Understanding the tolerance guidelines for aluminum extrusion parts is crucial for engineers and procurement managers to ensure high-quality production and performance.
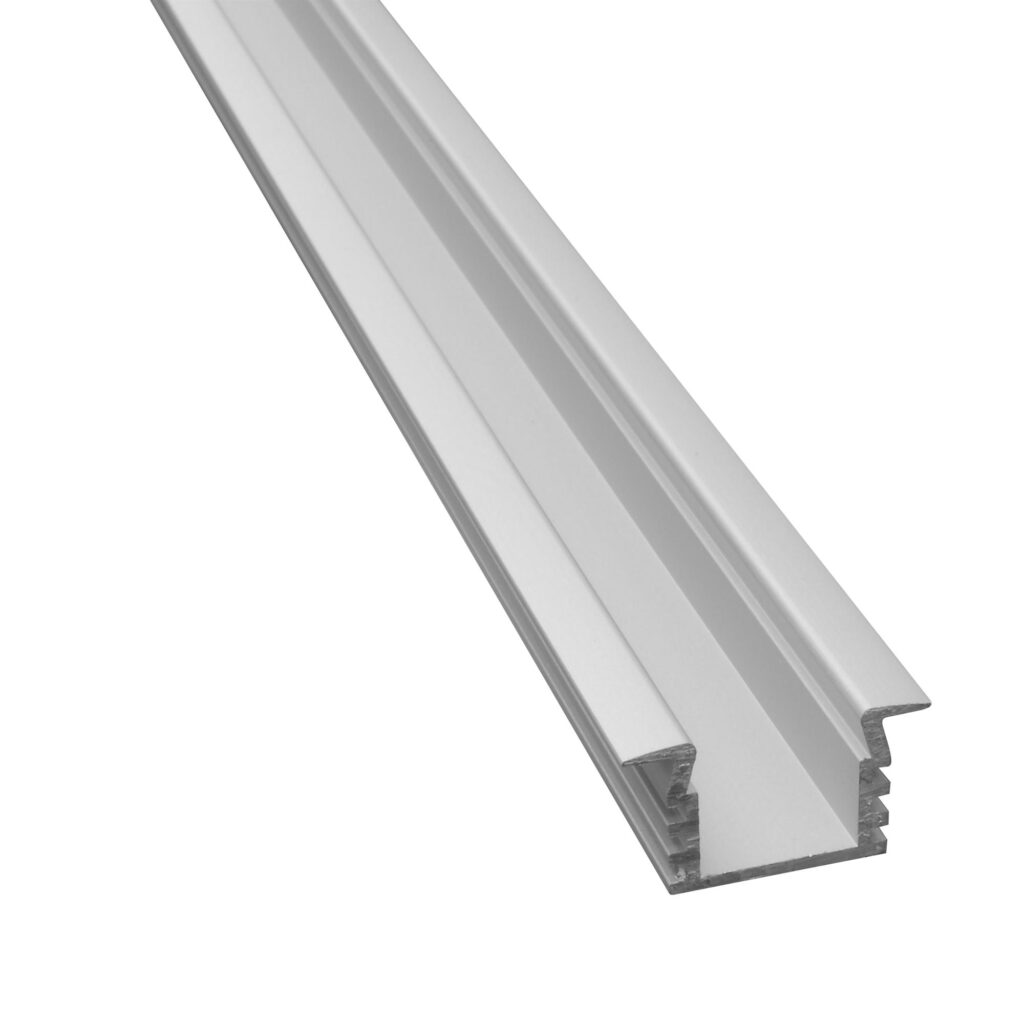
Aluminum extrusion parts tolerance defines the allowable limits of variation in the dimensions and shape of extruded parts. These guidelines ensure that parts fit and function correctly, maintaining the integrity and efficiency of the final product.
In this article, we offer general guidelines and specific recommendations from various manufacturers, providing a comprehensive overview for those involved in the design and procurement of aluminum extrusions.
