Brass, an alloy of copper and zinc, has been a cornerstone of the manufacturing industry for centuries. The proportions of copper and zinc can vary, leading to a wide range of brass types with differing properties.
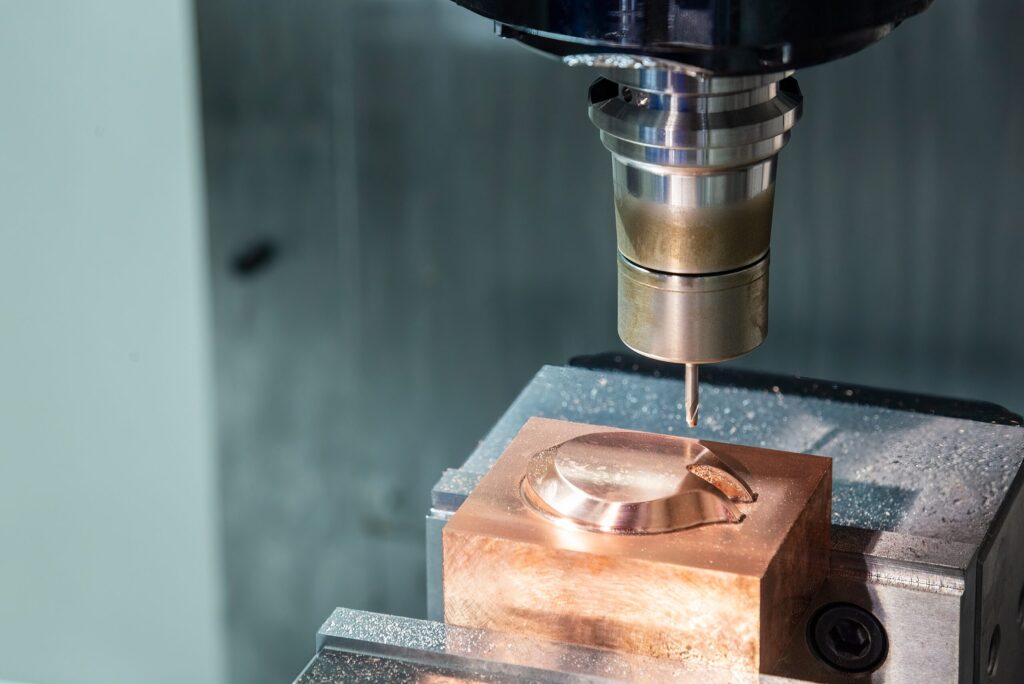
This variability makes brass a versatile material used in numerous applications. Brass is known for its excellent workability, machinability, and antibacterial and anti-biofouling characteristics.
Its unique properties make it an ideal material for various applications, from intricate decorative pieces to robust industrial components.
Next, we will explore several aspects, including the components, types, properties, manufacturing process, and expected uses of brass, to help you understand brass as a manufacturing material.
