In the world of manufacturing, the question of whether aluminum die casting requires post finishing often arises.
While the initial casting process produces high-quality parts, various factors necessitate additional finishing steps to meet specific durability, protection, and cosmetic requirements, which are crucial for ensuring optimal product performance and longevity.
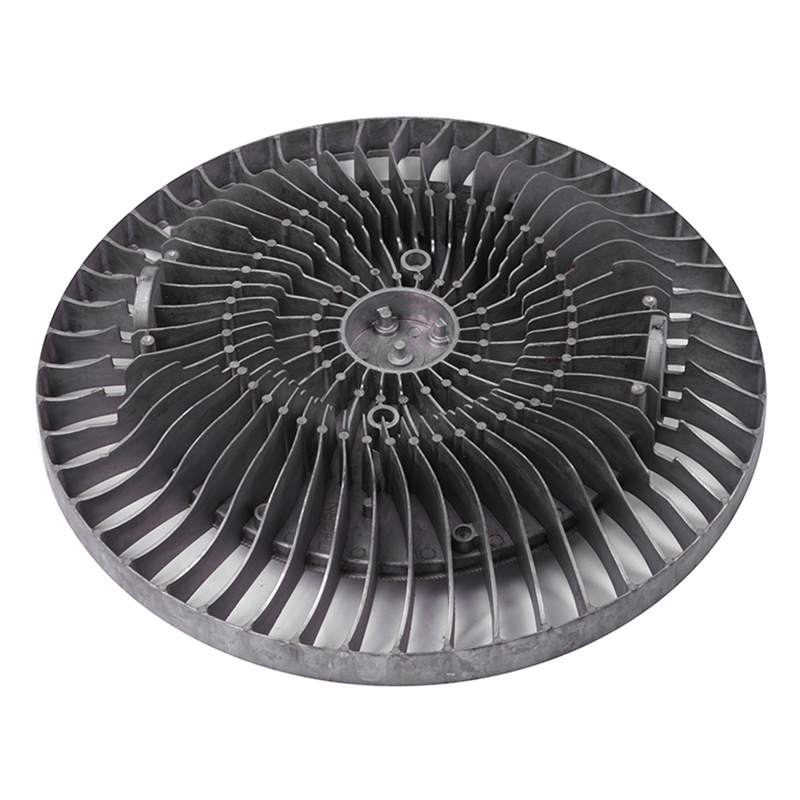
Yes, in most cases, aluminum die-casting requires post finishing.
Depending on the specifications on durability, protection, and cosmetic appearance, most aluminum, magnesium, and zinc die castings will receive one to three post-casting finishing steps: deburring, conversion and/or combined conversion functional coating, and a final surface finish coating.
If you want to get more information about post finishing in aluminum die casting, let’s dive deeper into the details of these essential post-finishing processes and their significance.
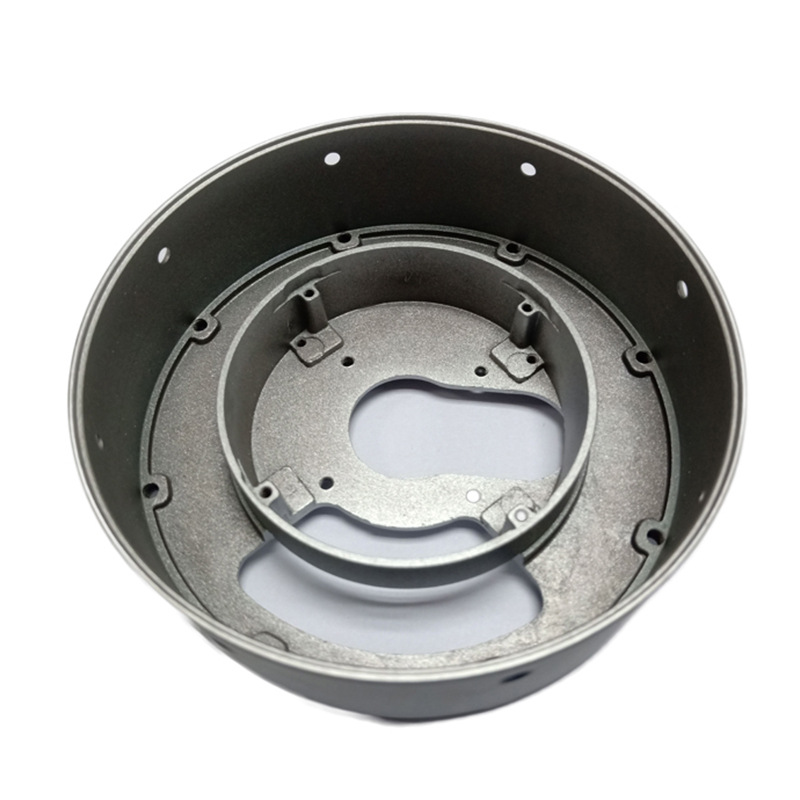
What is the Post Process of Aluminum?
