When designing or sourcing LED lighting components, choosing the right material can feel overwhelming.
With aluminum and stainless steel both offering unique strengths, how do you determine which one truly meets your needs for performance, longevity, and cost-efficiency?

To give you a straight answer: aluminum is generally the better choice for most LED lighting components because of its excellent heat dissipation, lightweight nature, and lower overall cost.
However, stainless steel may outperform in harsh environments where durability, impact resistance, or aesthetics are critical.
This article breaks down all the key decision factors — from heat performance to installation ease — so you can confidently select the best material for your LED project.
Now, let’s delve into these in detail.
-
Table Of Contents
-
1. Aluminum vs. Stainless Steel: Which Material Is Truly Best for Your LED Lighting Components?
-
2. Quick Comparison: Aluminum vs. Stainless Steel for LED Components
-
3. Why Does Material Choice Matter in LED Lighting?
-
4. Is It Better to Get Aluminum or Stainless Steel for LED Lighting?
-
5. Heat Dissipation: Why Aluminum Wins in Thermal Management?
-
6. Cost: Upfront and Long-Term Considerations
-
7. Why Aluminum Is So Common in LED Lighting Fixtures?
-
8. What Should Buyers Ask Before Choosing a Material?
-
9. Final Verdict: Which Should You Choose?
-
10. Summary
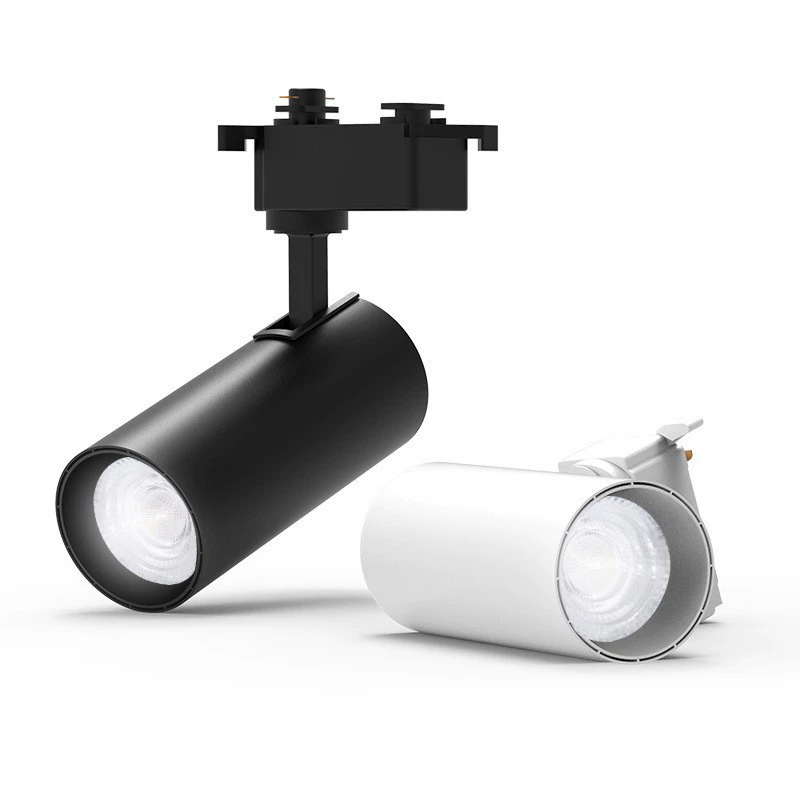
Quick Comparison: Aluminum vs. Stainless Steel for LED Components
Let’s begin with a quick side-by-side summary:
Feature |
|
| ||
Weight | Lightweight (⅓ the weight of stainless steel) | Heavy | ||
Heat Dissipation | Excellent | Poor | ||
Corrosion Resistance | Good (natural oxide layer) | Good (depends on grade) | ||
Strength | Moderate | High | ||
Machinability | Easy to machine | Harder to machine | ||
Cost | Lower | Higher | ||
Best Use | Everyday and outdoor lighting | Industrial, marine, or decorative fixtures |
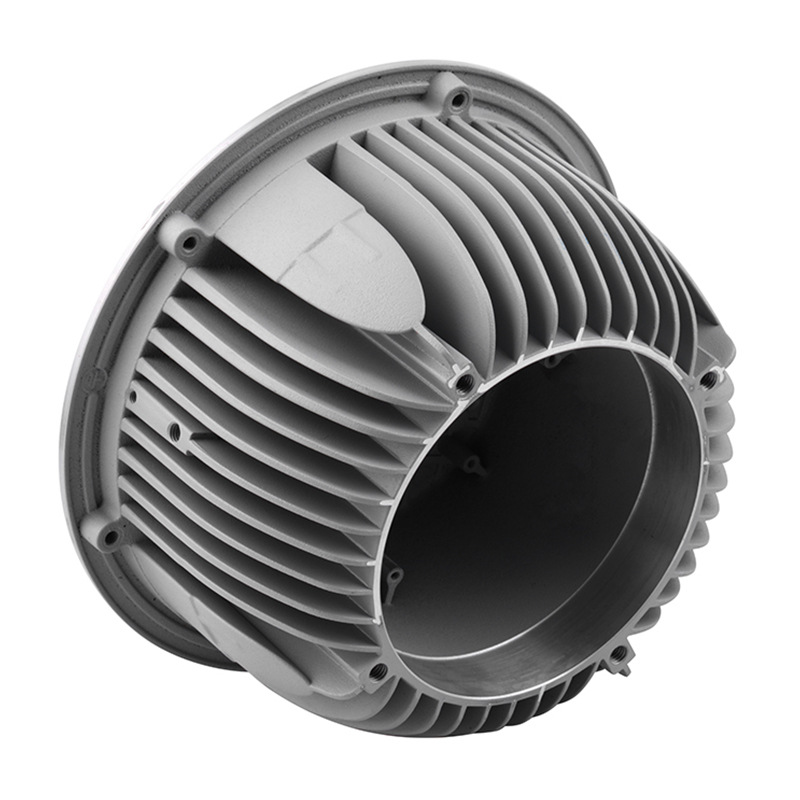
Why Does Material Choice Matter in LED Lighting?
Material selection in LED component design isn’t just a technical decision — it directly impacts performance, installation cost, maintenance, and lifespan.
For engineers and buyers alike, getting this right means balancing durability, thermal performance, budget constraints, and environmental conditions.
Whether you’re designing for mass production or sourcing parts for a one-time project, understanding how material properties align with your application is essential for success — both technically and financially.
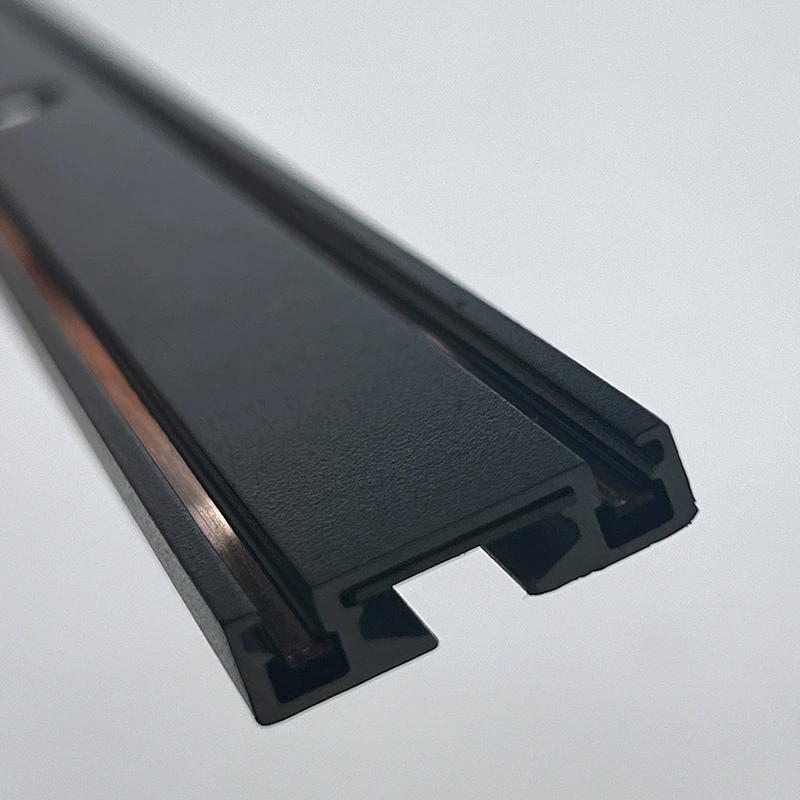
Is It Better to Get Aluminum or Stainless Steel for LED Lighting?
