Using advanced techniques and technologies to enhance the quality of aluminum die casting parts is crucial for manufacturing engineers and quality control managers.
By understanding common quality issues and implementing best practices, it’s possible to improve product reliability and performance significantly.
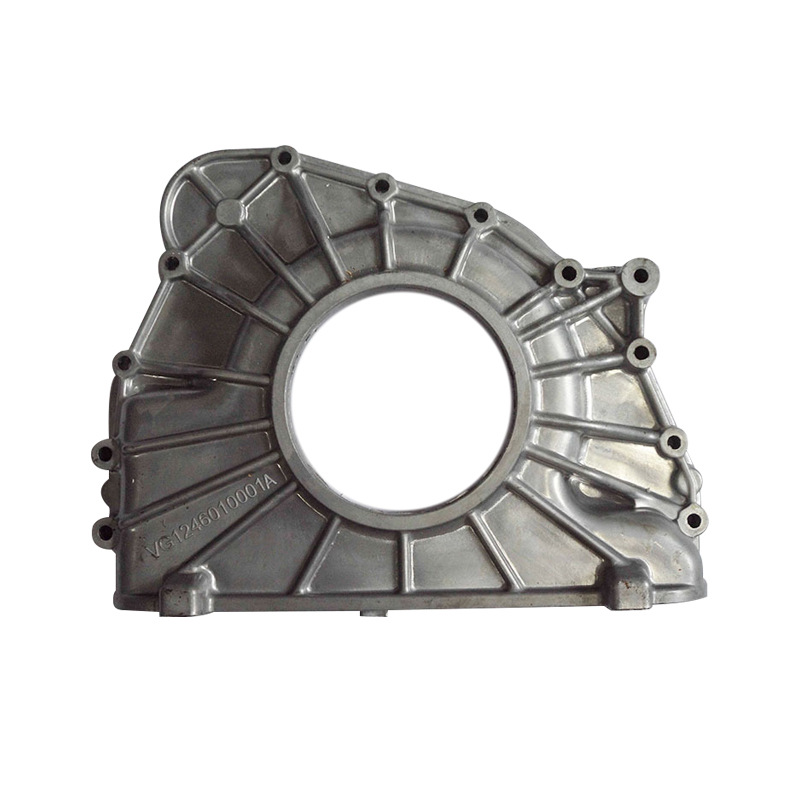
To improve the quality of aluminum die casting parts, use ribs and gussets to increase part strength without significantly adding to the weight or wall thickness.
Consider the flow of molten aluminum and gate locations to ensure complete cavity fill and minimize air entrapment.
This article covers the typical quality issues, best practices, and emerging technologies that can help in producing high-quality aluminum die casting parts. Now, let’s explore them.
-
Table Of Contents
-
1. How to Improve Aluminum Die Casting Part Quality?
-
2. What are Common Quality Issues in Aluminum Die Casting?
-
3. How to Reduce Porosity in Aluminum Casting?
-
4. What are the Best Practices for Aluminum Die Casting Design?
-
5. Additional Tips for Improving Die Casting Quality
-
6. New Technologies in Aluminum Die Casting
-
7. Summary
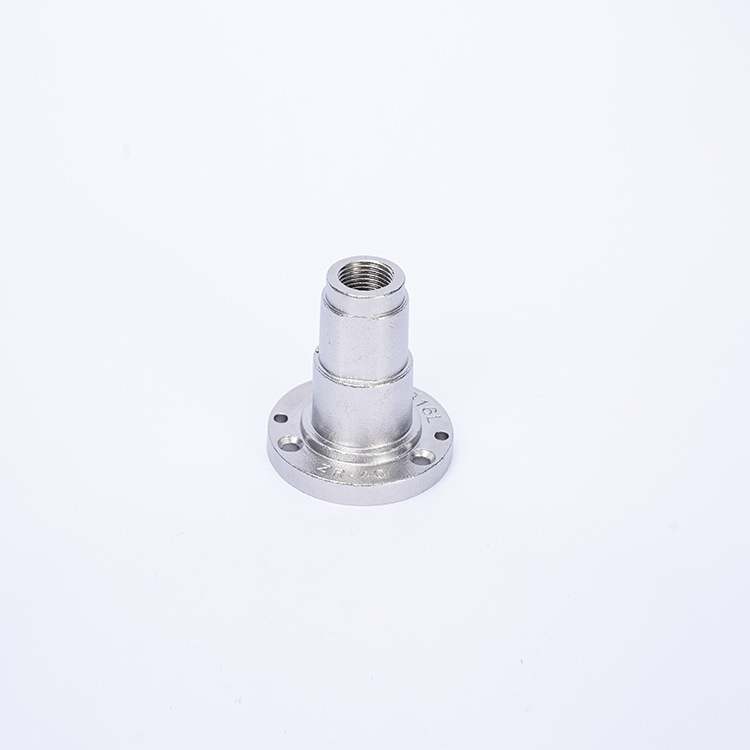
What are Common Quality Issues in Aluminum Die Casting?
