The CNC lathing process is a cornerstone of modern manufacturing, offering precision and efficiency in producing cylindrical parts. In this article, we will go deep into the intricacies of CNC lathing, covering its brief history, workings, methods, equipment, applications, benefits, and comparisons with other machining processes.
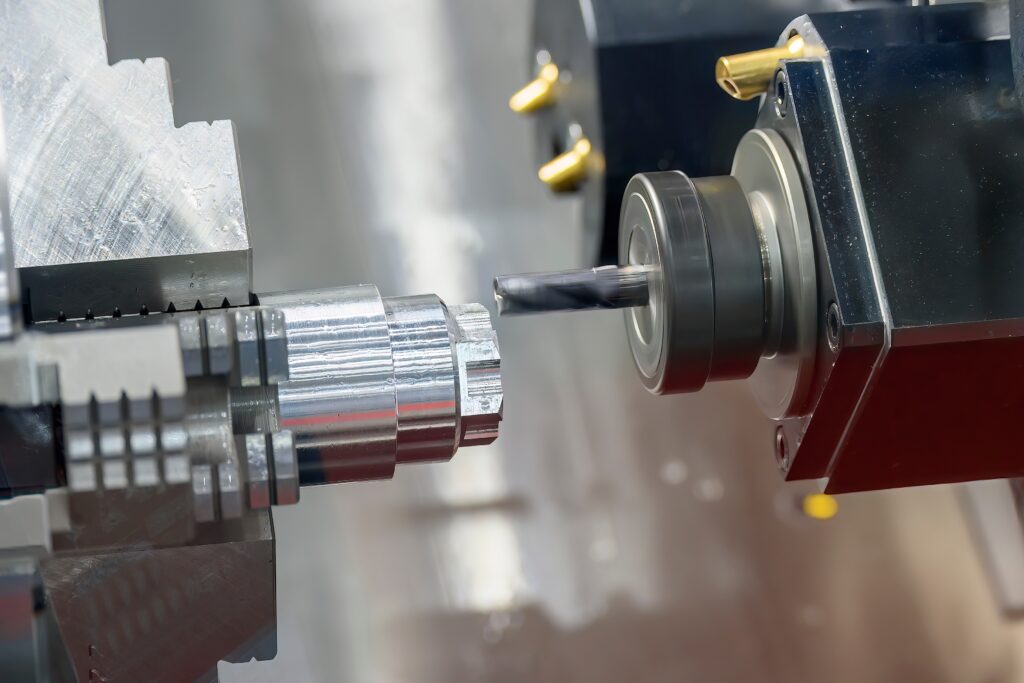
CNC lathing involves using a computer-controlled lathe to shape materials into desired forms. The process starts with a CAD model, translated into a CNC program that directs the lathe to cut, shape, and finish the material with high precision.
Now, let’s explore the CNC lathing process in more detail to understand its significance in modern manufacturing.
-
Table Of Contents
-
1. Everything You Need to Know About CNC Lathing Process
-
2. What is CNC Lathing?
-
3. What Are the Steps of the CNC Lathing Process?
-
4. What Are the Various CNC Lathing Methods?
-
5. What is the Equipment Used in the CNC Lathing Process?
-
6. What Are the Applications of CNC Lathing?
-
7. What Are the Benefits of CNC Lathing?
-
8. Comparison with Other Machining Processes
-
9. Summary
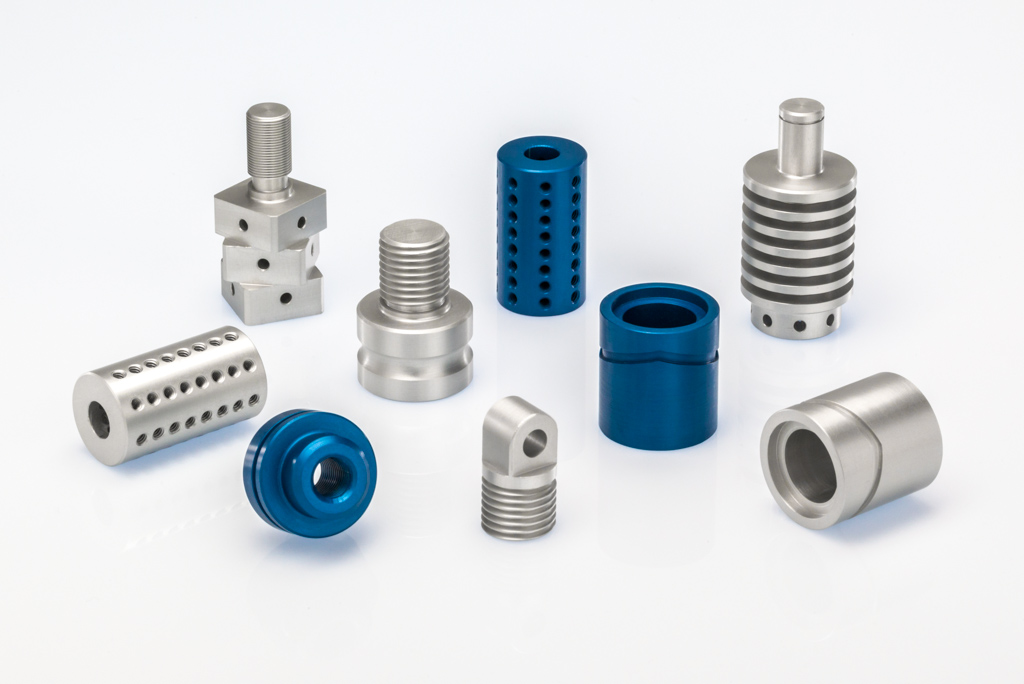
What is CNC Lathing?
