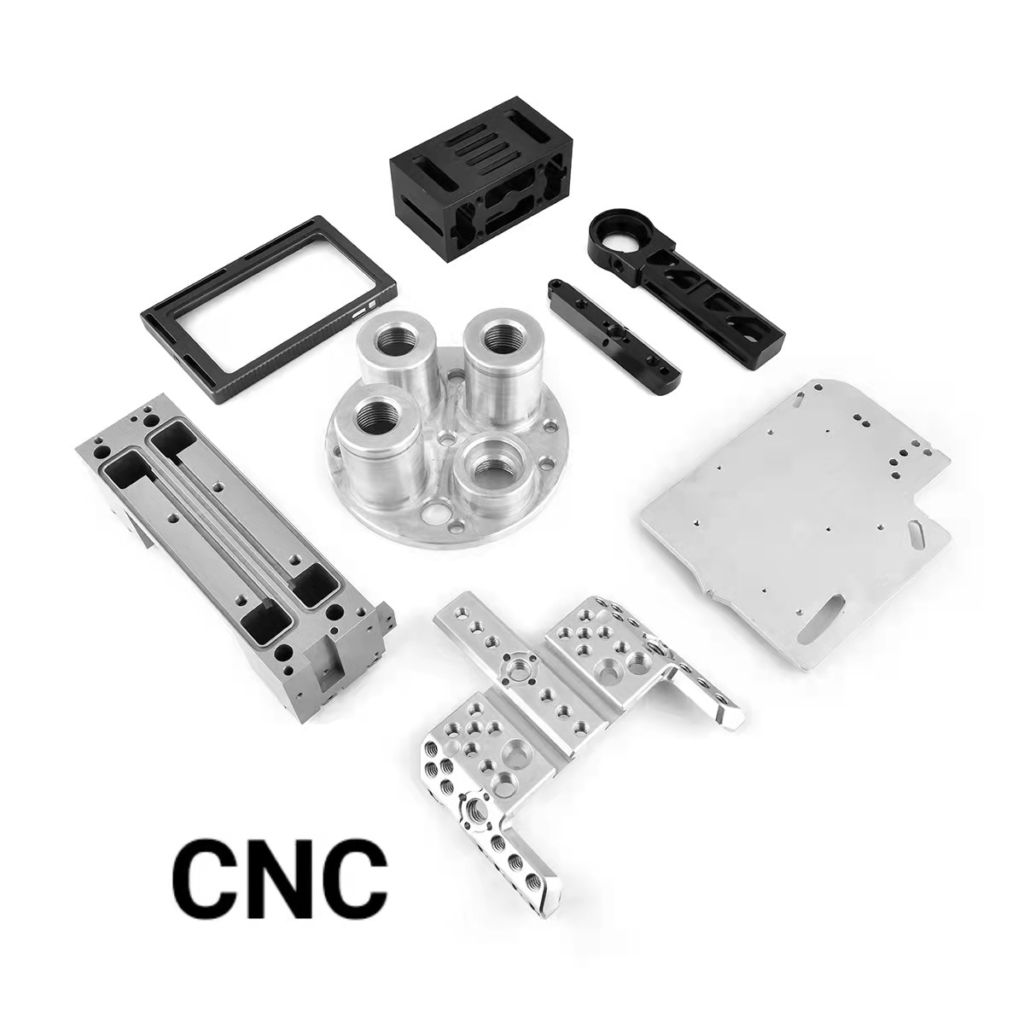
How is AI used for defect inspection?
Defect inspection is one of AI’s strongest use cases in manufacturing.
Traditional inspection methods rely on human inspectors or basic imaging tools to catch defects.
However, these methods are prone to inconsistencies, fatigue, and errors. AI, on the other hand, brings unparalleled accuracy and speed to the table.
1. AI-Based Visual Inspection:
AI uses computer vision technology to inspect components for flaws such as cracks, misalignments, or surface irregularities.
High-resolution cameras capture detailed images of machined parts, and AI algorithms analyze these images in milliseconds, identifying even the smallest defects.
For example, in aerospace manufacturing, AI-powered vision systems scan turbine blades for surface irregularities, ensuring safety-critical parts meet stringent standards.
2. Real-Time Monitoring:
AI doesn’t wait until production is complete to identify issues.
