Stainless steel CNC machining combines the precision of CNC technology with the strength and durability of stainless steel, creating essential components for industries like automotive, aerospace, and medical.
Known for its corrosion resistance and versatility, stainless steel is a preferred material, but machining it comes with unique complexities due to its toughness and thermal properties.
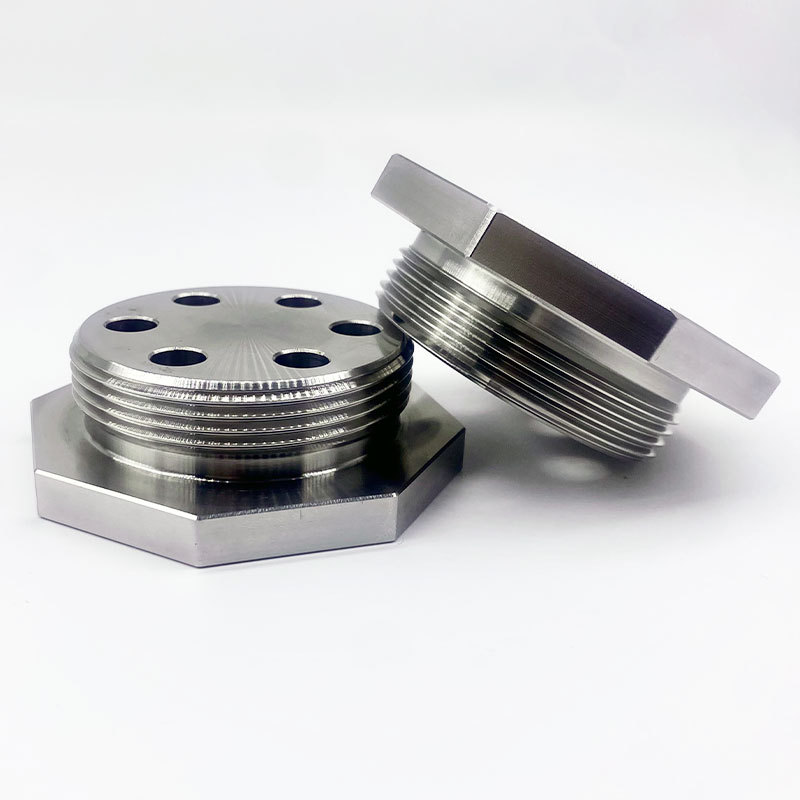
Machining stainless steel is demanding due to its hardness, heat retention, and tendency to work harden, but the right techniques can overcome these obstacles.
From selecting optimal cutting speeds and specialized tooling to using advanced coolant systems, we’ll cover essential methods that enable manufacturers to achieve precision and efficiency.
Read on as we delve into strategies for overcoming these challenges and maximizing the potential of stainless steel CNC machining.
