Electrical systems in industries such as automotive, aerospace, and manufacturing demand durable components capable of withstanding extreme temperatures.
Among these, stamped connectors often raise the question: Can they maintain reliable performance in such conditions?
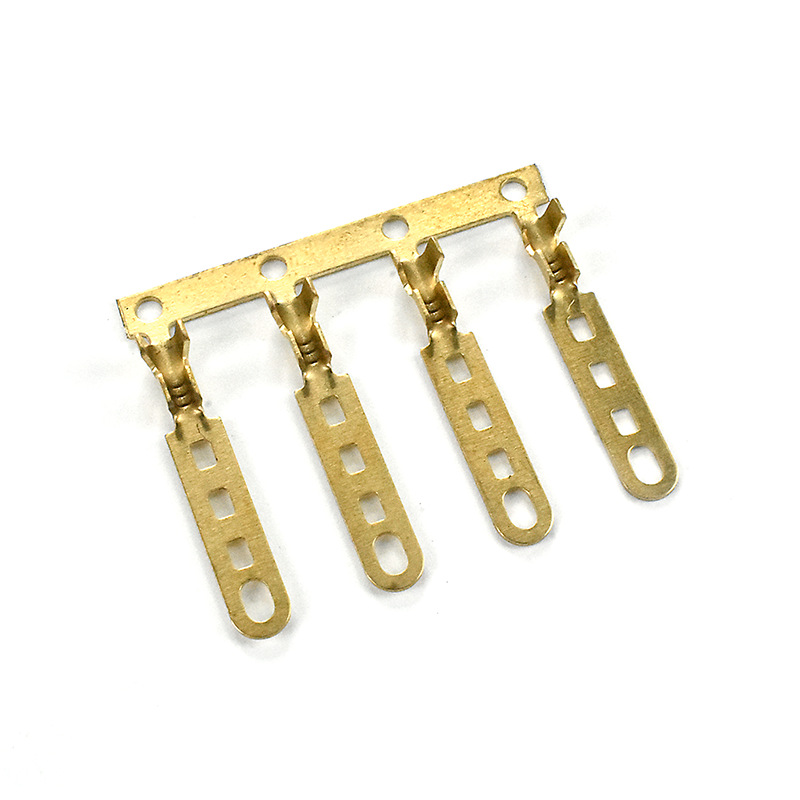
Stamped connectors are a reliable choice for high-temperature environments, provided they are crafted from heat-resistant materials like nickel or copper alloys and enhanced with protective coatings or insulation.
Their cost-effectiveness, lightweight structure, and adaptability make them an increasingly popular solution in applications requiring thermal resilience.
Now, let’s explore the advantages of stamped connectors, their role in high-temperature environments, key selection factors, and practical tips for overcoming potential challenges.
-
Table Of Contents
-
1. Are Stamped Connectors Reliable in High-Temperature Environments?
-
2. What Makes Stamped Connectors Suitable for High Temperatures?
-
3. Why Choose Stamped Connectors Over Machined Contacts?
-
4. How Do Coatings and Insulators Enhance Performance?
-
5. What Challenges Do Stamped Connectors Face in Extreme Environments?
-
6. Best Practices for Maintaining Stamped Connectors in Extreme Conditions
-
7. Summary
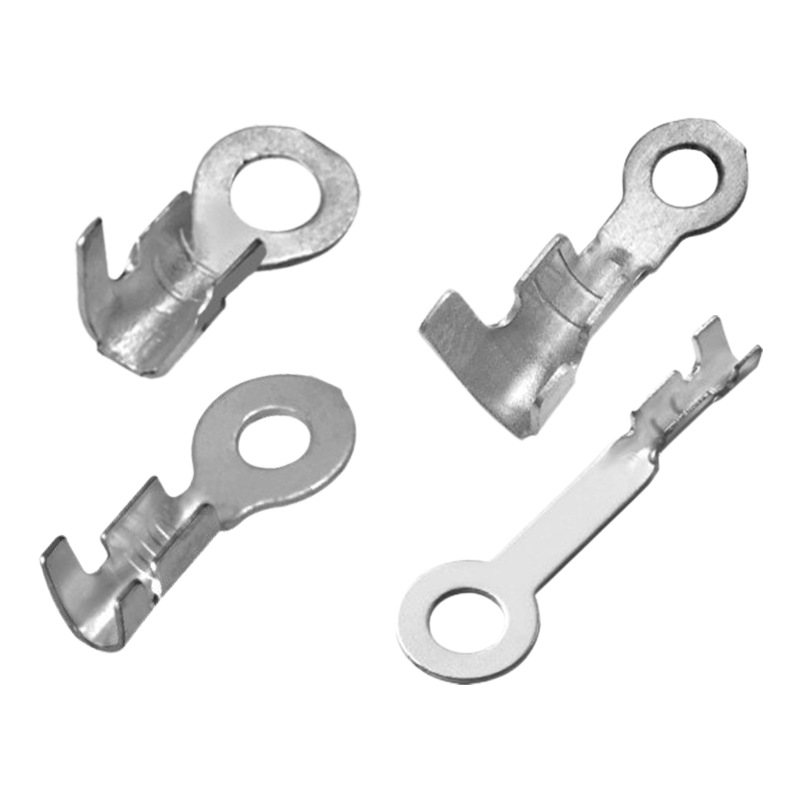
What Makes Stamped Connectors Suitable for High Temperatures?
