CNC machined parts are integral components in various mechanical systems. Common examples include gears, bushings, shafts, and housings.
These parts are crafted with precision to meet specific functional requirements and are essential in industries like automotive, aerospace, and manufacturing.
When working with CNC machined parts, ensuring customer satisfaction through effective sample confirmation is crucial.
This article concludes key steps to confirm samples with customers, covering communication, documentation and several testing methods.
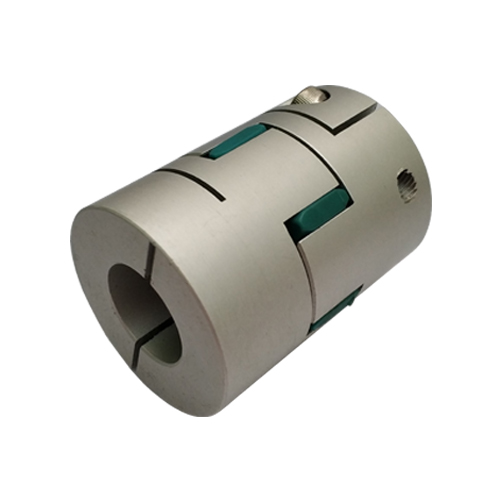
Based on our decades of experience in the CNC industry, we recommend the following steps for confirming samples of CNC machined parts with our customers:
- Communicating effectively to understand our customer needs
- Providing detailed documentation of the parts
- Testing and validating
Now, let’s dive into the specifics of how to achieve above steps effectively.
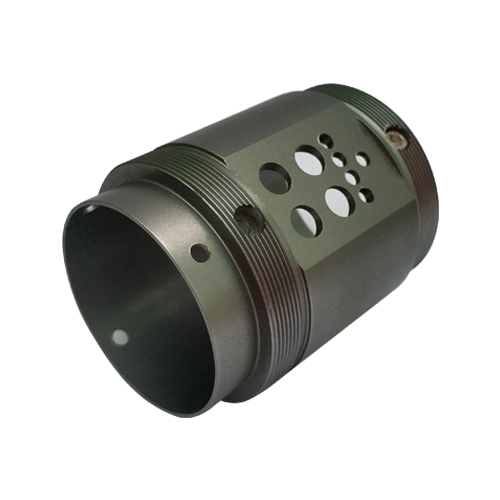
Communicating effectively to understand customer needs
Effective communication is key to confirming samples of CNC machined parts. Regular updates and detailed reports keep customers informed throughout the production process.
Use multiple communication channels like email, video calls, and in-person meetings to discuss sample specifications, production timelines, and any issues that arise. Clear and concise information builds trust and alignment. Communication methods can be divided as follows:
- Initial Consultation: Start with an initial consultation via email, phone call, or video conference to understand the customer’s requirements and expectations. Discuss the specifications of the parts, including materials, dimensions, tolerances, and special features.
- Regular Updates: Maintain regular communication throughout the production process. Provide updates on the progress of the machining, including any challenges encountered and how they are being addressed. This transparency keeps the customers informed and builds trust.
- Detailed Reports: Send detailed reports after each key production stage, including materials used, machining processes, and quality control measures. Send images or videos of the parts at various stages to give the customer a visual understanding.
- Final Review Meeting: Once the samples are ready, schedule a final review meeting with the customer. Present the completed samples, review quality control documentation, discuss any final adjustments and agree on the next steps for production.
Effective communication involves providing information and listening to the customer’s feedback, ensuring satisfaction with samples and confidence in the final production.
Quality Control Measures
Implementing stringent quality control measures is essential to guarantee that CNC machined parts meet customer expectations. Therefore, let’s expand on quality control measure a bit here.
Start with a thorough inspection of the raw materials and continue with in-process checks using precision measuring tools to verify dimensions and tolerances. Conduct functional tests to ensure the parts operate correctly. Document all quality control procedures and results for transparency.
By implementing robust quality control measures, you can ensure that the CNC machined parts meet the customer’s specifications and expectations. This not only enhances customer satisfaction but also builds a reputation for delivering high-quality products.