-
Table Of Contents
-
1. Stainless Steel CNC Machining: What Makes It Challenging and How to Master It?
-
2. Common Types of Stainless Steel for CNC Machining
-
3. Key Challenges in Stainless Steel CNC Machining
-
4. Proven Techniques for Machining Stainless Steel
-
5. The Advantages of Stainless Steel in CNC Machining
-
6. Advanced Solutions for Overcoming Machining Challenges
-
7. How to Enhance Efficiency and Cost-Effectiveness in Stainless Steel CNC Machining?
-
8. Summary
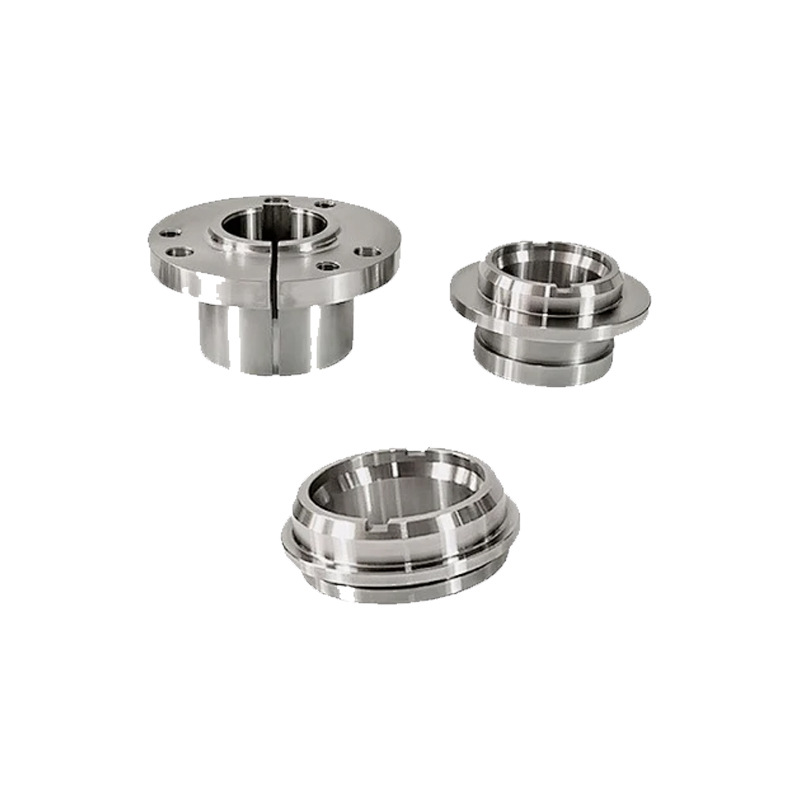
Common Types of Stainless Steel for CNC Machining
Various types of stainless steel are suited to different applications in CNC machining. Here are some common types:
1. Austenitic Stainless Steel (e.g., 304, 316)
304: The most common type, valued for corrosion resistance and formability. Widely used in food processing and medical devices.
316: Known for enhanced resistance to chemicals, making it suitable for marine and chemical industries.
2. Martensitic Stainless Steel (e.g., 410, 440C)
410: Offers high strength and moderate corrosion resistance, often used in cutlery and valves.
440C: Noted for extreme hardness and wear resistance, used in bearings, surgical tools, and cutting instruments.
3. Ferritic Stainless Steel (e.g., 430)
Typically more affordable and moderately resistant to corrosion. Found in automotive parts and kitchen appliances due to its reliability and cost-effectiveness.
4. Duplex Stainless Steel
Combines austenitic and ferritic structures for enhanced strength and corrosion resistance, ideal for use in oil, gas, and chemical applications.
Understanding the properties of these types of stainless steel can help machinists choose the most suitable one for specific applications.
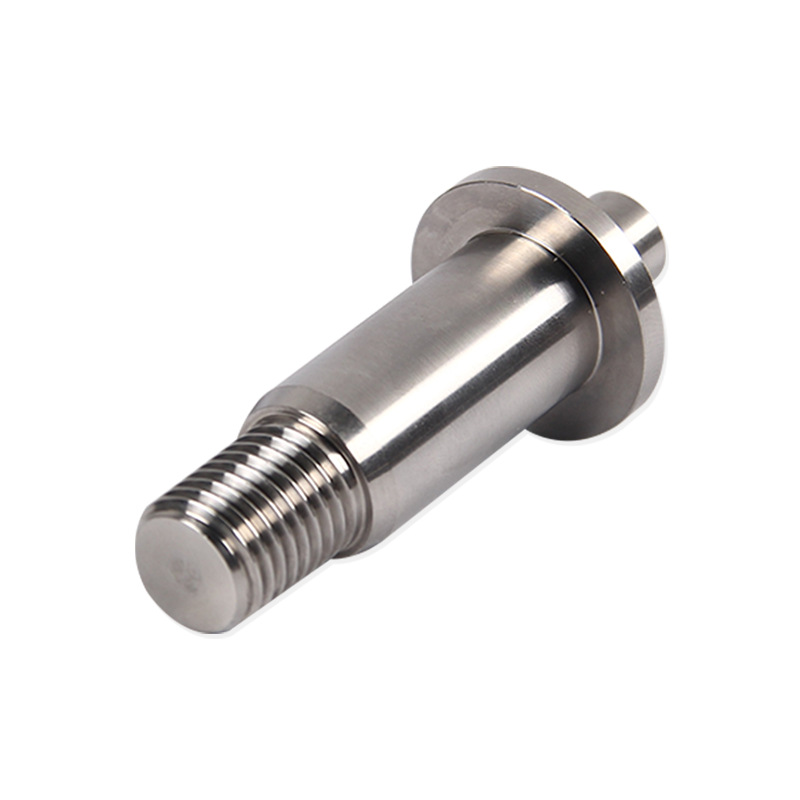
Key Challenges in Stainless Steel CNC Machining
While stainless steel offers undeniable benefits, its unique properties introduce specific challenges during CNC machining:
1. Hardness and Strength: The high strength of stainless steel makes it harder to cut than other metals, resulting in increased tool wear and requiring durable, high-performance cutting tools.