Stamped connectors excel in high-temperature environments due to their carefully chosen materials, coatings, and designs.
These features ensure durability and efficiency under thermal stress, making them reliable for demanding applications.
Here’s a closer look at the key factors:
1. Heat-Resistant Materials
Stamped connectors are constructed using metals designed to withstand high temperatures:
• Nickel Alloys: Common in aerospace and automotive applications, nickel alloys are prized for their ability to resist thermal fatigue and corrosion, even at sustained high temperatures.
• Copper Alloys: These alloys balance high electrical conductivity with moderate thermal resistance, making them suitable for systems that prioritize energy efficiency alongside heat tolerance.
• Stainless Steel: Known for its durability, stainless steel can endure extreme heat and resist corrosion, though it is heavier than other options.
By selecting the appropriate material based on specific use cases, engineers ensure the longevity and performance of the connector under harsh conditions.
2. Advanced Coatings
Protective coatings enhance the thermal and mechanical properties of stamped connectors:
• Nickel Plating: Adds a protective layer to combat oxidation and corrosion, ensuring consistent performance.
• Gold Coating: Though more costly, gold provides superior electrical conductivity and is often used in high-reliability environments like aerospace systems.
• Specialized Polymers: Insulating coatings like PEEK (Polyether Ether Ketone) or silicone resist heat and shield against chemical exposure and physical wear.
3. Optimized Design Features
The design of stamped connectors plays a crucial role in their thermal performance:
• Heat-Dissipation Slots: Prevent localized overheating by allowing air circulation around the connector.
• Spring Mechanisms: Accommodate thermal expansion and contraction without losing electrical contact, ensuring consistent signal transmission.
Through these innovations, stamped connectors deliver reliability in various extreme conditions.
Stamped connectors are precision-engineered electrical components created through a sophisticated metal stamping process.
At Partzcore’s metal stamping services, these connectors are crafted using advanced techniques that ensure exceptional quality and performance.
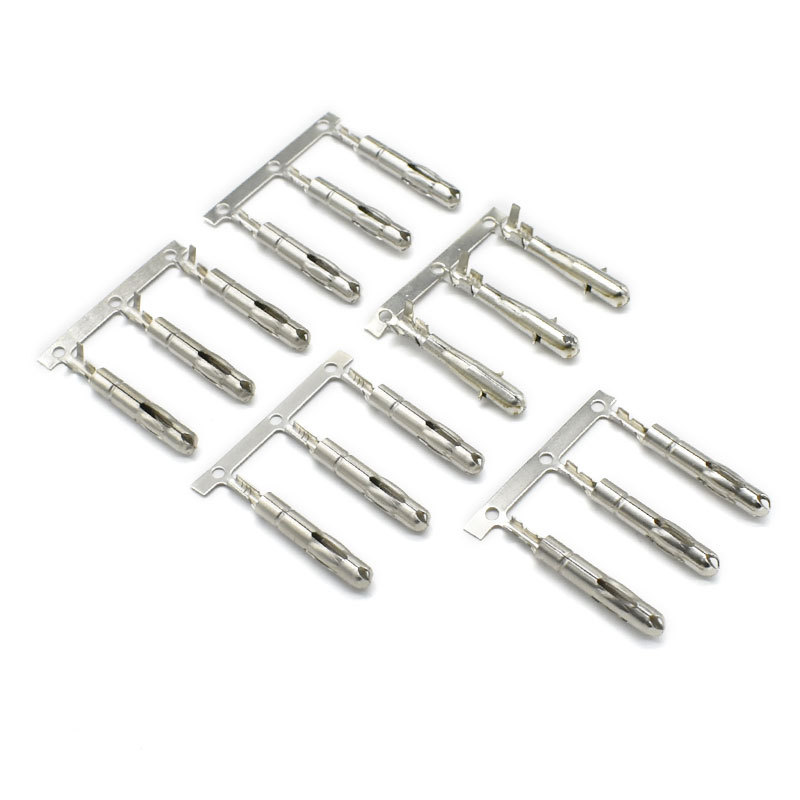
Why Choose Stamped Connectors Over Machined Contacts?
