CNC fixtures are essential tools in modern machining processes, playing a crucial role in ensuring precision, efficiency, and consistency. In the realm of CNC machining, the importance of fixtures cannot be overstated.
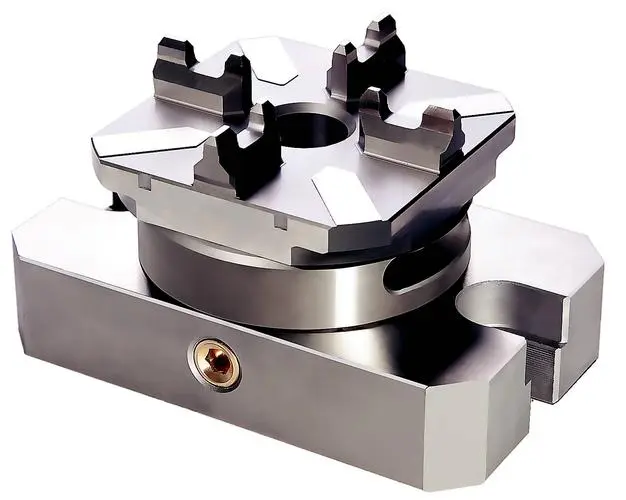
CNC fixtures are devices designed to hold, support, and secure a workpiece in a fixed position during CNC machining operations. These fixtures ensure the workpiece remains steady and correctly aligned, allowing for precise and repeatable machining processes.
By using CNC fixtures, manufacturers can achieve high levels of accuracy, reduce setup times, and improve overall productivity.
Follow us in this article, you will know more about various types of CNC fixtures and gain valuable design tips for creating custom fixtures.
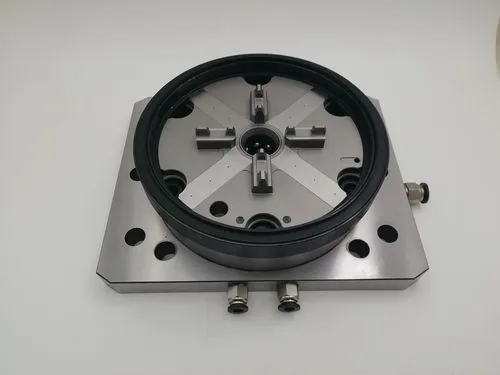
Applications Of CNC Fixture
CNC fixtures are used across various industries, including aerospace, automotive, electronics, and medical devices. Common applications include:
• Milling: Holding workpieces for complex operations, improving surface finishes, and achieving tight tolerances.
• Drilling: Securing parts for accurate drilling and tapping, crucial for precise hole locations.
• Turning: Ensuring stability during CNC lathe operations, particularly for cylindrical workpieces.
• Grinding: Maintaining precise positioning for high-precision surface finishes and dimensional accuracy.
The primary goal of CNC fixtures is to provide stability, reduce vibrations, and enhance machining accuracy, thereby improving product quality and production efficiency.
By using the appropriate fixture for each application, manufacturers can improve the quality of their products and increase their production efficiency.
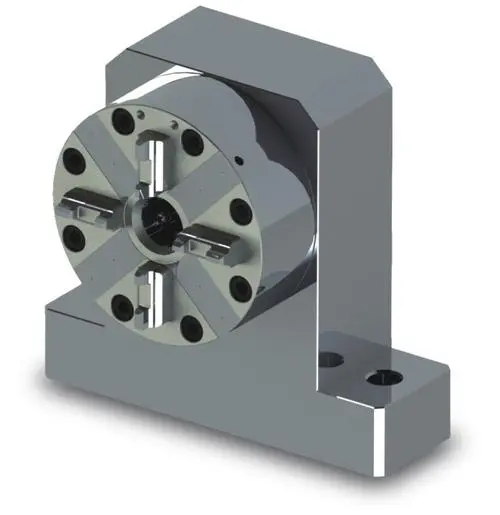
Types Of CNC Fixture
There are several types of CNC fixtures, each designed for specific functions and applications. Some common types include:
• Vises: A vise holds the workpiece in position while allowing access for machining. Vises come in various types, including standard vises, self-centering vises, and multi-axis vises.