CNC lathing, or CNC turning, is a subtractive manufacturing process where a cutting tool removes material from a rotating workpiece to create a desired shape.
The term “CNC” stands for Computer Numerical Control, which refers to the automated control of machining tools via a computer.
CNC lathing is widely used in various industries due to its precision, efficiency, and ability to produce complex geometries that would be difficult or impossible to achieve with manual machining.
The CNC lathe, unlike traditional lathes, operates under the control of sophisticated software, which ensures the consistency and accuracy of the parts produced.
This automation reduces human error and allows for high-speed production, making it an essential tool in modern manufacturing environments.
CNC lathing can be applied to a variety of materials, including metals, plastics, and composites, making it a versatile process for creating parts with tight tolerances and intricate details.
What Are the Steps of the CNC Lathing Process?
The CNC lathing process is methodical and precise, involving several steps to ensure that the final product meets the required specifications. Here’s a detailed look at each step:
1. Design and Planning: The process begins with the creation of a detailed CAD model. This model is reviewed to ensure it meets all design requirements and can be manufactured efficiently. The design phase may also involve selecting the appropriate material for the workpiece based on factors such as strength, durability, and machinability.
2. Programming: Once the design is finalized, the CAD model is converted into G-code. This programming step is crucial as it translates the design into a series of instructions that the CNC lathe will follow. The G-code specifies the tool paths, cutting speeds, feed rates, and other parameters.
3. Setup and Calibration: The workpiece is securely mounted in the chuck, and the cutting tools are loaded into the tool turret. The machine is then calibrated to ensure that the tools are positioned correctly relative to the workpiece. This setup step is vital for achieving accurate cuts and preventing errors.
4. Rough Machining: The initial cuts are made to remove the bulk of the material and create the rough shape of the part. This stage involves high-speed cutting and may produce significant amounts of chips or debris.
5. Finishing Machining: After the rough shape is achieved, the finishing cuts are made to achieve the final dimensions and surface finish. This stage requires precise control and may involve slower cutting speeds to ensure a high-quality finish.
6. Quality Inspection: The finished part is inspected to ensure it meets all specifications. This may involve measuring dimensions, checking surface finish, and performing other quality control tests.
7. Post-Processing: Depending on the part’s requirements, additional post-processing steps may be needed, such as heat treatment, coating, or assembly.