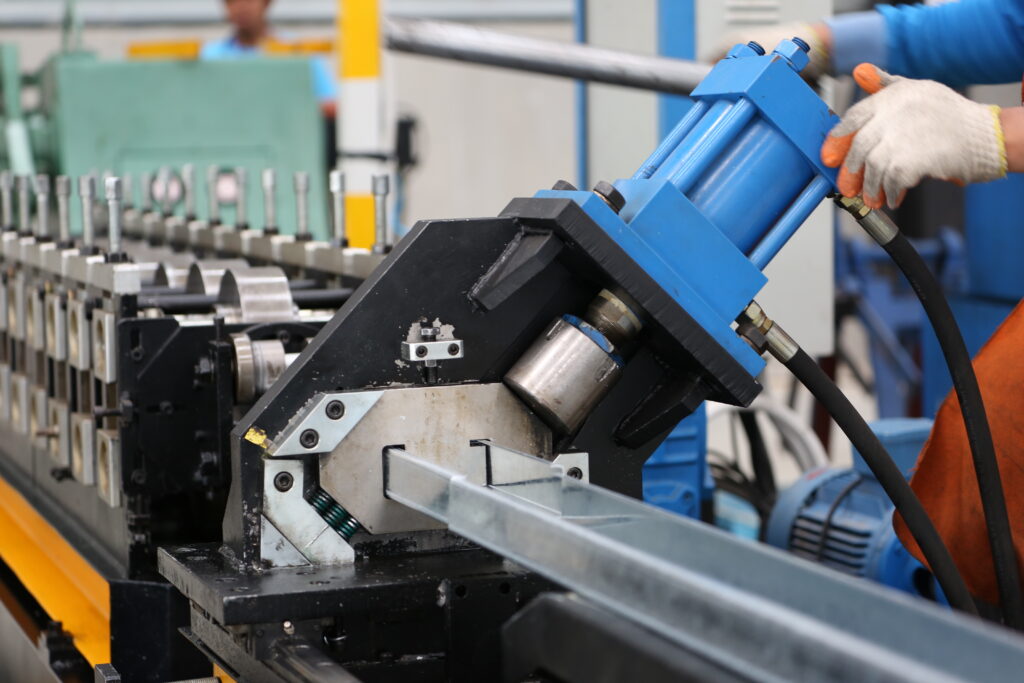
General Guidelines for Aluminum Extrusion Tolerances
Aluminum extrusions must adhere to precise tolerances to ensure proper fit and function. Here are the general guidelines that are typically followed in the industry:
• Linear Cross Section Dimensions: ± 0.008″ per inch of the dimension. This tolerance ensures that the cross-sectional dimensions of the extruded part remain within acceptable limits, allowing for consistent fit and performance across different applications.
• Wall Thickness: ± 10% of the specified dimension. This tolerance accounts for variations in wall thickness, which can impact the strength and weight of the extruded part.
• Twist: ½ degree per foot of length. Twist tolerance ensures that the extruded part remains straight and true, preventing issues during assembly and use.
• Straightness: 0.0125″ per foot of length. This tolerance ensures that the extruded part does not deviate from a straight line, which is crucial for applications requiring precise alignment.
These general guidelines help maintain consistency and quality across various applications, ensuring that extruded parts meet the necessary specifications for their intended use.
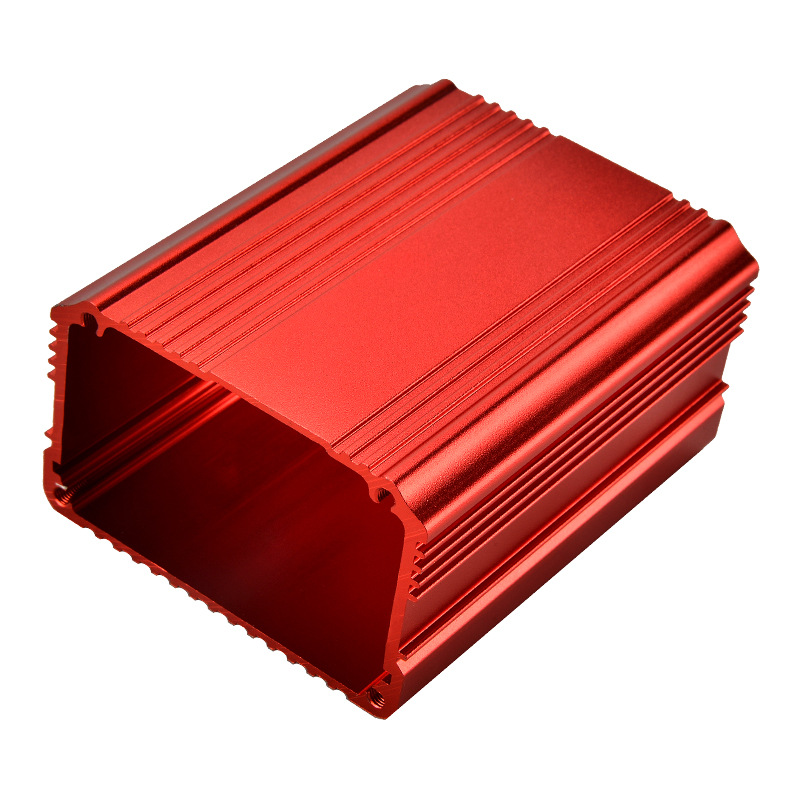
Common Issues with Tolerances
According to our production experience, despite thorough preparation, several common issues will arise during the production and use of aluminum extrusions. Understanding these issues helps in implementing effective strategies to mitigate their impact:
1. Material Variability
Material Variability: Aluminum alloys can exhibit different properties based on their composition and processing history. Variations in material properties can affect the consistency of the extrusion process and the final dimensions of the parts.