The choice between aluminum and stainless steel depends on various factors such as weight, strength, maintenance, and longevity.
Let’s analyze these factors one by one:
1. Weight & Ease of Installation
• Aluminum is about three times lighter than stainless steel.
• Why does this matter? A lighter material makes installation easier, especially for large-scale lighting setups, streetlights, or ceiling-mounted LED fixtures.
• Stainless steel is significantly heavier, making it less suitable for overhead or portable lighting applications.
Aluminum is the better option if your project requires lightweight, easy-to-handle materials.
2. Strength & Durability
• Stainless steel is stronger than aluminum, offering higher tensile and impact strength.
• In harsh environments, such as industrial or marine applications, stainless steel performs better against physical damage.
• Aluminum is still strong enough for most LED applications but can be more prone to dents or deformation under heavy impact.
If durability and structural integrity are a priority, stainless steel is the better choice.
3. Corrosion Resistance
• Aluminum naturally resists corrosion by forming an oxide layer.
• Stainless steel also resists corrosion, but in high-salinity or chemical environments, some grades may require additional coatings.
• Marine and industrial applications where chemicals or moisture are present may favor stainless steel with corrosion-resistant finishes.
If your application is exposed to harsh outdoor conditions, aluminum is a more maintenance-free option.

Heat Dissipation: Why Aluminum Wins in Thermal Management?
1. Why Heat Dissipation Is Crucial?
LEDs may be energy-efficient, but they still generate heat. Without proper heat management, LED lifespan and brightness suffer.
That’s why materials with high thermal conductivity are essential for heat sinks and housings.
2. Aluminum’s Superior Thermal Conductivity
Aluminum has a thermal conductivity of about 205 W/m·K, compared to stainless steel’s 15 W/m·K.
This means aluminum disperses heat over a wider area more efficiently, preventing LED degradation.
For any component near an LED’s heat source — such as housings or reflectors — aluminum is the clear winner.
Cost: Upfront and Long-Term Considerations
1. Raw Material and Machining Costs
• Aluminum is typically 30–50% cheaper than stainless steel per kilogram.
• It is also faster and easier to machine, which cuts down production time and tool wear.
2. Maintenance and Replacement
While stainless steel might last longer in certain harsh conditions, aluminum’s lower material and maintenance costs make it more budget-friendly overall for most lighting projects.
Cost-Conscious Verdict: Aluminum is ideal for projects where thermal performance and cost control are priorities.
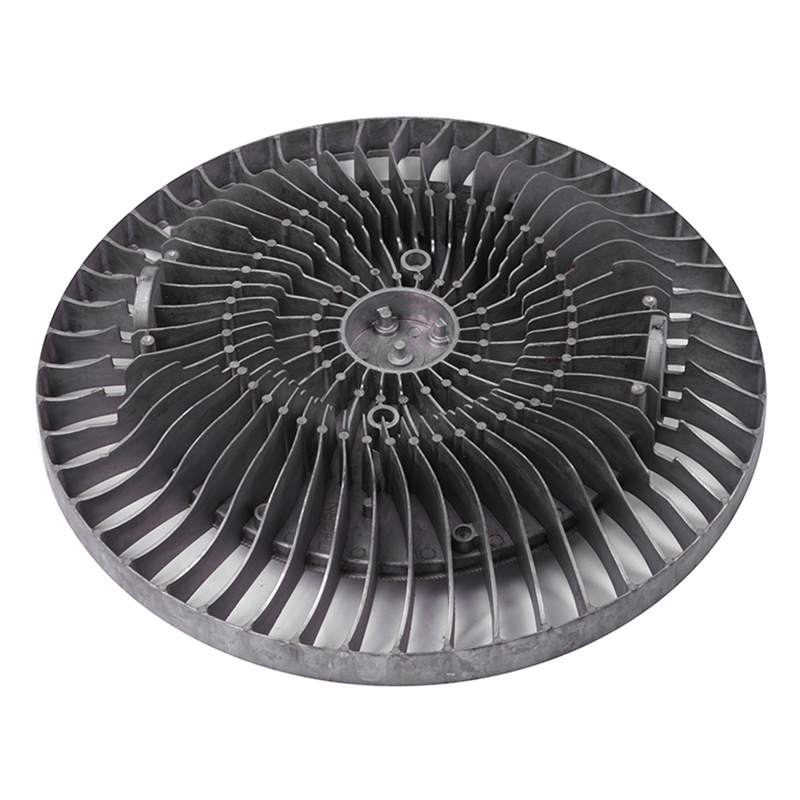
Why Aluminum Is So Common in LED Lighting Fixtures?