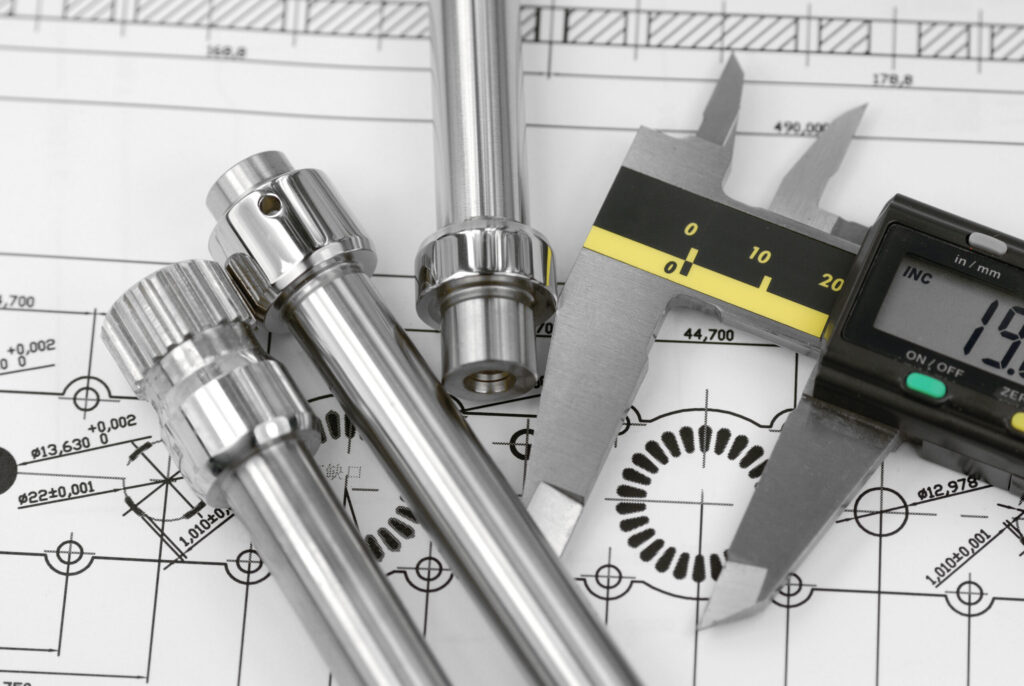
Providing detailed documentation of the parts
Comprehensive documentation is vital when confirming CNC machined parts. Almost every step in the process needs to be documented, which facilitates us to review the details at any time.
This level of detail also helps customers understand the quality and precision of the parts they are receiving. Here are the detailed steps:
- Machining Process Documentation: Provide an overview of the machining process, including CNC machines, tools, and techniques used. Describe the sequence of operations and special procedures.
- Material Specifications: Include detailed information on the materials used for the parts. Specify the type of material, grade, and properties like hardness, tensile strength, and thermal conductivity. Provide material certificates or test reports if available.
- Inspection Reports: Prepare comprehensive reports detailing quality control checks, key dimensions, tolerances, and surface finishes. Explain how deviations are addressed.
- Visual Documentation: Include photographs and videos at all production stages, from raw materials to finished samples. Visual documentation helps customers understand the machining process and final product quality.
- Test Reports: Include functional test results, describing tests conducted, methods used, and outcomes. Highlight critical findings and their significance.
- Delivery Documentation: Prepare a delivery note or packing list with part descriptions, quantities, and handling instructions. Organize documentation neatly for easy understanding.
Thorough documentation confirms sample quality and provides a valuable reference for future production. By maintaining detailed records, you can ensure consistency and traceability for quality assurance and customer satisfaction.
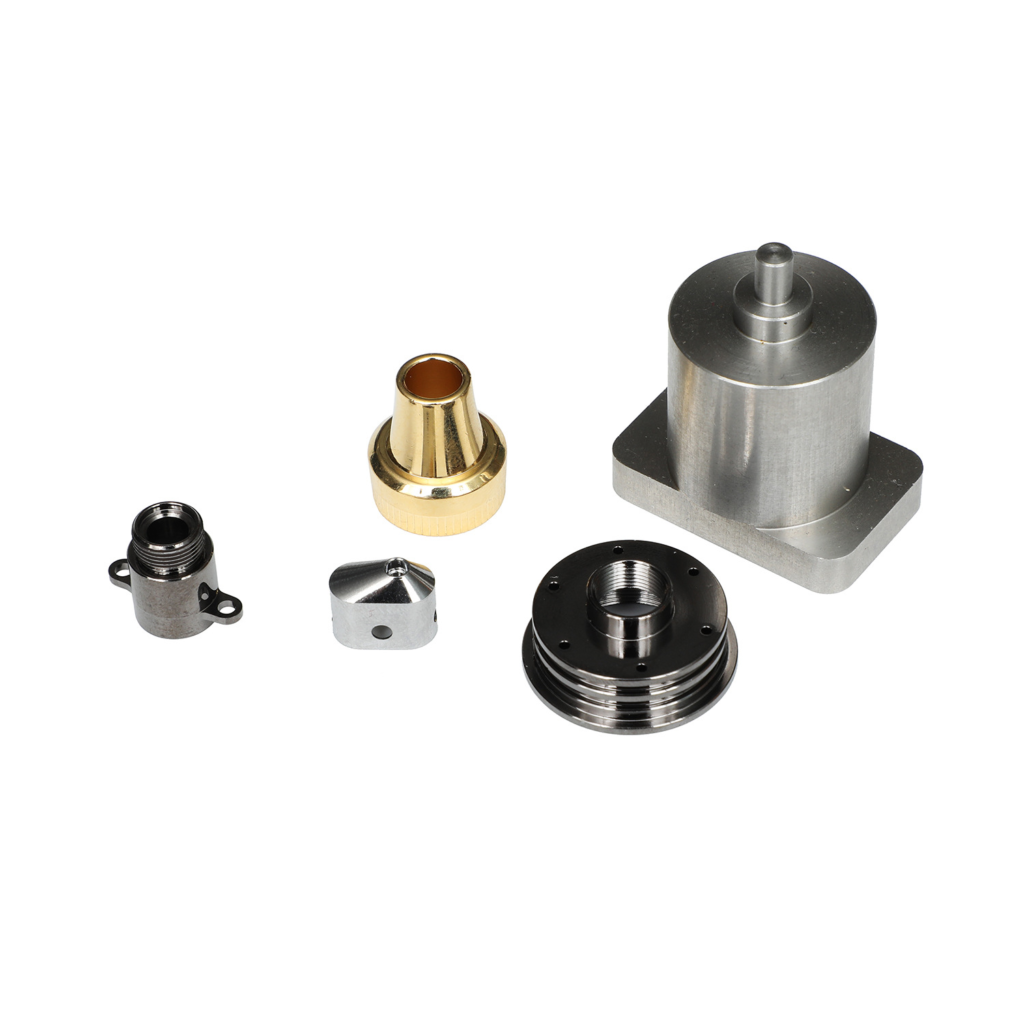
Testing and validating
Testing the accuracy of a CNC machine involves several steps. This process helps ensure that the machine is operating within the required tolerances and that the parts produced will meet the necessary specifications.
