The final stages of sheet metal fabrication hold the key to maximizing the performance and visual appeal of metal parts.
Surface finishing and post-processing are essential in ensuring that metal components can withstand harsh environments while meeting aesthetic and functional demands.
These processes are indispensable, whether for industrial or personal use.
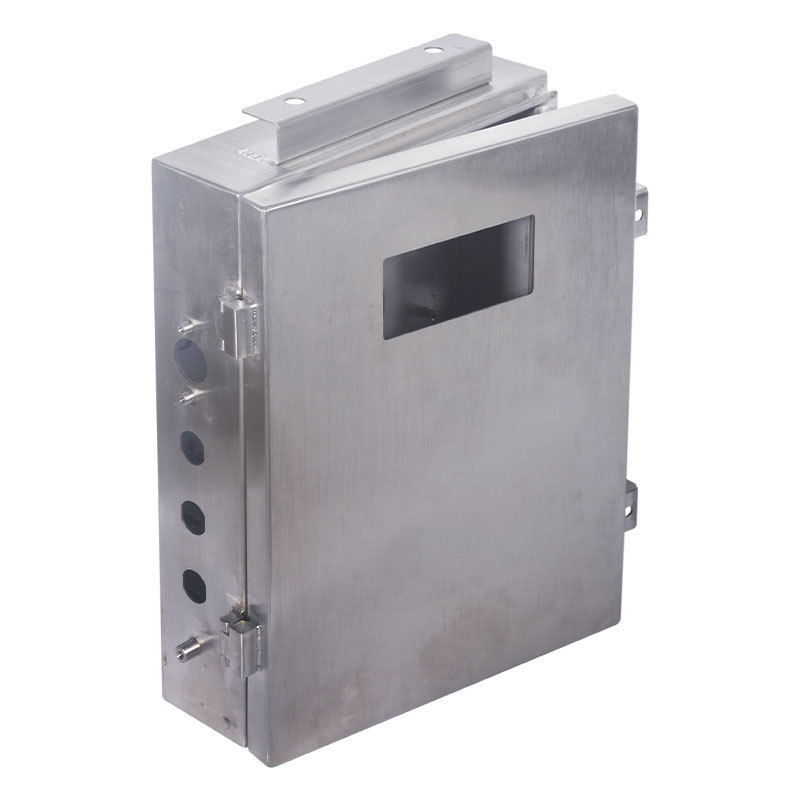
Surface finishing improves external characteristics such as texture, durability, and corrosion resistance, while post-processing techniques refine internal properties for better overall performance.
Together, they prepare sheet metal parts to meet rigorous standards in various applications.
Let’s delve into the techniques and benefits of surface finishing and post-processing, providing insights into their critical role in modern manufacturing.