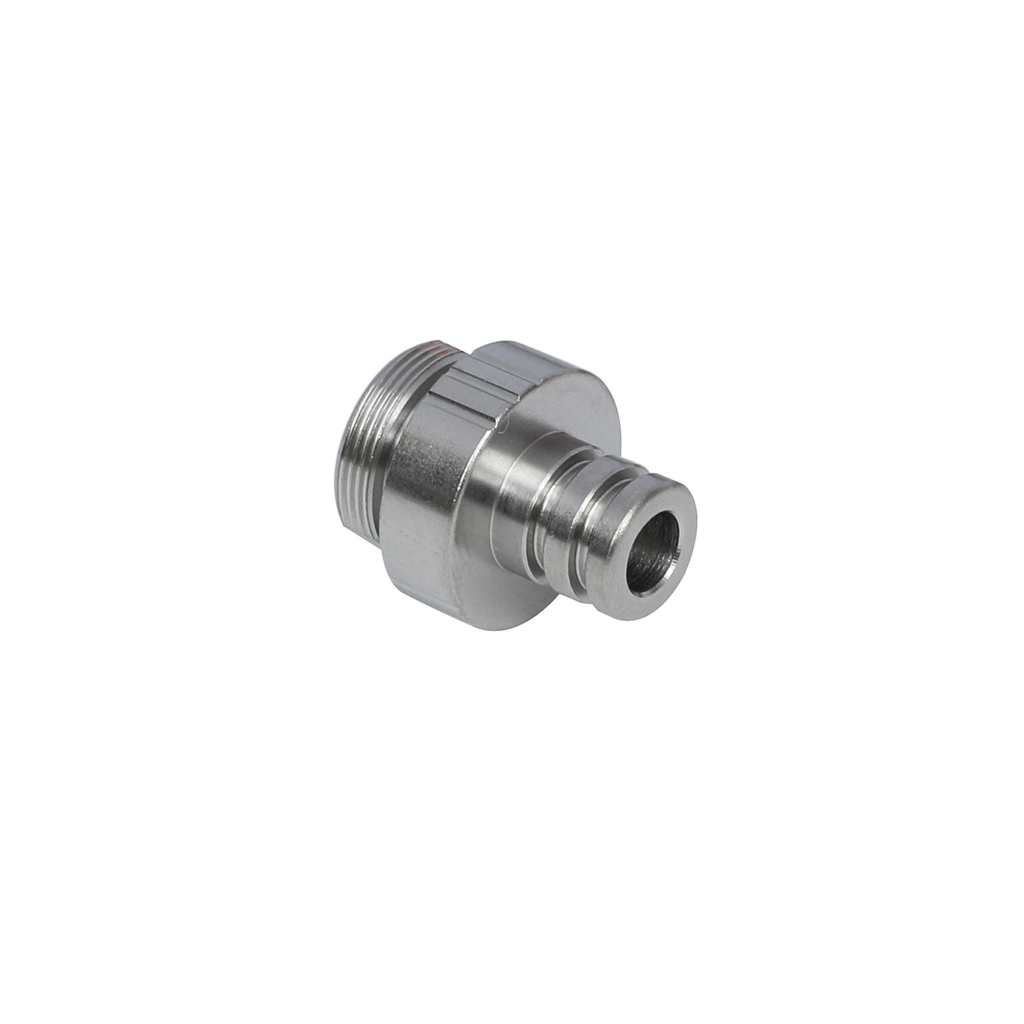
What Are the Various CNC Lathing Methods?
CNC lathing encompasses several methods, each suited to different types of operations and materials. Here are some of the most common methods:
• Turning: The primary method in CNC lathing, turning involves the removal of material from the outer diameter of a rotating workpiece. This method is used to create cylindrical shapes and is fundamental to most CNC lathe operations.
• Facing: In facing, the cutting tool moves across the end of the workpiece to create a flat surface. This method is used to produce a smooth, flat surface perpendicular to the workpiece’s axis.
• Thread Cutting: Thread cutting involves creating threads on the exterior or interior surfaces of the workpiece. This method is used to produce threaded components, such as bolts and nuts.
• Grooving: Grooving involves cutting a groove into the workpiece. This method is used to create features such as O-ring seats or snap ring grooves.
• Parting: Parting, also known as cutoff, involves cutting off a portion of the workpiece. This method is used to separate a finished part from the remaining material.
• Boring: Boring is the process of enlarging an existing hole in the workpiece. This method is used to create precise, smooth internal diameters.
• Knurling: Knurling involves creating a textured pattern on the surface of the workpiece. This method is used to produce grip surfaces on handles or knobs.