Stamped connectors offer unique advantages compared to their machined counterparts, especially in high-temperature environments.
While both types have their place, stamped connectors are increasingly favored for specific applications:
Cost Efficiency
The stamping process involves high-speed, automated production, which significantly lowers manufacturing costs.
Stamped connectors provide an economical yet high-quality solution for industries requiring large-scale production, such as automotive and consumer electronics.
Lightweight Structure
Stamped connectors are typically thinner and lighter than machined contacts.
This weight reduction is especially valuable in sectors like aerospace and electric vehicles (EVs), where minimizing system mass can improve fuel efficiency and performance.
Customizability and Versatility
Stamped connectors can be tailored to fit specific design requirements, from low-power signaling to high-current applications.
They are compatible with automated assembly processes, ensuring precise and consistent production.
Advancements in Durability
While machined contacts are traditionally seen as more robust, innovations in materials and coatings have elevated the durability of stamped connectors.
Today, they can withstand extreme heat and harsh environments as effectively, making them a viable alternative for many high-demand applications.
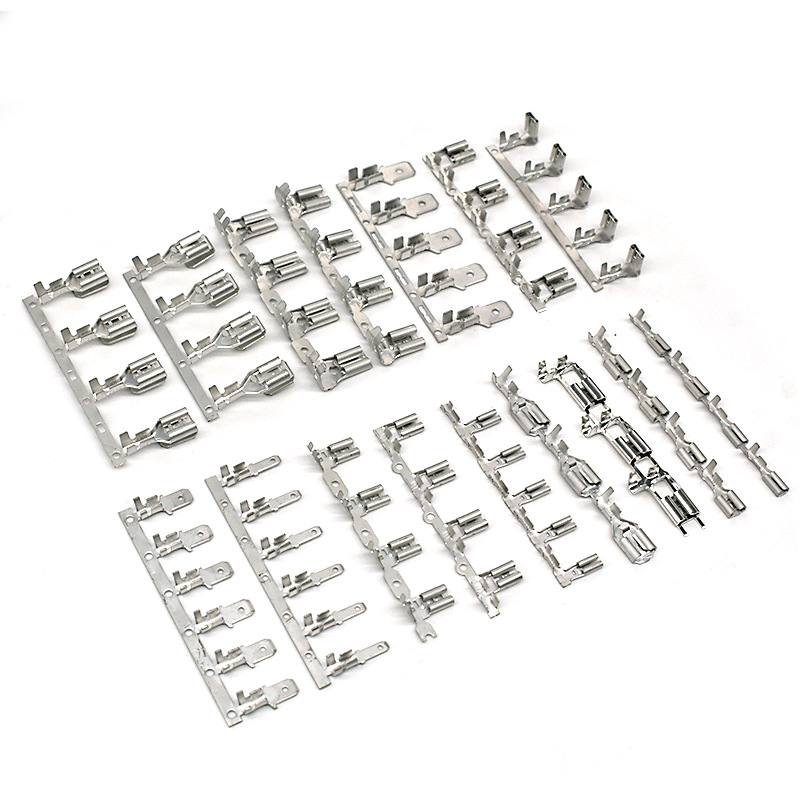
How Do Coatings and Insulators Enhance Performance?
The longevity and effectiveness of stamped connectors in high-temperature environments heavily rely on the quality of their coatings and insulation.
These enhancements play a dual role in thermal protection and maintaining electrical integrity:
Protective Coatings
1. Nickel Coatings:
o Provide a barrier against oxidation, which can weaken connectors over time.
o Enhance thermal resistance, allowing connectors to perform reliably in prolonged high-temperature settings.
2. Gold Coatings:
o Offer unmatched electrical conductivity, ensuring stable performance even under thermal stress.
o Resist tarnishing and corrosion, making them ideal for precision applications.
Thermal Insulators
1. PEEK Insulation:
o Highly resistant to extreme temperatures, PEEK is often used in aerospace and industrial applications where connectors encounter both heat and chemical exposure.
o Provides structural integrity, reducing the risk of deformation under prolonged stress.
2. Silicone Jackets:
o Flexible and durable, silicone insulation is particularly effective in dynamic environments where connectors experience vibration or movement.
