Understanding how to protect metal parts from corrosion is crucial for industrial professionals and engineers. Corrosion can lead to significant damage, resulting in costly repairs or replacements.
By implementing effective corrosion prevention methods, you can extend the lifespan of metal components and ensure their reliability.
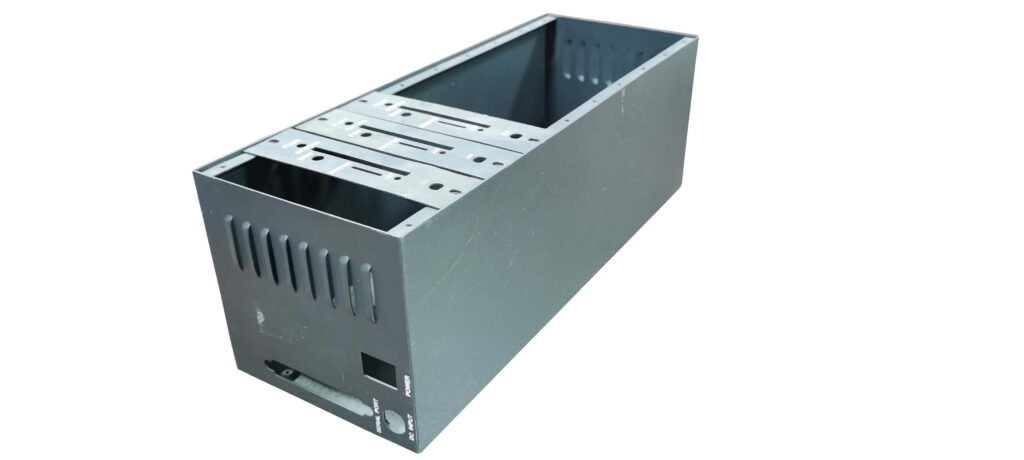
One of the easiest and cheapest ways to prevent corrosion is to use barrier coatings like paint, plastic, or powder.
Powders, including epoxy, nylon, and urethane, adhere to the metal surface to create a thin film. Plastic and waxes are often sprayed onto metal surfaces.
If you want to have a deeper and broader understanding of preventing parts from corrosion, then follow us in this article and let’s explore more detailed information.
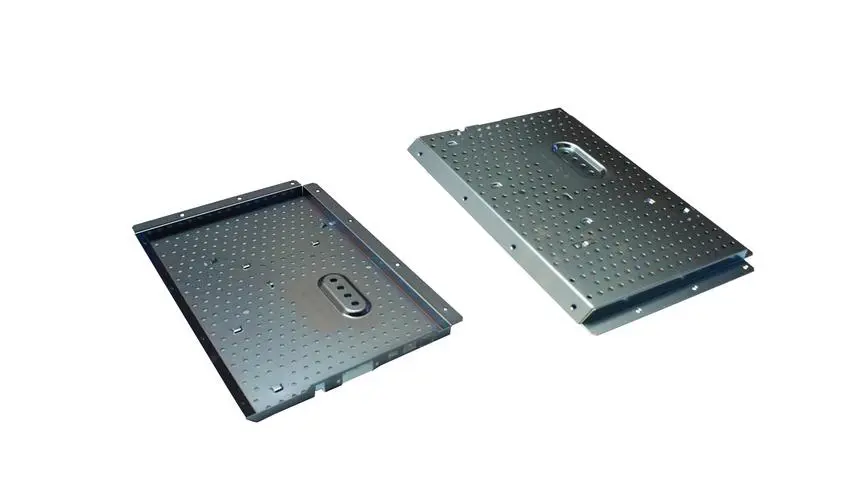
Why Do We Need to Make Metal Parts Corrosion-Resistant?
Metal corrosion poses significant hazards to both industrial applications and everyday life. Corrosion can weaken metal structures, leading to catastrophic failures in critical infrastructure such as bridges, pipelines, and buildings.
In industrial settings, corrosion can result in costly repairs, replacements, and downtime, impacting productivity and profitability. Moreover, the compromised integrity of metal parts can lead to safety risks, accidents, and environmental contamination.