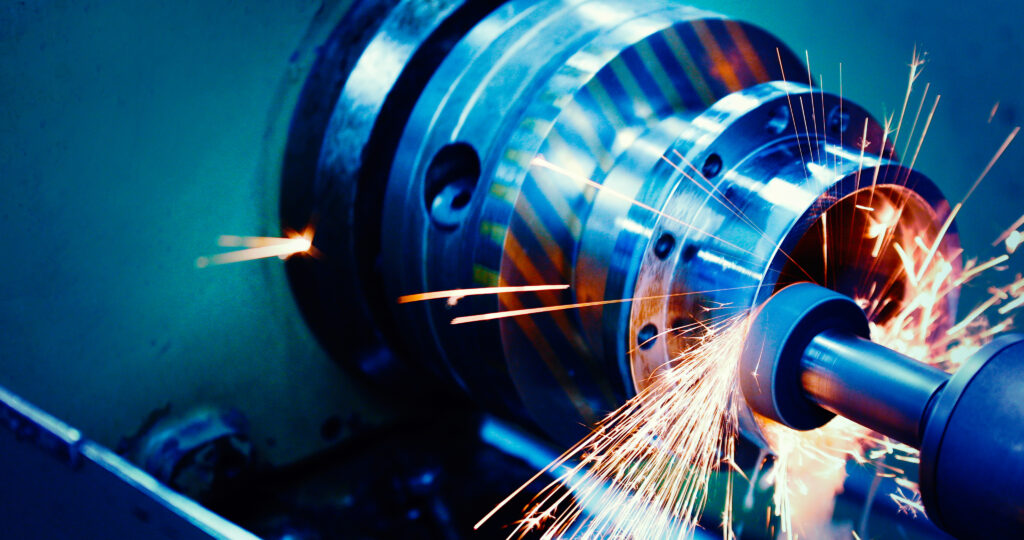
What is the Equipment Used in the CNC Lathing Process?
The CNC lathing process requires several pieces of specialized equipment to achieve precision and efficiency. Here are the key components:
• CNC Lathe Machine: The primary equipment for the process, a CNC lathe machine includes a bed, headstock, tailstock, and a tool turret. The machine’s movements are controlled by a computer program.
• Chuck: The chuck is a clamping device that holds and rotates the workpiece. Chucks can have three or four jaws, depending on the shape and size of the workpiece.
• Cutting Tools: Various cutting tools are used in CNC lathing, including turning tools, boring bars, thread cutting tools, and grooving tools. These tools are made from high-speed steel (HSS), carbide, or other durable materials.
• Tool Turret: The tool turret holds multiple cutting tools and rotates to position the desired tool for the operation. This allows for quick tool changes and efficient machining.
• Coolant System: The coolant system delivers a coolant to the cutting area to reduce heat and friction. This helps extend the life of the cutting tools and improves the surface finish of the workpiece.
• Control Panel: The control panel is the interface where operators input and adjust the CNC program. It includes a display screen, keyboard, and other controls for operating the machine.
• Tailstock: The tailstock supports the workpiece and can be used to hold tools for operations such as drilling or reaming.
What Are the Applications of CNC Lathing?
CNC lathing is used in various industries due to its versatility and precision. Here are some common applications:
• Automotive: CNC lathing is used to manufacture engine components, shafts, gears, and other critical parts for vehicles.
• Aerospace: In the aerospace industry, CNC lathing produces precise aircraft parts, such as turbine blades, landing gear components, and structural elements.
• Medical: The medical industry uses CNC lathing to create surgical instruments, implants, and prosthetic components. Precision and reliability are paramount in these applications.
• Electronics: CNC lathing is employed to make connectors, housings, and other components for electronic devices. The process ensures consistent quality and tight tolerances.
• General Manufacturing: CNC lathing is used to produce parts for machinery, equipment, and consumer products. The process is ideal for creating custom components with complex geometries.
• Oil and Gas: In the oil and gas industry, CNC lathing is used to manufacture parts for drilling equipment, valves, and pumps. These components must withstand harsh environments and high pressures.
• Defense: The defense sector relies on CNC lathing to produce parts for weapons systems, vehicles, and communication equipment.
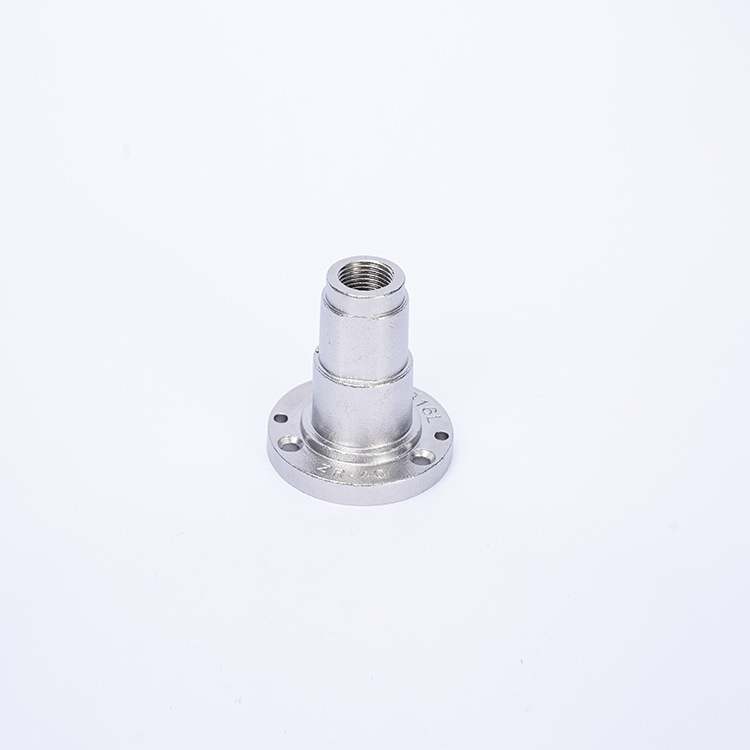
What Are the Benefits of CNC Lathing?