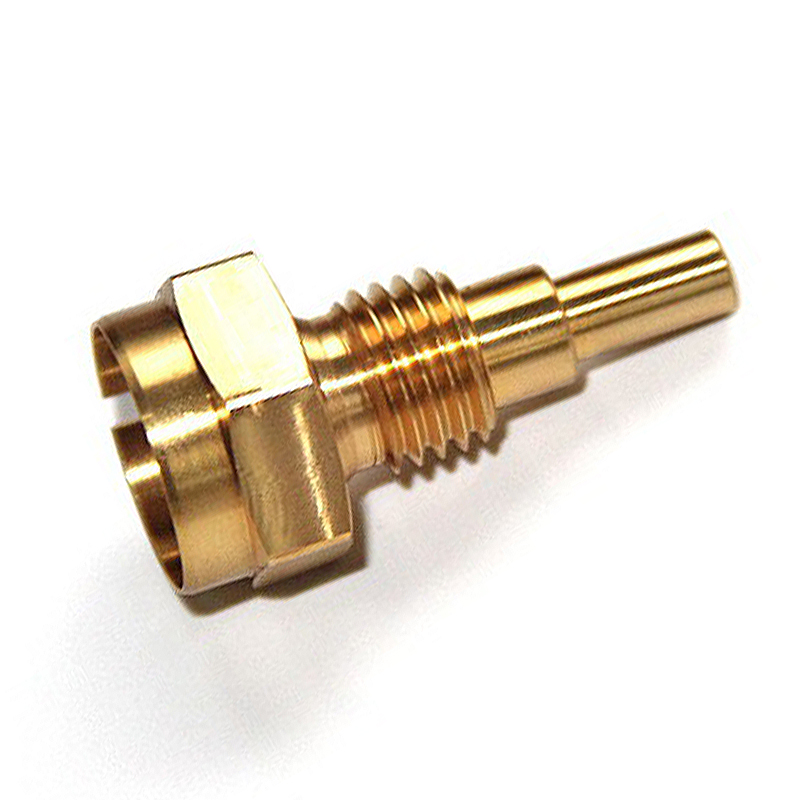
What Are the Components of Brass?
Brass typically consists of copper and zinc in varying proportions. Some types of brass also contain small amounts of other elements such as lead, tin, iron, aluminum, silicon, and manganese to enhance specific properties.
Copper: Copper is the primary component of brass, providing excellent electrical and thermal conductivity and good corrosion resistance.
Zinc: Added to copper to create brass, zinc increases strength and ductility, allowing the alloy to be easily formed and worked.
Lead: Often added in small amounts to improve machinability, making the alloy more manageable to cut and shape into intricate designs.
Tin: Sometimes included to enhance corrosion resistance, particularly in marine environments.
Iron: Small quantities can increase strength and hardness.
Aluminum and Silicon: These elements can improve the strength and durability of brass, making it more resistant to wear and tear.
What Are the Different Types of Brass?
Alpha Brass: Contains less than 37% zinc and is known for its excellent cold-working properties, which are used in applications requiring high corrosion resistance and ductility.
Beta Brass: Contains between 37% and 45% zinc, offering good hot-working properties but less ductility.
Alpha-Beta Brass (Duplex Brass): Contains between 35% and 45% zinc, combining properties of both alpha and beta brasses. This type of brass is versatile and used in a wide range of applications.
Lead Brass: Contains small amounts of lead, which enhances machinability. It is commonly used in applications requiring precise machining, such as gears and valve components.
High Brass: Contains more than 45% zinc, offering high strength and good corrosion resistance.
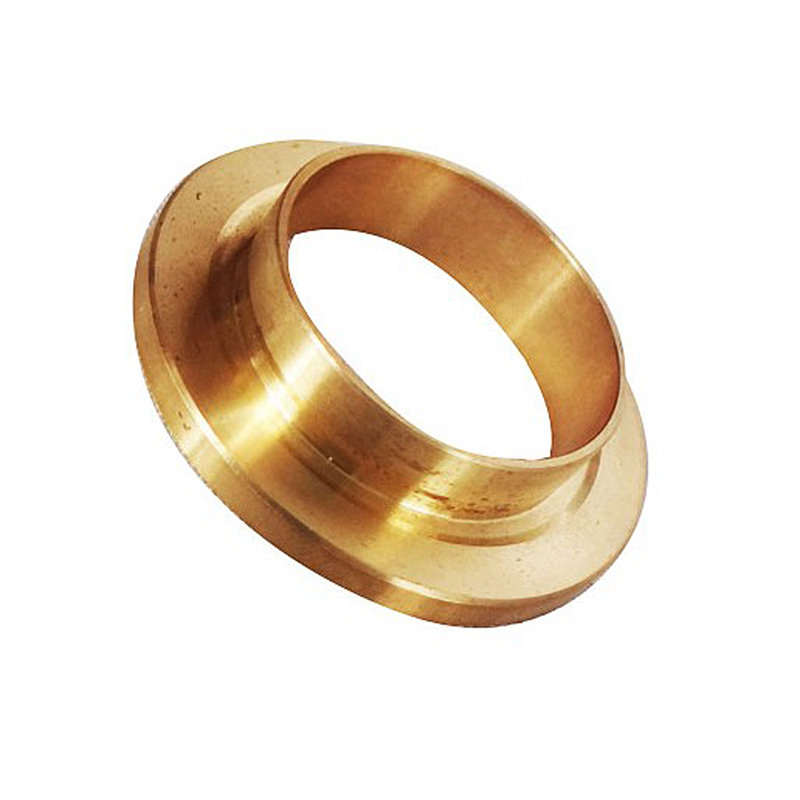
What Are the Properties of Brass?