Instead, it continuously monitors processes, identifying deviations from desired parameters (e.g., temperature, pressure, or speed) that might lead to defects.
Early detection could allow manufacturers to make immediate corrections, reducing scrap rates and downtime.
3. Enhanced Traceability:
AI systems log data from every inspection, creating detailed reports on defect types, frequencies, and locations.
This information helps manufacturers pinpoint recurring problems and refine their processes.
For companies like Partzcore’s CNC machining services, AI, as an additional approach to reducing defects and providing products with higher precision and quality, helps fully utilize previously complete and advanced equipment.
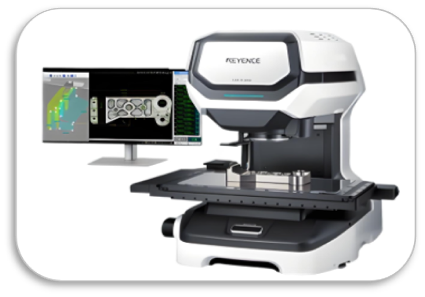
What can AI do in reducing errors?
Errors in machining often result from undetected anomalies in equipment or materials. AI excels at identifying and addressing these errors through:
1. Pattern Recognition:
AI analyzes historical data to identify patterns that indicate potential problems.
For instance, if a CNC machine produces slightly warped parts after running for a certain number of hours, AI can recognize this trend and recommend preventative maintenance.
2. Anomaly Detection:
Machine learning models are trained to detect deviations from the norm.
These anomalies might include tool wear, fluctuations in material quality, or inconsistencies in machining parameters.
By flagging these issues early, AI prevents small errors from escalating into larger defects.
3. Predictive Maintenance:
Predictive maintenance is a game-changer in machining.
AI predicts when a machine component is likely to fail and alerts operators to perform maintenance before breakdowns occur.
This proactive approach not only prevents defects but also extends the lifespan of machinery.
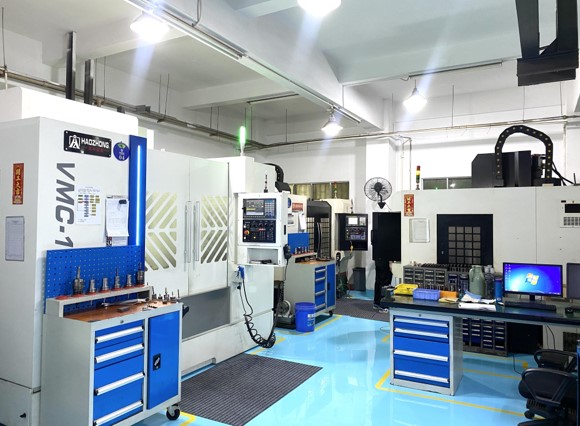
What are the benefits and challenges of AI in CNC machine defects?
AI has now been applied in the CNC machining industry, but we have yet to fully understand its benefits and challenges since its adoption is relatively recent.
Only by comprehensively grasping the role AI plays can we maximize its strengths and mitigate its weaknesses, significantly reducing defects and improving production efficiency.
Generally, AI enhances CNC performance in several ways:
1. Precision Manufacturing:
AI improves the dimensional accuracy of parts, ensuring they meet exact specifications.
This is critical for industries like aerospace, where even minor inaccuracies can have catastrophic consequences.
2. Reduced Scrap Rates:
Defects often lead to scrap, wasting materials and money. AI minimizes these losses by catching issues early in the process.
3. Faster Turnaround Times:
AI-powered inspection systems work at lightning speed, allowing manufacturers to produce more parts in less time without sacrificing quality.
4. Predictive Analytics:
AI predicts when tools or machines will fail, preventing sudden breakdowns that could disrupt production.