Post-processing aluminum involves several key methods to enhance its properties and appearance:
Anodizing
Anodizing increases the corrosion resistance and surface hardness of aluminum parts. This electrochemical process involves immersing the aluminum part in an acid electrolyte bath and passing an electric current through it. The result is a durable and protective oxide layer that can be dyed in various colors for aesthetic purposes.
Painting and Powder Coating
Painting and powder coating provide decorative and protective finishes for aluminum parts. These processes involve applying a layer of paint or powder to the surface, which is then cured to form a hard, durable coating.
Brushing and Polishing
Brushing and polishing improve the aesthetic appeal of aluminum parts by creating a smooth, shiny surface. Brushing involves using abrasive brushes to create a uniform, textured finish, while polishing uses finer abrasives to produce a high-gloss shine.
Bead Blasting
Bead blasting is a finishing process that uses high-pressure air to blast small beads at the surface of the aluminum part. This creates a uniform matte or textured finish, which can be used for both aesthetic and functional purposes. Bead blasting is particularly useful for removing surface imperfections and preparing the part for further finishing processes.
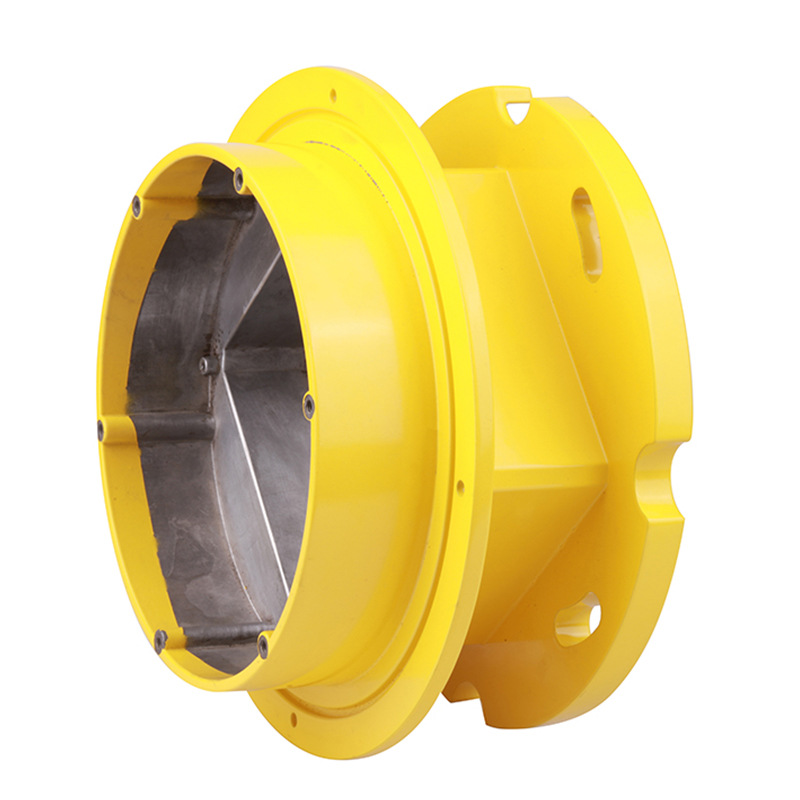
Chemical Etching
Chemical etching creates detailed patterns or textures on the surface of aluminum parts. This process involves applying a resist to the surface of the part and then immersing it in a chemical solution that etches away the exposed areas. Chemical etching is used for decorative purposes and to create functional textures on the surface of the part.
Passivation
Passivation removes surface contaminants from aluminum parts to improve their corrosion resistance. This process involves immersing the part in a chemical bath that removes impurities and forms a protective oxide layer on the surface. Passivation is commonly used for parts that will be exposed to harsh environments.
Electroplating
Electroplating adds a layer of metal coating to aluminum parts to enhance their durability and appearance. This process involves immersing the part in an electrolyte solution and passing an electric current through it, causing metal ions to deposit onto the surface. Electroplating can provide additional protection against corrosion and wear, as well as improve the aesthetic appeal of the part.
Vibratory Finishing
Vibratory finishing uses a vibrating machine and abrasive media to deburr and polish the surface of the part. This process can create a smooth, polished finish and is often used for parts that require a high level of aesthetic appeal.