2. Heat Generation: Stainless steel’s poor thermal conductivity means that heat builds up in the cutting zone, which can deform tools, reduce precision, and negatively impact surface finish.
3. Work Hardening: Stainless steel tends to work harden—meaning it becomes harder as it is deformed, especially during machining. This can dull or break tools if not controlled properly.
4. Tool Wear: Stainless steel’s toughness and poor heat dissipation cause rapid tool wear. Carbide tools, which maintain hardness at high temperatures, are frequently used but require careful management to extend their lifespan.
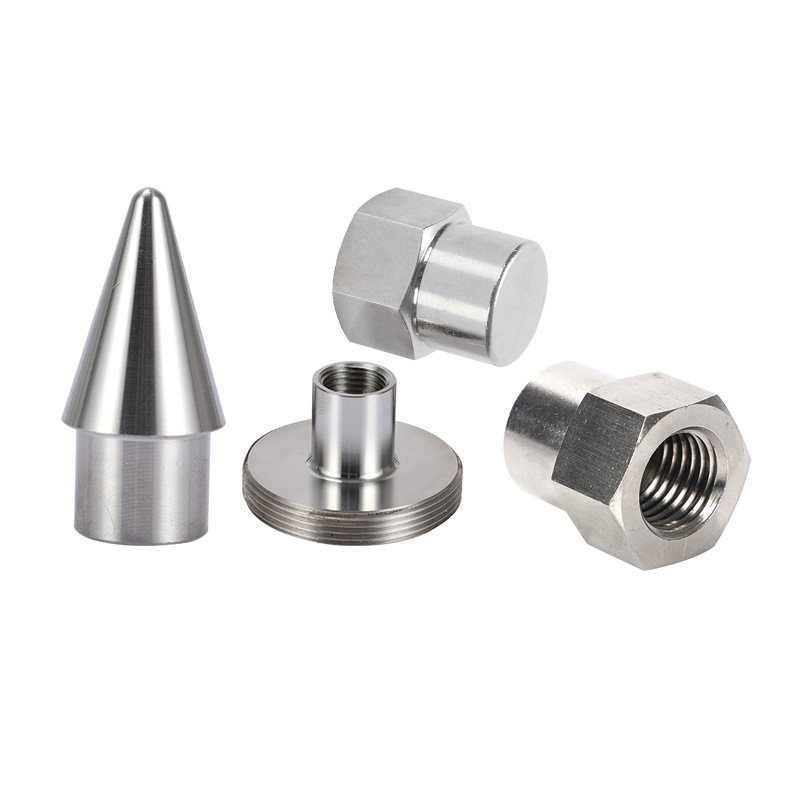
Proven Techniques for Machining Stainless Steel
Effective machining of stainless steel depends on employing specific techniques tailored to its properties:
1. Adjusting Cutting Speeds and Feed Rates
Lower cutting speeds reduce heat generation, while higher feed rates help evacuate chips quickly, minimizing work hardening.
2. Using Coolants
Coolants are essential for controlling the temperature at the cutting edge. High-pressure coolant systems are particularly effective in improving tool life and ensuring a quality surface finish.
3. Selecting the Right Tools
Carbide tools are a popular choice due to their high hardness and wear resistance at elevated temperatures. Coated tools, such as those with titanium nitride, further reduce friction, extending tool life.
4. Optimizing Tool Geometry
Tools with positive rake angles and sharp cutting edges reduce cutting forces and prevent work hardening. Careful tool geometry design enhances machinability, especially with harder grades of stainless steel.
5. Machining in Multiple Passes
A multi-pass approach, starting with a roughing pass followed by finishing passes, helps achieve desired precision and surface quality while managing tool wear.
