Understanding the intricacies of aluminum die casting is crucial for optimizing manufacturing processes. Despite its importance, many professionals struggle with the technical details and best practices of die casting.
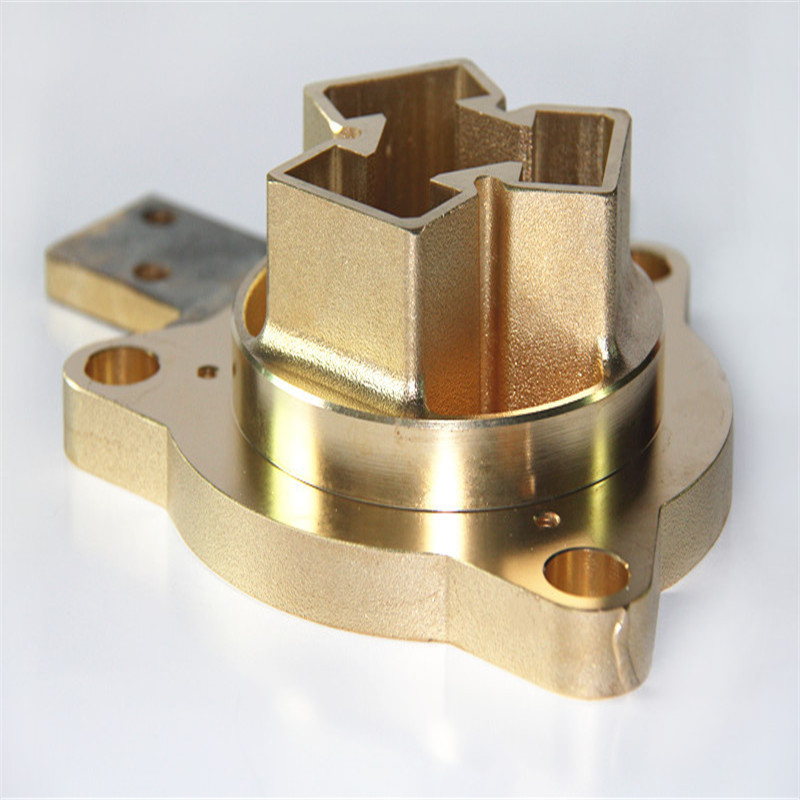
In the process, molten aluminum is injected into the die cavity where it solidifies quickly. These sections are mounted securely in a machine and are arranged so that one is stationary while the other is moveable. The die halves are drawn apart and the casting is ejected.
Now, let’s delve deeper into the specifics of the aluminum die casting from various aspects, especially the process.
This guide provides detailed information, addressing common questions and concerns, helping people involved in the industry navigate the complexities of this essential process.
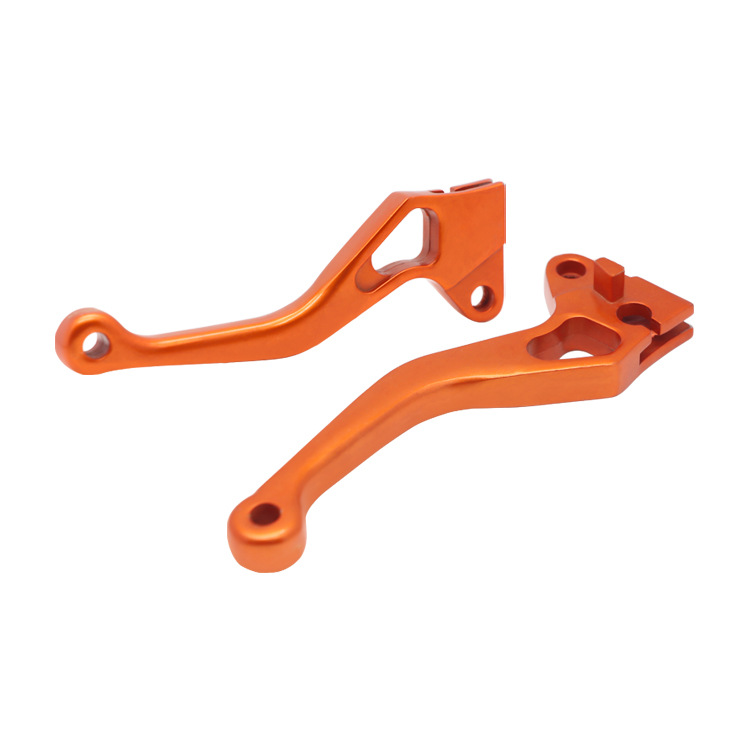
How Does Aluminum Die Casting Work Step by Step?
1. Melting the Aluminum: Aluminum is heated until it reaches a molten state, typically at temperatures above 600°C. The molten aluminum is then ready for injection into the mold.
2. Injection: The molten aluminum is transferred to a cold chamber machine, where it is injected into a steel mold at high pressure. The pressure ensures that the molten aluminum fills the mold cavity completely, even in intricate and thin sections.
3. Cooling: Once the aluminum fills the mold, it is allowed to cool and solidify. The cooling process is carefully controlled to ensure the casting has the desired microstructure and mechanical properties.
