CNC (Computer Numerical Control) programming has long been the backbone of precision manufacturing.
By converting computer models into machine-readable instructions, it ensures that parts are produced with unmatched accuracy.
However, with the rise of Artificial Intelligence (AI), a critical question arises: Can AI replace manual CNC programming?
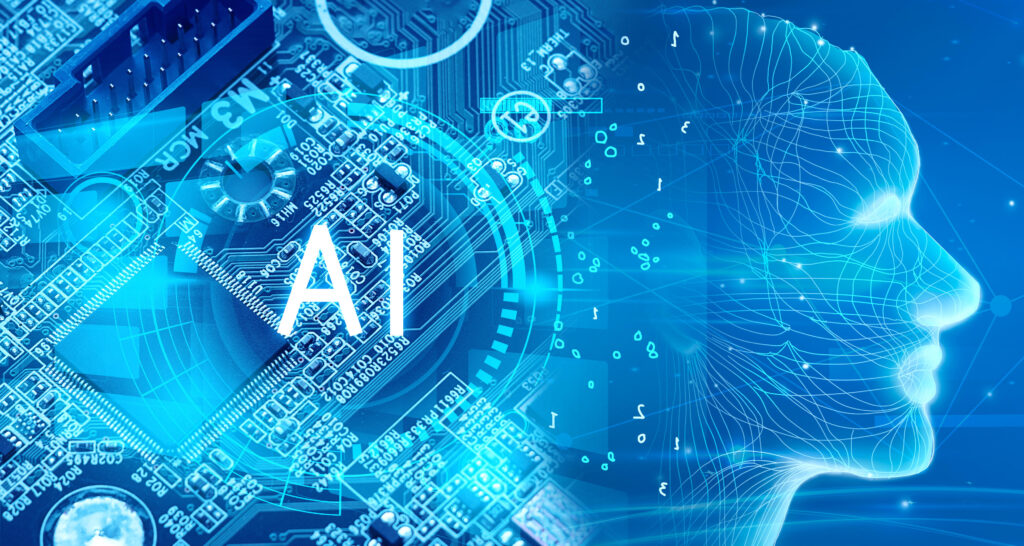
As AI continues to reshape industries, manufacturers are grappling with its potential to revolutionize CNC programming.
While AI promises automation, reduced errors, and increased efficiency, many wonder if it can completely replace the expertise of human programmers.
This article explores the potential of AI in CNC programming, its advantages, limitations, and whether it can truly replace the critical human touch in manufacturing.
By delving into the various benefits, real-world applications, and challenges of AI, we’ll offer a comprehensive view of the evolving role of AI in CNC programming and its future in modern manufacturing.
-
Table Of Contents
-
1. Can AI Replace Manual CNC Programming?
-
2. AI in CNC Programming: A Game-Changer for Manufacturing
-
3. What Are Advantages of AI in CNC Programming?
-
4. What Are Limitations of AI in CNC Programming?
-
5. Can AI Replace Manual CNC Programming?
-
6. The Future Trend: A Collaborative Approach
-
7. Summary
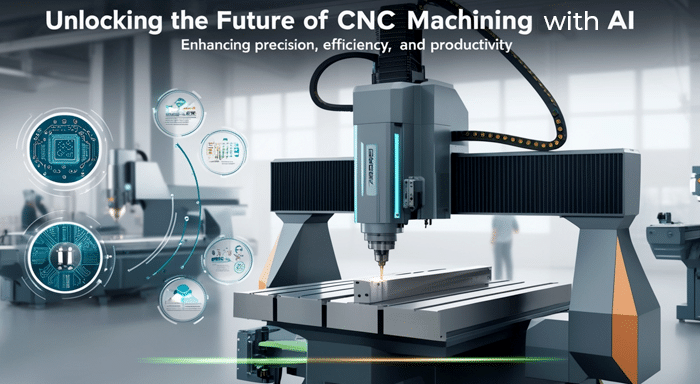
AI in CNC Programming: A Game-Changer for Manufacturing
AI has already begun to transform CNC programming by streamlining tasks that were once entirely manual.
Leveraging machine learning and advanced algorithms, AI can analyze CAD models, generate optimized G-code, and propose machining parameters that ensure precision and efficiency.
Key Features of AI in CNC Programming:
• Automated tool path generation.
• Real-time error detection and correction.
• Adaptive machining strategies based on material properties.
• Intelligent simulation for process validation.
The impact of AI on CNC programming is profound, reducing programming times, improving accuracy, and opening doors to new levels of automation in manufacturing.
The manufacturing world is experiencing a transformative revolution, with Artificial Intelligence (AI) emerging as a game-changing force in CNC machining services.