1. Pre-Test Preparation: Clean the machine and ensure tools and fixtures are properly installed and calibrated.
2. Indicator Setup: Attach a dial indicator to the spindle or tool holder, ensuring it contacts a reference surface securely and moves freely without obstruction.
3. Initial Measurement: Fully depress the indicator against the reference surface, zero the dial, move the axis away from the surface, back it out about 1/32 of an inch, and zero the indicator again.
4. Running the Test: Move the machine’s axis a precise distance (typically one inch) and record the indicator reading. Repeat for each axis.
5. Repeatability Check: Perform multiple tests to assess the repeatability. Consistent measurements indicate good repeatability.
6. Analysis and Adjustment: Analyze the test results to identify any deviations. Adjust settings as necessary, then retest to ensure improved accuracy.
Regular accuracy testing maintains high precision and quality, improving product reliability and customer satisfaction.
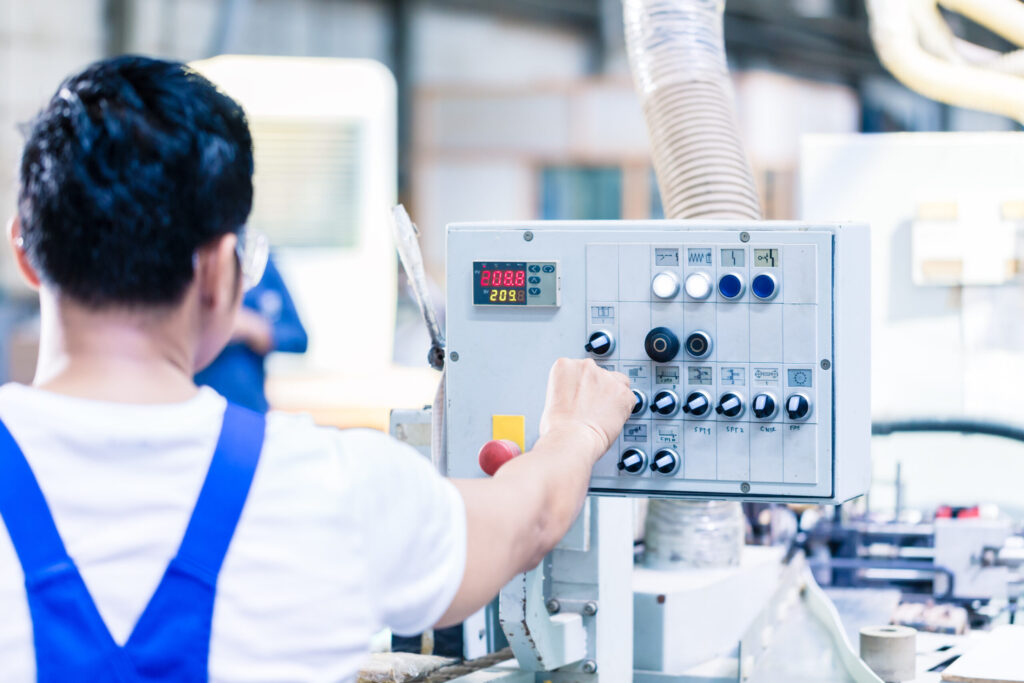
Summary
Confirming CNC machined parts samples with customers requires clear communication, comprehensive documentation, and accuracy testing.
Prioritizing transparency and precision ensure customer satisfaction and high-quality CNC machined parts.
Regular testing and continuous improvement further enhance the reliability and performance, fostering strong customer relationships and long-term success.