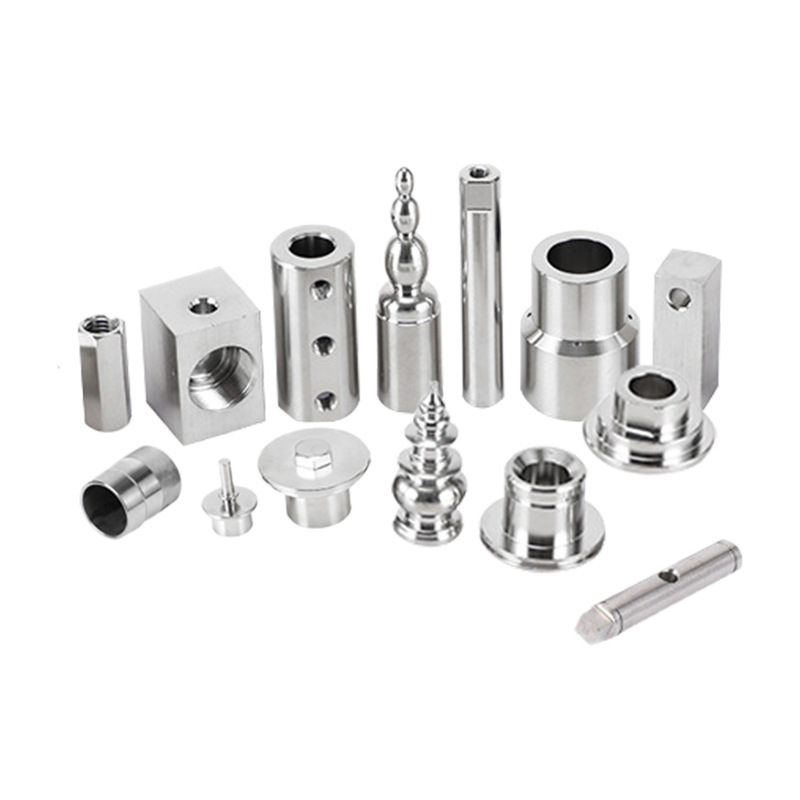
Multiple industries have successfully implemented AI-driven defect reduction strategies. For instance, in CNC machining and turning, manufacturers have documented:
• 40% defect reduction in automotive manufacturing
• Over 50% improvement in predictive maintenance
• Enhanced product consistency and reliability
While the benefits of AI are clear, its implementation comes with challenges:
1. High Initial Costs:
AI systems require significant investment in hardware, software, and infrastructure. Small and medium-sized manufacturers may struggle with these upfront expenses.
2. Data Requirements:
AI relies on large volumes of high-quality data for training. Manufacturers with limited data may face difficulties in deploying effective AI solutions.
3. Workforce Training:
Employees must be trained to operate and maintain AI-powered tools, which can be time-consuming and expensive.
4. Integration Complexities:
Integrating AI into legacy systems can be challenging, requiring specialized expertise and custom solutions.
Despite these challenges, the long-term benefits of AI—such as reduced defects, higher productivity, and lower costs—make it a worthwhile investment.
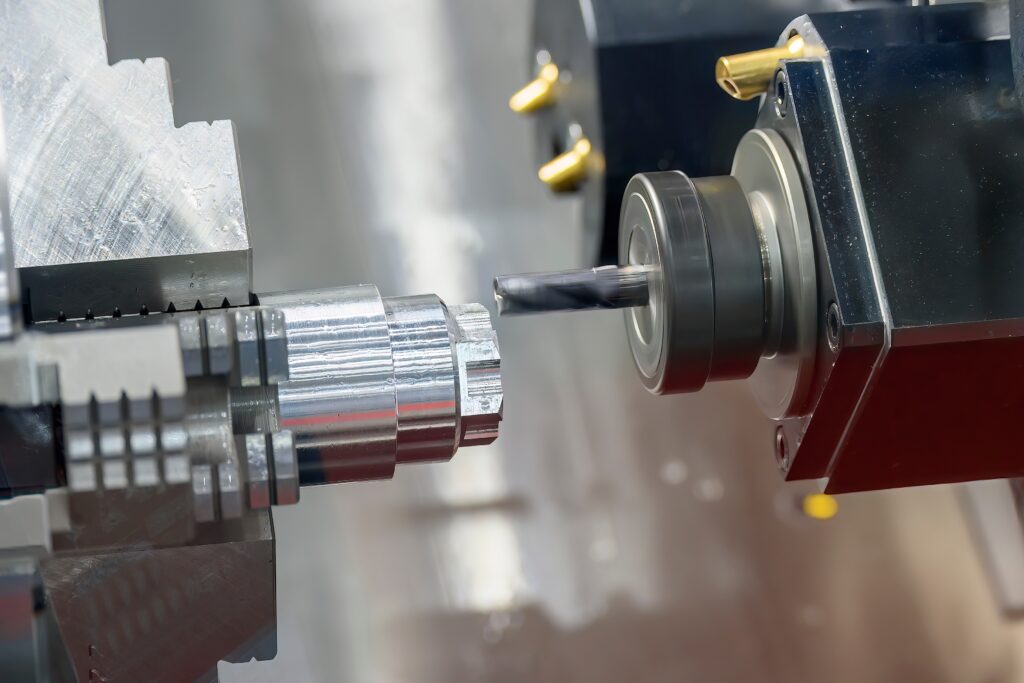
The future of AI in CNC machining
As AI technology continues to evolve, its transformative impact on CNC machining will deepen, opening doors to unprecedented efficiency, precision, and innovation.