Corrosion Resistance: Brass does not rust and is highly corrosion-resistant, especially from saltwater. This property makes it ideal for marine and outdoor applications.
Machinability: Brass is easy to machine, which makes it a preferred material for precision components. It can be easily cut, drilled, and shaped into complex designs.
Conductivity: Brass conducts heat and electricity well, making it useful in electrical and plumbing applications. Its excellent thermal conductivity makes it suitable for heat exchangers and other thermal applications.
Strength and Ductility: Brass offers a good balance of strength and ductility, allowing it to be formed into various shapes without breaking. It is strong enough to withstand significant stress while remaining flexible enough to be bent and shaped.
Aesthetic Appeal: Brass has a bright, gold-like, aesthetically pleasing appearance. It is often used in decorative applications, such as architectural fittings and jewellery.
Brass is the best material from which to manufacture many components because of its unique combinations of properties. For example, good strength and ductility are combined with excellent corrosion resistance and superb machinability.
Brass’s versatility and ease of fabrication make it a favourite among manufacturers. It can be cast, forged, rolled, and extruded into various shapes and sizes. Its ability to be quickly joined by soldering, brazing, and welding further enhances its suitability for complex manufacturing processes.
What is the Manufacturing Process of Brass?
1. Composition and Melting of Raw Materials: The raw materials are melted in an induction furnace.
2. Continuous Casting: The molten brass is continuously cast into solid forms. This process produces billets, slabs, or rods that can be further processed.
3. Cutting: The cast brass is cut into manageable pieces. These pieces are then ready for further processing, such as extrusion or rolling.
4. Heating and Extrusion: The brass is heated and extruded into desired shapes. Extrusion involves forcing the heated brass through a die to create long shapes with consistent cross-sections.
5. Continuous Pickling: The brass undergoes continuous pickling to remove impurities.
6. Cold Drawing: Cold drawing involves pulling the brass through a die to reduce its diameter and increase its length, improving its mechanical properties.
7. Straightening and Cutting: The drawn brass is straightened and cut to length. This step ensures that the final product meets the required specifications.
8. Low-Temperature Annealing: The brass undergoes low-temperature annealing to relieve stresses, improving its ductility and workability.
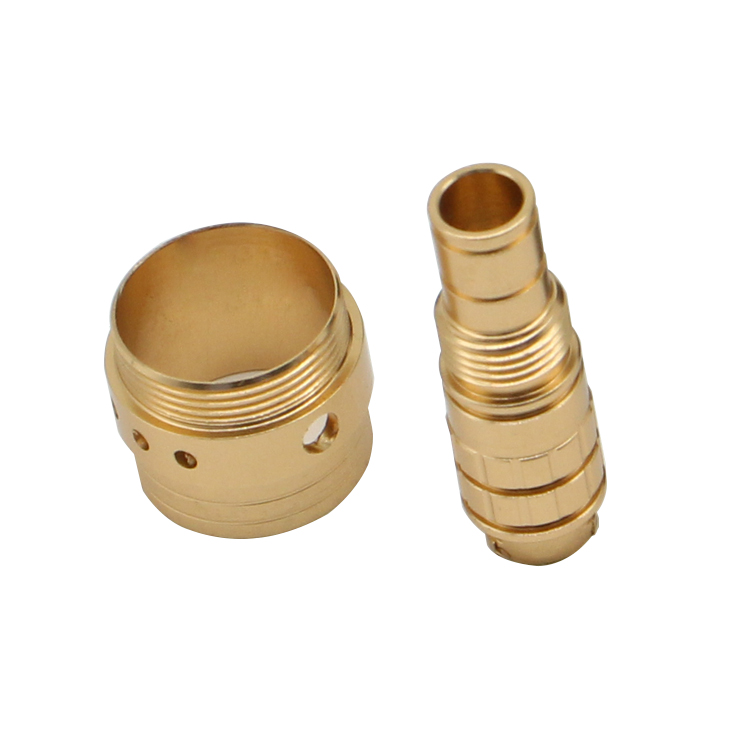
What Are the Uses of Brass in Industry?