Making metals corrosion-resistant is crucial to mitigate these risks. By employing corrosion-resistant measures, we can extend the lifespan and reliability of metal components, ensure the safety of structures, and reduce maintenance costs.
Corrosion-resistant methods enhance the durability and performance of metal parts, ensuring they can withstand harsh environments and maintain their functionality over time.
This not only improves operational efficiency but also contributes to sustainable practices by reducing the need for frequent replacements and conserving resources.
How to Make Metal Corrosion Resistant?
Galvanizing
Galvanizing applies a protective coating of zinc over iron or steel. Since zinc corrodes about 30 times slower than iron, galvanizing can be a cheap and effective way to prevent rust.
This method is widely used in industrial settings due to its cost-effectiveness and durability. Galvanizing not only protects the metal from corrosion but also enhances its strength and durability.
The process involves dipping the metal into molten zinc, which forms a robust layer of protection. This method is particularly effective for steel and iron parts exposed to harsh environments.
Anodizing
Anodizing is an electrochemical process that increases the thickness of the natural oxide layer on the surface of metal parts, particularly aluminum.
This method enhances corrosion resistance and improves the durability and lifespan of the metal.
Anodizing also allows for the addition of dyes and colorants, making it a popular choice for both protective and decorative purposes.
The process involves immersing the metal in an electrolyte solution and applying an electric current, which causes the oxide layer to thicken and harden. This creates a highly durable and corrosion-resistant surface that is ideal for a wide range of applications.
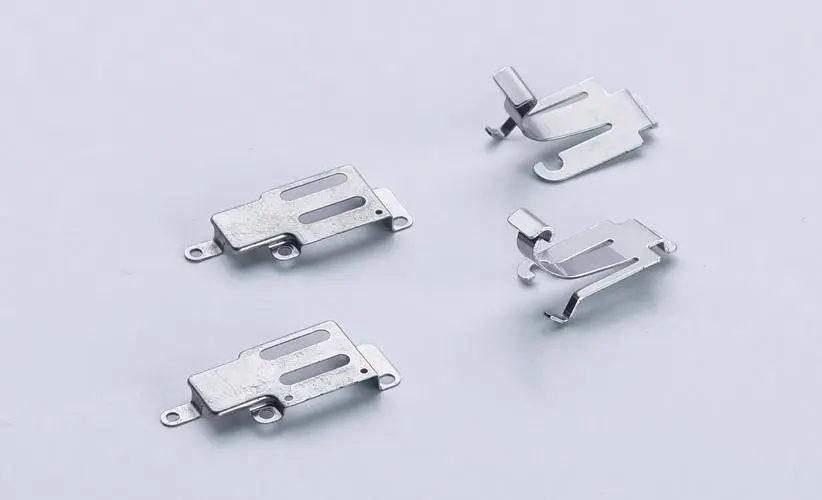
Cathodic Protection
Cathodic protection is a technique used to control the corrosion of a metal surface by making it the cathode of an electrochemical cell.
This method is widely used in industries such as oil and gas, marine, and infrastructure to protect pipelines, tanks, and other metal structures from corrosion.
There are two types of cathodic protection: sacrificial anode and impressed current.
Sacrificial anode protection involves attaching a more easily corroded “sacrificial” metal to the protected metal. The sacrificial metal corrodes instead of the protected metal, thus preventing corrosion.
Electroplating
Electroplating is a process that uses an electric current to reduce dissolved metal cations, allowing them to form a coherent metal coating on an electrode. This method is widely used to improve the corrosion resistance, wear resistance, and appearance of metal parts.
Commonly electroplated metals include nickel, chrome, and zinc. The process involves immersing the metal part in an electrolyte solution containing the desired plating metal and applying an electric current.
The metal cations are reduced and deposited onto the surface of the part, creating a durable and corrosion-resistant coating.
Electroplating is commonly used in industries such as automotive, aerospace, and electronics to enhance the performance and longevity of metal components.