Traditional CNC programming, once entirely dependent on manual expertise, is now being reimagined through the lens of advanced computational intelligence.

What Are Advantages of AI in CNC Programming?
1. Increased Efficiency and Speed:
AI reduces the time traditionally required for manual CNC programming.
Routine tasks like tool selection, defining machining strategies, and generating G-code are now automated, completing in a fraction of the time.
This acceleration enables manufacturers to handle more projects and meet demanding deadlines while reducing lead times.
2. Enhanced Precision and Accuracy:
Human error is inevitable, and in CNC programming, even small mistakes can result in costly delays and defects.
AI minimizes these risks by analyzing historical data, spotting potential errors, and offering preventive solutions before they happen.
3. Cost Savings:
Automation with AI leads to reduced dependency on manual labor for programming tasks.
As a result, businesses can significantly cut labor costs and reduce the risk of human error that may otherwise lead to production delays and added expenses.
Over time, businesses can experience substantial cost savings by adopting AI-powered programming solutions.
4. Scalability and Adaptability:
AI can adapt to different machining operations and materials.
Whether dealing with complex aerospace components or simple automotive parts, AI can fine-tune machining parameters to ensure optimal outcomes across various tasks, providing consistent quality throughout.
5. Data-Driven Insights:
AI systems capture and analyze vast amounts of production data.
This data can reveal patterns that optimize machining operations, predict maintenance needs, and help improve overall production performance.
AI-driven insights enable manufacturers to make informed decisions that drive efficiency.
At Partzcore’s CNC part design services, these technologies are being strategically implemented to enhance manufacturing precision and efficiency.
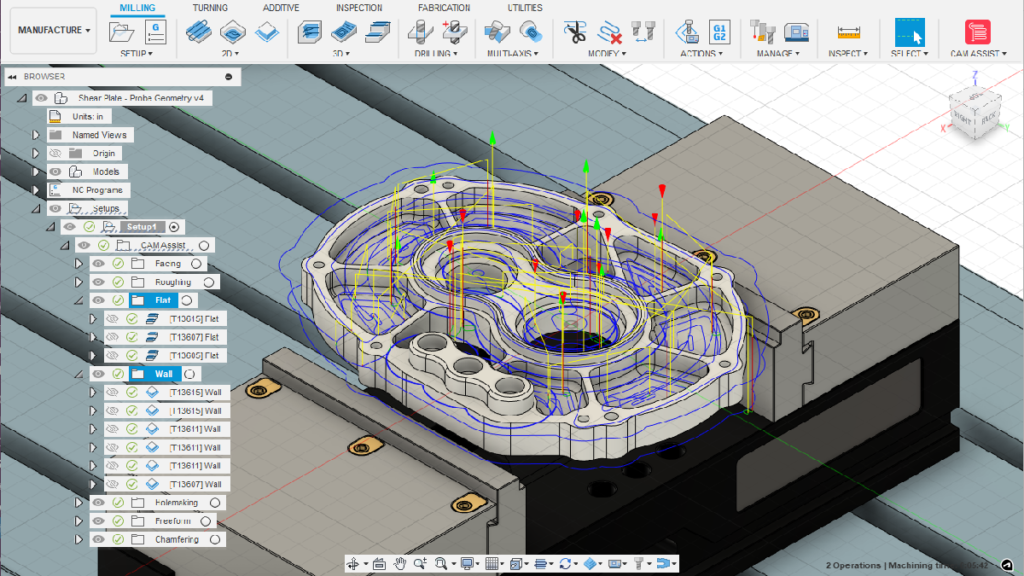
What Are Limitations of AI in CNC Programming?
Despite its incredible advantages, AI in CNC programming does have its limitations.
Understanding these challenges is crucial when considering AI as a replacement for manual programming.
1. Limited Creativity:
While AI excels at analyzing data and following predefined rules, it struggles with creativity.
Human programmers bring invaluable ingenuity to tasks that require unconventional approaches or intricate designs, such as parts with unique geometries or materials.
2. Dependence on Quality Input:
AI relies heavily on high-quality data.
The AI system may produce inaccurate or suboptimal results if the input—such as CAD models or machine specifications—is flawed or incomplete.
In such cases, human intervention becomes necessary to correct these issues.
3. Lack of Contextual Understanding:
AI lacks the ability to understand context the way humans do.
For instance, if a machining issue arises mid-production, such as a sudden defect in materials, AI may struggle to adjust the process accordingly, requiring the expertise of a human programmer to make quick, informed decisions.
4. High Initial Investment:
Implementing AI solutions can be costly, with substantial software, hardware, and training investments.
Small and medium-sized manufacturers may find these costs prohibitive, which limits the widespread adoption of AI in CNC programming.