Aluminum die casting, while a highly efficient manufacturing process, often faces several quality issues. Understanding these issues is the first step towards mitigating them:
1. Porosity
Porosity occurs due to trapped air or gases within the casting. It can weaken the structure and lead to leaks in pressure-containing parts. Porosity can manifest as either gas porosity, caused by trapped air during the casting process, or shrinkage porosity, which happens as the metal solidifies and contracts.
2. Incomplete Filling
This happens when the molten aluminum doesn’t completely fill the mold cavity, leading to parts with missing sections or weak spots. Factors contributing to incomplete filling include inadequate pouring temperature, improper gating system design, and insufficient pressure during the casting process.
3. Surface Defects
Surface defects such as cold shuts, flow lines, and rough surfaces can result from improper mold temperatures or poor gating design. Cold shuts occur when two streams of molten metal meet but do not fuse properly, while flow lines are marks left by the metal flow on the surface of the casting.
4. Dimensional Inaccuracies
Variations in part dimensions can occur due to thermal expansion, improper mold design, or inadequate cooling rates. These inaccuracies can lead to problems in assembly and function, necessitating costly rework or rejection of the parts.
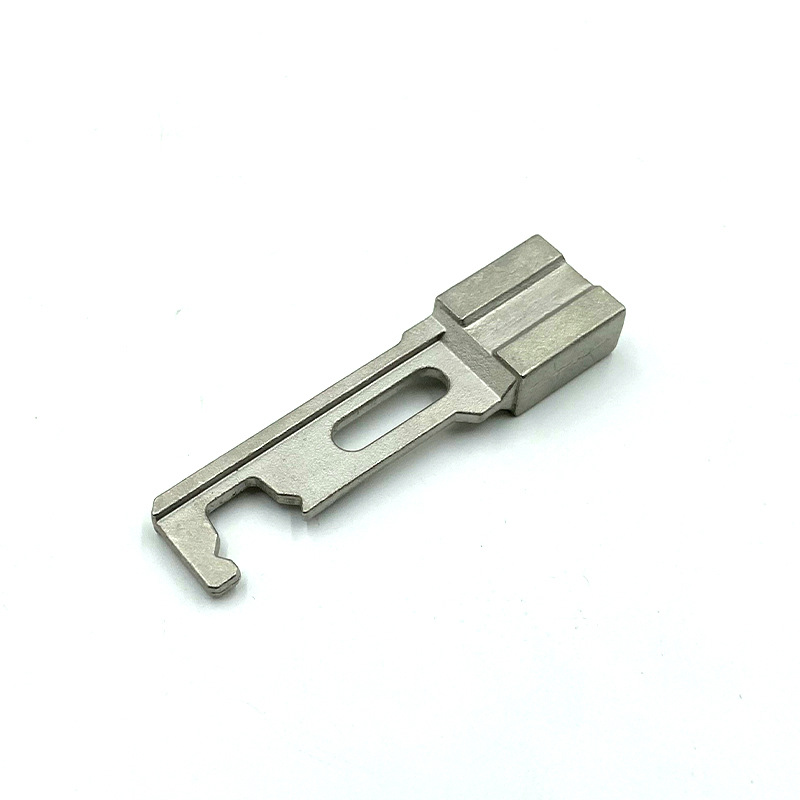
How to Reduce Porosity in Aluminum Casting?
Reducing porosity involves a combination of good design practices and process improvements:
1. Good Mold Design
Ensuring proper venting and gating in the mold design can help in the efficient evacuation of air and gases. Properly designed vents and gates allow trapped gases to escape, reducing the risk of porosity.
2. Introducing Nitrogen
Introducing nitrogen into the aluminum before pouring can help in reducing gas porosity by displacing dissolved gases. This process, known as degassing, involves bubbling nitrogen gas through the molten aluminum to remove hydrogen and other dissolved gases.
3. HiPping (Hot Isostatic Pressing)
HiPping can eliminate small amounts of internal porosity by applying high pressure and temperature to the casting, thus improving its density and mechanical properties.