Solution: Implementing strict material quality control measures and selecting appropriate alloys for specific applications can help minimize the impact of material variability on extrusion tolerances.
2. Profile Complexity
Profile Complexity: More complex profiles may have tighter tolerances, making them harder to produce consistently. Intricate designs can lead to challenges in maintaining dimensional accuracy throughout the extrusion process.
Solution: Utilizing advanced simulation and modeling tools during the design phase can aid in predicting and addressing potential tolerance issues.
3. Temperature Variations
Temperature Variations: Aluminum’s thermal expansion can affect dimensional accuracy during production and in-service conditions. Temperature fluctuations can lead to deviations from specified tolerances, impacting the fit and function of the parts.
Solution: Control the extrusion process environment and account for thermal expansion in the design phase. Implement proper cooling and heat treatment processes to enhance dimensional stability.
4. Tool Wear
Tool Wear: Extrusion dies wear over time, potentially leading to deviations from specified tolerances. Worn tools can produce parts with inconsistent dimensions and surface finish, affecting the overall quality.
Solution: Regular maintenance and replacement of extrusion dies are essential. Monitor tool wear and implement predictive maintenance strategies to minimize tool degradation’s impact on extrusion tolerances.
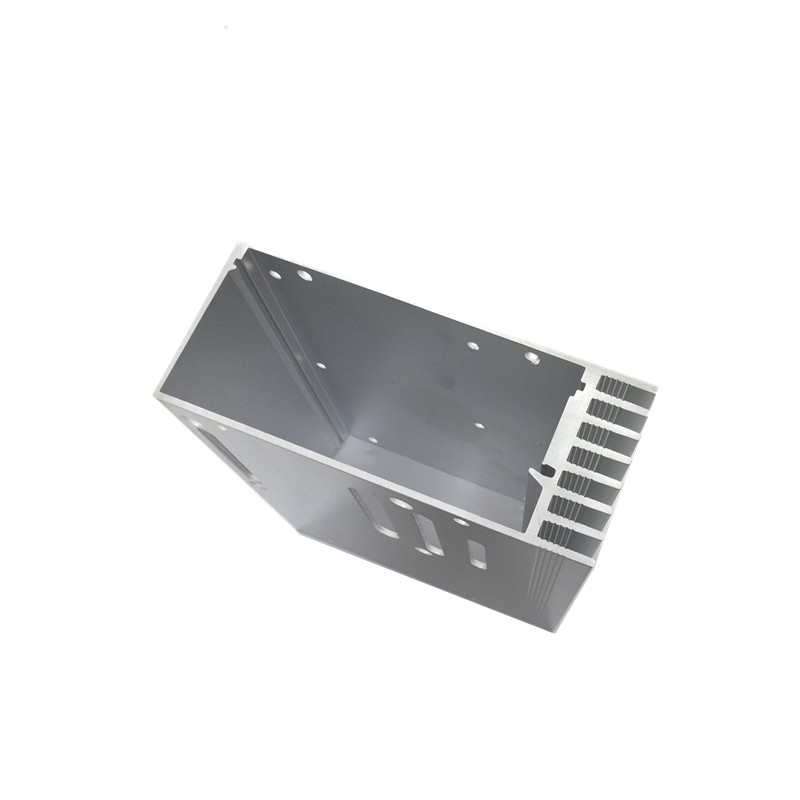
Design Considerations for Aluminum Extrusions
When designing aluminum extrusions, it is essential to consider the impact of tolerances on the final product. Here are some design considerations to keep in mind:
1. Critical Dimensions
Critical Dimensions: Identifying and prioritizing critical dimensions that directly impact the fit, function, and performance of the extruded parts is crucial. These dimensions should have tighter tolerances to ensure precise control.
