In precision manufacturing, even a 0.001-inch error can lead to part failure, poor fit, or costly rework.
For industries like aerospace, automotive, or robotics—where every millimeter counts—understanding CNC machining tolerances isn’t just a technical detail, it’s a business-critical decision.
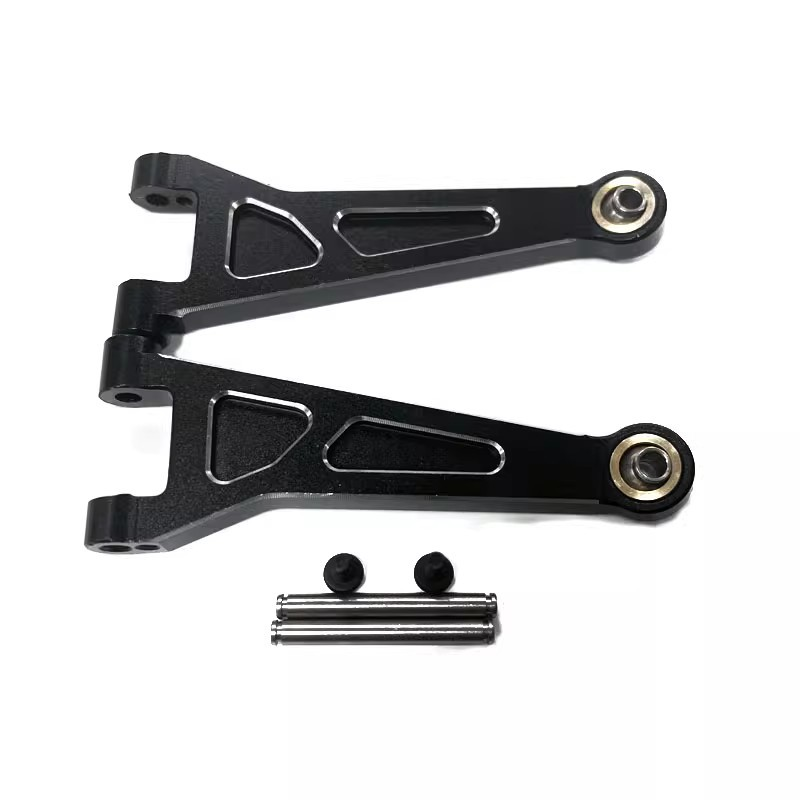
These tolerances define the acceptable range of variation in a part’s dimensions.
This article explains everything engineers, product developers, and buyers need to know about CNC tolerances.
You’ll learn what tolerances are, how they affect performance and cost, and how to choose the right level of precision for your specific project—without overpaying for features you don’t need.
Read on to discover how smart tolerance choices can improve quality, reduce waste, and keep your production on schedule and within budget.