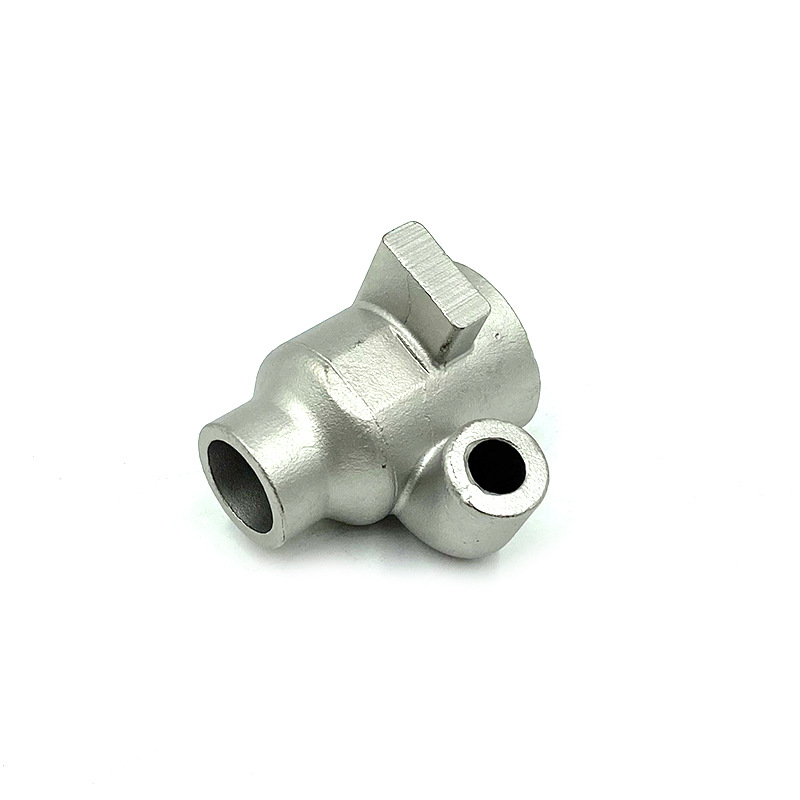
What are the Best Practices for Aluminum Die Casting Design?
Implementing design best practices can significantly improve the quality of aluminum die casting parts:
1. Use of Ribs and Gussets
These structural elements increase part strength without adding excessive weight. Ribs and gussets provide additional support and rigidity, preventing deformation and enhancing the overall strength of the part.
2. Optimal Gate Locations
Proper placement of gates ensures complete cavity fill and reduces the risk of air entrapment. Gates should be designed to allow smooth and uninterrupted flow of molten metal, minimizing turbulence and ensuring a uniform fill.
3. Ensuring Complete Cavity Fill
Designing for smooth and continuous flow of molten aluminum minimizes defects and improves overall part quality. The use of simulation software can help in optimizing the flow patterns and identifying potential issues before actual production.
4. Wall Thickness Management
Maintaining uniform wall thickness in the design reduces the risk of thermal stress and warping. Thin walls can cool quickly, leading to internal stresses, while thick walls can result in longer cooling times and potential shrinkage defects.
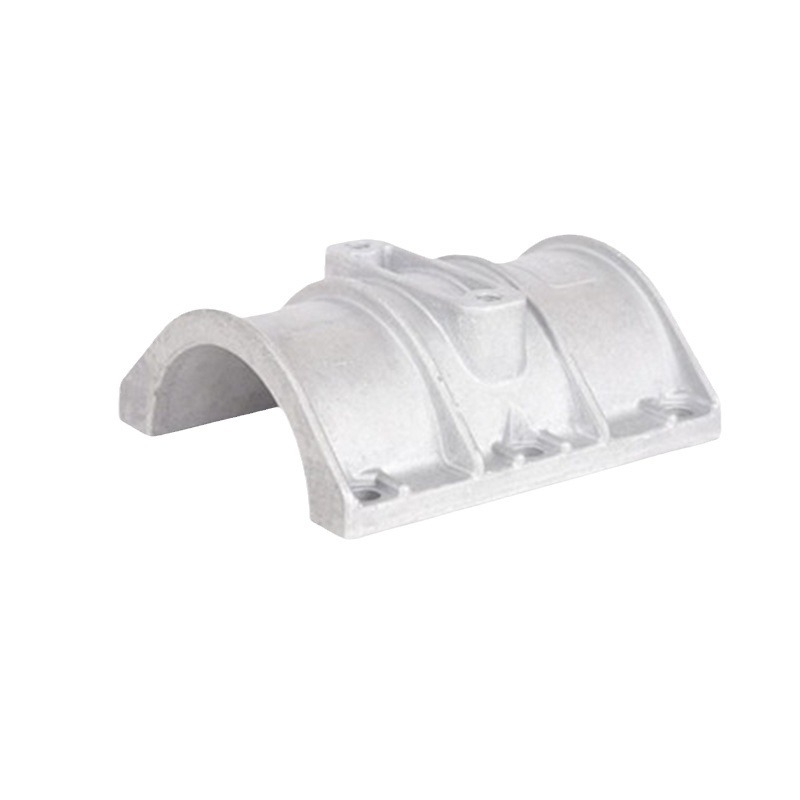
Additional Tips for Improving Die Casting Quality
1. Regular Mold Maintenance
Regular inspection and maintenance of molds prevent defects and extend mold life. Maintenance activities include cleaning, repairing, and refurbishing the molds to ensure they are in optimal condition for casting.