4. Ejection: After solidification, the mold is opened, and the casting is ejected using ejector pins. The ejection process must be precise to avoid damaging the casting.
5. Trimming: Any excess material, such as flash, gates, and runners, is trimmed from the casting. This can be done manually or using automated trimming machines.
6. Finishing: Additional finishing operations, such as machining, polishing, or coating, may be performed to meet the final specifications. The finished casting is then inspected for quality and dimensional accuracy.
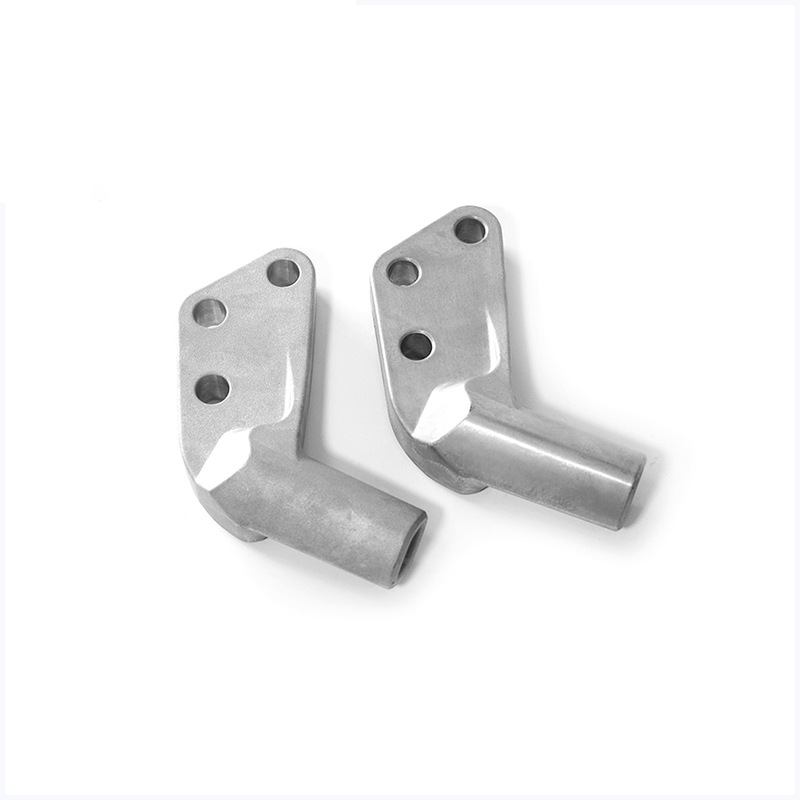
What are Types of Casting Process for Aluminum?
Die casting is highly suited for aluminum due to its ability to produce large quantities of precise, complex parts with excellent surface finish and mechanical properties.
However, the best casting process for aluminum can vary depending on the specific requirements of the application. Here are some common casting processes for aluminum:
1. Sand Casting: Ideal for producing large parts with complex geometries. Sand casting involves creating a mold from sand, into which molten aluminum is poured. This process is cost-effective for low to medium production volumes but may require additional machining and finishing.
2. Gravity Die Casting: Also known as permanent mold casting, this process uses a reusable steel or iron mold. Molten aluminum is poured into the mold under gravity. Gravity die casting produces parts with better mechanical properties and surface finish than sand casting but is more expensive.
3. Low Pressure Die Casting: In this process, molten aluminum is introduced into the mold under low pressure. This method provides good dimensional accuracy and is suitable for producing complex shapes and thin-walled parts.
4. High Pressure Die Casting: This is the most common method for aluminum die casting. It involves injecting molten aluminum into a steel mold under high pressure. High pressure die casting is suitable for high-volume production and produces parts with excellent surface finish and dimensional accuracy.
5. Investment Casting: Also known as lost-wax casting, this process involves creating a wax model of the part, which is then coated with ceramic material to form a mold. The wax is melted away, and molten aluminum is poured into the ceramic mold. Investment casting is ideal for producing small, complex parts with high precision.