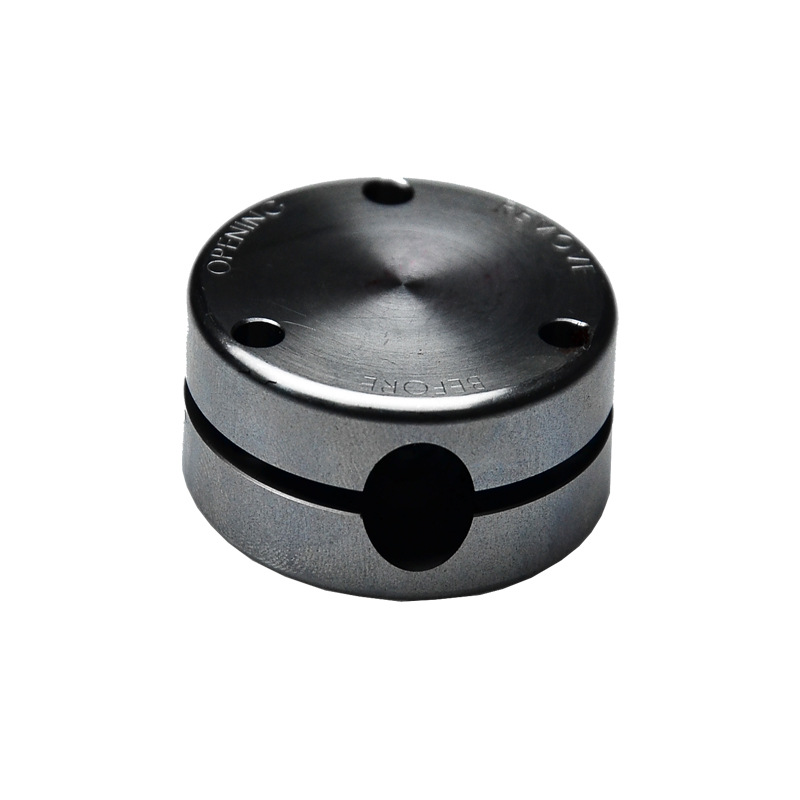
The Advantages of Stainless Steel in CNC Machining
Despite the challenges, stainless steel remains a popular choice due to its many advantages:
1. Corrosion Resistance
Stainless steel’s resistance to rust and corrosion makes it suitable for parts exposed to moisture, chemicals, or extreme temperatures, such as marine and chemical processing applications.
2. Durability and Strength
Stainless steel parts are highly durable, making them ideal for high-stress environments in the automotive and aerospace industries.
3. Aesthetic Appeal
Stainless steel has a polished, clean appearance, popular in consumer electronics, kitchen appliances, and architectural elements. Additionally, it is easy to clean, adding value in the food industry.
Advanced Solutions for Overcoming Machining Challenges
For manufacturers aiming to master stainless steel machining, the following advanced solutions can improve productivity and extend tool life:
1. High-Performance Cutting Tools
Tools coated with ceramics or diamond-like materials offer enhanced durability, especially beneficial when machining tougher stainless steel grades like 440C.
2. High-Pressure Coolant Systems
Advanced coolant systems improve chip removal and keep cutting tools cool, reducing wear and maintaining precision.
3. Optimized Tool Paths
CNC software optimization can reduce tool engagement time and heat generation, especially in challenging areas. This strategy also reduces the risk of tool deformation.
4. Vibration Damping
Tools with vibration-damping properties reduce chatter, resulting in smoother finishes and improved tool longevity.
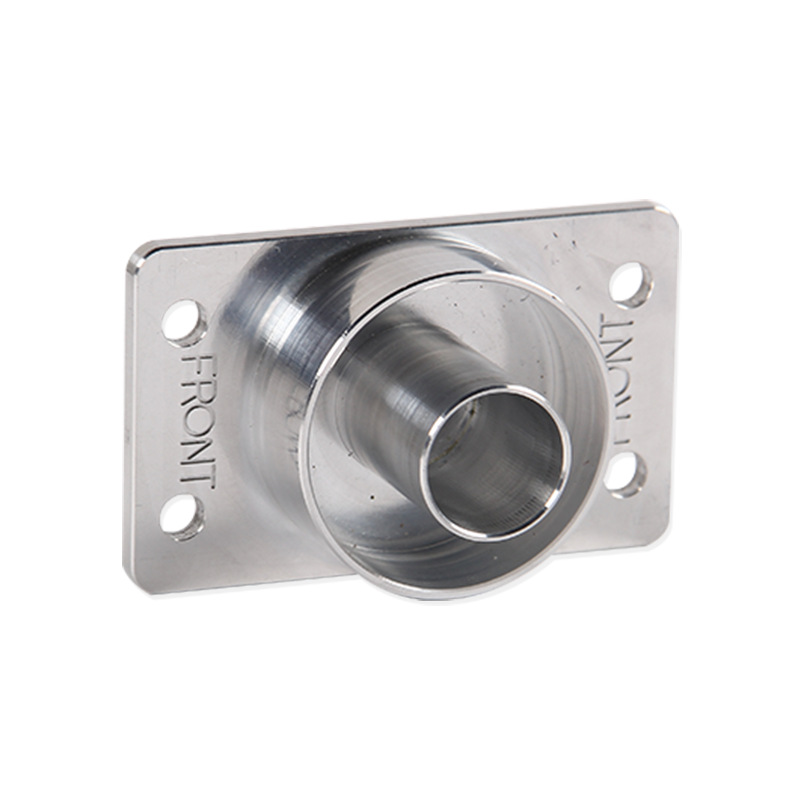
How to Enhance Efficiency and Cost-Effectiveness in Stainless Steel CNC Machining?