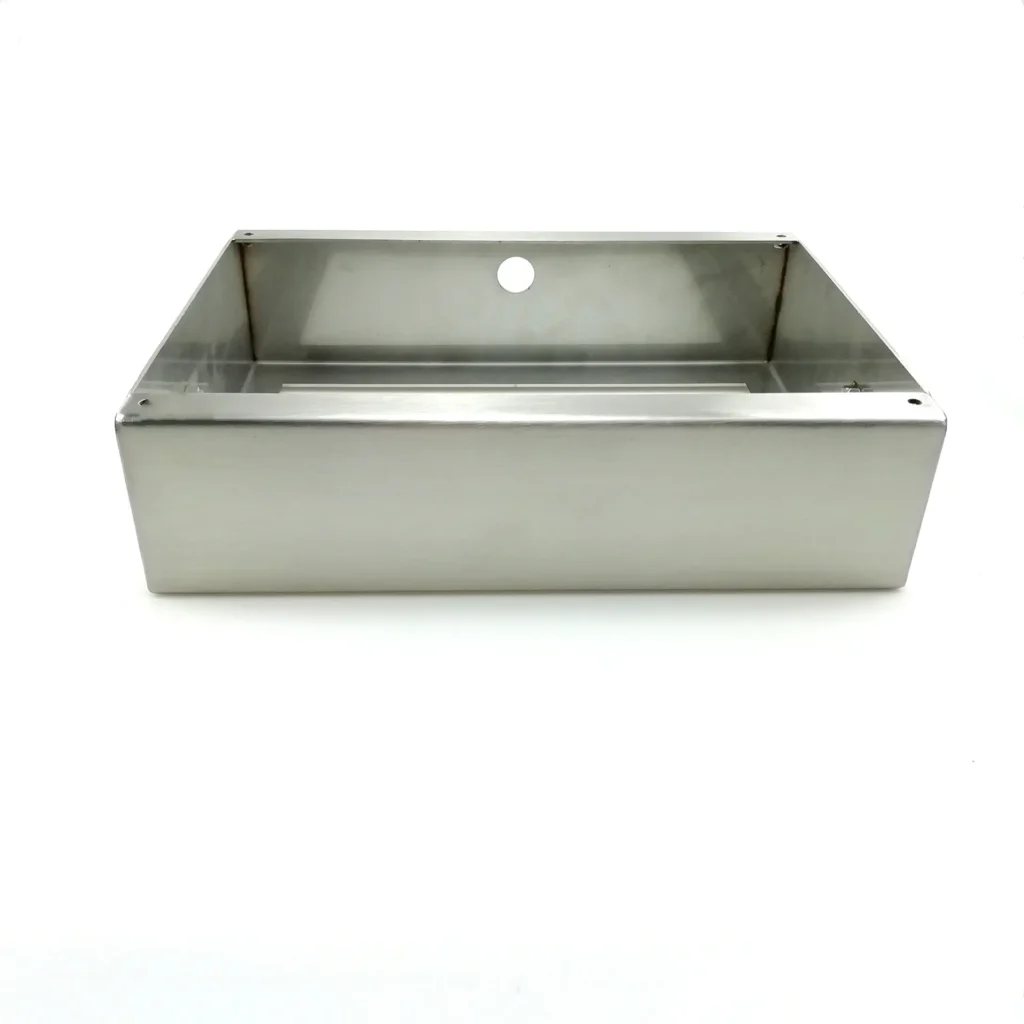
How to Prevent Corrosion in Metals?
Environmental Measures
Controlling the environment is another effective way to prevent corrosion. This can involve using dehumidifiers in storage areas, applying anti-corrosion sprays, or simply ensuring that metal parts are kept dry and clean.
Environmental measures can also include controlling the temperature and humidity levels in manufacturing and storage facilities to minimize the risk of corrosion.
Modifying the Design
Design considerations can also play a significant role in preventing corrosion. For instance, designing parts with smooth surfaces can minimize areas where water and debris can accumulate, thereby reducing the risk of corrosion.
Other design modifications can include avoiding sharp corners and crevices, which can trap moisture and promote corrosion.
Using corrosion-resistant materials, such as stainless steel and aluminum, in the design phase can also help to minimize the risk of corrosion.
What is the Best Thing to Put on Metal to Prevent Rust?
Rust-resistant coatings such as sodium hydroxide and potassium nitrate can be highly effective. These chemicals form a coating that’s effective in preventing rust.