Despite its transformative potential, AI in CNC programming has its limitations. It’s essential to understand these drawbacks before making a leap into full automation.
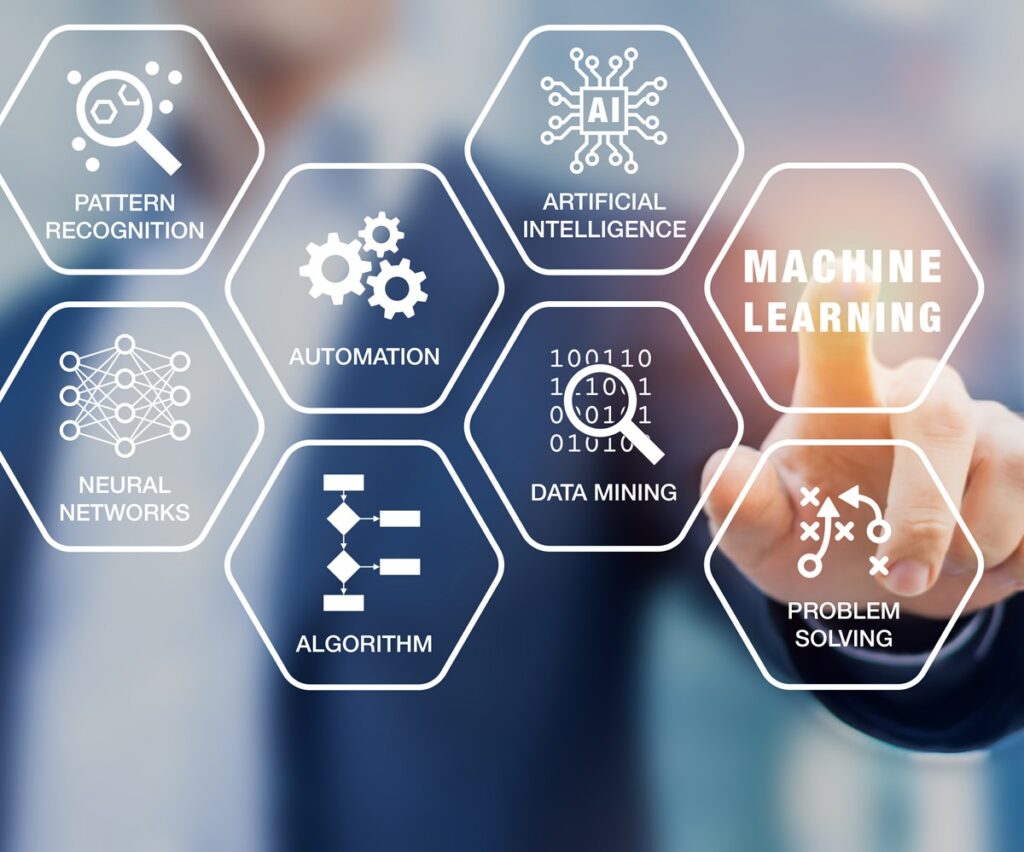
Can AI Replace Manual CNC Programming?
The short answer is no, at least not entirely.
While AI can automate many aspects of CNC programming, human expertise remains indispensable for several reasons:
1. Handling Complex Customizations:
Many machining jobs require unique solutions beyond AI algorithms’ capabilities.
Human programmers excel at thinking outside the box and developing creative strategies for complex or highly customized parts.
2. Ensuring Safety and Compliance:
CNC programming involves strict adherence to safety and quality standards.
Human oversight ensures that these standards are met, especially in industries like aerospace and healthcare, where even minor errors can have severe consequences.
3. Bridging the Gap Between Design and Manufacturing:
AI cannot fully understand the intent behind a design.
Human programmers are crucial in translating design specifications into actionable machining instructions, ensuring that the final product aligns with the designer’s vision.