Here’s a look at potential future advancements:
1. Autonomous Machining
Future AI-powered machines could operate entirely without human intervention.
These systems would leverage real-time data analysis, self-calibration, and process optimization to carry out complex tasks with minimal oversight.
Autonomous machining would reduce defects caused by human error, improve operational efficiency, and enable round-the-clock production.
2. Self-Learning Systems
AI systems are advancing toward self-learning capabilities, allowing them to adapt and master new machining techniques without requiring external retraining.
This would enable machines to adjust dynamically to changes in materials, tools, or production requirements, ensuring consistent quality even in highly variable scenarios.
3. Predictive Design and Prototyping
AI may soon assist in the design and prototyping stages, predicting potential defects before production begins.
Manufacturers can refine designs and minimize waste by simulating machining processes in virtual environments, accelerating product development cycles.
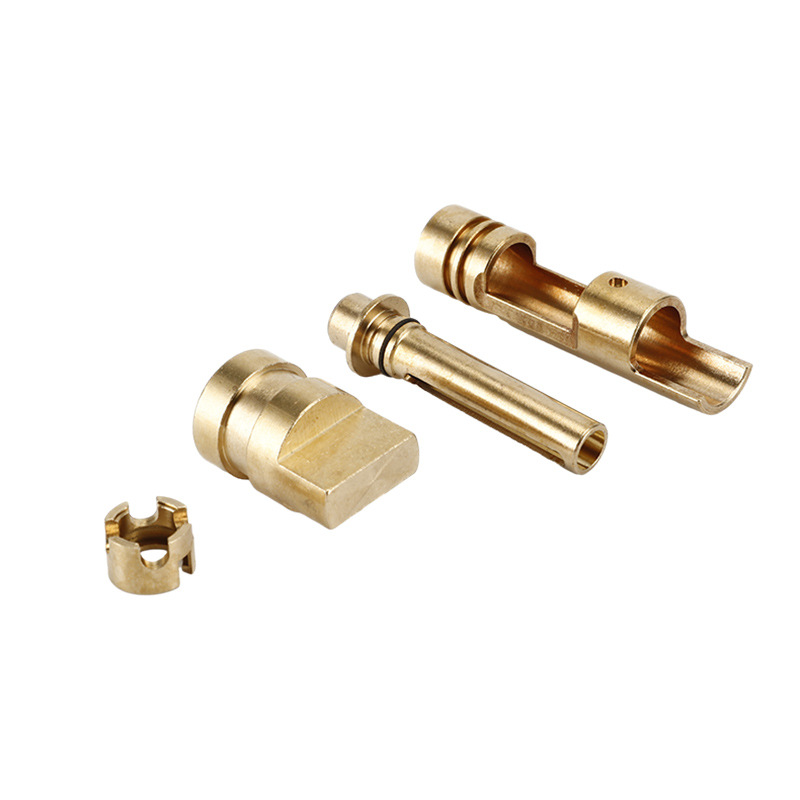
Conclusion
AI is transforming defect reduction in machining, offering manufacturers unparalleled precision, efficiency, and quality control.
By integrating AI, businesses can reduce waste, improve customer satisfaction, and enhance competitiveness.
Manufacturers must act swiftly to harness AI’s potential. As a strategic imperative, adopting AI is no longer optional—it’s essential for thriving in an increasingly demanding market.
Whether through defect prevention or process optimization, AI represents the future of smart manufacturing.