-
Table Of Contents
-
1. Understanding CNC Machining Tolerances: Why Precision Matters?
-
2. What Are CNC Machining Tolerances?
-
3. Why Do CNC Tolerances Matter So Much?
-
4. What Is a Reasonable Tolerance for Your Application?
-
5. Types of Tolerances in CNC Machining
-
6. The Hidden Cost of Tight Tolerances: Are They Worth It?
-
7. How to Balance Precision and Price?
-
8. What If Tolerances Are Too Loose or Too Tight?
-
9. Summary
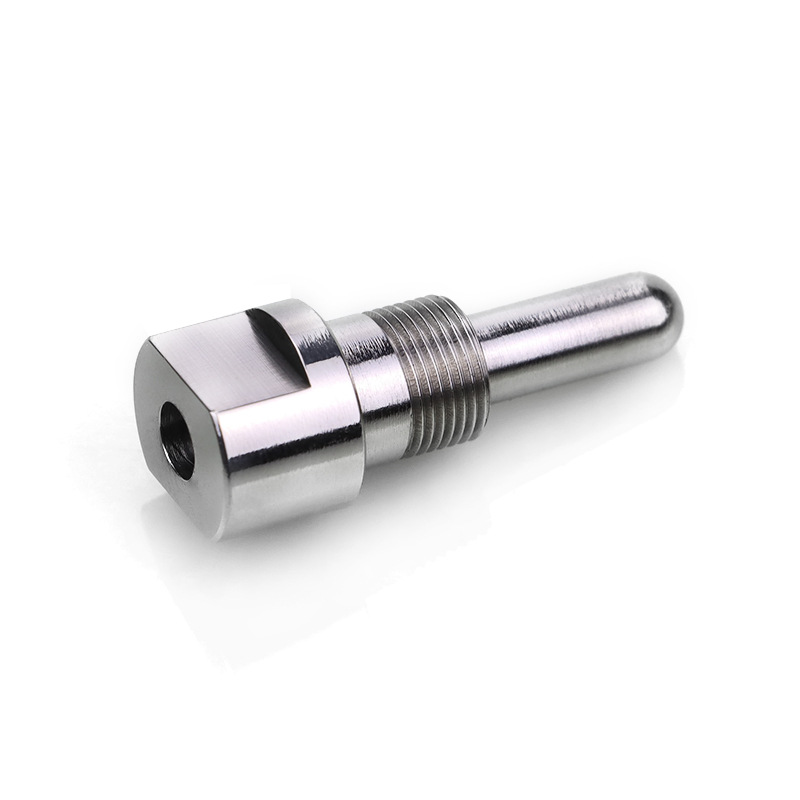
What Are CNC Machining Tolerances?
CNC machining tolerances define the allowable variation from a part’s specified dimensions.
No machine can deliver a “perfect” cut every time, but tolerances ensure that every finished piece falls within acceptable deviation limits for proper function.
Standard tolerances typically range from:
• ±0.005 inches (0.127 mm) for general parts
• ±0.001 inches (0.025 mm) for high-precision applications
• ±0.0001 inches (0.0025 mm) for ultra-precision parts
Properly specified tolerances help maintain part functionality, reduce fitment issues, and prevent production delays due to excessive rework.
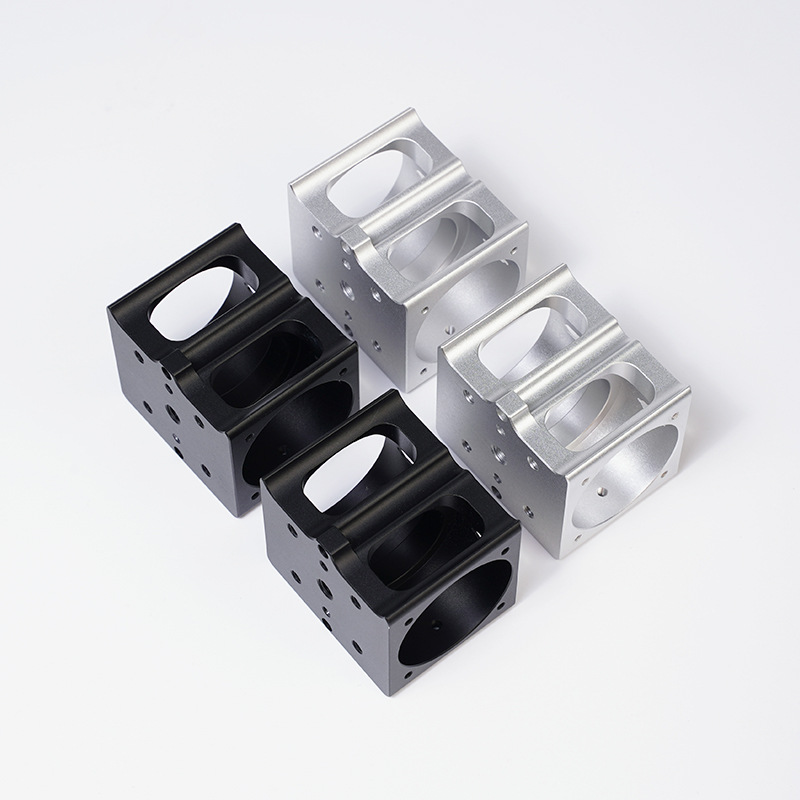
Why Do CNC Tolerances Matter So Much?
