Understanding the strengths and weaknesses of various techniques is essential when choosing the best method for producing metal parts.
Among these, sheet metal fabrication, CNC machining, casting, and 3D printing each offer unique advantages that impact quality, speed, and cost.
Making the right choice can be a game-changer for your project.
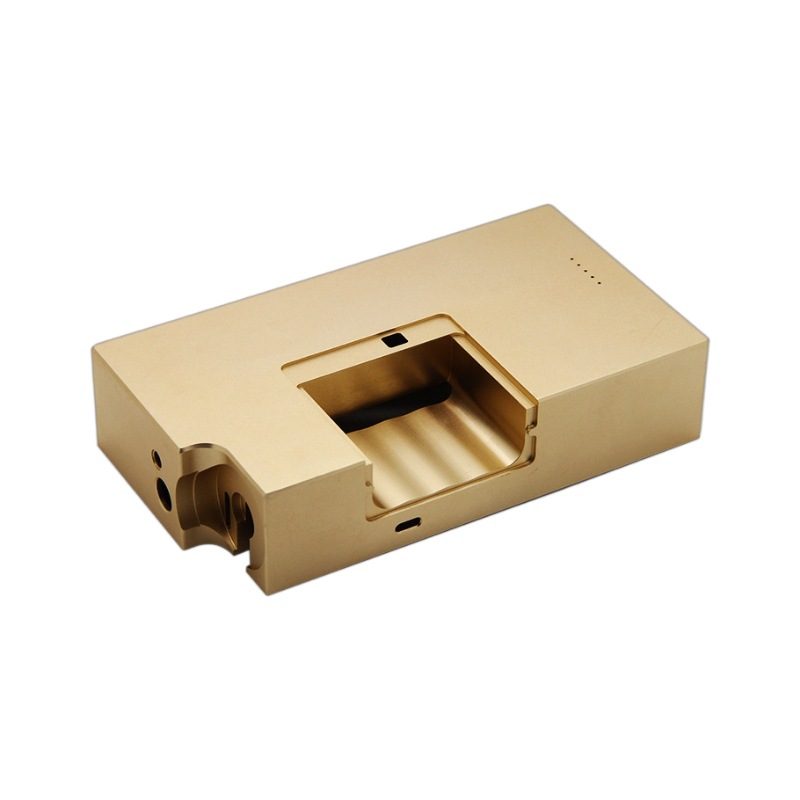
This article provides a comparison of sheet metal fabrication with other techniques, weighing their benefits and limitations.
While sheet metal fabrication is versatile and economical for simpler designs, CNC machining and 3D printing excel in producing intricate or high-precision parts.
By considering your design complexity, material needs, and production volume, you’ll be able to make a more informed decision.
Let’s explore each method, from what they entail to their pros and cons, so you can determine the best manufacturing process for your project.
-
Table Of Contents
-
1. How to Choose Between Sheet Metal Fabrication and Other Manufacturing Methods for Your Project?
-
2. What Sets Fabrication Apart from Manufacturing?
-
3. Core Sheet Metal Fabrication Techniques
-
4. Sheet Metal Fabrication vs. CNC Machining: Key Differences
-
5. 3D Printing vs. Sheet Metal Fabrication: When to Choose Which?