-
Table Of Contents
-
1. How Do Surface Finishing and Post-Processing Enhance Sheet Metal Parts?
-
2. What Is the Surface Coating Process for Sheet Metal?
-
3. What Is Surface Finish in Sheet Metal?
-
4. What Is Surface Treatment in Sheet Metal?
-
5. How Do You Surface Finish Metal?
-
6. Why Choose the Right Surface Finish?
-
7. What Challenges Can Surface Finishing Solve for Manufacturers?
-
8. Summary
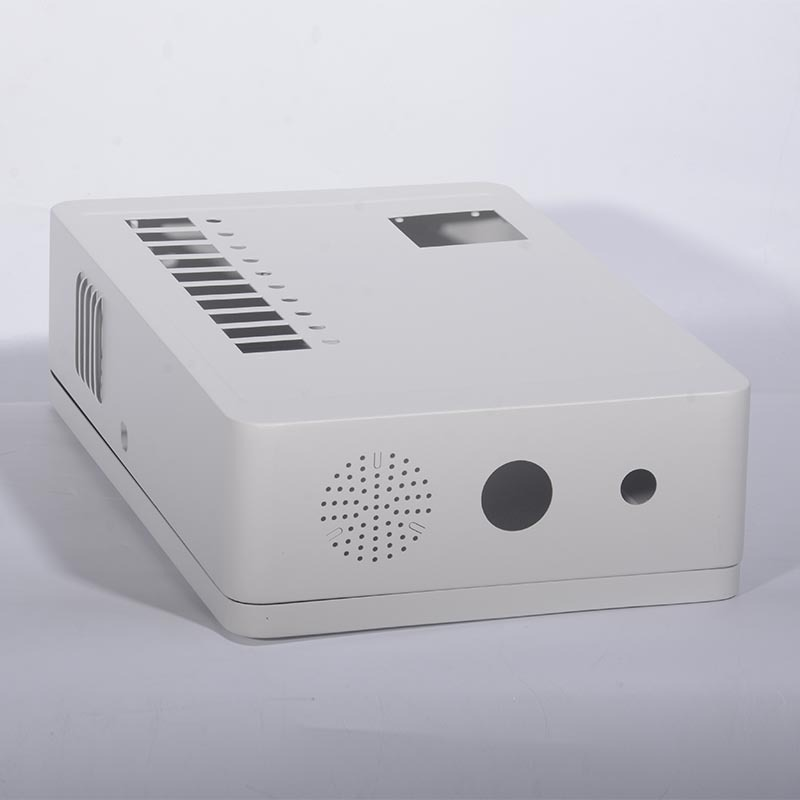
What Is the Surface Coating Process for Sheet Metal?
Surface coating is among the most common methods for enhancing the durability and aesthetics of sheet metal.
Metal parts often endure harsh environments, facing corrosion, wear, and damage.
By applying a protective layer, manufacturers can significantly extend the lifespan of these parts.
Key Surface Coating Methods:
• Spray Painting: An economical method ideal for general-purpose applications, offering a broad range of colors. However, its durability may be limited in abrasive environments.
• Electrostatic Painting: Ensures even paint coverage through electrostatically charged particles, providing a uniform and aesthetically pleasing finish. It’s frequently used in automotive and appliance manufacturing.
• Powder Coating: Known for its superior durability, powder coating uses dry powder that’s baked onto the surface, forming a hard, corrosion-resistant layer. It’s ideal for outdoor applications like bicycles and furniture.
• Dipping and Brushing: Manual methods for precise application on intricate or small components, commonly used in custom or low-volume production.
Each technique offers distinct advantages, tailored to specific functional and aesthetic requirements.
What Is Surface Finish in Sheet Metal?
Surface finish refers to the texture and smoothness of a metal’s surface, which can influence its performance and appearance.
The right finish can improve resistance to wear, reduce friction, or simply enhance visual appeal.
Common Surface Finishes:
• Matte Finish: Non-reflective and suitable for industrial components where appearance is secondary.
• Satin Finish: Offers a smooth, slightly reflective surface, balancing functionality and aesthetics, often used in consumer electronics.
• Mirror Finish: Highly reflective and polished, perfect for decorative applications like automotive trim or kitchen appliances.
The choice of finish depends on the component’s functional needs and its intended use environment.
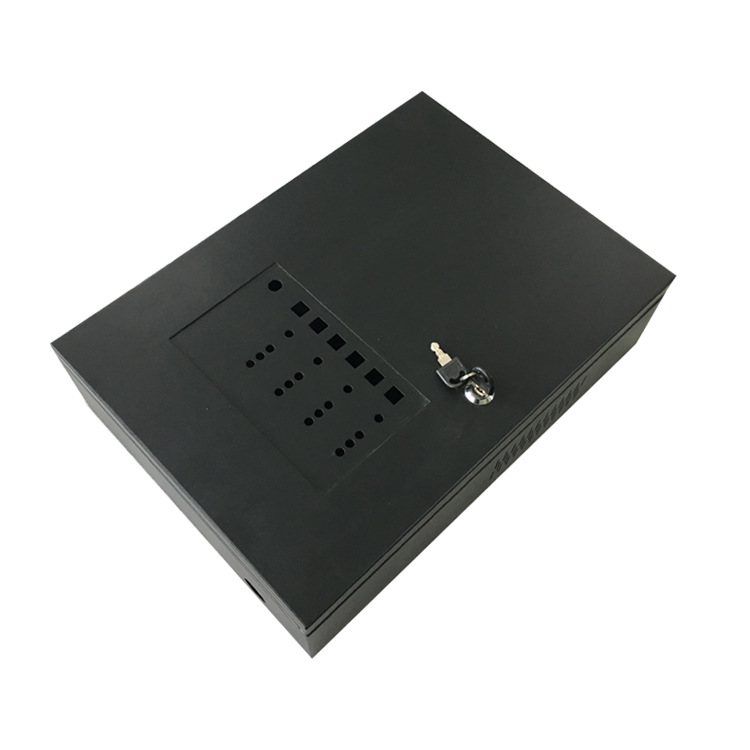
What Is Surface Treatment in Sheet Metal?