When parts are even slightly off, they may not fit, function, or assemble correctly.
This has serious consequences, especially in industries where safety and reliability are paramount.
The Benefits of Correct Tolerancing:
• Interchangeability – Enables seamless replacement or repair of components.
• Product Quality – Enhances consistency and reduces defect rates.
• Cost Efficiency – Saves on raw materials and rework time.
• Operational Safety – Critical for aircraft, medical implants, or automated machinery.
Real Example: In the aerospace sector, even a 0.001-inch misalignment can disrupt aerodynamics or cause system failure.
That’s why understanding and applying the right tolerance is non-negotiable.
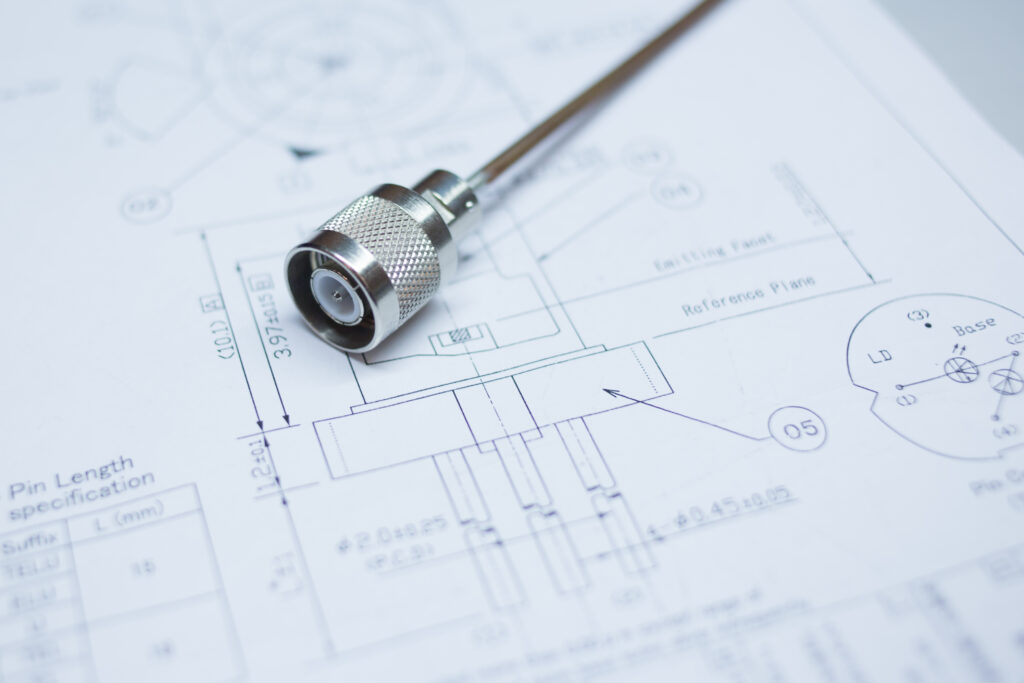
What Is a Reasonable Tolerance for Your Application?
There’s no one-size-fits-all answer. “Reasonable” depends on several factors, including:
Material Type – Harder materials like steel allow tighter tolerances than plastics.
Part Functionality – Does the part need to move? Fit tightly? Or allow some flexibility?
Manufacturing Process – Processes like grinding or EDM achieve tighter tolerances than milling.
Cost Constraints – The tighter the tolerance, the higher the machining cost.
Tolerance Ranges by Material
Material | Recommended Tolerance |
Plastic | ±0.010 inches (0.25 mm) |
Aluminum | ±0.005 inches (0.127 mm) |
Stainless Steel | ±0.002 inches (0.05 mm) |
Titanium | ±0.0005 inches (0.012 mm) |
Feature | Standard Tolerance (inches) | Standard Tolerance (mm) |
Hole Diameter | ±0.002 | ±0.050 |
Shaft Diameter | ±0.001 | ±0.025 |
Linear Dimensions | ±0.005 | ±0.127 |
Surface Flatness | ±0.002 | ±0.050 |
Angular Tolerance | ±0.5° | ±0.5° |
The charts help engineers and manufacturers determine the most practical tolerances for their projects.