-
6. Final Decision: Which Manufacturing Technique Is Best?
-
7. Summary
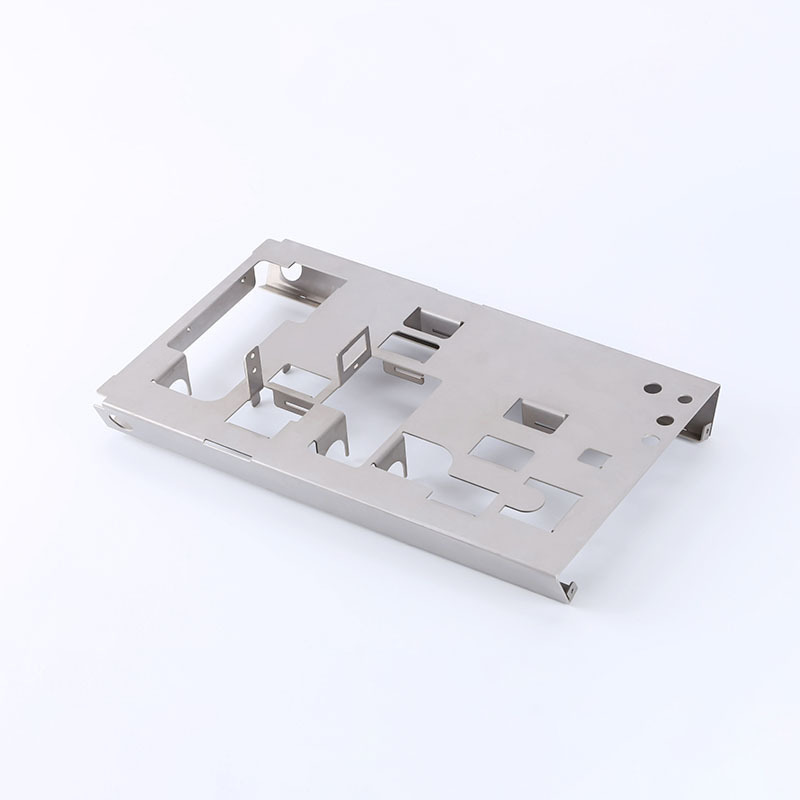
What Sets Fabrication Apart from Manufacturing?
Before delving into specifics, it’s important to distinguish between “fabrication” and “manufacturing,” terms often used interchangeably but with subtle differences in production contexts.
• Manufacturing: This term refers to the entire process of turning raw materials into finished products.
Manufacturing encompasses numerous methods, including fabrication, assembly, and machining, depending on the final product requirements.
• Fabrication: Specifically, this involves creating individual components, often from metal, through cutting, shaping, or forming.
These components may later be assembled into larger products. For instance, a car’s assembly involves manufacturing, while creating metal parts like brackets or enclosures falls under fabrication.
In summary, while manufacturing covers the entire process, fabrication zeroes in on creating parts essential for a final product.
Core Sheet Metal Fabrication Techniques
In sheet metal fabrication, transforming flat metal sheets into functional parts involves three main techniques: cutting, forming, and welding.
Each serves a unique purpose, depending on the part’s requirements.
1. Cutting: This initial step involves dividing large sheets into workable pieces. Methods vary by project needs:
Shearing: Uses a large blade for simple cuts, ideal for thin sheets.
Laser Cutting: A precise, high-quality method for intricate designs.
Plasma Cutting: Uses ionized gas to cut thick metals quickly and powerfully, often for industrial applications.
2. Forming: Essential for shaping metal sheets, forming techniques include:
Bending: Using a press brake, metal is bent to form various shapes like enclosures and frames.
Stamping: Common in high-volume production, stamping presses metal into a die for uniform shapes.
Roll Forming: Metal sheets are passed through rollers, creating cylindrical or curved shapes, commonly for pipes or tubes.
3. Welding: After cutting and forming, parts need joining:
MIG Welding: Ideal for thin metals, MIG welding is fast and effective.
TIG Welding: Provides high-precision welds for delicate metals.
Spot Welding: Common in automotive assembly, this method joins thin sheets at designated points.
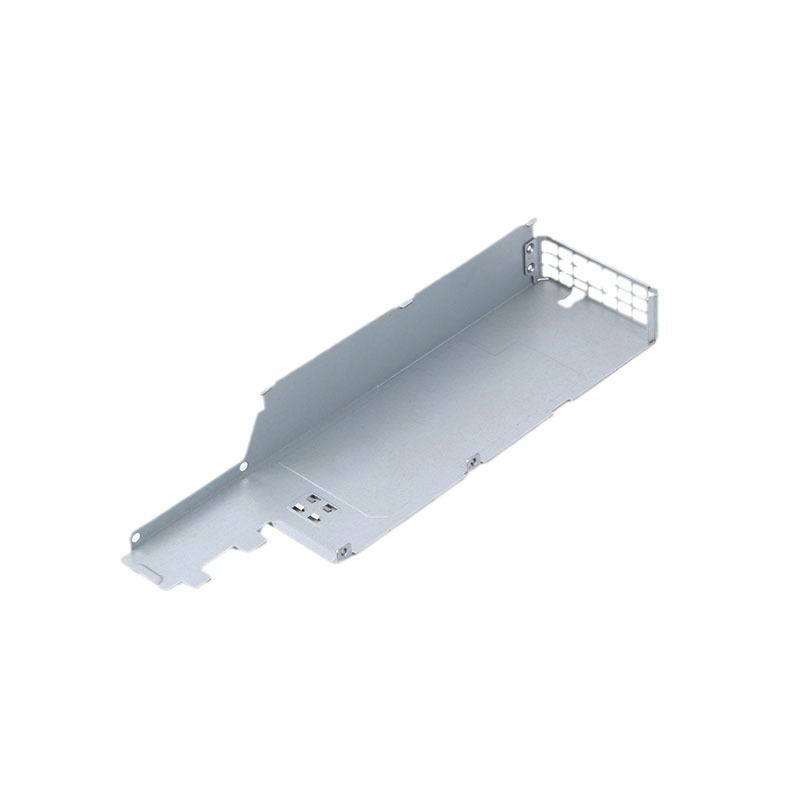
Sheet Metal Fabrication vs. CNC Machining: Key Differences
Both sheet metal fabrication and CNC machining have widespread use but differ significantly in approach and application.