• Clamps: Clamps are used to securely hold sheet materials or odd-shaped parts in position. Clamps can be manual, pneumatic, or hydraulic, and they are often used in combination with other fixtures to provide additional support and stability.
• Jigs: A jig positions and supports the workpiece while also guiding the cutting tool. Jigs are typically custom-designed for specific applications and can greatly enhance the accuracy and efficiency of machining operations.
• Modular Fixtures: Modular fixtures are composed of interchangeable components that can be reconfigured to accommodate different workpieces and machining operations. This flexibility makes modular fixtures a cost-effective solution for manufacturers with varying production needs.
• Pallet Fixtures: Pallet fixtures allow for the quick and easy loading and unloading of workpieces, reducing setup times and increasing production efficiency. These fixtures are often used in automated machining environments where high volumes of parts are produced.
• Vacuum Fixtures: Vacuum fixtures use suction to hold workpieces in place, making them ideal for machining thin or delicate materials that might be damaged by mechanical clamping forces.
• Magnetic Fixtures: Magnetic fixtures use magnetic force to hold ferrous workpieces in place. These fixtures are particularly useful for machining complex shapes and contours, as they can provide uniform clamping force without deforming the workpiece.
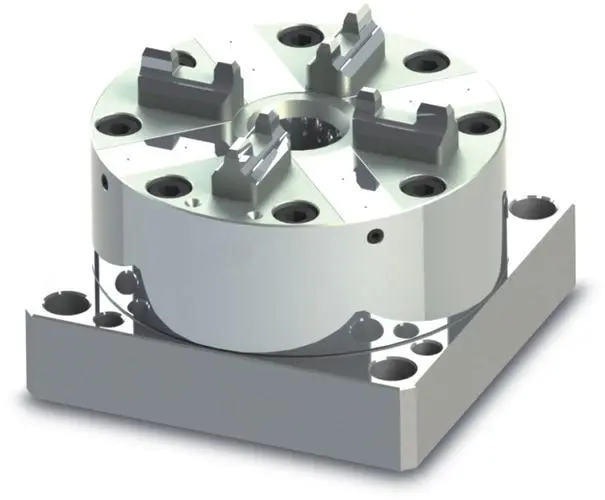
Helpful Considerations For Custom Fixture Design
When designing custom CNC fixtures, several factors should be considered to ensure optimal performance and functionality:
• Material Selection: Choose materials that offer the necessary strength, durability, and resistance to wear and tear. Common materials for fixtures include steel, aluminum, and composites. The choice of material will depend on the specific requirements of the machining operation.
• Design Software: Utilize CAD (Computer-Aided Design) software to create detailed and accurate fixture designs. It allows engineers to visualize and test fixture designs before they are manufactured.
• Ease of Use: Ensure the fixture is easy to set up, adjust, and operate, reducing setup times and minimizing operator fatigue. Fixtures should be designed with user-friendly features, such as quick-release mechanisms and ergonomic handles, to enhance usability and efficiency.
• Flexibility: Design fixtures that can accommodate a range of part sizes and shapes, providing versatility in the machining process. Modular and adjustable fixtures can be reconfigured to suit different workpieces, reducing the need for multiple dedicated fixtures and lowering costs.
• Accuracy and Precision: Ensure the fixture provides the necessary support and alignment to achieve the desired machining accuracy. Fixtures should be designed to minimize movement and vibration, which can negatively impact the quality of the machined part.
• Clamping Force: Determine the appropriate clamping force needed to securely hold the workpiece without causing deformation or damage. The clamping force should be evenly distributed to avoid distorting the workpiece, especially for thin or delicate materials.
• Repeatability: Design fixtures that allow for consistent and repeatable setups, reducing the risk of errors and defects. Fixtures should be easy to align and position, enabling operators to achieve the same setup every time.