While tighter tolerances improve accuracy, they also increase machining time and costs.
Choosing the right tolerance is about balancing precision with efficiency.
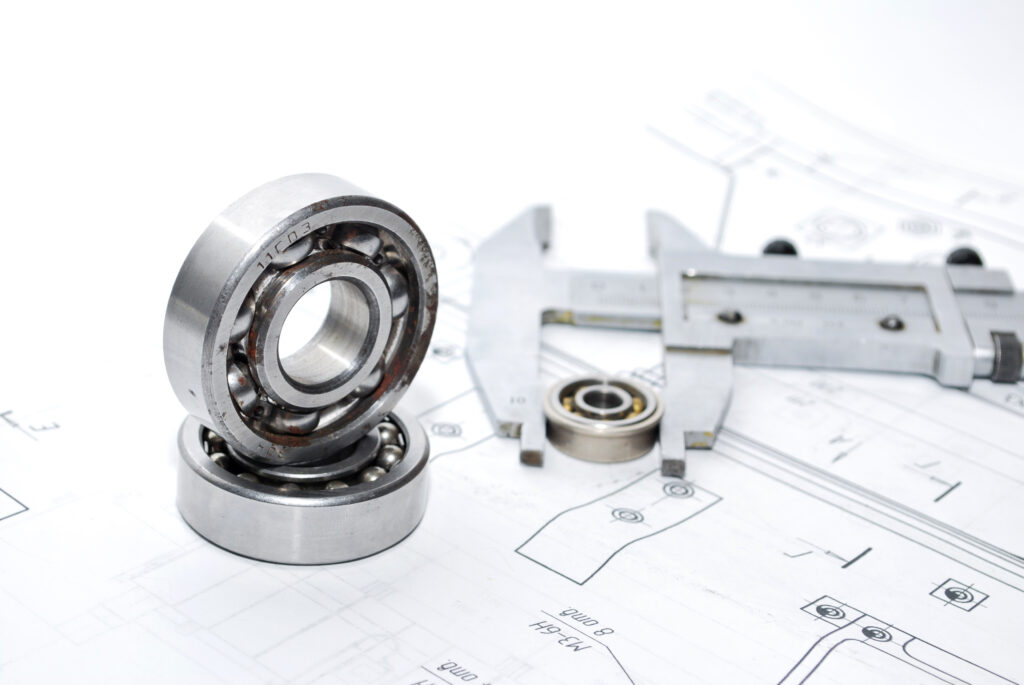
Types of Tolerances in CNC Machining
Knowing how tolerance types affect production helps engineers make smarter design decisions.
1. Unilateral Tolerance
• Allows deviation in one direction only (either above or below nominal).
• Example: +0.002 / -0.000 inches — part can be slightly larger but not smaller.
2. Bilateral Tolerance
• Allows variation in both directions.
• Example: ±0.002 inches — provides flexibility for fits and assemblies.
3. Geometric Tolerances (GD&T)
• Defines allowable variation in shape, form, orientation, and location.
• Includes flatness, roundness, perpendicularity, and concentricity—especially useful in parts that must rotate or align precisely.