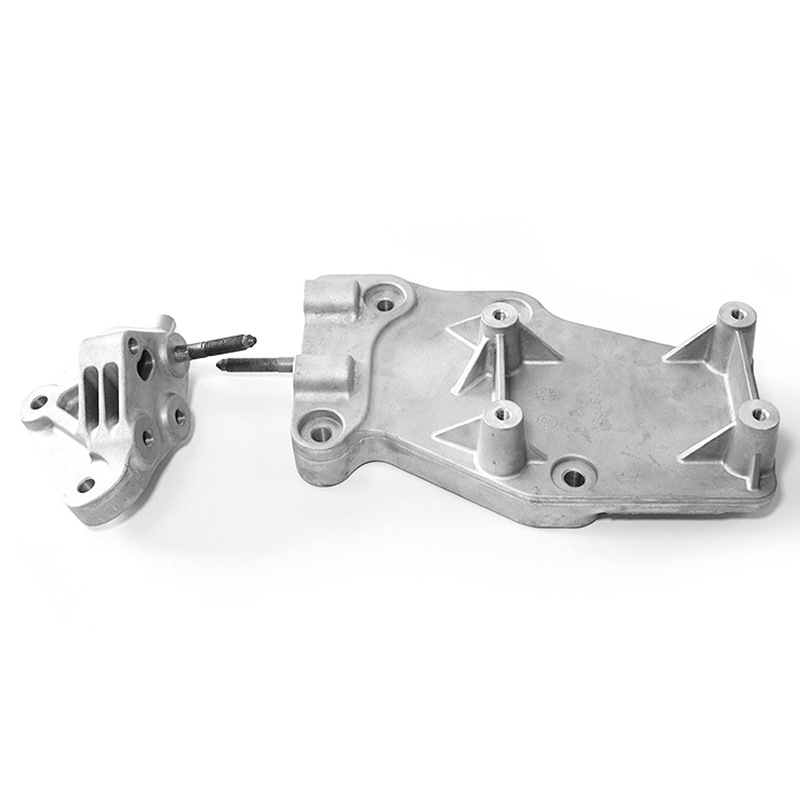
What are Properties of Aluminum Die Cast
Aluminum die cast is prized for its excellent material properties, which make it suitable for a wide range of applications. Here are some key properties of die cast aluminum:
1. High Strength-to-Weight Ratio: Aluminum is a lightweight metal with excellent strength, making it ideal for applications where weight reduction is critical, such as in the automotive and aerospace industries.
2. Good Corrosion Resistance: Aluminum naturally forms a protective oxide layer on its surface, which enhances its corrosion resistance. This property is particularly beneficial in applications exposed to harsh environments.
3. Excellent Thermal Conductivity: Aluminum has high thermal conductivity, making it suitable for heat dissipation applications, such as in electronic enclosures and heat sinks.
4. High Electrical Conductivity: Aluminum’s high electrical conductivity makes it an excellent choice for electrical and electronic components.
5. Good Machinability: Die cast aluminum parts can be easily machined to tight tolerances, allowing for the production of complex and precise components.
6. Recyclability: Aluminum is 100% recyclable without losing its properties, making it an environmentally friendly material choice.

Die Cast Aluminum vs Stainless Steel
When choosing between die cast aluminum and stainless steel, several factors must be considered, including weight, strength, corrosion resistance, and cost.
1. Weight: Aluminum is significantly lighter than stainless steel, making it ideal for applications where weight reduction is crucial, such as in automotive and aerospace industries.
2. Strength: While aluminum has a high strength-to-weight ratio, stainless steel is generally stronger and more durable. Stainless steel is better suited for applications requiring high strength and resistance to wear and tear.
3. Corrosion Resistance: Both materials have excellent corrosion resistance, but stainless steel offers superior resistance in highly corrosive environments. Aluminum’s natural oxide layer provides good corrosion protection, but it may not be as robust as the protective layer on stainless steel.
4. Cost: Aluminum is generally less expensive than stainless steel, making it a cost-effective choice for many applications. However, the total cost will depend on the specific requirements of the project, including the need for additional finishing or machining.
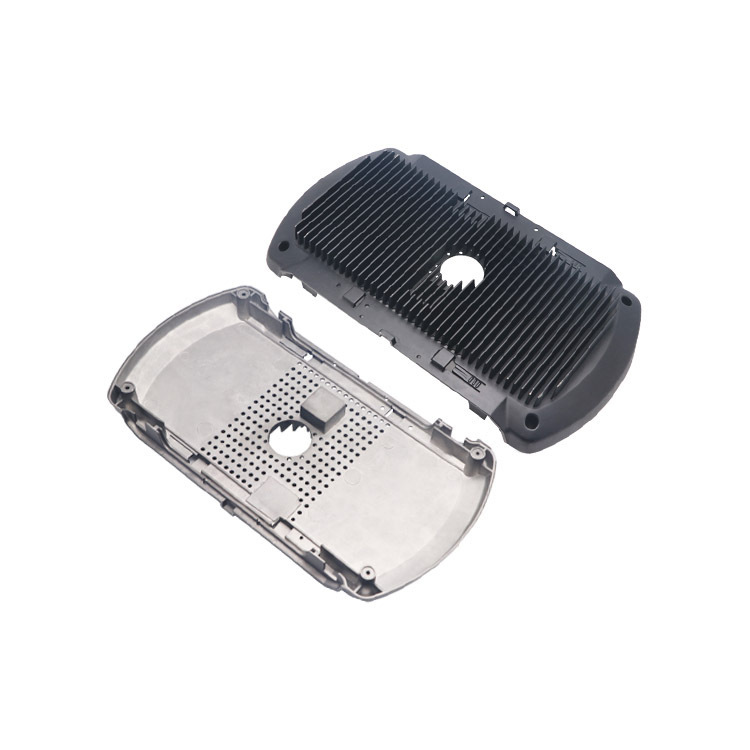
Summary:
Aluminum die casting offers high precision and the ability to produce complex shapes efficiently. This guide provides a comprehensive guide to the aluminum die casting, which achieves a pivotal position in manufacturing industry.
For those involved in the industry, understanding these steps, types and considerations is essential for optimizing manufacturing efficiency and product quality.