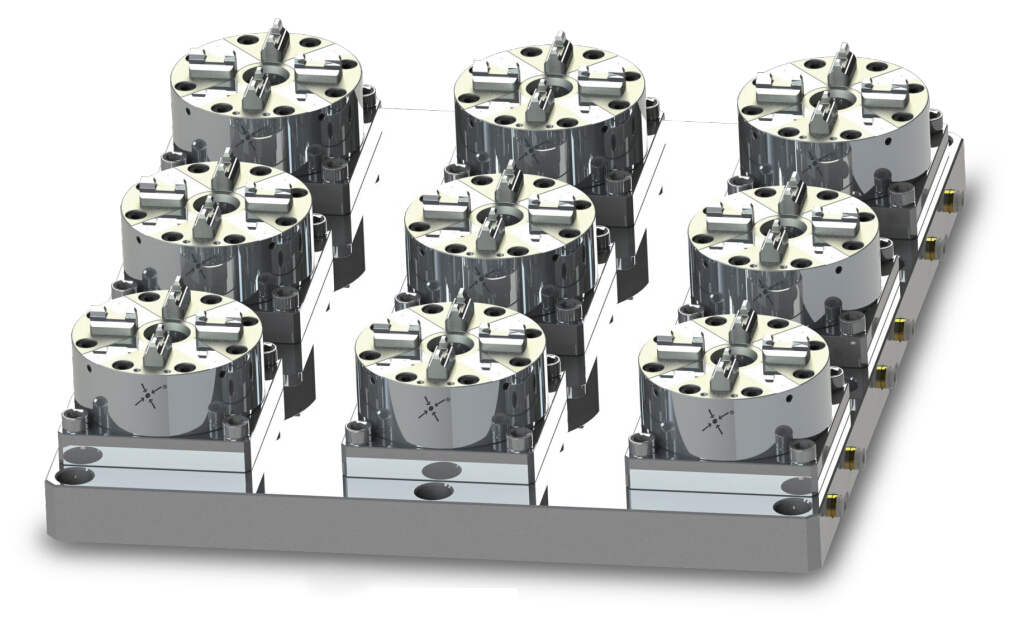
Advanced CNC Fixture Design Techniques
In addition to the basic considerations mentioned above, advanced CNC fixture design techniques can further enhance the performance and functionality of custom fixtures. Some of these techniques include:
• Finite Element Analysis (FEA): Using FEA software to simulate the performance of the fixture under different loads and conditions. This allows engineers to identify potential weaknesses and optimize the design for maximum strength and durability.
• Additive Manufacturing: Utilizing 3D printing technology to create complex fixture designs that would be difficult or impossible to manufacture using traditional methods.
• Integrated Sensors: Incorporating sensors into the fixture design to monitor key parameters such as clamping force, temperature, and vibration.
• Automation: Designing fixtures that can be easily integrated with automated machining systems, such as robotic arms and CNC machines.
• Ergonomics: Considering the ergonomic aspects of fixture design to reduce operator fatigue and improve productivity. Fixtures should be designed to be easy to handle and adjust, with features such as quick-release mechanisms and ergonomic handles.
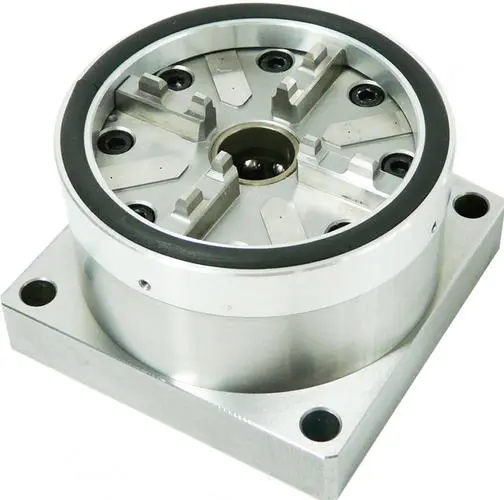
Summary:
CNC fixtures are essential tools in machining, providing stability, precision, and efficiency. Understanding different types, applications, and design considerations can enhance machining processes and results.
By carefully considering these factors and utilizing advanced design techniques, manufacturers can create fixtures that improve the accuracy and efficiency of their machining operations and provide long-term cost savings and enhanced product quality.