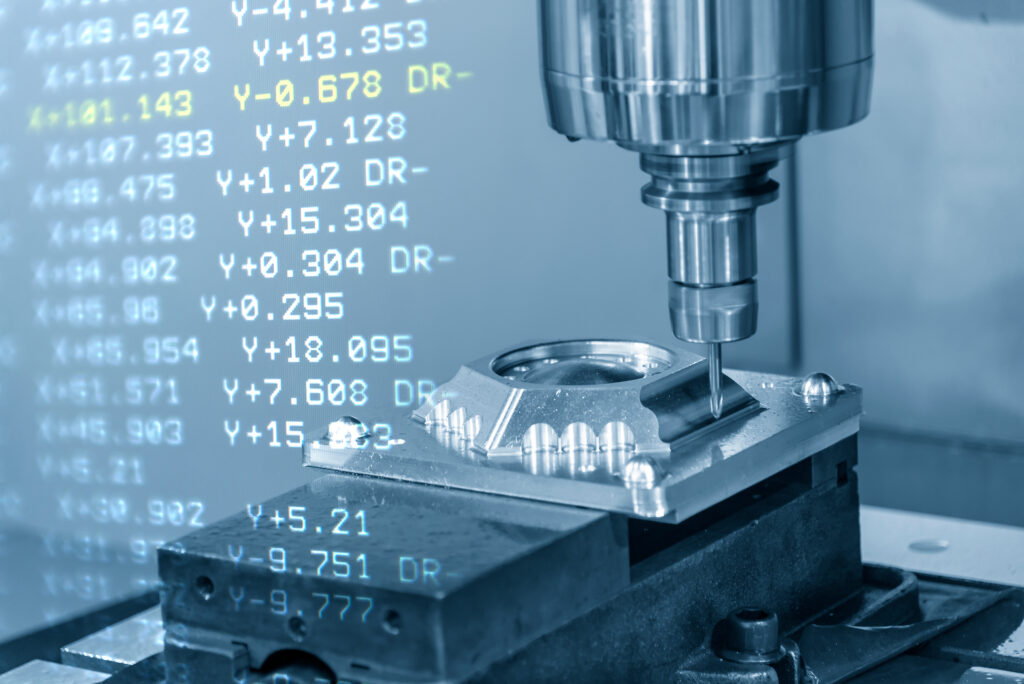
The Hidden Cost of Tight Tolerances: Are They Worth It?
While tight tolerances improve quality, they come at a price—literally.
Why Tight Tolerances Increase Cost:
• More machining time – Requires slow feed rates and precision tools.
• Higher scrap rates – Any part that exceeds the tolerance range must be discarded.
• Specialized equipment – Ultra-precision machining requires high-end CNC machines and temperature-controlled environments.
When You Absolutely Need Tight Tolerances:
• High-speed moving parts
• Interchangeable assemblies
• Aerospace, automotive, medical components
• Any scenario where performance and safety are mission-critical
For less critical parts, looser tolerances can dramatically cut costs without sacrificing functionality.
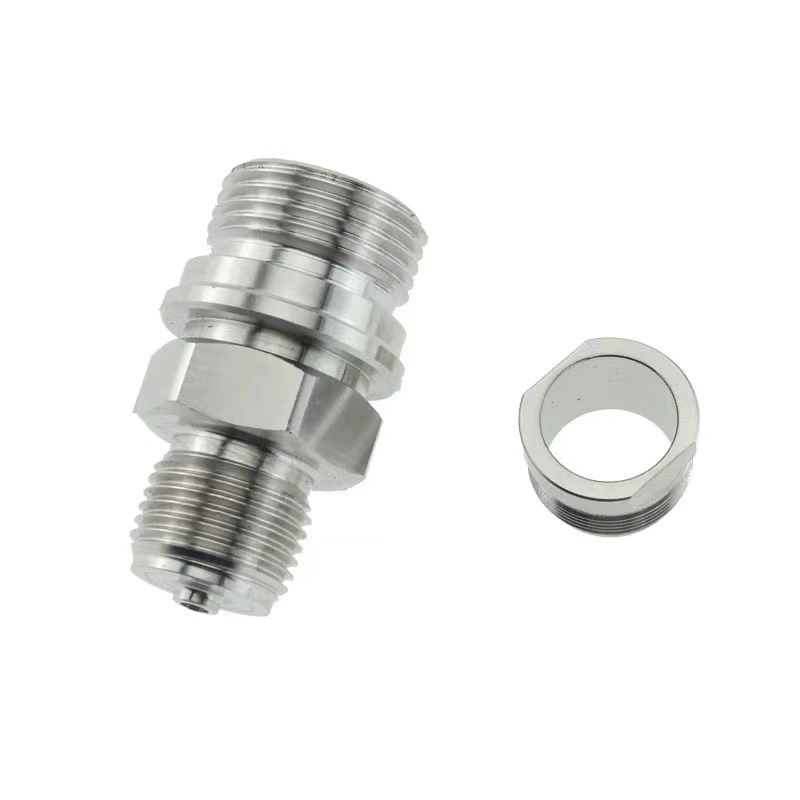
How to Balance Precision and Price?