Although not aesthetically pleasing, these coatings get the job done. Additionally, common paints are also an easy way to protect metal from rust. Rust-resistant coatings can be applied using various methods, including brushing, spraying, and dipping.
Each method has its advantages and is suitable for different applications. For example, brushing is ideal for small and intricate parts, while spraying is more efficient for large surfaces. Dipping is often used for parts with complex shapes, ensuring complete coverage and protection.
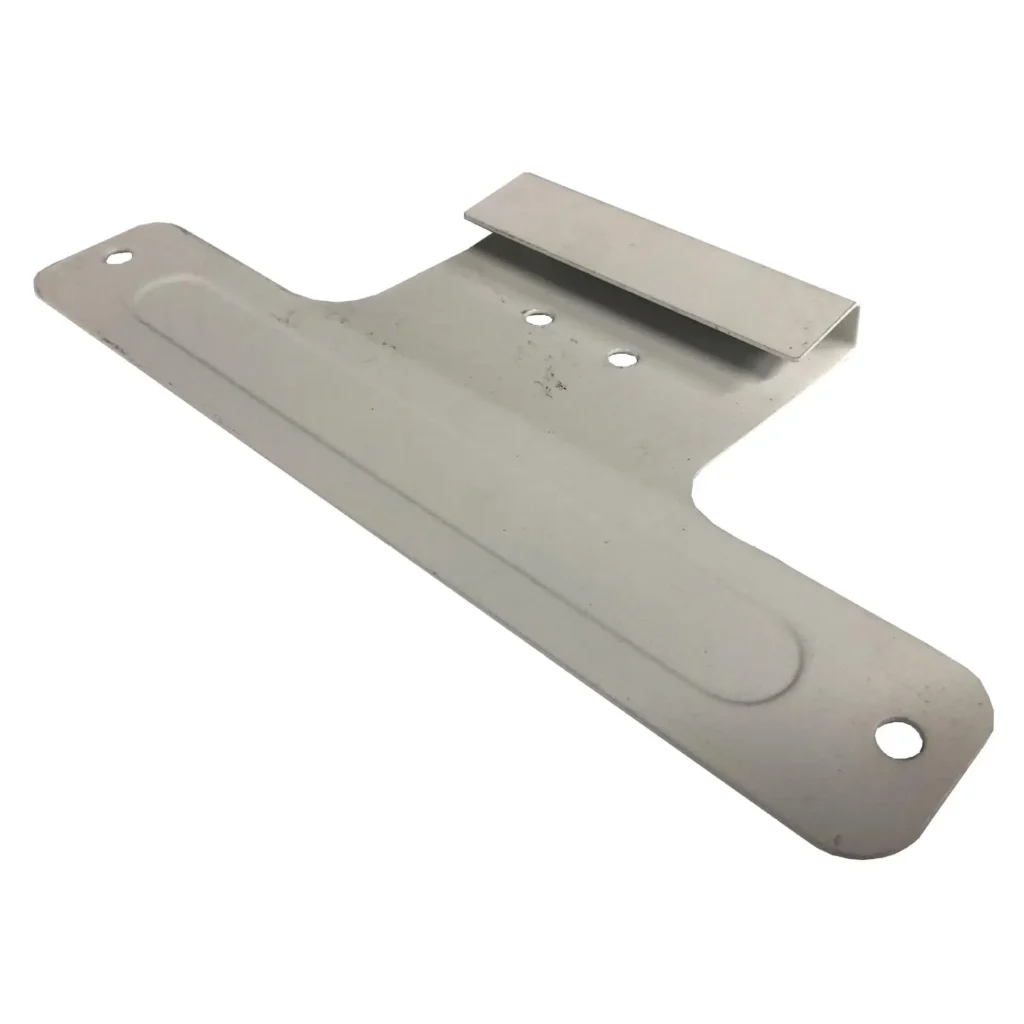
Summary:
By understanding and implementing various corrosion prevention methods, we can significantly extend the lifespan and reliability of your metal parts.
Regular maintenance and monitoring are key to ensuring the effectiveness of these methods. Remember to choose the appropriate method based on your specific needs and the type of metal you are working with.
With these strategies, we can keep metal parts corrosion-resistant, ensuring longevity and efficiency in their applications.