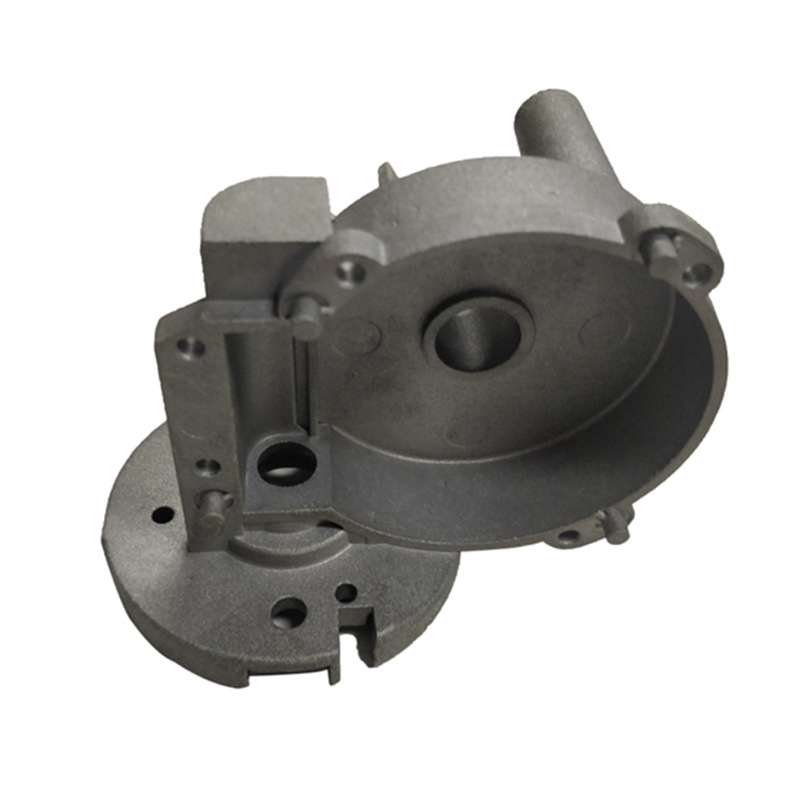
Common Standards for Surface Roughness
There are several standards for surface roughness that manufacturers must adhere to, including ISO 1302 and ASME B46.1.
These standards provide guidelines for measuring and specifying surface roughness, ensuring that parts meet the required specifications for their intended applications.
By following these standards, manufacturers can ensure that their parts perform well and meet the expectations of their customers.
Significance of Post-Finishing in Aluminum Die Casting
The post-finishing processes in aluminum die casting are vital for several reasons.
Each step is carefully designed to enhance the quality, functionality, and appearance of the final product. Let’s explore the significance of each process in detail:
1. Deburring
Deburring is the initial post-finishing step where excess material, or burrs, is removed from the cast part. This process is crucial for several reasons:
Safety: Burrs can be sharp and hazardous to handling. Removing them ensures the safety of workers and end-users.
Fit and Assembly: Burrs can interfere with the assembly process and the proper fitting of parts. Deburring ensures that components fit together seamlessly.
Aesthetic Appeal: Removing burrs enhances the visual appearance of the part, making it more attractive and suitable for consumer products.
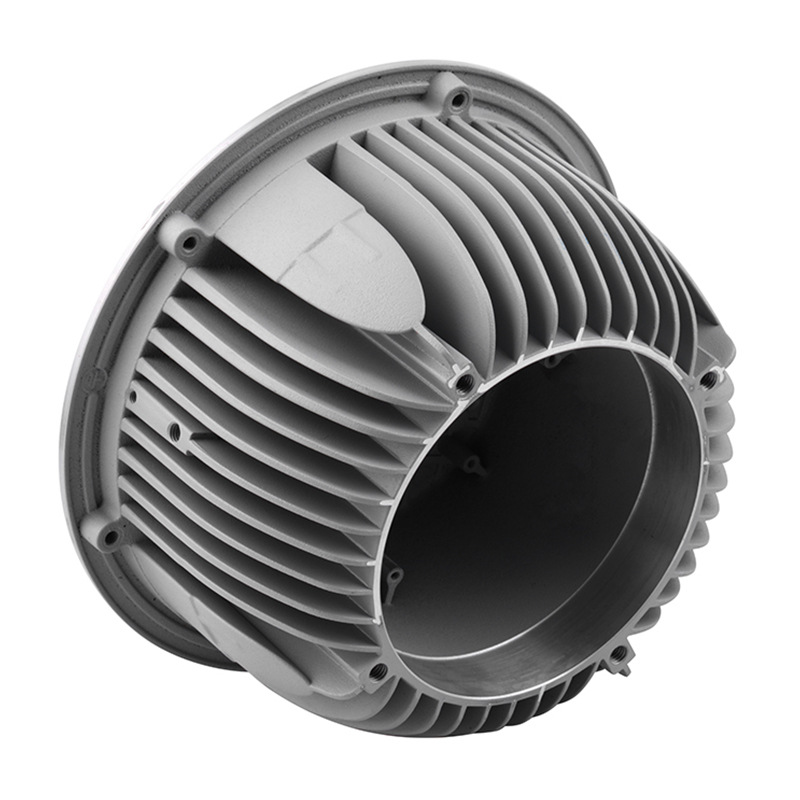
2. Conversion Coating
Conversion coating involves treating the surface of the cast part to enhance its properties. This can include processes like anodizing or applying a phosphate or chromate coating. The benefits include:
Corrosion Resistance: Conversion coatings provide a protective layer that prevents oxidation and corrosion, extending the lifespan of the part.