Unlike coatings, surface treatments chemically or electrochemically modify the metal itself, enhancing its properties without adding an external layer.
Notable Surface Treatments:
• Zinc Plating: Protects steel by creating a sacrificial zinc layer, often used in automotive and construction industries.
• Anodizing: A process for aluminum that thickens its oxide layer, offering enhanced corrosion resistance and the possibility of colorful finishes.
• Passivation: Enhances the natural corrosion resistance of stainless steel by creating a protective oxide layer, widely applied in food and pharmaceutical industries.
• Electropolishing: Removes surface imperfections, resulting in a smooth, high-gloss finish. Commonly used in medical and high-precision industries.
These treatments can also be combined with coatings for optimal performance.
How Do You Surface Finish Metal?
The process of achieving a specific surface finish involves several techniques, chosen based on the desired outcome and material type.
Core Finishing Techniques:
• Grinding: Uses abrasive wheels to achieve a precise, smooth surface, suitable for high-precision components like engine parts.
• Sanding: A versatile method for smoothing surfaces, often used to prepare metal for further finishing.
• Polishing: Creates a glossy finish through progressive abrasives, ideal for decorative or reflective applications.
• Bead Blasting: Uses fine particles to achieve a uniform matte or satin finish, commonly seen in industrial tools.
• Electropolishing: As previously mentioned, this method offers superior smoothness and shine for critical applications.
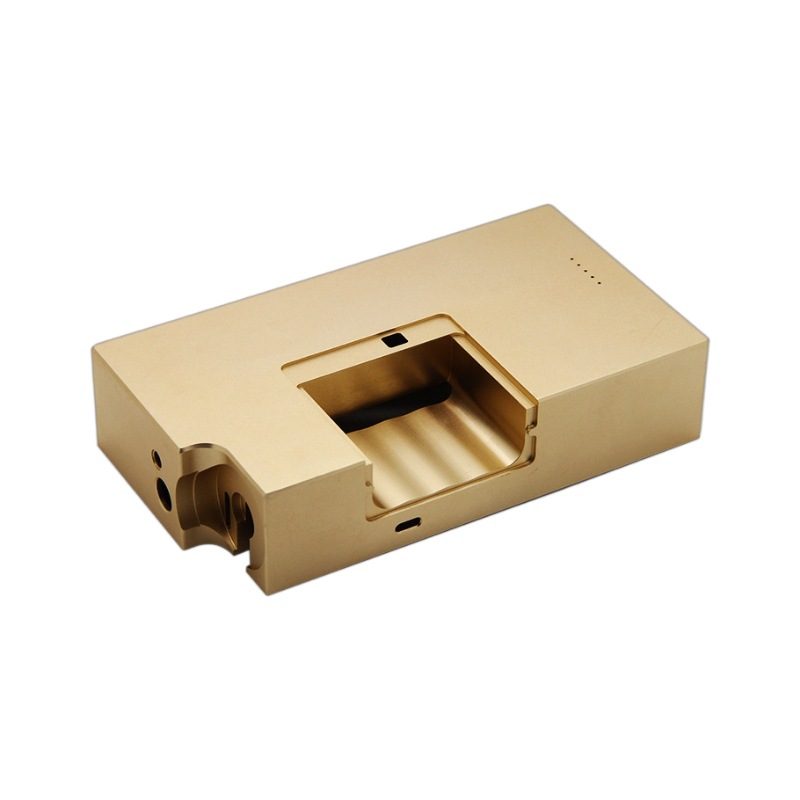
Why Choose the Right Surface Finish?