Improving efficiency and reducing costs are key priorities in stainless steel CNC machining. Implementing the following strategies can help meet these goals effectively:
1. Optimizing for Batch Production
When demand is high, batch production can significantly lower the cost per unit. By planning orders in advance and using consistent setups and programs, manufacturers can reduce preparation time for each part, thereby increasing overall production efficiency.
2. Regular Maintenance of Equipment and Tooling
Regular maintenance checks, timely tool replacements, and inspections for wear can enhance cutting accuracy and reduce the risk of costly downtime due to equipment failure.
3. Implementing Smart Monitoring and Process Control
Smart monitoring systems that track real-time data on tool wear, machine vibration, and temperature can optimize the machining process and reduce waste.
These systems help to catch issues early, reducing human error and scrap rates, while providing alerts for maintenance needs, thus extending equipment longevity and improving overall productivity.
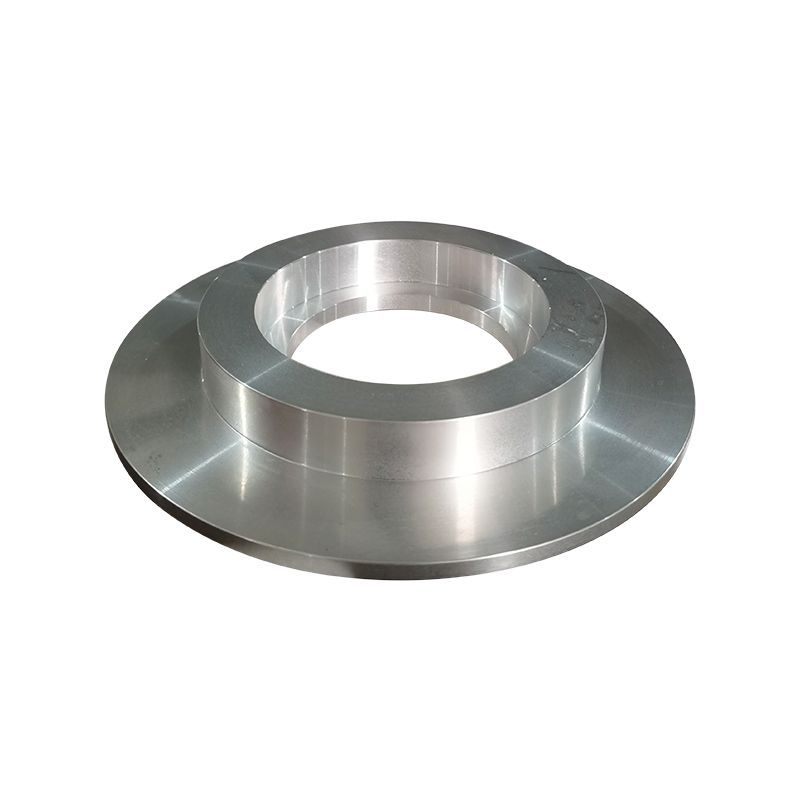
Conclusion
Mastering stainless steel CNC machining involves understanding the material’s challenges and utilizing appropriate techniques and tools.
By optimizing cutting speeds, using high-performance tools, and investing in advanced coolant systems, manufacturers can effectively tackle stainless steel’s inherent difficulties, achieving high-quality results that meet industry standards.