Solution: Work closely with the extrusion manufacturer to establish achievable tolerances for critical dimensions.
2. Geometric Dimensioning and Tolerancing (GD&T)
Geometric Dimensioning and Tolerancing (GD&T): GD&T provides a standardized method for specifying and controlling the geometric characteristics of extruded parts. It allows for precise control over form, orientation, and location, ensuring that parts fit together correctly.
Solution: Implement GD&T in the design phase to communicate necessary tolerances and requirements to the extrusion manufacturer. Use advanced CAD and simulation tools to accurately define and verify GD&T specifications.
3. Surface Finish
Surface Finish: The surface finish of extruded parts can impact their appearance, performance, and suitability for specific applications. Tolerances related to surface finish should be specified to ensure consistent quality.
Solution: Collaborate with the extrusion manufacturer to define achievable surface finish tolerances.
4. Assembly Considerations
Assembly Considerations: Tolerances can affect the ease and reliability of assembling extruded parts. Ensuring that parts fit together correctly and consistently is crucial for efficient assembly processes.
Solution: Consider assembly requirements during the design phase and specify appropriate tolerances. Conduct assembly simulations and prototypes to identify and resolve potential tolerance issues.
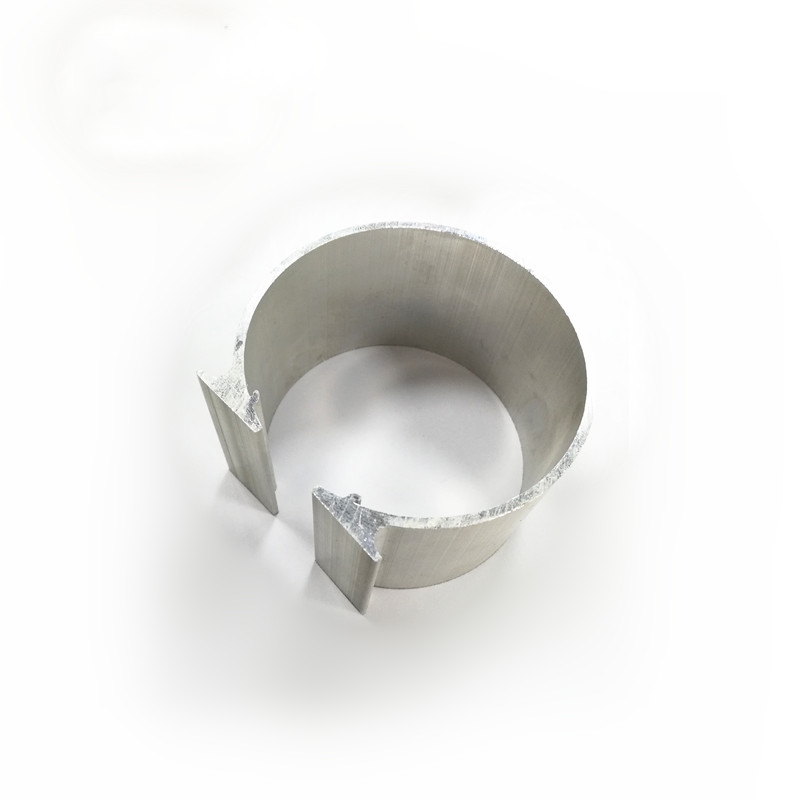
Summary
Adhering to tolerance guidelines is critical for producing high-quality aluminum extrusion parts. By understanding general guidelines, specific manufacturer recommendations, and common issues, engineers and procurement managers can ensure their projects meet the necessary standards and perform reliably.
Implementing effective design and quality control measures can help mitigate tolerance-related challenges, ensuring the success of aluminum extrusion projects.
Understanding and implementing these tolerance guidelines will help in achieving optimal performance and reliability in aluminum extrusion projects.
By maintaining a focus on quality and precision, engineers and procurement managers can ensure that their aluminum extrusions meet the necessary specifications and deliver consistent performance in their applications.