By integrating these coatings and insulators, stamped connectors deliver superior reliability and longevity in harsh operating conditions.
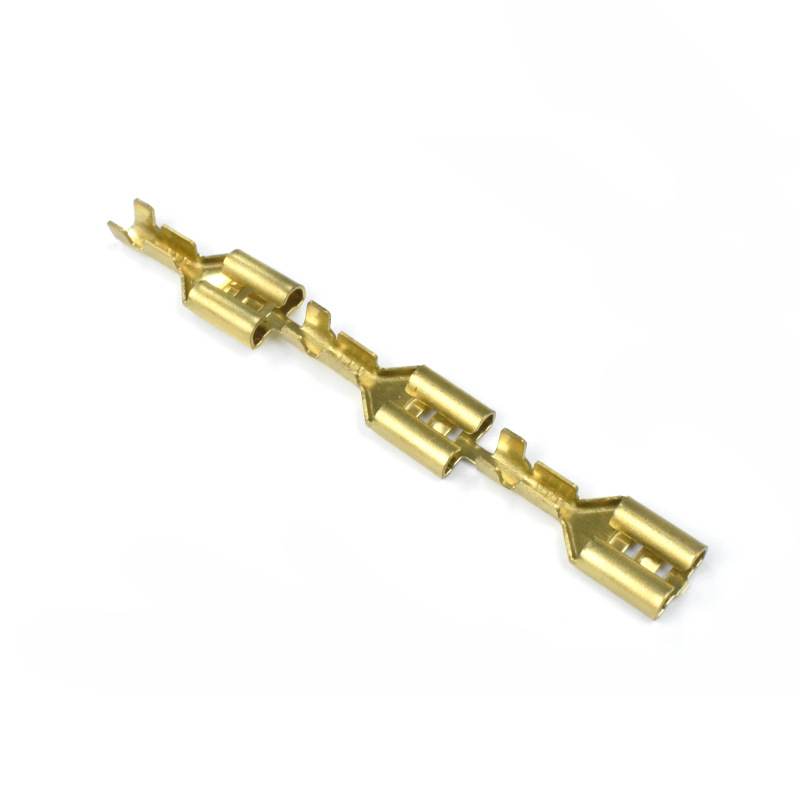
What Challenges Do Stamped Connectors Face in Extreme Environments?
Stamped connectors are not without limitations, and understanding these challenges is essential for ensuring optimal performance:
Material Fatigue
Prolonged exposure to high temperatures can weaken connector materials, causing them to crack or deform.
This is particularly concerning in applications where connectors undergo repeated thermal cycles.
Our high-precision metal stamping parts leverage advanced materials:
Titanium Alloys: Exceptional heat resistance
Stainless Steel Variants: Robust thermal performance
Specialized Nickel Alloys: Superior high-temperature characteristics
Increased Electrical Resistance
As temperatures rise, the electrical resistance of certain metals can increase, potentially reducing signal transmission efficiency.
This requires a careful selection of materials and coatings to mitigate the effect.
Corrosion Risks
High temperatures often accelerate chemical reactions, leading to faster corrosion, especially in environments with high humidity or chemical exposure.
Protective coatings like nickel or gold are essential to counteract this issue.
Mechanical Wear
Thermal expansion and contraction can lead to loosening or misalignment over time, compromising the connector’s structural and electrical integrity.
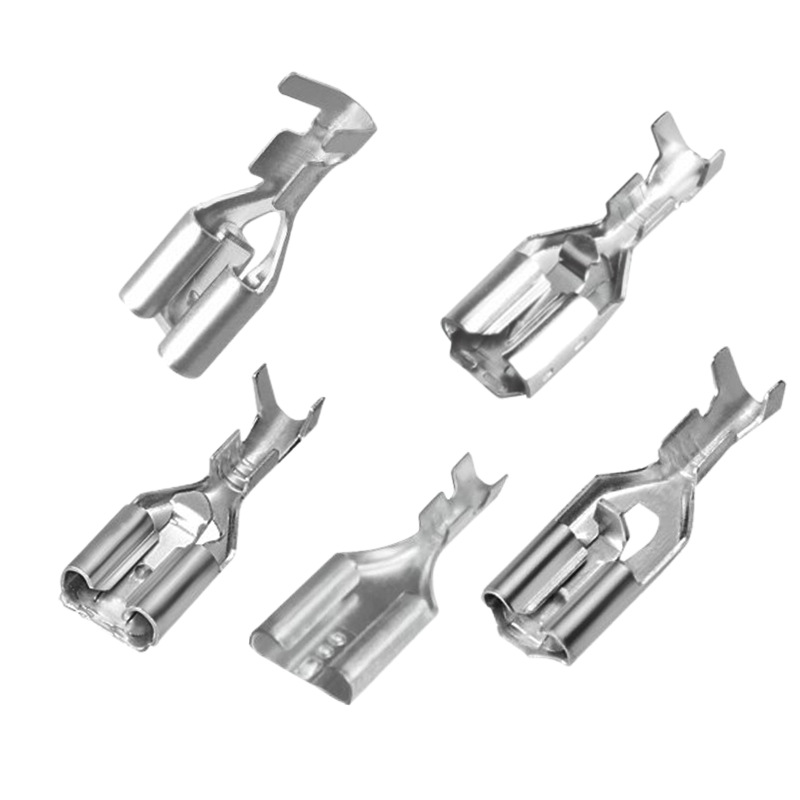
Best Practices for Maintaining Stamped Connectors in Extreme Conditions
Ensuring the longevity and performance of stamped connectors in high-temperature applications involves strategic maintenance practices.