If you’re sourcing CNC parts and struggling with balancing precision and price, you’re not alone.
Here’s a practical approach:
Optimize Tolerances Without Overpaying:
• Break down your part into zones – Not every feature needs ±0.001”!
• Talk to your machinist early – A CNC expert can often suggest design tweaks to reduce costs.
• Standardize where possible – Avoid custom tolerance specs unless absolutely necessary.
• Use prototyping – Test function before committing to ultra-tight tolerances in bulk.
This way, you’ll get parts that perform well—without inflating your unit cost.
What If Tolerances Are Too Loose or Too Tight?
Let’s say your part’s tolerance is off—what’s the worst that can happen?
If Tolerances Are Too Loose:
• Parts may not align, rotate properly, or maintain pressure seals.
• Increased wear, noise, or vibration in mechanical systems.
• Assembly delays and manual rework during production.
If Tolerances Are Too Tight:
• High rejection rates during quality inspection.
• Parts become over-engineered and overpriced.
• Longer lead times and higher tooling/tool wear costs.
Tip: Tolerances should reflect function, not perfection.
Ask, “What is the part supposed to do?” and let that guide your tolerance spec.
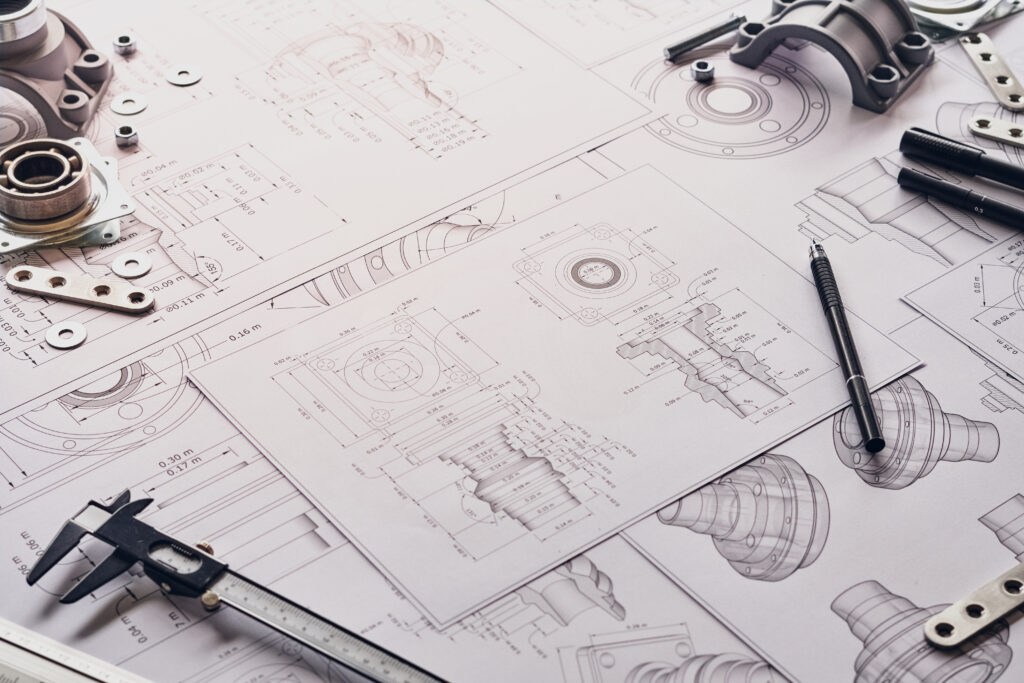
Conclusion:
Understanding CNC machining tolerances isn’t just for engineers—it’s essential knowledge for buyers, designers, and production managers who want reliable, cost-effective parts.
By considering material type, part function, and process capability, you can avoid unnecessary costs, ensure compatibility and performance, and reduce waste, scrap, and delivery delays.
Ultimately, the goal isn’t to chase perfection—it’s to achieve just enough precision to make your product perform flawlessly while keeping manufacturing practical and affordable.