Adhesion: These coatings improve the adhesion of subsequent layers of paint or other finishes, ensuring they stay intact and do not peel off.
Electrical Conductivity: In some cases, conversion coatings can improve the electrical conductivity of the part, which is essential for certain applications.
3. Surface Finish Coating
The final surface finish coating is applied to enhance both the functionality and appearance of the cast part. This can involve painting, powder coating, or applying a specialized finish. The significance of this step includes:
Aesthetic Enhancement: Surface finish coatings can be tailored to provide a wide range of colors and textures, improving the visual appeal of the product.
Protection: Coatings protect the part from environmental factors, such as UV radiation, moisture, and chemicals, ensuring durability and longevity.
Functionality: In some cases, surface coatings can provide additional functionalities, such as wear resistance, non-stick properties, or electrical insulation.
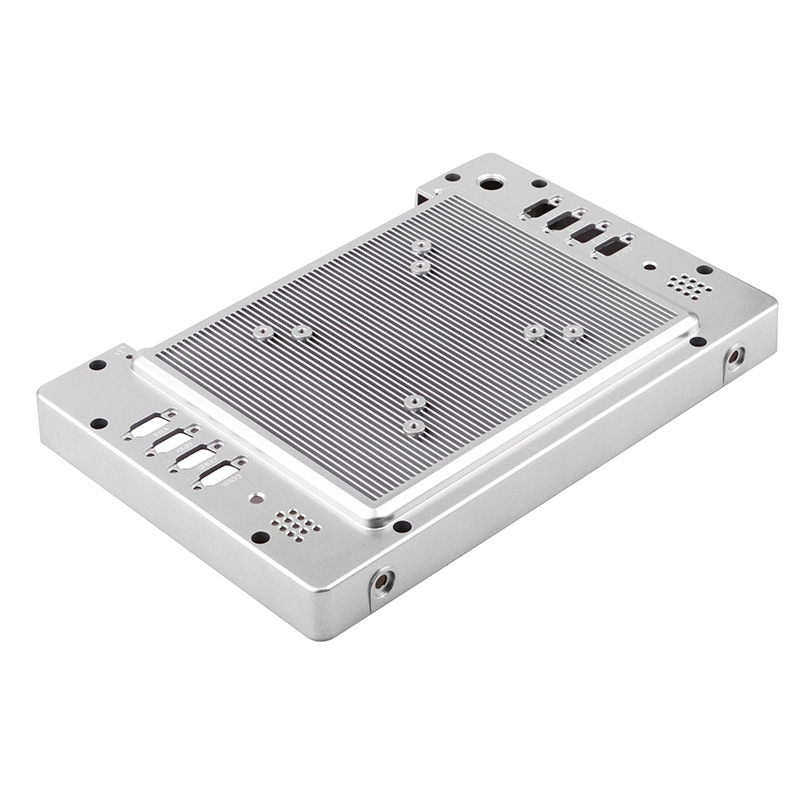
Summary:
In conclusion, aluminum die casting often requires post finishing to meet specific durability, protection, and cosmetic requirements.
Processes like deburring, conversion coating, and surface finishing are essential for achieving high-quality parts.
By implementing these finishing steps, the products are ensured to meet the high standards of performance and appearance.
Whether it’s through anodizing, painting, brushing, or any other post-finishing process, the goal is always to enhance the functionality and aesthetics of the die cast parts, ensuring they perform well in their intended applications.