• Sheet Metal Fabrication: This subtractive process shapes flat sheets through cutting, bending, and assembly. It’s efficient for high-volume production runs of simpler parts, making it a cost-effective choice for projects requiring moderate accuracy and durability.
• CNC Machining: Known for precision, CNC machining removes material from a solid block to create intricate parts. Controlled by computers, CNC machining offers precise cuts suitable for complex designs, such as medical or aerospace components.
Pros and Cons
• Cost: Sheet metal fabrication is economical for large production volumes, as it requires less machine time per part. CNC machining, while precise, can be costlier due to higher material waste and longer machine time.
• Precision: CNC machining provides superior precision, ideal for projects with intricate geometries. Sheet metal fabrication is best suited for simpler shapes.
• Material Use: Sheet metal fabrication uses flat sheets, while CNC machining starts with a solid block, shaping it down to the final form.
Cost Efficiency in Sheet Metal Fabrication
Cost-effectiveness often plays a crucial role in selecting a manufacturing method.
For high-volume production, sheet metal fabrication usually incurs lower upfront costs and has faster production times.
Cutting, bending, and assembling metal sheets is economical, especially for large quantities of simple parts.
Conversely, CNC machining’s costs arise from the time and resources needed to machine each part from a solid block.
While CNC machining may be pricier, it’s justified in projects where precision or complex designs are essential, particularly for small-batch production or prototyping.
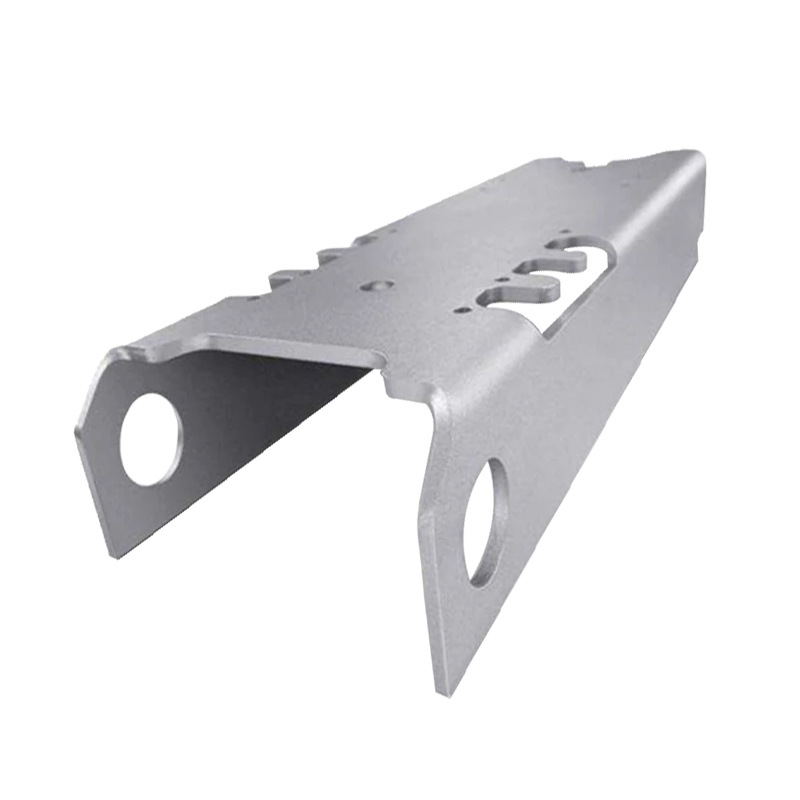
3D Printing vs. Sheet Metal Fabrication: When to Choose Which?