Selecting the correct surface finish or treatment is not merely a technical decision; it has far-reaching implications for performance, cost, and sustainability.
Here are the reasons:
Enhanced Performance:
Different environments demand tailored finishes. For instance, a mirror finish on stainless steel can significantly reduce bacterial growth, ideal for medical and food-processing equipment. Meanwhile, a powder-coated finish can protect automotive parts from harsh road conditions.
Cost Efficiency:
Investing in the right finish upfront minimizes long-term costs associated with maintenance, repairs, or replacements. For example, zinc plating extends the life of steel components exposed to moisture, reducing the need for frequent replacements.
Sustainability:
Finishes like anodizing and powder coating are environmentally friendly options. Anodizing uses fewer hazardous chemicals, while powder coating emits fewer volatile organic compounds (VOCs), aligning with green manufacturing initiatives.
By aligning surface finish choices with operational goals and environmental considerations, manufacturers can achieve a balance between performance and responsibility.
What Challenges Can Surface Finishing Solve for Manufacturers?
Manufacturers often face several challenges in delivering high-quality sheet metal parts.
These include corrosion, wear and tear, and achieving specific aesthetic or functional requirements.
Surface finishing and post-processing offer effective solutions:
• Corrosion Resistance: Untreated metal is highly susceptible to rust, especially in outdoor or humid environments. Techniques like anodizing and powder coating form protective layers that guard against corrosion, ensuring parts last longer.
• Improved Wear Resistance: For parts exposed to friction or heavy use, processes such as electropolishing and zinc plating reduce wear and extend service life.
• Enhanced Aesthetics: Many industries require metal parts to meet certain visual standards. Mirror finishes, satin textures, or colored anodized surfaces provide sleek, professional looks while maintaining functionality.
• Precision Fit and Functionality: Post-processing methods like grinding and sanding ensure parts fit accurately in assemblies and function as intended, reducing the likelihood of operational failures.
Understanding these challenges helps manufacturers choose the right finishing processes to enhance product quality and reliability, meeting both customer expectations and industry standards.
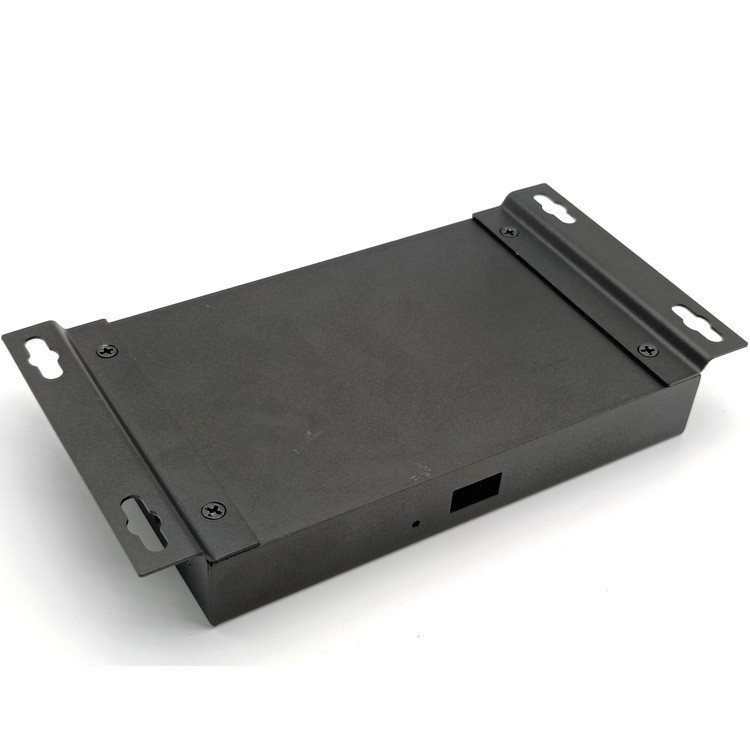
Conclusion
Surface finishing and post-processing are indispensable in sheet metal fabrication, ensuring components meet functional and aesthetic requirements.
These techniques not only improve durability and performance but also enhance the visual appeal of metal parts across various industries.
By understanding the available methods and their applications, manufacturers and hobbyists alike can optimize their projects for superior results.