Brass is commonly used in applications requiring corrosion resistance and low friction. Some of its industrial uses include:
Locks and Hinges: Brass is durable and provides smooth operation. Its corrosion resistance ensures long-lasting performance in these applications.
Gears and Bearings: Its low friction properties are ideal for moving parts. Brass’s ability to withstand wear and tear makes it suitable for gears and bearings requiring smooth, reliable operation.
Ammunition Casings: Brass is strong and corrosion-resistant. Its ductility allows it to quickly form into casings, while its strength ensures reliable performance.
Plumbing and Electrical Components: Brass’s conductivity and resistance to corrosion make it ideal for use in fittings, valves, and connectors.
Decorative Items: Brass’s bright, gold-like appearance and ability to be effortlessly polished make it famous for decorative pieces. Summary
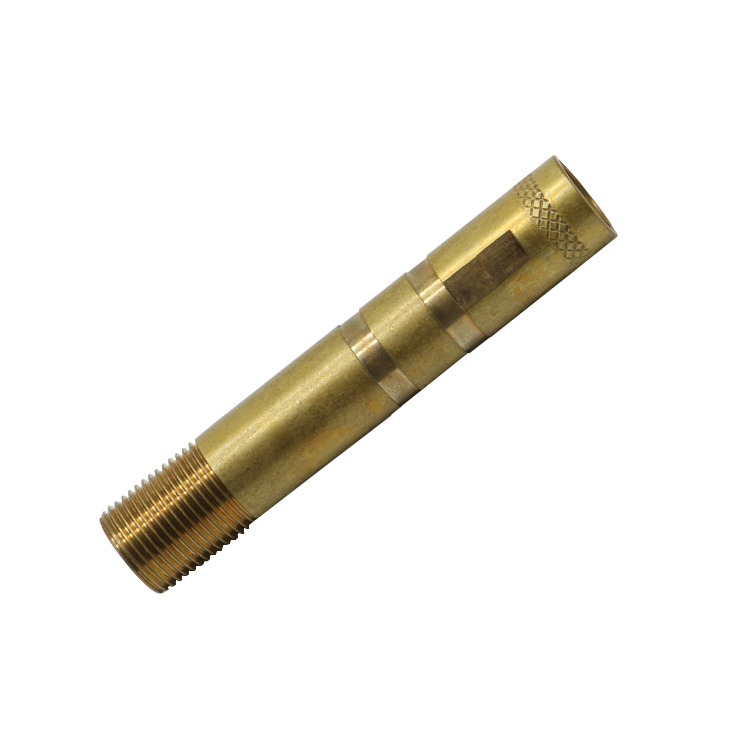
Summary
In conclusion, brass stands out as a manufacturing material due to its excellent properties and versatility. Whether in industrial applications or decorative items, brass’s unique characteristics make it an invaluable material in various fields.
Its strength, corrosion resistance, machinability, and aesthetic appeal ensure its continued relevance in manufacturing. As technology advances, brass will continue to play a crucial role in modern manufacturing, providing reliable performance and enduring appeal.