2. Real-time Monitoring
Implementing real-time monitoring systems helps in identifying and addressing issues during the casting process. Sensors and data acquisition systems can provide real-time feedback on critical parameters such as temperature, pressure, and metal flow, enabling proactive quality control.
3. Continuous Training for Personnel
Ongoing training ensures that the workforce is skilled in the latest techniques and technologies, promoting overall process improvement. Training programs should cover best practices in die casting, quality control, and the use of new technologies to keep the personnel up-to-date and proficient.
4. Lean Manufacturing Practices
Adopting lean manufacturing principles can improve efficiency and reduce waste in the die casting process. Techniques such as value stream mapping, 5S, and Kaizen can help in identifying and eliminating non-value-added activities, improving productivity and quality.
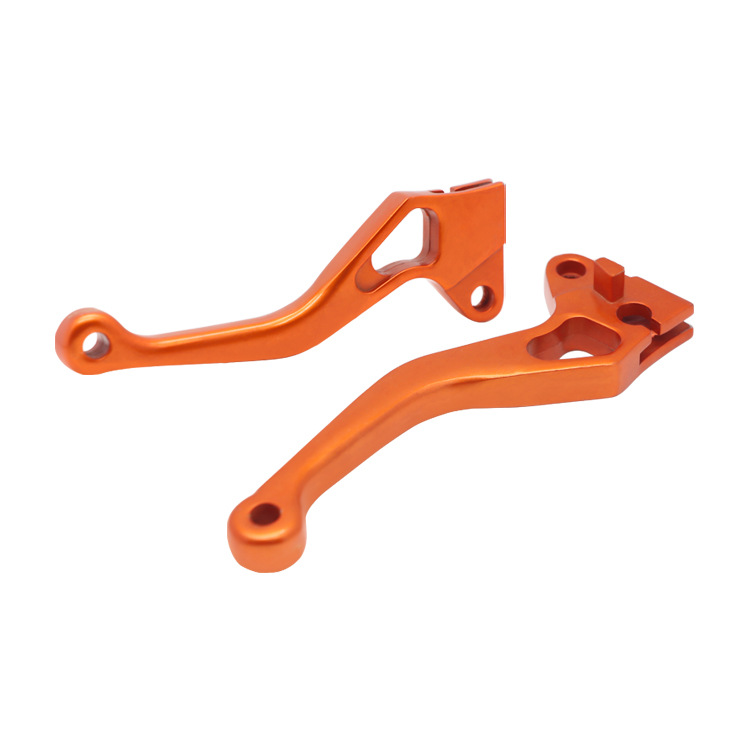
New Technologies in Aluminum Die Casting
Emerging technologies are revolutionizing the aluminum die casting process:
1. Advances in Die Coatings
Coatings such as titanium nitride (TiN) and chromium nitride (CrN) provide a hard, wear-resistant surface that extends the life of the die and improves the surface finish of the cast parts.
2. Use of Simulation Software
Software like MAGMASOFT and ProCAST can simulate the flow of molten metal, solidification, and cooling, helping in optimizing the design and process parameters.
3. Automated Quality Control
Technologies such as X-ray inspection, ultrasonic testing, and 3D scanning provide detailed insights into the integrity of the cast parts, allowing for early detection of defects and continuous quality improvement.

Summary:
By implementing these strategies and staying updated with the latest technologies, the quality of aluminum die casting parts can be significantly improved.
Regular assessments and adopting best practices ensure superior performance and reliability in the final products. Embracing new technologies and continuous improvement initiatives will position manufacturers to meet the increasing demands for high-quality aluminum die casting parts in various industries.