There’s a reason why aluminum dominates the LED lighting industry:
• High Reflectivity – Enhances brightness by reflecting more light
• Fast Heat Dissipation – Extends LED lifespan and efficiency
• Formability – Easily extruded, stamped, or milled into complex shapes
• Corrosion Resistance – Withstands outdoor elements with minimal upkeep
In fact, over 90% of LED heat sinks are made from aluminum for these very reasons.
What Should Buyers Ask Before Choosing a Material?
For buyers, especially those sourcing large volumes or customized parts, asking the right questions is critical to avoiding costly mistakes:
Will the lighting fixture be exposed to salt, chemicals, or high humidity?
Is weight a concern for shipping or installation?
Will the fixture face vibration, impact, or wear?
What’s more important: cost savings or extreme durability?
Can the supplier offer surface treatments for additional protection?
Tip: Always request material samples or small production runs to validate real-world performance before committing to large orders.
Final Verdict: Which Should You Choose?
There’s no one-size-fits-all answer, but here’s a simplified decision tree:
Project Priority | Recommended Material |
Heat Management & Lightweight | Aluminum |
Impact Resistance & Strength | Stainless Steel |
Budget-Conscious Production | Aluminum |
Harsh Industrial Environments | Stainless Steel |
High-Volume Outdoor Fixtures | Aluminum |
Premium Architectural Finish | Stainless Steel |
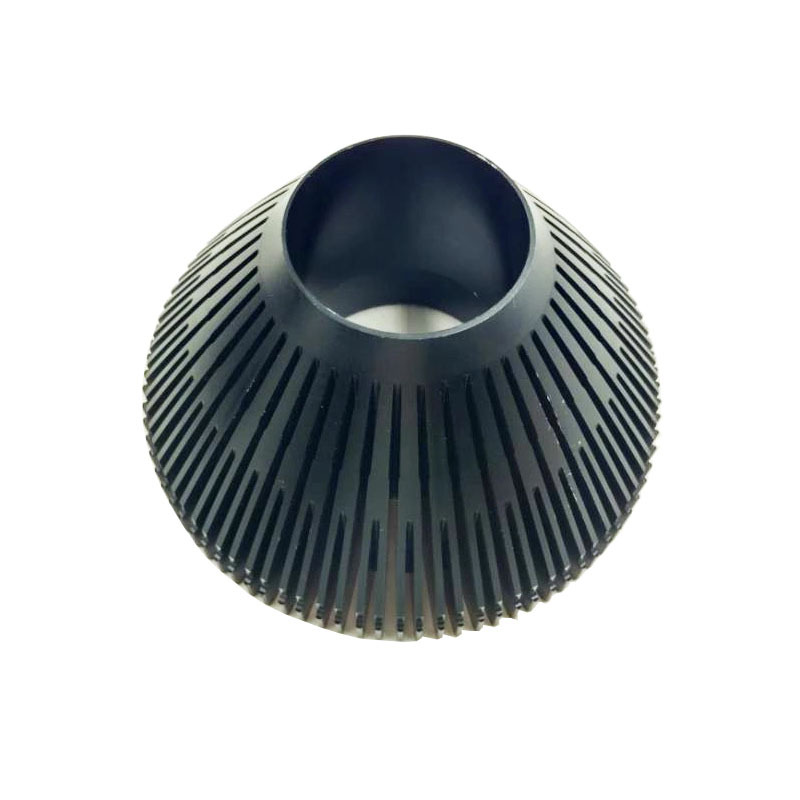
Conclusion
Choosing between aluminum and stainless steel for your LED lighting components comes down to understanding your application’s demands and balancing performance with practicality.
For most LED lighting components, aluminum is the preferred material due to its superior heat dissipation, corrosion resistance, and lower cost.
However, for applications in harsh environments or where extreme durability is needed, stainless steel may be worth the investment.
Need help selecting or machining the right material for your LED lighting project?
Contact the professional team today for expert advice!