1. Regular Inspections
Conduct periodic visual and electrical inspections to identify early signs of material fatigue, corrosion, or wear. This proactive approach prevents system failures and reduces maintenance costs.
2. Adequate Ventilation
Install connectors in environments with sufficient airflow to dissipate heat. Ventilation minimizes the risk of localized overheating, which can degrade the connector.
3. Load Management
Avoid overloading connectors beyond their rated electrical capacity, as excessive current can cause overheating and accelerated wear. Using connectors that match the application’s electrical requirements is critical.
4. Corrosion Prevention
Consider additional protective measures such as weatherproof enclosures or enhanced coatings for environments prone to humidity or chemical exposure. These safeguards ensure the connector remains functional despite external challenges.
By implementing these practices, engineers can maximize the efficiency and lifespan of stamped connectors, even in the harshest conditions.
Stamped connectors have proven their reliability in high-temperature environments through advanced engineering and material science.
For specialized metal stamping solutions, look no further than Partzcore.
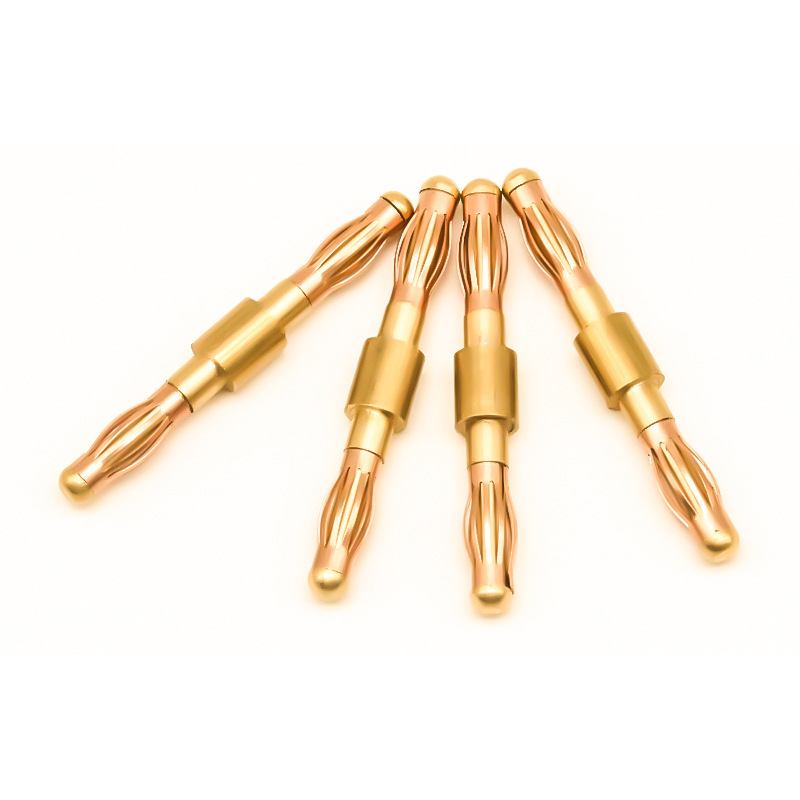
Conclusion
Stamped connectors have evolved into a reliable, cost-effective solution for high-temperature environments.
While challenges like material fatigue and corrosion exist, these can be addressed through careful material selection, routine maintenance, and adherence to best practices.
As technology advances, stamped connectors will continue to play a pivotal role in meeting the demands of modern engineering.