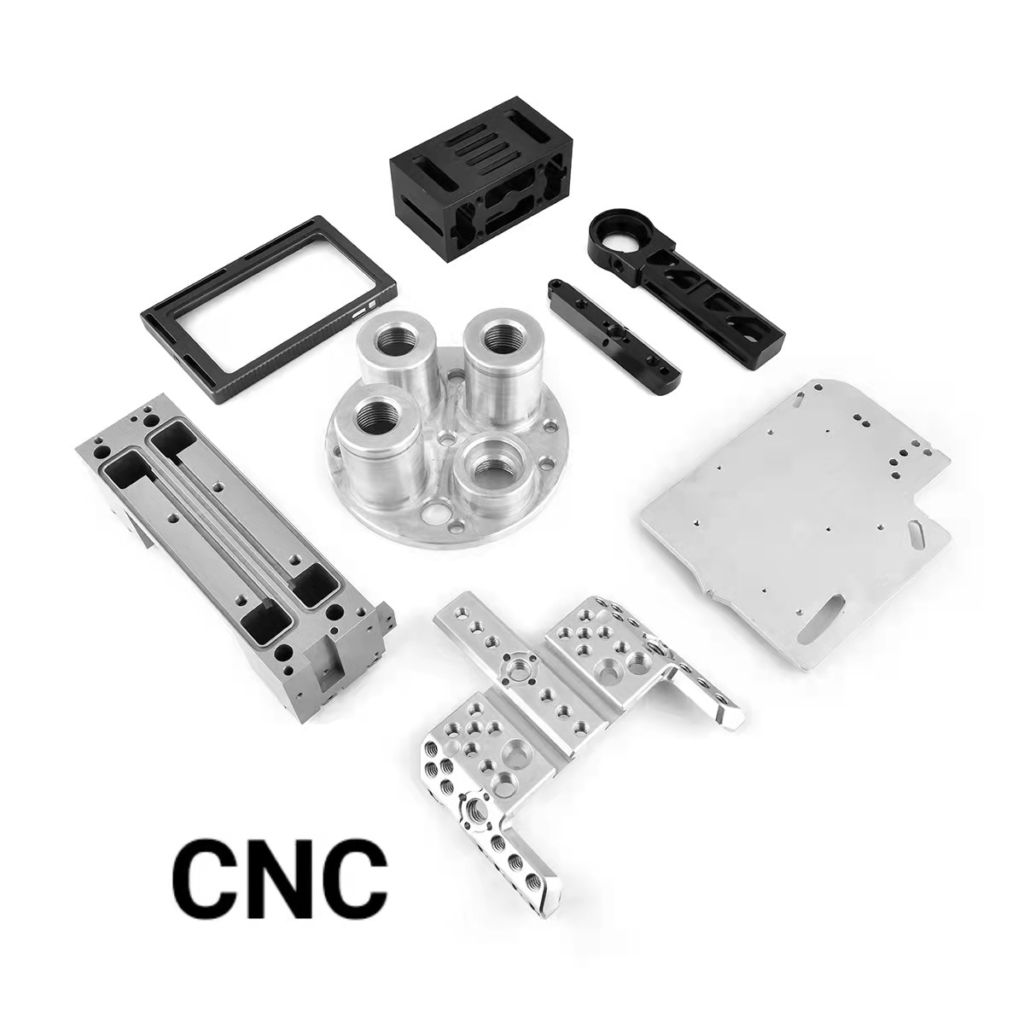
The Future Trend: A Collaborative Approach
The future of CNC programming lies in collaboration between AI and human programmers.
AI will continue to evolve, handling routine tasks and providing data-driven insights, while human experts focus on high-value activities like innovation, troubleshooting, and system optimization.
• Hybrid Programming Models: Combining AI-driven automation with manual programming for greater flexibility and control.
• AI-Powered Training Tools: Using AI to train new programmers by simulating real-world scenarios and providing instant feedback.
• Predictive Maintenance: Leveraging AI to monitor CNC machines in real-time, predicting maintenance needs and preventing costly breakdowns.
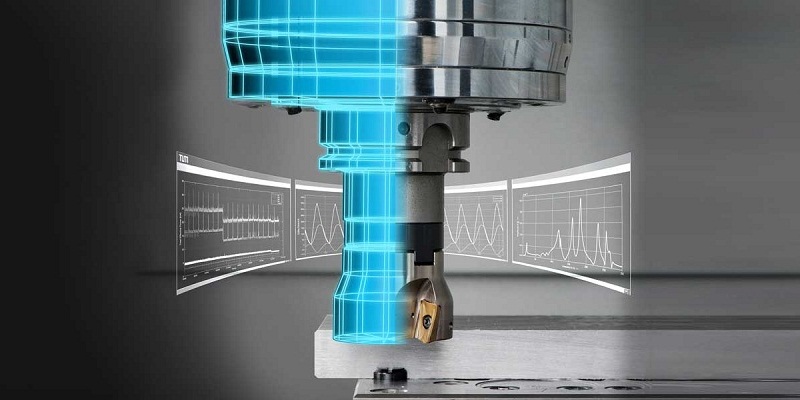
Conclusion
Artificial Intelligence is undoubtedly transforming CNC programming, offering numerous benefits such as increased efficiency, reduced errors, and cost savings.
However, it is not a replacement for manual programming but a powerful tool to augment human capabilities.
By embracing AI, manufacturers can unlock new levels of productivity and innovation while preserving the invaluable role of skilled programmers.
The path forward is clear: collaboration over replacement.
As AI continues to evolve, the synergy between human expertise and machine intelligence will define the future of CNC programming.