• Precision: CNC lathing provides high accuracy and tight tolerances, ensuring that parts meet exact specifications.
• Efficiency: The automated nature of CNC lathing allows for faster production times compared to manual machining. This efficiency is critical in high-volume manufacturing.
• Consistency: CNC lathing produces identical parts with minimal variation, ensuring consistent quality across production runs.
• Versatility: CNC lathes can handle a wide range of materials and create complex shapes and designs that would be difficult or impossible with manual methods.
• Cost-Effective: By reducing labor costs and material waste, CNC lathing can be a cost-effective solution for manufacturing. The ability to produce parts quickly and accurately also minimizes the need for rework.
• Flexibility: CNC lathes can be quickly reprogrammed to produce different parts, allowing manufacturers to respond to changing demands and custom orders.
• Safety: CNC lathing reduces the risk of injury by automating dangerous tasks. Operators are less exposed to moving parts and cutting tools.
Comparison with Other Machining Processes
CNC lathing is often compared to other machining processes, such as CNC milling and drilling. Here are some key differences and similarities:
• CNC Milling: CNC milling involves rotating cutting tools to remove material, creating complex 3D shapes. Milling is ideal for parts with intricate geometries and multiple surfaces. While CNC lathing is best for cylindrical parts, milling excels at producing flat and contoured surfaces.
• CNC Drilling: CNC drilling is primarily used for creating holes in the workpiece. It involves a rotating drill bit that penetrates the material. Drilling is often combined with other processes, such as milling or lathing, to create complete parts.
• CNC Lathing: CNC lathing is best suited for producing symmetrical, cylindrical parts. The workpiece rotates while the cutting tool remains stationary, allowing for precise control over the shape and dimensions.
Each of these processes has its own strengths and applications, and they are often used together in manufacturing operations to produce complex parts. The choice of process depends on the part’s design, material, and production requirements.
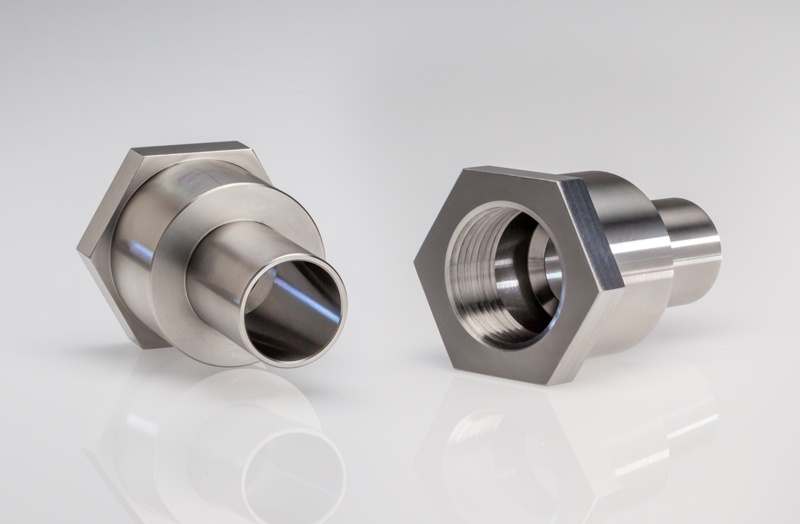
Summary
In conclusion, CNC lathing stands out for its precision, efficiency, and versatility in manufacturing. By understanding its processes and benefits, professionals can better leverage this technology to enhance production capabilities.
Whether used in the automotive, aerospace, medical, or electronics industries, CNC lathing is a critical tool for producing high-quality, consistent parts. Its ability to create complex geometries with tight tolerances makes it indispensable in modern manufacturing.
The advancements in CNC technology continue to push the boundaries of what is possible in machining, making it an exciting field with ongoing innovations.
By staying informed about the latest developments and best practices in CNC lathing, professionals can ensure that they remain competitive and capable of meeting the demands of today’s manufacturing landscape.