3D printing, an innovative manufacturing technology, offers exceptional design freedom, especially in prototyping.
However, it may not always surpass traditional methods like sheet metal fabrication.
Use 3D Printing When:
• Prototyping: 3D printing is rapid, ideal for testing designs before mass production.
• Complex Designs: It handles intricate geometries, often impossible in sheet metal fabrication.
• Low Volume: For small batch production, 3D printing can be more affordable than fabricating metal.
Use Sheet Metal Fabrication When:
• Durability: Sheet metal fabrication is ideal for parts needing strength, such as structural or load-bearing components.
• Large Production Runs: For high-volume output, fabrication is significantly more economical than 3D printing.
• Metal Materials: Although 3D printing can work with some metals, sheet metal fabrication excels in producing durable, bulk metal parts.
Final Decision: Which Manufacturing Technique Is Best?
Choosing the right manufacturing method depends largely on the specific needs of your project.
• Sheet Metal Fabrication: Perfect for high-volume production, this method is cost-effective and efficient for producing durable, moderately complex metal parts. Its material flexibility (steel, aluminum, copper) and scalability make it a popular choice across industries.
• CNC Machining: Opt for this if precision is paramount. CNC machining is unparalleled in creating complex parts with tight tolerances, suitable for high-precision industries like aerospace and medical devices. Though pricier, it’s ideal for projects demanding high accuracy.
• 3D Printing: Best for prototyping or low-volume production runs with complex designs, 3D printing allows fast, flexible production but may lack the material strength or cost-effectiveness needed in large-scale applications.
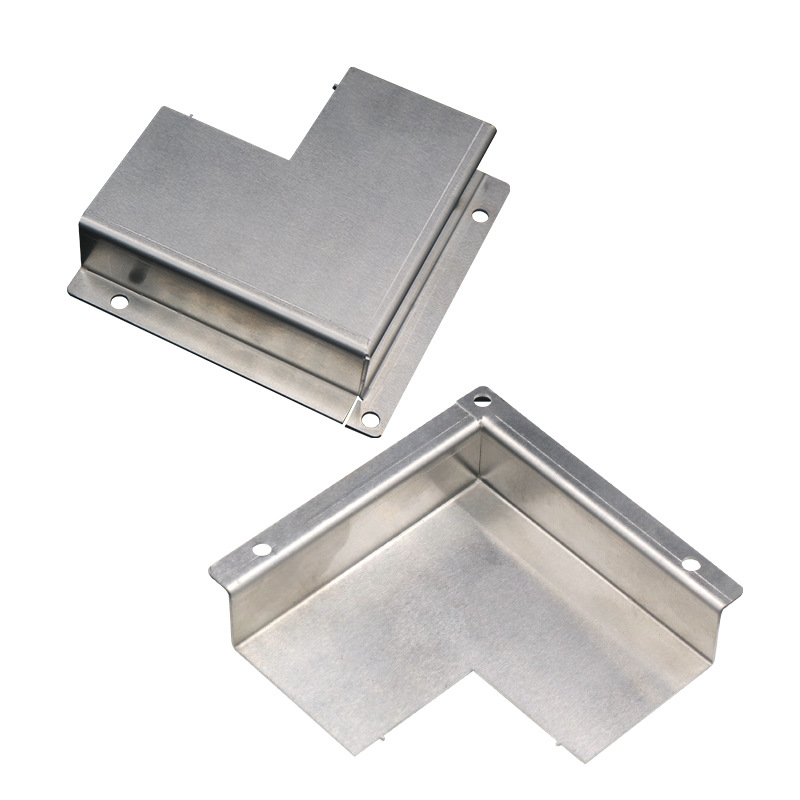
Conclusion
In conclusion, each manufacturing technique has unique strengths tailored to specific project needs.
Sheet metal fabrication shines in high-volume, economical production of simple to moderately complex parts, while CNC machining and 3D printing provide advantages in precision and design complexity.
By carefully evaluating your project’s requirements—whether it’s durability, volume, or precision—you can choose the optimal method that aligns with your goals, maximizing both quality and cost-effectiveness.